微细电火花制备大长径比微细电极的工艺研究术
2017-1-3 来源:哈尔滨工业大学机电工程学院 作者:孟洁,白基成,李强,曹剡
摘要:针对电火花块电极磨削效率高和线电极磨削精度高的优点,采用块电极磨削为微细电极的粗磨削、线电极磨削为微细电极的中、精磨削方式,对大长径比微细电极的制作技术进行研究。通过分析微细电火花加工大长径比微细电极的影响因素,对影响大长径比微细电极制作的加工参数进行了大量的工艺试验,得到各参数对微细电极制作的影响规律,优选得到相关的大长径比微细电极的加工参数,并进行了实验验证。
关键词:微细电火花;微细电极;块电极磨削;线电极磨削;大长径比
O. 引言
随着微机电系统的发展,对微型结构的零部件需求量越来越大。目前,加工微型结构的方法很多,其中微细电火花铣削加工技术以其非接触式加工、不受材料硬度限制等优势成为加工微型结构的一种重要方法。采用微细电火花铣削技术加工具有微型腔、微小孑L以及阶梯孔等微型结构的零部件,需要制备直径很小的微细电极;另一方面,在微细电火花铣削加工中,微细电极的损耗非常严重,微细电极的长度在很大程度上影响了铣削的加工效率,而且微细电极的精度也会影响型腔或者孔的精度,因此需要制备大长径比微细电极。
目前国内外很多学者对微细电极的制作有相关的研究。日本学者增泽隆久采用线电极磨削装置加工出直径为2.轧m的微细轴?。韩国首尔大学的Se HyunAhn等人利用微细电解方法加工出直径为3mm,长度为4mm的微细电极旧J。美国学者Ra’a A,Said在cu.S04·5H:O溶液中用玻璃绝缘铂电极的侧壁加工出直径为2轧m,长为6.5mm的铜微细电极‘3』,但是加工效率低,表面质量不理想。哈尔滨工业大学李刚通过采用块电极粗加工,刃口电极精加工相结合的方法,加工出直径3.5肛m,长度为60灿m的微细电极,但刃口电极的制作和安装限制了其发展H J。S.H.Choi等人采用电火花光刻法通过光致抗蚀剂掩模成功加工电极直径为轧m,长度为3mm,带有O.2。锥度的大长径比微细电极。
由于存在二次安装误差,采用电解或者光刻法等方法加工的微细电极,无法作为微细电火花铣削加工用的工具电极。因此,对于研究采用微细电火花技术在线制作高精度的大长径比微细电极的技术具有重要意义。
1.微细电极的制作方法
目前微细电极的制作方法总体分为离线制作和在线制作两种。离线制作方法有通过冷拔得到金属细丝,或者通过切削、磨削等方法哺]。通过冷拔得到的金属丝会出现直径不一致等缺陷,而通过切削或磨削得到的电极精度会受到很明显的切削力影响。另外,离线制作的电极再次安装时会产生二次安装误差,重复定位误差o¨等问题,使经过二次安装的微细电极无法用于微细电火花铣削加工。在线制作微细电极的方法有电火花块电极磨削(Block Electrical Discha略e Grind—ing,简称BEDG)、线电极磨削(wire Electrical Discha昭e Grinding,简称wEDG)、块电极磨削和线电极磨削相结合的方式(BEDG-wEDG),刃口电极电火花磨削方法等。
块电极磨削电极时,块电极与微细电极之间的放电面积大,加工效率比较高。但是块电极的工作面与工作台台面存在垂直度误差和块电极本身存在平面度误差,导致加工的电极产生锥度,尺寸不易控制,所以仅采用块电极磨削电极很难达到大长径比的目的。线电极制作微细电极时,待制作电极与线电极之间是点放电,每次放电点比较集中,且脉冲能量小,蚀除的工
件材料很少,使加工效率比较低,但加工精度高。因此将BEDG和wEDG相结合作为大长径比微细电极的制作方法。
另外,影响大长径比微细电极在线制作的因素有很多,主要包括:
(1)电极材料
采用电火花加工技术在线制作微细电极时,待制作的微细电极材料应该具有导电性、自身较小的损耗、不易加工成形以及高熔点等特征。钨熔点很高,且化学性质较稳定,目前微细电极的材料趋向于钨材料,有利于大长径比微细电极的制作。
(2)工作液
工作液主要起冷却、排屑、形成放电通道以及压缩放电通道等作用。煤油的绝缘性比去离子水好,有利于提高加工精度,但煤油中分解的含碳化合物会产生二次放电,使加工状态不稳定,且煤油的传热性能以及排屑功能差。相比于煤油,去离子水流动性和传热性好,有利于排屑和散热一1;且去离子水可使加工效率高,加工工件的表面形貌好,所以去离子水更有利于大长径比微细电极的制作。
(3)加工极性
由于待加工微细电极直径较小,所需脉冲能量小,脉宽很窄,频率很高。当加工工件接正极时,加工工件的蚀除量远远大于工具电极的蚀除量,有利于提高加工效率和降低工具电极的损耗。
(4)脉冲电源
制作大长径比微细电极时,因为电极尺寸微小,磨削量较大,同时需要保证磨削的加工效率,因此作为微细电火花加工重要部分的脉冲电源,需要能够同时实现具有微小能量和大能量相结合的多功能脉冲电源,同时脉冲电源的不同参数对微细电火花铣削加工具有较大的影响。
常用的微能脉冲电源的电源模式主要有可控电容电源模式(简称TC电源模式),RC电源模式以及可控电阻电源模式(简称TR电源模式)。TR电源模式能够提供很高的脉冲频率,加工效率较高;Rc电源模式工作可靠,结构简单,且加工效率比TR的高;而TC电源模式下电流波动较大,材料蚀除不均匀,使电极表面质量和直径一致性比较差,但是加工效率比前两者都高。所以在块电极粗磨削时采用Tc电源模式,线电极中磨削时采用RC电源模式,精磨削时采用TR电源模式。
(5)加工参数
影响电极制作的加工参数很多,如伺服进给速度、进给方式、加工方法等,也会在很大程度上影响电极加工的效率和质量。一般情况下,所选的加工参数需使加工效率高、电极表面形貌好、加工状态稳定。下面主要针对电火花加工技术在线制作大长径比微细电极的电参数进行试验研究,以优选出适合制作大长径比微细电极的参数。
2.试验方案及试验条件
本文研究所采用的试验设备是哈尔滨工业大学特种加工及机电控制研究所自行研制的微细电火花机床,该机床集在线制作电极、电极在线测量、微细阵列型腔铣削加工于一体。
(1)试验方案
本文采用块电极磨削装置进行电极的粗磨削,旨在提高加工效率;用线电极磨削装置进行中磨削和精磨削,中磨削的目的是进一步减小电极径向尺寸,并为精磨削作准备,精磨削主要是提高电极表面质量,保证加工精度。另外因块电极加工时会产生损耗,为了减小块电极损耗对加工电极的影响,一般采用块电极进行两次粗磨削;为了便于根据加工后的电极直径、表面质量以及加工需求确定下一工序的具体加工参数,对应的线电极在中磨削和精磨削时也进行两次磨削。
(2)试验条件
本文针对影响块电极粗磨削和线电极中、精磨削大长径比电极的电参数进行多次工艺试验,选择出适合大长径比微细电极制作的最佳参数,并通过实验验证所选的加工参数,试验过程中所使用的试验条件如表1所示。
表1制作微细电极的试验条件
biao 1
3.大长径比微细电极制作的工艺试验研究
块电极粗磨削电极时采用TC电源模式,影响电极磨削的电参数有开路电压、脉冲宽度、占空比以及电容等,因为块电极磨削旨在提高加工效率,其加工参数以表2为准,该参数是已经通过大量实验验证过,此处没有必要研究。下面主要对线电极磨削电极进行研究。
3.1线电极中磨削时的工艺试验
线电极中磨削微细电极主要为了进一步减小电极直径,并具备一定的表面质量,为精磨削做准备。此时采用RC电源模式。通过对开路电压、电容、电阻进行单因素试验研究,分析各个因素对微细电极直径以及表面形貌的影响规律,进而确定制作大长径比微细电极的最佳参数。
(1)开路电压对加工电极的影响
以线电极第一次中磨削为例,加工所需的脉冲能量应比粗磨削时小。加工前的电极直径为10咄m,电阻、电容分别取100Q、1000pF,电极径向进给量为10灿m,而其他加工参数不变的情况下只改变开路电压。在对应的每个开路电压下,磨削长度为10毗m,结果如图l所示。
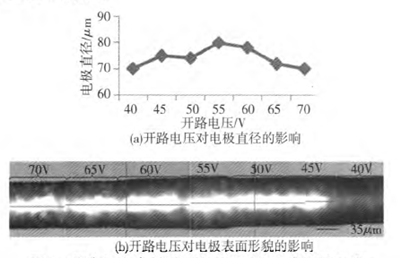
图1线电极中磨削时开路电压对加工电极的影响
从图la可明显地看出,在所选试验条件范围内,线电极中磨削时,当开路电压小于55V时,脉冲能量比较小,加工时易出现短路,导致电极直径减小;当开路电压大于55V时,微细电极的直径随着开路电压的增大而减小。但脉冲能量增大,蚀除凹坑变大,表面质量变差,如图1b所示。综合加工效率和表面质量,优选60V作为中磨削的开路电压。
(2)电阻对加工电极的影响
以线电极第一次中磨削为例,加工前的电极直径为8毗m,在开路电压为60V,电容为1000pF,电极径向进给轧m而其他加工参数不变的情况下只改变电阻。在对应的每个电阻下,磨削长度为15毗m,结果如图2所示。
从图2可以看出,在所选的电阻条件范围内,电阻值大时,电流小,蚀除的工件材料较少,电极直径变化小,但蚀除凹坑小,电极表面质量好。当电阻为100Q时,加工状态不稳定,易发生短路现象。所以选择510n为中磨削的电阻值。
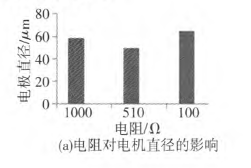
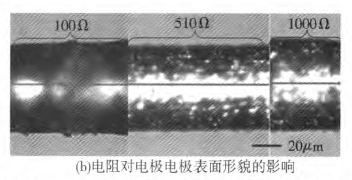
图2线电极中磨削时电阻对加工电极的影响
(3)电容对加工的影响
以线电极第二次中磨削为例,加工前的电极直径为3轧m,当开路电压取60V,电阻取510Q,电极径向进给靴m而在其他加工参数不变的情况下只改变电容。在对应的每个电容档下,磨削长度为12毗m,结果如图3昕示。
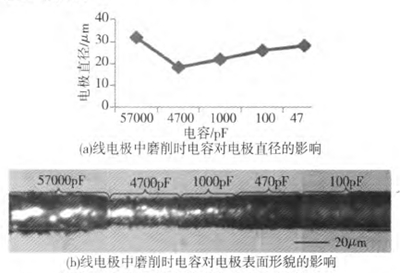
图3线电极中磨削时电容对电极的影响
从图3可以看出,在所选电容条件范围内,除了57000pF点,电极直径随电容数值的减小而增大,其主要因为电容减小,脉冲能量减小,单位时间内蚀除的材料减少,且放电间隙减小,废屑不能及时排出,使电极直径增大,而电容在57000pF和4700pF下加工的电极表面形貌差。所以在中磨削时优选1000pF为电容参数。
3.2线电极精磨削时的工艺试验
经过线电极第一次精磨削后,电极尺寸已经很接近目标尺寸,为了进一步提高电极表面质量,提高加工精度,进行线电极第二次精磨削。此时采用加工电极径向“零进给”¨0|,线电极“零运丝速度”以及主轴“非伺服运动”等加工策略。在线电极精磨削电极时采用的是TR电源模式,主要是精修电极的表面质量,所以所需能量很小。以下主要对开路电压、电阻以及脉宽和占空比进行工艺实验,分别研究它们对电极直径和电极表面形貌的影响。
(1)电阻对加工的影响
以线电极第一次精磨削为例,所需的脉冲能量很小,且加工时径向进给量很小,重在提高表面质量。当加工前的电极直径为4轧m,开路电压为28V,脉宽为3200 ns,占空比为1:3,电极径向进给钆m而其他加工参数不变的情况下只改变电阻,在对应的每个电阻下磨削长度为12毗m,结果如图4所示。从图4可以看出,在试验所选数据范围内,电极直径随电阻值的减小而减小,因电阻减小,电流增大,单位时间内蚀除的工件材料就增加,电极直径变小,但蚀除凹坑会变大,导致加工质量变差。所以优选1000Q为精磨削的电阻参数。
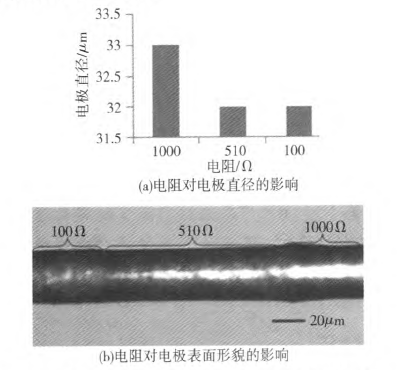
图4线电极精磨削电极时电阻对加工电极的影响
(2)开路电压对加工的影响
以线电极第二次精磨削电极为例,经过线电极第一次精磨削的修整,电极表面有很大的改善。为进一步提高表面质量和直径一致性,进行线电极最终精磨削。为了避免线电极振动对电极直径一致性的影响,将运丝速度设为零,而且在检测到有放电现象时,电极径向不进给,即径向零进给,其余加工参数和第一次精磨削时的相同。如图5所示上下分别为采用28V和24V电压精磨削加工的电极表面形貌,可以明显地看出在24V时加工的电极表面形貌比28V要好。所以在线电极第一次精磨削时选用28V的开路电压,在提高加工效率的情况下,保证加工精度;在第二次精磨削电极时选取24V的开路电压,以进一步提高电极表面质量。
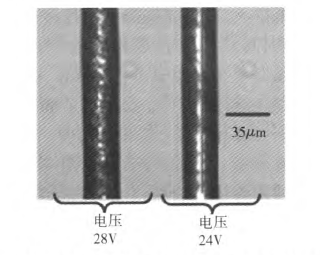
图5不同电压下精磨削的电极表面形貌
(3)脉宽及占空比对加工的影响
用线电极精磨削电极时,脉宽以及占空比也是影响微细电极制作的影响因素,以第一次精磨削为例,加工前电极直径为10钆m,在开路电压为28V,电阻为1000Q,电极径向进给量为轧m,以不同的脉宽和占空比做实验,结果如图6所示。从图6可以看出,在试验所选条件范围内,占空比不变时,电极直径随脉宽的增大反而增大,原因是在脉宽为3200ns时,加工能量较小,加工时出现轻微短路现象,使电极直径更小;当脉宽不变时,电极直径随着占空比的减小基本呈增大趋势。因精磨削时重在提高微细电极表面质量,在保证无明显短路的前提下,尽量使加工能量小,蚀除凹坑小,达到表面质量好的目的。所以选择脉宽为3200ns,占空比为l:3作为精磨削电极的参数。
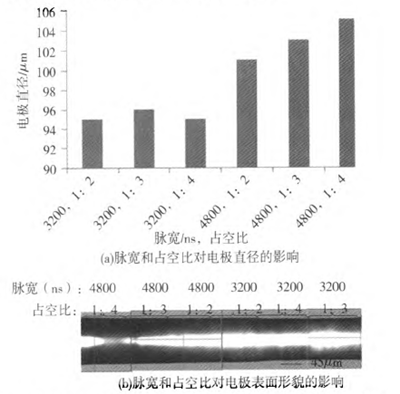
图6线电极精磨削电极时脉宽和占空比对加工电极的影响
经过多次试验研究,总结出制作单根大长径比微细电极的具体加工工艺规划,如表2所示。经过试验,验证,依据表2的加工参数,稳定地加工出直径为4μm,长度120μm以及直径为7μm,长度为440μm的大长径比微细电极,其长径比高达60以上,且直径偏差小于1μm,如图7和图8所示。
表2微细电极的加工工艺规划及参数
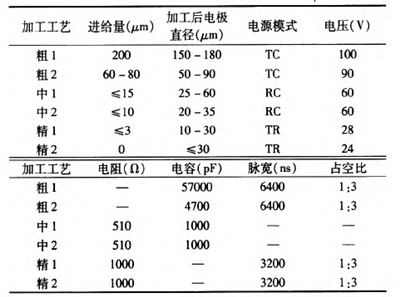
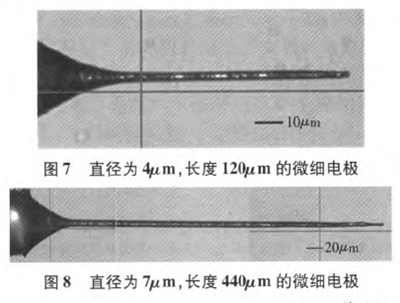
4.结论
本文主要研究了采用微细电火花技术制作大长径比微细电极的方法,通过理论分析和试验研究,得出了以下结论:
(1)根据块电极电火花磨削和线电极电火花磨削的特点,利用多模式微能脉冲电源,采用块电极磨削装置进行电极的粗磨削,线电极磨削装置进行中磨削和精磨削的大长径比微细电极加工方法,并分析、总结了相应的的加工方案和加工条件;
(2)通过大量试验研究了在线电极磨削电极时开路电压、电阻、电容、脉宽以及占空比等对电极直径和电极形貌的影响规律,获得了适合大长径比微细电极制作的优选参数;
(3)通过实验验证,使用该优选参数稳定地加出了电极直径为7μm,长度440μm以及直径为4μm,长度为120μm的大长径比微细电极,长径比高达60以上,且直径偏差小于1卢m,达到了直径小、长径比大的预期效果。
投稿箱:
如果您有机床行业、企业相关新闻稿件发表,或进行资讯合作,欢迎联系本网编辑部, 邮箱:skjcsc@vip.sina.com
如果您有机床行业、企业相关新闻稿件发表,或进行资讯合作,欢迎联系本网编辑部, 邮箱:skjcsc@vip.sina.com
更多相关信息