往复走丝电火花线切割加工技术发展瓶颈及研究思路
2016-12-21 来源:南京航空航天大学机电学院 作者:刘志东
摘要:分析了当前往复走丝电火花线切割机床在高效切割、解决丝耗、导丝定位等方面遇到的技术瓶颈,提出了相应的解决思路。对于高效切割,关键问题是要解决大电流加工条件下工作液在极间迅速汽化的问题;对于丝耗问题,提出了一种往复走丝渐进送丝的新走丝方式;对于电极丝导丝问题,认为采用非强制间隙约束方式是导丝器的发展方式。
关键词:往复走丝;电火花线切割加工;发展瓶颈;研究思路
具有中国自主知识产权的往复走丝电火花线切割机床自20 世纪70 年代步入市场后,以其很高的性价比为模具加工市场所接受,目前已成为机械加工领域不可替代的加工手段,且其应用领域在不断拓展,技术水平也在不断提升,并正在逐步为世界各国所接受[1,2]。近十几年来,伴随着具有多次切割功能的往复走丝电火花线切割机床(俗称“中走丝线切割机床”)的发展,往复走丝线切割加工技术获得了长足的进步, 但由于其自身的加工特点,目前遇到了如高效切割、电极丝损耗处理及导丝持久性等一系列技术瓶颈。本文的目的在于针对这些问题,从放电加工机理方面加以分析,为业内的研究人员提供一个解决问题的参考思路。
1.往复走丝的“非对称性”加工特点
往复走丝电火花线切割加工虽然冠以往复的名称,但在往复走丝的加工过程中,由于受到重力的作用,从微观角度而言,其加工过程中的冷却、排屑及消电离均是非对称过程, 因此其加工始终是“非对称”的,也即走丝形式上的对称由于遭遇到重力的影响而被改变,从而显示出了正反向走丝时各自差异的特性。这种“非对称”的特征在高效、小参数精加工及高厚度切割时体现的尤为明显,主要体现在切割表面在工件的上下端面表面质量包括烧伤情况(图1)不同甚至会影响到切割的精度;在正反走丝时也会因为切割稳定性不同导致进给速度的不同;切割过程中电极丝张力会逐渐出现单边松丝[3]等问题。因此在细化研究往复走丝切割时,应该针对其“非对称”加工的观点,通过改变正反向走丝时的高频电源参数、伺服跟踪速度、走丝速度等来达到提高正反走丝加工工艺指标均匀性和一致性的目的,如果再考虑到切割方向不同导致的因导轮对电极丝定位的影响,这个问题将更加复杂。
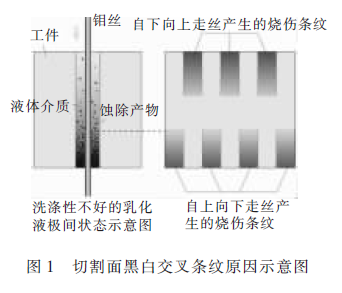
2.往复走丝的技术瓶颈问题
2.1 高效稳定切割
往复走丝电火花线切割加工的工艺指标尤其是切割效率在解决了极间冷却的指导思想、经历了从20 世纪80 年代至21 世纪初的沉寂后, 目前已有了质的提高。但由于其自身往复走丝的特点,使其切割精度不可能与单向走丝电火花线切割加工进行最终的抗衡,其良好性价比的一个重要体现在于能进行高效、长期稳定的切割加工,尤其体现在高厚度切割方面,因此对于往复走丝线切割加工而言,切割效率的提高及持久性是一个永恒的话题。往复走丝线切割加工效率方面的研究重点可分为两方面:其一是提高实用的、持续稳定的切割效率,目前持续稳定的效率已达120~140 mm2/min,今后努力的目标希望能达到160~180 mm2/min,且对于150 mm 以上厚度的工件也同样适用; 其二是提高最高切割效率,目前采用智能脉冲电源,配合复合工作液,最大切割效率已达300 mm2/min。上述指标已接近或达到中档单向走丝线切割加工的一般效率要求,但运行成本仅仅是单向走丝线切割加工的几十分之一甚至百分之一[4],因此在中小批量零件的切割生产中具有十分明显的优势。
但必须注意的是:往复走丝线切割加工当切割效率超过150 mm2/min 后, 工件表面将逐渐产生严重的交叉烧伤痕迹,其最根本的原因还是高效切割时极间放电状况恶化所致。图2a 为极间有充足工作液的切割示意及工件切割后表面情况,此时切割表面色泽基本均匀,但如持续增加放电能量(平均加工电流>6 A)至效率超过150 mm2/min 后,切割效率随着放电能量的增加将上升十分缓慢,而工件表面烧伤则更严重,且电极丝断丝几率大大升高(图2b)。此时导致切割效率的提高又遇到另一个瓶颈。工件表面出现严重的交叉烧伤痕迹,说明极间处于十分恶劣的放电状态,其主要问题在于随着放电能量的增加,放电形成的热量将使得电极丝带入切缝(单边放电间隙约0.01~0.02 mm) 的有限工作介质瞬间汽化,导致极间尤其是在电极丝出口区域处于工作介质很少甚至无工作介质状态,致使该区域的冷却、洗涤、排屑及消电离状态恶化。由于工件和电极丝在该区域得不到及时的冷却, 造成排屑困难,从而使工件表面产生严重烧伤且断丝的几率大大增加。在此种加工条件下,任何对于高频电源的改进措施及伺服控制策略对于切割工艺指标的提高都将收效甚微,因为此时最关键问题已转化为极间放电状态的恶化及不稳定,所以如何能及时将工作介质带入放电间隙并将蚀除产物排出切缝已成为能否进一步提高切割效率的首要前提。
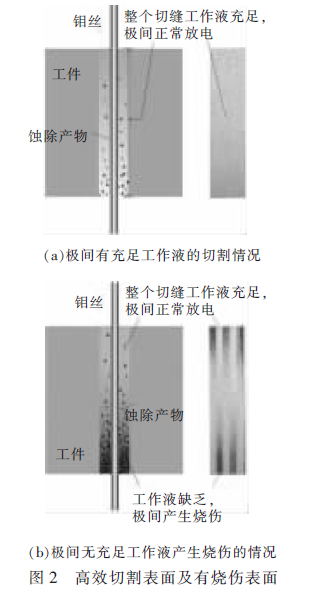
下面分两个部分来论述提高切割效率的途径。一方面为在洗涤冷却较充分前提下(一般切割电流<5 A),提高单位电流蚀除效率;另一方面是在大能量加工前提下(一般切割电流>6 A)提高高效切割效率。
(1)在洗涤冷却较充分前提下(一般切割电流<5 A),提高单位电流蚀除效率的主要措施:
① 进一步提高脉冲电源的脉冲加工利用率。目前一般的脉冲取样伺服进给配合佳润复合工作液的使用,可使脉冲电源的放电脉冲利用率接近甚至超过90 %,而采用智能化的脉冲电源可结合放电间隙状态的检测、等能量脉冲电源(图3)的应用、放电能量的控制及有害脉冲的抑制等技术,在进一步降低电极丝损耗的同时,提高放电脉冲的利用率至95%以上;同时由于抑制了有害脉冲的输出(如一旦检测出现持续短路情况就及时切断脉冲电源), 可使单位电流的切割效率从25~30 mm2/(min·A) 上升至30~35 mm2/(min·A)。但客观而言,在洗涤、冷却较充分前提下, 智能电源对切割效率的提高贡献限,研究的重点主要在电极丝使用寿命的提高方面。
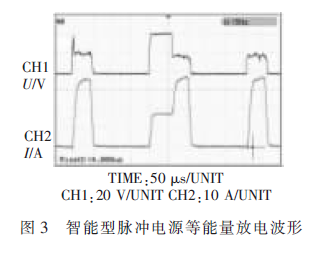
② 对脉冲蚀除方式的研究。放电后工件表面材料的蚀除形式主要有热熔化蚀除和热气化蚀除两种,业内对于往复走丝线切割加工脉冲能量蚀除方式的研究仍处在一个模糊阶段。蚀除方式不仅与蚀除效率有关,还与加工表面的完整性、电极丝的损伤程度等一系列指标有关,是一个值得深入研究的课题。
③ 工作液性能的进一步研究。目前以佳润复合工作液为代表的工作液主要解决了平均切割电流<5 A 条件下极间的洗涤、冷却及消电离问题,使极间处于正常的放电状态[5-7],而切割效率的提高还有一个重要的因素就是单个脉冲的放电蚀除量问题,该问题与放电后能量在极间的传输、热量的扩散等因素有关。鉴于上述机理,工作液应具有更低的电导率,以减少在放电过程中漏电流的能量损失,同时应具有较高的动态粘度, 以有利于压缩放电通道,使放电能量集中,达到高效蚀除材料的目的,此外还应具有较高的气化点,以减少极间工作介质的气化量。
④ 张力控制问题。张力的控制并不能直接获得加工效率的提升, 但可通过改善加工的稳定性、提高切缝的均匀性获得切割效率的提高。图4 是检测到的一般加工区电极丝张力与丝筒转速对应图。从图中可看出电极丝正反运行时张力的变化是十分明显的,出现一边松一边紧的问题,且换向时导轮的转动惯量会造成张力的突变[8]。电极丝正反走丝张力的变化会导致切割中电极丝的振动加强,并产生切缝宽度变宽及不均匀,因此如果能解决电极丝张力不均匀问题,将使放电脉冲利用率进一步提升且切缝宽度均匀及收窄,从而能从这方面获得因为切缝材料蚀除量降低所带来的切割效率的提高。
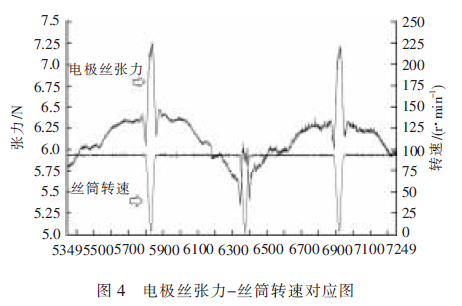
⑤ 电极丝进电问题。目前最常用的电极丝进电方式是导电块进电,导电块由硬质合金或钨钢材料制造,钼丝以8~12 m/s 的线速度贴着导电块表面滑动摩擦运动,两者接触处为一个短圆弧线段。由于钼丝与进电块之间的接触电阻不稳定,放电能量传输到加工区域必然因为有接触电阻及电极丝自身的电阻产生能量损耗。如能尽可能将进电点移动至靠近加工区域(图5 所示虚线框位置),减少能量消耗并尽可能获取更接近于加工区域的取样信号(通常取样点和进电点在一起), 将由此获取加工效率的进一步提高。
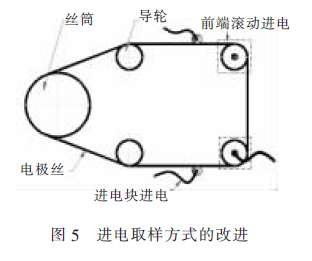
(2)大能量前提下(一般切割电流>6 A)提高高效切割效率问题:
在大能量前提下(一般切割电流>6 A)提高高效切割效率关键在于如何解决工作液在极间迅速被汽化[9]的问题,为此采用的主要措施可分为增加极间工作液的进入量的主动措施及减少极间工作液的汽化量的被动措施。
主动措施有:
① 增加喷液压力及放电间隙。以往往复走丝均采用浇注式冷却,基本是通过工作液吸附在电极丝上并随着电极丝带入切缝,而实验表明,采用一定压力将工作液喷入切缝,可将工作液尽可能多地带入切缝[7],但前提是,必须研制一种不产生泡沫的工作液, 以防止在高压喷射条件下形成大量的泡沫,影响加工的稳定性,且采用这种方式还须借助脉冲电源的改进,以增加放电间隙的宽度。
② 电极丝的外观形状及材料的改变。通过电极丝外观形状的改变,如采用绞合、螺旋形状的电极丝或使电极丝表面具有更好的吸附工作液性能,如毛化电极丝表面,使电极丝能将更多的工作液带入极间,同时带出更多的蚀除产物,其中双绞合电极丝示意如图6 所示。
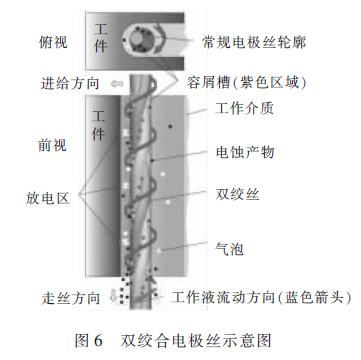
绞合电极丝在走丝过程中可通过自身螺旋状容纳空间及走丝时形成的对液体介质的螺旋吸入效应,尽可能多地“拖拽并吸入”外部及已加工切缝中的工作介质进入放电间隙,同时及时将蚀除产物“强制拖拽”出放电间隙,以提高高效切割时极间的冷却、洗涤、排屑及消电离作用。由于洗涤、冷却、排屑及消电离作用大大增强,尤其是强制性“拖拽并吸入”更多的工作介质,将使极间获得充分的冷却环境,解决极间因为高效切割产生的工作介质瞬间气化问题,使电极丝能获得及时冷却,从而承载更大的加工能量,提高切割效率。
被动措施有:
① 工作液方面, 在保障极间处于良好洗涤、冷却、消电离的条件下,使工作液具有更高气化点的组分,以减少工作液在极间的气化量,此外还可增加工作液在电极丝表面的吸附性能,让电极丝能尽可能多地将工作液带入切缝。
② 设计并采用使工作液气化率低的脉冲电源及参数,增大放电间隙,并采用“非对称”脉冲电源。脉冲电源在一个脉冲期间的能量分配及脉冲间隔分配均会导致对工作液产生不同的汽化率,且在正反向走丝时采用不同的脉冲间隔均会在一定程度上减少往复走丝的“非对称性”。
目前从实施的可行性而言,改变电极丝的截面外观以提高高效切割效率可行性较强,但电极丝截面形状的改变还需解决电极丝应力、变形、电极丝直径控制等问题。
3.电极丝损耗的解决途径
现有的往复走丝线切割加工由于采用单丝筒循环往复走丝,必然会产生以下缺陷:
(1)贮丝筒通常一次上丝的长度为200~300 m,由于这段电极丝一直在进行往复放电切割,电极丝产生损耗是必然现象。目前采用佳润复合工作液,以100 mm2/min 的切割效率连续切割时,切割15 万mm2,电极丝直径损耗0.01 mm(从直径0.18 mm 开始)。因此在大面积切割时,将由于电极丝的损耗导致起始切缝与最终切缝因为电极丝损耗而产生宽度不同,对切割精度形成影响。
(2)在大面积切割过程中一旦发生断丝,由于此时电极丝已从开始到断丝处有了损耗,如果采用通常的退回原起割点、重新换钼丝再进行切割的方法,从起割点到断丝点,就会因为切缝宽度逐渐变窄的原因(暂时不考虑工件变形及轨迹精度等问题),影响电极丝从起割点到断丝点的进给速度,也就是说, 此时从起割点到断丝点并不是空切了,而是需要再次切割才能到断丝点,这样就会大大延长总切割时间并影响加工精度。
(3) 传统的往复走丝线切割加工在走丝过程中,存在单边松丝问题,也就是在丝筒的两头,存在电极丝一头松一头紧的问题,虽然目前采用的恒张力装置(如机械重锤式张力机构、机械弹簧式张力机构等)可部分缓解该问题,但同时也会增加断丝的几率。
(4)电极丝的损耗会影响到多次切割修整的精度。
为解决上述问题,目前已有厂家在控制系统中采用软件补偿方法来弥补切割中因为电极丝损耗带来的切缝宽度改变产生的误差[10],也有厂家采用丝筒上电极丝分段投入加工的方法,如一次切割用丝筒上的一段电极丝,而多次切割,为减少因电极丝损耗对修整的影响,采用另外一段没有损耗的电极丝进行修整,但上述方法都不能完全解决电极丝损耗带来的对加工精度的影响。
目前由于电极丝冷拉工艺的日趋完善,钼丝在冷拉过程中,可按定长拉制。由此提出一种电火花线切割双丝筒电极丝往复渐进式走丝方式(已申请发明专利), 通过双贮丝筒使得电极丝在完成高速往复走丝的同时通过往复走丝的不对等控制,使电极丝整体微量推进,以抵消电极丝的损耗,从而使电极丝的损耗在整个切割过程中可通过电极丝的渐进补充而抵消,保障在切割过程中,切缝中的电极丝直径基本不变。在一定程度上保障了加工精度不会因为电极丝的损耗而降低,此外当断丝情况发生时电极丝可沿宽度一致的切缝快速空切到断丝点或在断丝点原地穿丝。该双丝筒结构同时保障了加工区域电极丝的张力处于恒定状态。电火花线切割电极丝往复渐进式走丝方式原理见图7。
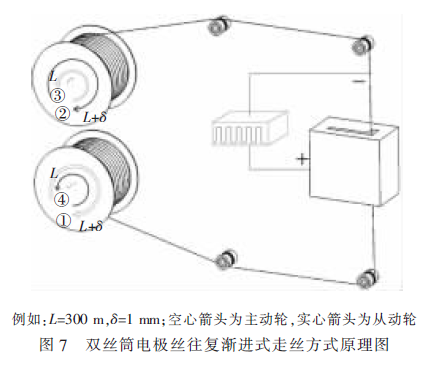
利用单片机控制贮丝筒的转动,实现电极丝的往复渐进式送丝运动,例如:正向走丝300.001 m 后反向收丝300 m, 再正向走丝300.001 m 后反向收丝300 m……如此往复运动, 每次循环总有1 mm的新丝补充进入加工区域,因而电极丝的损耗可依靠每次多进入加工区域的1 mm 电极丝来补偿,以减少加工过程中的电极丝损耗,尤其对于切割高厚度和大切割面积的工件效果更为明显,从而提高加工精度。且当断丝现象发生时,电极丝可沿宽度基本一致的切缝快速空切到断丝点或在断丝点原地穿丝,大大提高了加工效率。采用这种走丝方式后,由于电极丝损耗可依靠渐进进入加工区域的电极丝进行补偿,故损耗对加工的影响程度大大降低甚至可以忽略,因此诸如在单向走丝上适用的技术也可考虑在往复走丝上采用,如抗电解电源技术等。采用这种走丝方式,能基本消除以往电极丝损耗对加工的影响,当然目前这只是一个构想,具体结构及控制的实现还需进一步细化。
4.导丝方式问题
对于往复走丝线切割加工而言,往复走丝导致的对电极丝空间位置的影响是较大的,因此采用导丝器对电极丝进行定位和导向是目前“中走丝机床”普遍采用的方法。但导丝的方式决定了导丝器的精度和寿命。由于电极丝的反复使用及钼丝的硬度大大高于单向走丝线切割加工黄铜丝的硬度,因此在导丝器材料相同时,往复走丝线切割加工导丝器的使用寿命将大大低于单向走丝线切割加工,其对比情况见表1。
表1 往复走丝与单向走丝线切割加工导丝器寿命比较

由表1 可知,往复走丝线切割加工会大大降低导丝器的寿命, 因此其导丝方式只能以“减少电极丝抖动”为主要手段,如果硬要靠导丝器强制性牵拉电极丝以达到限位的作用是不现实的,这也就是为什么目前“中走丝”导丝器只能用在直体及随动导丝大锥度机床上的根本原因,至于在没有随动导丝的小锥度机床上使用导丝器并进行小锥度切割的加工方式,其导丝器的使用寿命将很短。
本课题组设计了一种六连杆大锥度随动导丝及喷水机构[11],其原理见图8。由于电极丝方向始终与导丝器中的V 型槽重合(图9),设计于导丝器上的喷水嘴喷出的工作液始终能包裹住电极丝并随电极丝进入加工区,因此能起到很好的洗涤、冷却和消电离作用,这对于加工精度、切割效率和表面质量的提高均起到积极作用[12]。随动导丝及喷水机构见图10a,切割现场见图10b。
5.结束语
本文分析了往复走丝线切割加工在高效切割、降低丝耗、导丝定位等方面遇到的技术瓶颈,并从放电加工机理方面着手分析,为研究人员提供一个解决问题的参考思路,望能进一步促进往复走丝线切割加工技术的发展。
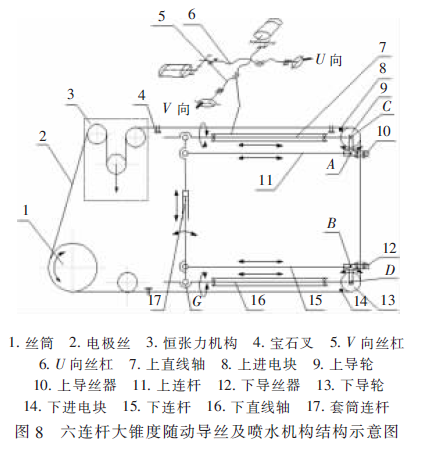
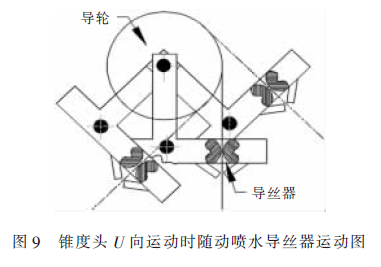
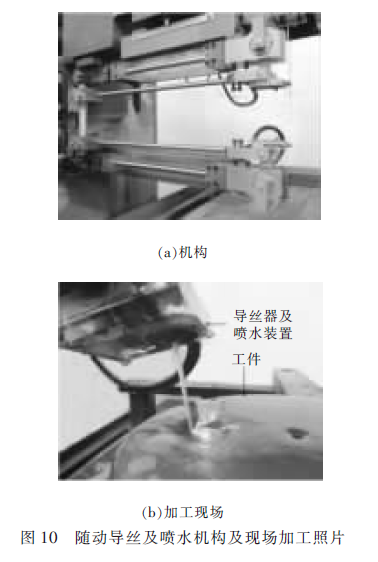
投稿箱:
如果您有机床行业、企业相关新闻稿件发表,或进行资讯合作,欢迎联系本网编辑部, 邮箱:skjcsc@vip.sina.com
如果您有机床行业、企业相关新闻稿件发表,或进行资讯合作,欢迎联系本网编辑部, 邮箱:skjcsc@vip.sina.com
更多相关信息