分层厚度对微细电火花铣削加工模具及热压制品表面粗糙度的影响
2017-1-6 来源: 大连理工大学机械工程学院 作者:项得胜,王会,李剑中,虞慧岚,余祖元
摘要:分层厚度直接影响微细电火花铣削加工的加工效率及表面粗糙度。为了合理规划微细电火花铣削加工的分层厚度,提高加工效率,研究了分层厚度对微细电火花加工的模具型腔及相应热压成形制品表面粗糙度的影响, 同时分析了热压成形制品表面与微模具型腔表面之间的关系,以及热压前、后微模具型腔表面轮廓的变化。结果表明:当电极轨迹重叠率一定时,模具型腔底面的表面粗糙度值随着分层厚度的增加而增大; 分层厚度对型腔侧壁表面粗糙度无明显影响;热压制品表面轮廓算术平均偏差小于模具型腔表面轮廓算术平均偏差;热压后的模具表面轮廓发生了变化,表面粗糙度值Ra 和峰高Rpk 减小,峰谷Rvk 增大。
关键词:微细电火花加工;微模具;热压成形;表面粗糙度
随着微机械电子系统的发展,微小制件得到了广泛的应用[1-2]。微注塑及微热压作为聚合物微塑成形技术,因其制品精度好,成形效率高,使其在电子、航空航天、生物科技及精密仪器等领域得到广泛应用[3]。微热压成形因聚合物流动少,能有效地避免内部应力,被应用于成形更精巧的结构[4]。聚合物微热压成形是在合适的温度、压力下,模具的微小结构复制到聚合物基板的一种工艺。
微模具的加工成为微塑成形的关键,因模具结构微小,尺寸精度及表面质量要求高,传统的制造方法已不能满足要求。因此,LIGA 技术、微铣削加工技术、微细电化学加工技术、微细电火花加工技术等先进制造工艺被应用于微模具的加工领域[5]。由于电火花加工是非接触式加工,工具与工件间无宏观作用力,所以利用简单截面的柱状电极,采用微细电火花逐层铣削的加工方式,能在任何导体及半导体材料上加工出任意复杂的三维结构[6]。
分层厚度是微细电火花铣削加工中的重要参数,既影响加工过程中的工具损耗,也直接影响三维结构加工的效率,层厚越大,加工效率越高。微细电火花加工的模具型腔表面比光刻工艺加工的更粗糙;此外,聚合物材料的性质使热压制品表面轮廓与微细电火花加工的模具型腔表面并非完全复制的关系。因此,微细电火花铣削加工的模具型腔表面粗糙度与热压制品表面粗糙度之间的关系,以及分层厚度对两者表面质量的影响值得研究,以达到合理规划分层层厚、提高加工效率的目的。本文采用微细电火花铣削加工工艺,在放电参数、电极轨迹重叠率一定的情况下,加工不同分层层厚的模具型腔。实验选取PMMA(聚甲基丙烯酸甲酯)作为热压成形材料,以Ra、Rpk、Rvk 作为表面质量的评定参数,研究了制品与模具表面轮廓的关系,以及分层厚度对模具侧壁、底面及制品相应表面的影响。
1.实验装置
微模具型腔加工设备为自制立式微细电火花加工机床(图1),其X、Y、Z 3 个移动平台的最小分辨率均为0.1 μm,单向重复定位精度为1 μm,最大行程为204 mm。旋转主轴径向跳动在1 μm 以内,最大转速为40 000 r/min。
本文所涉及的热压成形试验均在图2 所示的热压成形机上完成,该热压成形机是大连理工大学微系统研究中心自行研制而成。其上下热压采用独立的温度控制,控制精度为±1 ℃;压力通过传感器进行反馈控制,控制精度为±40 N;控制系统的软件采用面向对象的程序设计方法设计,可实现手动操作及全自动运行,均满足实验要求。
2.实验方法及过程
2.1 模具型腔的设计
本试验设计的模具结构见图3。三维型腔的设计尺寸为600 μm×600 μm×102 μm,其侧壁分别有60°、45°的倾角。具有倾角的侧壁结构一方面有利于热压制品的脱模,降低制品次品率;另一方面,可得到不同分层厚度条件下,侧壁台阶形误差的大小及对侧壁表面质量的影响。
2.2 模具型腔的加工
微细电火花铣削加工中, 选取的层厚不同,模具型腔的表面形貌也会不同,其对热压制品表面轮
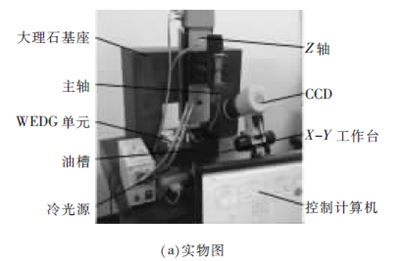
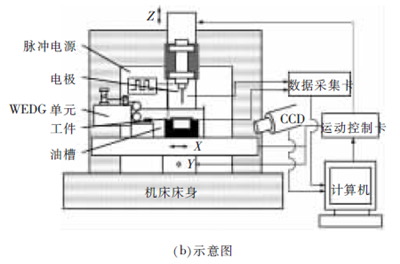
图1 微细电火花加工装置
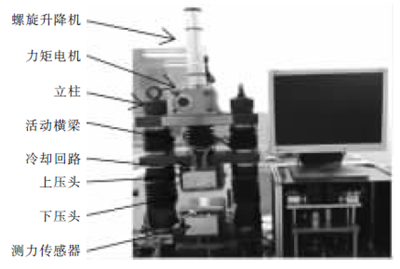
图2 热压成形机
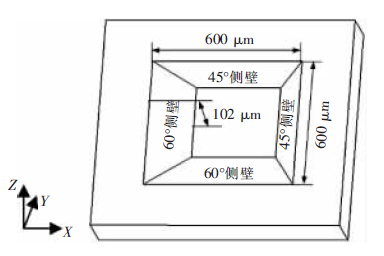
图3 模具三维模型
廓特征的影响值得研究。因此,在相同的工艺参数下,选择了不同层厚来加工模具型腔,分层厚度分别为0.5、1、1.5、2、3、4 μm。微细电火花铣削加工时的工艺参数(如开路时的扫描速度、短路的后退速度、短路电压、开路电压及插补步长等)见表1。
表1 微细电火花铣削加工条件
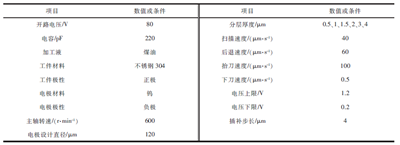
2.3 热压成形
热压成形的主要工艺参数有:保压压力、保压时间、保压温度、脱模温度,这些参数直接影响热压制品的成形质量。本试验的热压成形参数见表2。
表2 热压成形参数
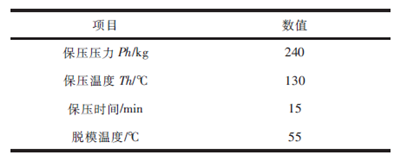
热压过程中温度、压力随时间的变化曲线见图4。热压成形法制作聚合物微器件的工艺过程为:
(1)将模具及聚合物板材加热到玻璃化转变温度Tg 以上。
(2)在保压温度Th 下,加压Ph 并保持一定的时间,使聚合物充满模具型腔。
(3)在加压的条件下,将模具和聚合物制品冷却到脱模温度(玻璃化转变温度Tg 之下)脱模。压印力一直保持到脱模时释放,是为了避免过早地释放热压压力造成热压制品的回弹及变形。
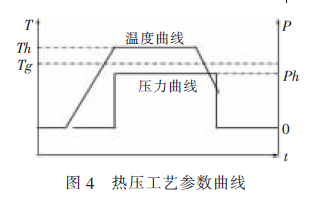
3 实验结果
3.1 模具型腔的加工结果
加工后的模具型腔SEM 扫描电镜照片见图5。由于采用分层铣削的原因,在加工侧壁轮廓表面不可避免地存在微小的台阶形误差, 分层层厚越大,台阶形误差越大(图6)。
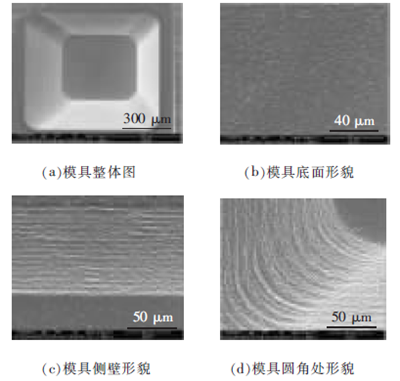
图5 模具型腔的SEM 图
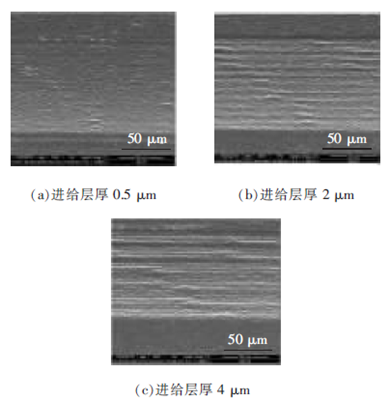
图6 不同分层厚度下的模具侧壁形貌
加工模具型腔后的工具电极见图7。可看出,基于微细电火花层层铣削原理加工后的电极端部保持不变,无明显损耗圆角。
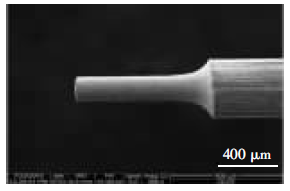
图7 微模具加工所用刀具
利用精密测量显微镜对模具进行测量,模具型腔的尺寸见表3。可见,随着分层厚度的增大,加工时间减少,效率提高。
3.2 制品成形结果
在表2 所示的热压参数下进行了5 组热压成形试验,选取其中一组表面质量较好、无明显缺陷的热压制品进行三维轮廓的测量。利用测量软件输出模具及制品对应区域的轮廓曲线,并在同一坐标下绘制两者的轮廓线。模具型腔侧壁与制品侧壁的拟合图见图8, 可见制品轮廓线与模具轮廓线基本重合,很好地复制了模具尺寸形貌。
表3 模具尺寸数据

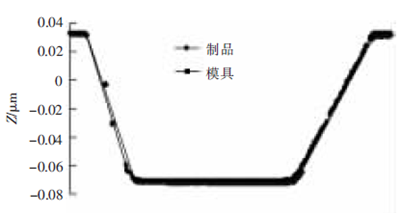
图8 模具与热压制品轮廓拟合图
热压制品的SEM 图片见图9。可以证明,在表2所示的热压参数下,制品表面轮廓复制良好。此外,从图9 还可发现,制品底面微观轮廓复制了电火花加工产生的放电凹坑,其侧壁轮廓也清晰地复制了微细电火花铣削产生的台阶形误差。
每个模具的热压制品各选3 个进行尺寸测量,并统计X、Y、Z 所有尺寸上的收缩率,求得各向收缩率的均值及上下偏差,结果见表4。可见,X、Y、Z 向的收缩率均值分别为0.380 %、0.372 %、0.373 %,由此可得热压制品各向收缩率一致,这与注塑成形塑料制品的收缩率存在各向异性[7-8]有明显区别。
3.3 热压制品与模具型腔表面关系分析
3.3.1 表面粗糙度评定参数选取
通常评价表面质量的标准大都采用轮廓算术平均偏差Ra,但其对表面微观几何形状的描述是不够完善的, 表面微观轮廓的很多信息会被平均掉。
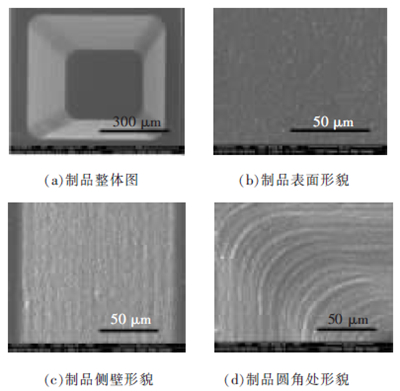
图9 制品SEM 图
因此,为了尽可能准确地表征模具及制品表面轮廓的信息,本文引入表面粗糙度参数Ra、Rpk、Rvk[9]来表征热压前、后模具及制品的表面轮廓信息。
3.3.2 制品与模具底面表面轮廓分析
利用白光干涉仪对模具热压前、后及热压制品进行三维轮廓扫描,得到其三维点云数据。由图10可知,制品表面微观轮廓与模具表面微观轮廓存在共轭关系。利用专业软件对得到的点云数据进行分析,测得模具及制品表面粗糙度数据,并进行对比分析。
表4 制品尺寸及各向收缩率
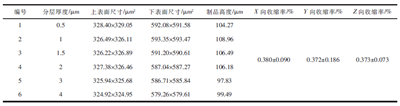
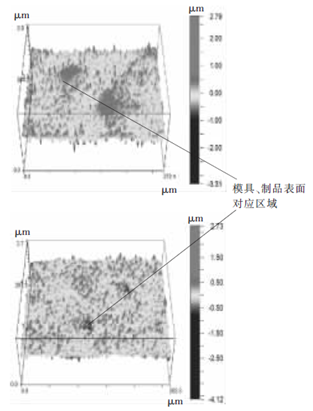
图10 模具及热压制品表面测量结果
从热压制品中选出表面完整、无明显缺陷的一组进行底面表面轮廓对比分析。利用专业测量软件对白光干涉仪获取的热压前、后模具及热压制品表面轮廓三维点云数据进行测量, 每个面各测量5次, 得到各个表面粗糙度参数Ra、Rpk、Rvk 的均值及上、下偏差。采用折线图的形式直观地将热压前、后模具表面微观轮廓与热压制品表面轮廓进行对比(图11~图13),其中,横坐标编号1~6 分别对应表3、表4 所示的编号1~6。
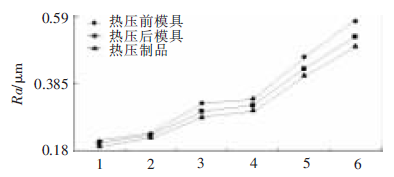
图11 轮廓算术平均偏差Ra 对比

图12 表面轮廓Rvk、Rpk 对比
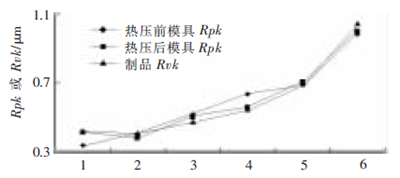
图13 表面轮廓Rpk、Rvk 对比
3.3.3 模具及制品侧壁表面轮廓分析
对模具60°的侧壁及热压制品相应表面进行了表面轮廓的测量。图14 是采用三维轮廓测量仪得到的结果,图15 是模具及制品对应侧壁的SEM 图。可得制品侧壁表面轮廓与模具侧壁表面轮廓也存在着共轭的关系。
由于制品侧壁表面质量受脱模影响较大,因此每个模具的热压制品各选3 件进行60°侧壁表面轮廓的测量。采用专业测量软件对每个制品的数据分别进行5 次测量,获得每个制品表面粗糙度参数的均值。然后,对每个模具的3 件制品的表面粗糙度参数均值进行数据处理,得到各个模具对应制品侧壁粗糙度参数的均值及上、下偏差。
热压前、后模具60°侧壁及制品相应表面轮廓算术平均偏差Ra 对比见图16。热压前、后模具60°侧壁表面Rpk 值及制品相应表面Rvk 值对比见图17。热压前、后模具60°侧壁表面Rvk 值及制品相应表面Rpk 值对比见图18。图16~图18 中的横坐标编号1~6 分别对应表3、表4 所示的编号1~6。
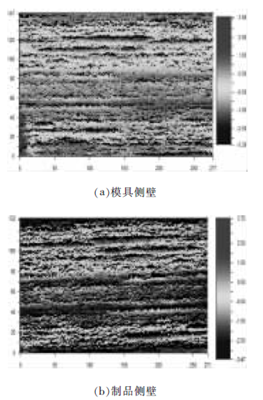
图14 模具与制品侧壁轮廓测量
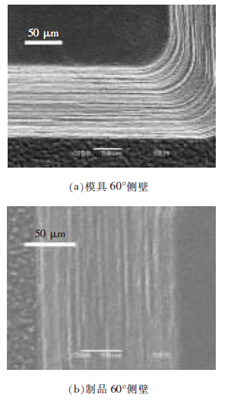
图15 型腔与制品侧壁SEM 图
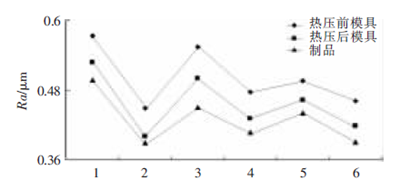
图16 侧壁表面轮廓算术平均偏差Ra 对比
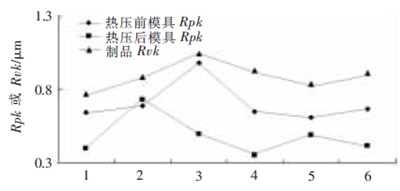
图17 热压前后模具侧壁表面轮廓Rpk 对比
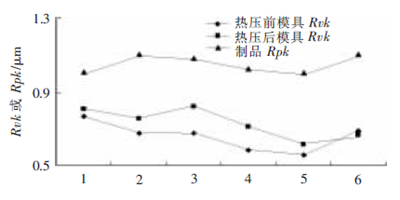
图18 热压前后模具侧壁表面轮廓Rvk 对比
4 结果分析
4.1 分层厚度对模具底面及制品相应表面轮廓的影响
由模具与热压制品的底面轮廓算术平均偏差Ra 对比(图11)可知,随着微细电火花铣削中分层厚度的增大,模具表面粗糙度Ra 值也增大。这是因为在分层去除微细电火花铣削加工中,两条相邻的电极运动轨迹之间存在切削痕迹(即刀痕,在Z 轴方向),当电极轨迹重叠率一定时,随着分层厚度的增加,刀痕残留高度也随之增加。在微细电火花铣削加工中,分层厚度的增加使加工中短路、拉弧的现象增多,加工不稳定;分层厚度减小后,表面的扫描更均匀, 放电凹坑的相互重叠使表面粗糙度Ra值减小。
在热压过程中,模具表面和热压制品间存在着接触。一方面,模具表面轮廓会复制到热压制品表面;另一方面,会使模具表面轮廓形貌改变。热压后模具底面的峰谷参数Rvk 较热压前增大,这是因为电火花加工表面由于受到瞬时高温作用并迅速冷却而产生残余拉应力,往往出现显微裂纹,其耐疲劳性能较低。由于在热压中PMMA 与模具表面存在力的作用及摩擦[10-11],而使模具表面显微裂纹扩展,表现为Rvk 增大。热压后模具底面表面轮廓算术平均偏差Ra 及峰高参数Rpk 有减小的趋势, 这与热压过程中PMMA 与模具表面的摩擦及相互作用力有关。
热压制品与模具表面轮廓存在共轭关系,热压制品的表面粗糙度Rpk 与模具表面粗糙度Rvk 对应,热压制品的表面粗糙度Rvk 与模具表面粗糙度Rpk 对应(图12、图13)。由于PMMA 的收缩及回弹特性, 热压制品的表面Ra 值较热压前后模具表面都减小;热压制品表面Rpk 比热压后模具表面Rvk小,两者变化的走势相同;制品表面Rvk 的变化趋势也与热压后模具表面Rpk 的变化趋势相同。
4.2 分层厚度对模具及制品侧壁表面轮廓的影响
由图16~图18 可看出,分层厚度的大小对模具侧壁表面粗糙度Ra、Rpk、Rvk 无明显影响。热压后模具侧壁表面轮廓发生变化,其中,Ra、Rpk 有减小的趋势,Rvk 有增大的趋势。这是因为在热压成形过程中,PMMA 与模具侧壁表面作相对运动时, 由摩擦导致模具表面微凸峰磨损,表面轮廓发生变化。热压制品侧壁表面与模具侧壁表面存在着复制的关系, 且两者侧壁表面粗糙度的变化趋势相同。由于PMMA 的收缩、回弹特性及脱模过程中存在的摩擦力, 导致热压制品侧壁表面粗糙度Ra 值较模具侧壁小。在制品脱模的过程中,制品侧壁与模具侧壁的摩擦力大,作用时间长;此外,脱模方向轻微的偏斜会导致摩擦力迅速增大,使制品侧壁局部出现破裂。因此,热压制品侧壁峰高参数Rpk、峰谷参数Rvk 较热压后模具侧壁Rvk、Rpk 要大。
5 结论
本文通过实验研究了微细电火花三维铣削加工中,分层厚度对模具型腔侧壁、底面的表面质量的影响,并分析了热压成形中,模具表面轮廓的变化及制品与模具型腔的复制关系,得到以下结论:
(1)在放电参数与电极轨迹重叠率一定时,随着分层厚度的增加,模具型腔底面表面粗糙度值也增大。在分层厚度较大时,应当增加刀具轨迹重叠率,以使底面轮廓扫描得更均匀。
(2)分层厚度对模具侧壁表面粗糙度Ra、Rpk、Rvk 没有明显影响。在对侧壁台阶形误差无严格要求的情况下, 适当地增大分层厚度可提高加工效率,且不会改变制品侧壁表面粗糙度大小。
(3)热压前、后,模具底面及侧壁表面轮廓发生变化, 表现在表面粗糙度参数值Ra、Rpk 减小及Rvk 增大。
(4)热压制品的表面轮廓与模具表面轮廓存在着复制的关系,但又有不同。热压制品底面表面粗糙度值Ra、Rpk、Rvk 较热压后模具底面粗糙度值Ra、Rvk、Rpk 小;制品侧壁表面粗糙度值Ra 较模具侧壁粗糙度值Ra 小, 而制品侧壁表面粗糙度值Rpk、Rvk 则大于模具侧壁粗糙度值Rvk、Rpk。
投稿箱:
如果您有机床行业、企业相关新闻稿件发表,或进行资讯合作,欢迎联系本网编辑部, 邮箱:skjcsc@vip.sina.com
如果您有机床行业、企业相关新闻稿件发表,或进行资讯合作,欢迎联系本网编辑部, 邮箱:skjcsc@vip.sina.com
更多相关信息