复杂流道电火花加工中的摆动进给
2016-12-16 来源:上海航天设备制造总厂 作者:刘晓 王晓娟 赵万生 王炜 陈风帆
摘要:叶轮类零件复杂流道电火花加工中普遍存在整体效率较低、加工状态不稳定的情况。提出了电极摆动进给策略,通过调整电极进给各阶段位姿,改善了加工区域前端工作液流场,扩大了加工过程中的蚀除产物排出空间。流道加工试验证明了摆动进给可有效改善加工稳定性,提高整体加工效率。
关键词:摆动进给;复杂流道;电火花加工;加工效率;加工稳定性
以闭式整体泵叶轮、涡轮盘为代表的叶轮类零件复杂流道加工, 是电火花加工的一种重要应用,其核心是成形电极沿预先规划的路径进给,然后进行拷贝加工[1]。由于复杂流道弯曲狭窄,成形电极在进给过程的大部分阶段,其加工状况均类似深盲孔加工,冲液措施无法将工作液有效喷入,难以将蚀除产物迅速带离电极前端的放电加工区域,因而易造成放电状态不稳定,产生拉弧、积碳等现象,严重影响加工效率。对此,通常采用抬刀措施以改善蚀除产物的排出状况。抬刀回退可分为两个阶段:首先,电极沿原进给路径回退一定距离,此时,纯净的工作液从流道外部进入加工区域;然后,电极再次沿进给路径前进, 将进入的工作液压出加工区域,蚀除产物随之被带出。然而,额外的抬刀运动势必影响整体加工效率。实际加工经验表明,在闭式叶盘类零件的电火花加工中, 抬刀措施不可避免,但抬刀的周期可根据加工状况进行调整[2]。抬刀周期过短,会影响加工效率;抬刀周期过长,则难以有效改善加工稳定性。
图1 是闭式整体泵叶轮流道电火花加工示意图。在成形电极进给运动过程中,电极与叶轮之间的距离狭窄弯曲,其间距略大于放电间隙,这意味着留给蚀除产物排出的区域非常有限;在确保不发生干涉的前提下, 扩大电极与叶轮之间的空间,将有助于改善蚀除产物的排出状况,以达到适当延长抬刀周期、提高加工效率的目的。对此,本文提出了电极摆动进给策略。
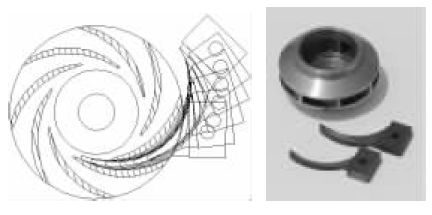
图1 闭式整体泵叶轮电火花加工电极进给路径
1. 电极摆动进给
电极摆动进给的目的在于扩大电极进给时其前端区域及侧面区域的空间,为工作液的冲入提供空间。图2 是电极摆动进给的流程。不失一般性,以图1 所示电极进给运动的某阶段为对象,阐述实施电极摆动进给的过程。
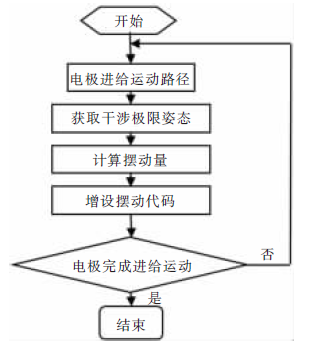
图2 电极摆动进给运动流程图
电极摆动进给的实施对象为描述电极运动路径的数控代码, 其可根据代码行数分为若干阶段。如图3 所示,第i 阶段的电极摆动进给,以该阶段的电极位姿为初始状态,以电极安装孔圆心为旋转中心,分别向C 轴正负方向、按一定的搜索步长调整电极姿态。每一步调整后,判断电极与叶盘的干涉状况,分别记录C 轴正、负方向上发生干涉时的转角,记为β1与β2,电极摆动进给量设置为δ1=η·β1,δ2=η·β2,其中,η 为摆动进给系数(0<η<1),其数值一般根据实际加工状况选取,通常不超过0.5。未实施摆动进给时的第i 阶段的数控代码为:
G01X(xi)Y(yi)Z(zi)C(ci)
设置进给摇动后的数控代码为:
G01X(xi)Y(yi)Z(zi)C(ci)
G01X(xi)Y(yi)Z(zi)C(ci+δi1)
G01X(xi)Y(yi)Z(zi)C(ci-δi2)
G01X(xi)Y(yi)Z(zi)C(ci)
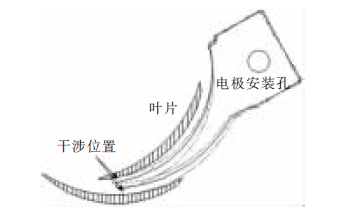
图3 电极进给运动第i 阶段的摆动进给
经摆动进给后,电极前端及侧面与叶盘的间距有所扩大,这为工作液带离蚀除产物提供了较开阔的空间,有利于改善加工稳定性和提高加工效率。
2 .电极摆动进给对极间流场的影响分析
为了更直观地了解电极摆动进给对改善蚀除产物排出状况的影响,采用计算流体力学方法分别对“无摆动进给”与“有摆动进给”两种情况下的极间工作液流场分布进行模拟[3]。实际经验表明,电极抬刀回退在加工中不可避免。对于加工中的一次抬刀回退,蚀除产物的排出是通过抬刀的第二阶段,即电极沿进给路径再次向加工区域运动的过程中实现的。以抬刀的第二阶段中某一时刻下,电极与工件之间的极间工作液介质作为仿真几何建模的对象,具体为:工件已完成第i阶段加工,电极再次进给至第(i-1)阶段时的位置姿态(图4)。模型中的放电间隙设定为0.08 mm,极间工作液为液相不可压缩流体, 密度为760 kg/m3,黏性系数为1.43×10-3 kg/(m·s);流场稳定后处于稳态,流场物理量仅与空间坐标有关,与时间无关。
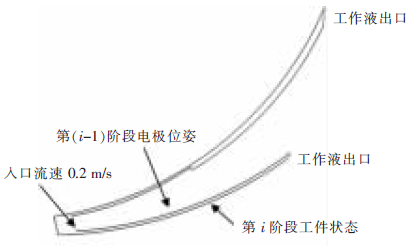
图4 电极摆动进给流场仿真建模
抬刀的第二阶段,即电极向加工区域进给过程中,其端面对极间工作液形成具有一定速度的类似活塞运动,而工作液从电极侧面与工件的间隙处向外部流出。为了简化仿真模型,对边界条件作如下设定:以电极端面为入口,入口边界设置为速度入口,入口速度为电极向加工区域运动的速度,设置为0.2 m/s;以叶盘两侧边缘为出口,出口边界设置为自由流出。极间工作液视为层流,网格划分采用四边形网格。图5 是无摆动进给与有摆动进给情况下,电极完成抬刀并再次向加工区域进给时的工作液流场速度云图。对比可见,摆动进给时,加工区域前端形成了范围更广泛、速度更高的涡流,有助于停留在加工区域中的蚀除产物获得更高的速度,进而离开加工区域。
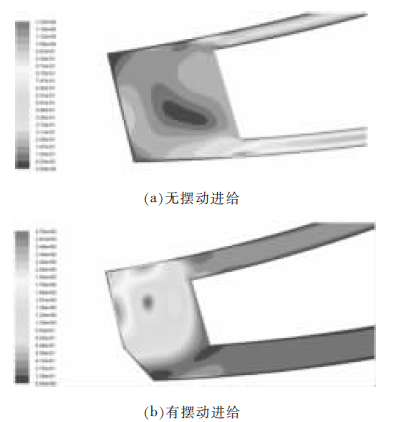
图5 有、无摆动进给下的加工区域前端流场分布
3. 电极摆动进给验证实验
为了验证电极摆动进给对复杂流道电火花加工效率及稳定性的影响,以图1 所示的闭式整体泵叶轮为对象,分别采用“无摆动进给”和“有摆动进给”的方式加工单个流道。为尽量消除影响加工稳定性的因素,工件材料选用电火花较易加工的模具钢,电极材料选用POCO EDM-C3 渗铜石墨,放电规准见表1[4]。在有、无摆动进给的对比实验中,工件、电极材料与放电规准完全一致。
表1 石墨电极加工模具钢泵叶轮的放电规准
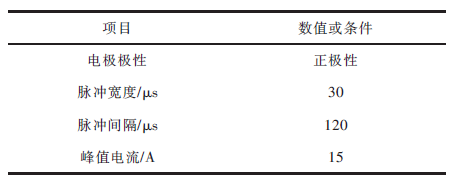
图6 是摆动进给对泵叶轮单个流道加工稳定性及加工效率的影响。在加工稳定性方面,电极无摆动进给加工时,只有当抬刀周期T 缩短至1 s 时,才能保证稳定加工,且在电极前端出现明显的积碳点。当电极增加摆动进给后,抬刀周期T=1.5 s 即可确保稳定加工。
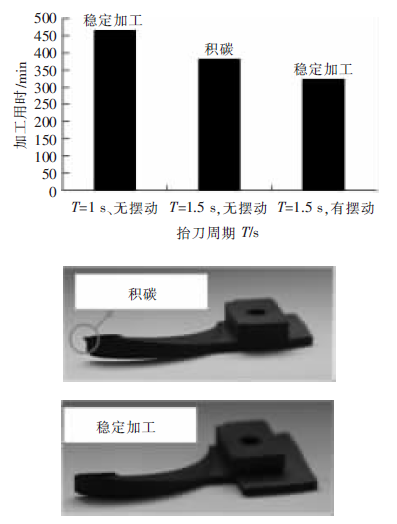
图6 电极摆动进给对加工稳定性及加工效率的影响
从图6 还可看出,在加工效率方面,电极无摆动进给加工时, 抬刀周期T=1.5 s 时完成单个流道加工需耗时385 min;抬刀周期T=1 s 时加工单个流道需耗时467 min。当电极增加摆动进给后,抬刀周期T=1.5 s 时完成单个流道加工仅需耗时326 min,与相同抬刀周期下的无摆动工况相比,加工效率提升了15.32 %,与稳定加工的无摆动工况相比,加工效率提升了30.19 %。
为了进一步了解摆动进给对加工效率的影响,对电极进给运动过程中完成各运动阶段所需的时间进行单独分析。需要指出的是,在电极进给路径规划过程中,为了提高规划效率,电极进给运动的早期,各阶段间距较大;而后期电极运动空间较小时,各阶段间距较小。这使得在整个电极进给运动中,完成各阶段加工的用时并不相同。
图7 是当抬刀周期T=1.5 s 时,有、无摆动进给条件下,完成各相邻运动阶段所用的加工时间。可见,在电极进给运动的早期阶段,摆动工况下的加工用时略高于无摆动工况。这是由于电极尚未深入流道,蚀除产物的排出并不困难,此时,摆动进给并未体现其功效,相反会占用一部分加工时间,影响加工效率。随着加工的进行,电极逐渐深入流道,蚀除产物的排出状况愈加恶劣,此时,摆动进给改善排屑状况的作用开始显现,各阶段加工效率的提升幅度随之上升;在执行第24 阶段运动时,摆动进给对单阶段加工效率的提升幅度达到最高值40.3 %。由于电极进给至第25 阶段时,流道被加工通畅,蚀除产物的排出状况随即改善,此时,摆动进给对单阶段加工效率的提升程度有所下降,但摆动进给工况下的加工用时仍略低于无摆动工况。
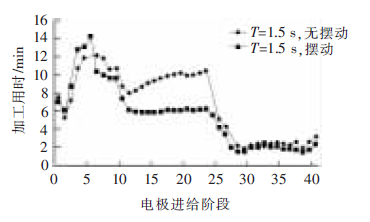
图7 摆动对电极进给各阶段加工效率的影响
4 .结语
本文针对复杂流道电火花加工中整体效率较低、加工状态不稳定的情况,提出了电极摆动进给策略,在避免干涉的前提下,通过调整电极进给各阶段的位姿,扩大电极与工件之间供蚀除产物排出的空间。仿真结果显示,摆动进给可显著改善加工区域前端的工作液流场;闭式整体泵叶轮流道加工试验结果表明, 摆动进给可有效改善加工稳定性,降低对抬刀周期的依赖; 随着电极进给的深入,摆动进给对提高加工效率的作用愈加明显。
投稿箱:
如果您有机床行业、企业相关新闻稿件发表,或进行资讯合作,欢迎联系本网编辑部, 邮箱:skjcsc@vip.sina.com
如果您有机床行业、企业相关新闻稿件发表,或进行资讯合作,欢迎联系本网编辑部, 邮箱:skjcsc@vip.sina.com
更多相关信息