小型齿轮加工单元自动上下料系统的设计与实现
2019-11-13 来源:南京工业大学机械与动力工程学院等 作者:陆 宁 洪荣晶 谢 杰
采用机械手实现自动上下料技术是机器人技术应用的一个重要方面。机器人自动上下料系统具有定位精度高、无疲劳作业、结构简单、便于维护等优点,因此广泛应用于各制造领域。
在小型齿轮加工过程中,大多数中小企业仍采用人工或半自动作业,齿轮的上下料需要重复持续作业,工人劳动强度较大,持续作业的一致性与精准性得不到保证而导致的齿轮质量不合格问题也时有发生。随着用工成本的提高及生产效率提升带来的竞争压力,加工能力的自动化程度及柔性制造能力成为企业竞争力提升的关键。
本文以某企业实际生产需求为研究背景,从改进小型齿轮加工过程中人工上下料存在的不足出发,设计了一套小型齿轮加工单元自动上下料系统。系统以S7-1500PLC 为主控制器,综合运用了工业机器人技术、工业以太网技术及传感器技术等,有效的实现了齿轮加工过程中的自动上下料工作。降低了工人劳动强度,保证了产品加工质量,实现了小型齿轮的大批量、自动化生产。
1、系统方案提出
1. 1 系统组成、布局确定
此项目要求机器人上下料工件为小型齿轮,如图1 所示。工件包括两道加工工序: 端面及外圆车削和轮齿加工。
由工件加工工艺分析拟定采用数控车床对齿轮的端面及外圆进行车削。考虑到齿轮整体加工精度要求不高,且需要大批量加工,故选取滚齿的加工工艺。在合理计算、规划机床加工时间与机器人上下料时间的前提下,本项目采用一台工业机器人为一台数控车床及一台数控滚齿机上下料的方案,辅以工件翻转台、工件储料架等周边设备,搭建一个小型齿轮加工单元自动上下料系统。机器 人 选 用 UR10 工 业 机 器人,有效负载 10kg,工作范围可达 1300mm,接口兼容大多数工业传感器及 PLC,支持以太网通讯; 采用 SIEMENS 数控系统的数控机床,机床卡盘与防护门均采用气动控制方式,且设有工作到位检测开关。系统布局如图 2所示。
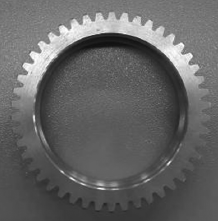
图 1 工件实物图
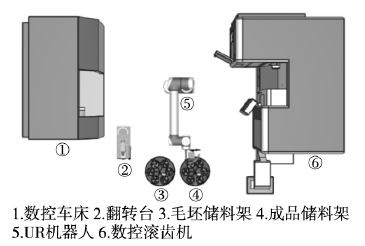
图 2 系统整体布局
1. 2 工作过程规划
根据加工单元技术要求及工艺特点,并结合加工单元结构组成,对工作过程进行规划,如图 3 所示。
考虑到加工单元初次工作时,数控车床内部并无成品完成件,因此需由机器人首次取料至车床加工,待加工完成后,由翻转台进行加工面更换,继续上料数控车床,然后从毛坯储料架继续抓料。待前工件加工完成后,机器人双手爪工作,进行车床上下料操作,滚齿机内部同样无成品完成件,因此只进行一次车削完成件的上料操作。如图中虚线框所示。
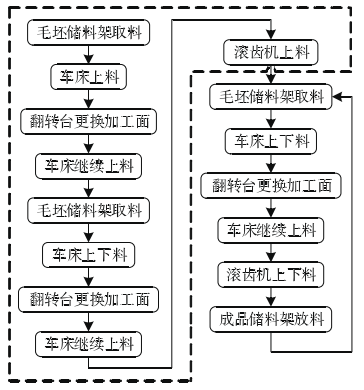
图 3 系统工作流程
2、控制系统设计
2. 1 控制单元组成
系统包括数控车床、数控滚齿机、工业机器人、储料架、翻转台 5 个控制单元。各控制单元完成动作后,须有相应的动作完成信号发出,从而通知系统下一步的动作。
为保证各控制单元的正常工作顺序及控制逻辑的合理性,加工单元采用西门子 S7-1500 系列 PLC 作为主控制器,统一接收处理各控制单元的传输信号,协调各设备之间的动作响应。PLC 接有人机界面触摸屏,实现对现场设备工作状态的集中监控。翻转台及储料架的动作由主控 PLC 控制,机器人与数控机床由自身集成的控制器控制,机器人、数控机床控制单元采用MODBUS-TCP 协议与主控 PLC 通讯。加工单元控制系统结构关系示意图如图 4 所示。
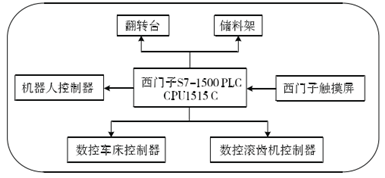
图 4 控制系统结构关系示意图
2. 2 通信系统建立
为提升系统整体结构的时效性,有效实现各设备之间的通讯连接,上下料系统需采用安全可靠、准确快速的通讯方式。
系统采用工业以太网通讯方式,将机器人、数控机床、主控 PLC、触摸屏、终端计算机等进行通讯连接。其中机器人负责工件上下料示教编程,主控 PLC 除协调其他设备之间的信息交互,还控制翻转台及储料架的动作。触摸屏用于工作状态的监控、提示。终端计算机负责程序的编程与调试。网络通信系统结构如图 5 所示。
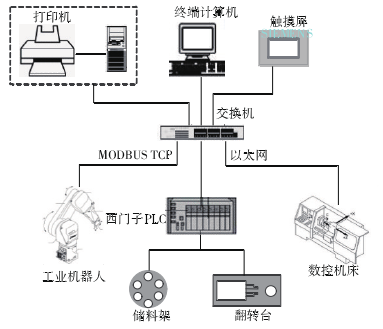
图 5 通信系统结构
2. 2. 1 MODBUS TCP 通信协议
MODBUS-TCP 通信协议是运行在 TCP / IP 上的一种通信传输协议,利用该协议构建的以太网络具有成本低,通讯高效、稳定,简单易用等特点,可实现设备与设备之间,设备与网络之间的有效通讯,因此广泛应用于工业控制领域。本系统中,主控 PLC、机器人、数控机床控制器等均集成以太网接口,可通过 MODBUS-TCP 通信协议实现通讯连接。数据传输建立之前,MODBUS-TCP 通信协议需确定设备之间的逻辑关系,并建立 MODBUS 与 PLC 间的响应地址,从而保证通信的正常稳定。
2. 2. 2 主控 PLC 与机器人通讯
调用西门子 TIA Portal 软件内嵌的 S7-1500 MOD-BUS-TCP 库函数实现主控 PLC 与机器人的以太网通信,完成设备间的参数配置及状态读写。主控 PLC 作为MODBUS-TCP 客户端发送读写请求,服务端机器人负责请求的响应。
为保证主控 PLC 正确地发送和接收机器人数据,MODBUS-TCP 通信必须设计好两者之间的数据读写区域。通信数据以字节为单位存储于设备寄存器中,以字作为传输单位,以位为寻址单位。以 PLC 读取机器人状态数据为例,通过“机器人状态字”读取函数,将机器人内部输出变量 SYSTEM /DO0 对应的 MODB-US 地址开始的 4 个字,读入主控 PLC 并存放在 P #M3000. 0 开始的 4 字中; 当 PLC 发送数据至机器人时,“机器人控制字”函数工作,将 P#M3100. 0 中的开始 4个字 节 写 入 机 器 人 输 入 变 量 SYSTEM /DI0 对 应 的MODBUS 地址开始的 4 个字节中。主控 PLC 读取和写入机器人部分信号见表 1。
表 1 主控 PLC 读取和写入机器人部分信号表
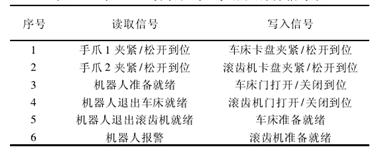
IP 地址分配是使用 MODBUS-TCP 通信的必须步骤,要保证所有设备网络地址必须在同一网段内。利用 TIA Portal 为系统各个硬件分配 IP 地址,主控PLC IP 地址为 192. 168. 8. 10,机器人 IP 地址为 192.168. 8. 103。
明确了机器人与主控 PLC 之间读写信号及相关参数设定,分配各设备 IP 地址后,调用“MB_CLIENT”通信指令,实现客户端与服务端之间的数据读写通信连接。编制的 MODBUS-TCP 通讯程序如图 6 所示。
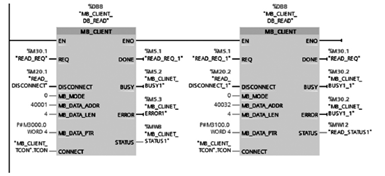
图 6 主控 PLC 与机器人通讯程序
3、机器人上下料程序设计
3. 1 机器人上下料路径规划
机器人要完成在储料架、数控机床、翻转台之间的上下料工作,移动路径多样,有必要对机器人上下料运动路线进行设计。根据系统结构布局,利用 UR 机器 人 示 教 编 程,规划的机器人上下料路线图如图7 所 示。 设 计 过程 中,为 减 小 机器 人 与 储 料 架、机床夹具之间的配 合 偏 差,固 定配 合 移 动 方 向,保证工件持续装夹作业的一致性,需在机器人上下料处设置不同的 TCP 坐标点,即建立不同的工具坐标系。
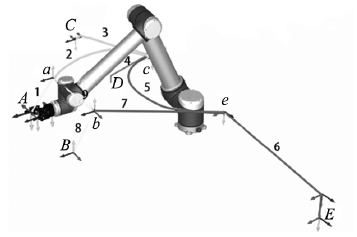
图 7 机器人上下料路径
图中 A、B 两点为毛坯抓取点与成品放置点,a、b为上下料的初始准备位置; C、D、E 分别为数控车床、翻转台、数控滚齿机的工件装夹处,c、e 分别为机器人与数控机床之间上下料的初始准备位置。
3. 2 机器人上下料流程设计
根据机器人上下料路径规划,设计的机器人运动流程图如图 8 所示。
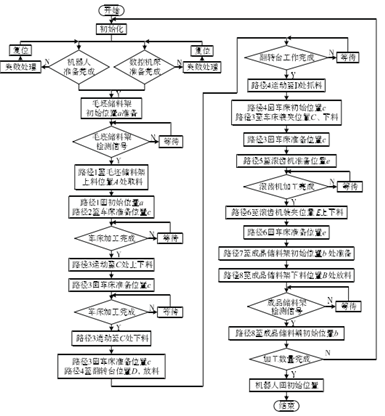
图 8 机器人运动流程
3. 3 机器人上下料程序编程
Polyscope 编程为 UR 机器人 UI 层编程方式,示教器上编辑程序,机器人执行,编程方式简单,程序易于调试、修改。根据机器人的轨迹规划及上下料流程,编写了机器人上下料程序。以机器人上下料数控车床运动程序为例,描述如下。图 9 为机器人上下料数控车床现场图。
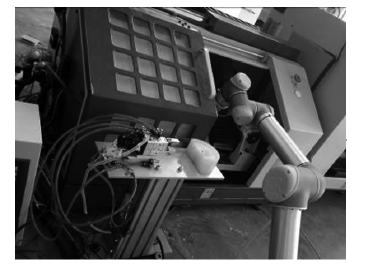
图 9 机器人上下料数控车床
. . . . . .
LOOP 9 TIMES
MOVEJ Waypoint1; 机器人初始位置准备
Call Sub Program1: 机器人抓取毛坯件子程序
Call Sub Program2: 机器人上下料数控车床子程序
MOVEJ Waypoint4; 机器人至车床准备位置
Wait DI14 = HI; 等待车床加工完成信号
Wait DI6 = HI; 等待车床门打开到位信号
MOVEL Waypoint5; 手爪 2 至卡盘右侧 5CM 处
MOVEL Waypoint6; 手爪 2 至工件装夹处
Set DO1 = OPEN; 手爪 2 夹紧
Wait DI3 = HI; 等待手爪 2 夹紧到位信号
Wait DI12 = HI; 等待车床卡盘松开到位信号
MOVEL Waypoint5;
MOVEJ Waypoint7; 手爪 1、2 位置互换
MOVEL Waypoint6; 手爪 1 至工件装夹处
Wait DI10 = HI; 等待车床卡盘夹紧到位信号
Set DO0 = CLOSE; 手爪 1 张开
Wait DI4 = HI; 等待手爪 1 张开到位信号
MOVEL Waypoint5;
MOVEL Waypoint4;
Wait DI8 = HI; 等待车床门关闭到位信号
Wait DI14 = HI; 等待车床加工完成信号
Wait DI6 = HI; 等待车床门打开到位信号
MOVEL Waypoint5;
MOVEL Waypoint6;
Set DO0 = OPEN; 手爪 1 夹紧
Wait DI2 = HI; 等待手爪 1 夹紧到位信号
Wait DI12 = HI; 等待车床卡盘松开到位信号
MOVEL Waypoint5;
MOVEL Waypoint4;
Call Sub Program3; 机器人上料翻转台子程序
Call Sub Program4; 机器人上料数控车床子程序
Call Sub Program5; 机器人上下料滚齿机子程序
Call Sub Program6; 机器人下料成品件子程序
MOVEJ Waypoint1;
对企业布局的 6 处小型齿轮加工单元进行加工试验,分别加工齿轮 20 件,与人工作业相比,自动上下料系统加工效率得到显著提高,产品稳定性得到进一步改善。对比结果见表 2。
表 2 自动上下料系统与人工作业对比
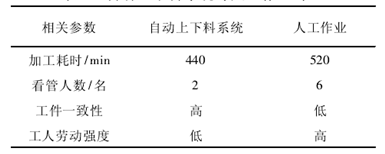
4、结束语
在“智能制造”的发展规划下,小型齿轮加工单元自动上下料系统的设计为中小企业自动化程度及竞争力的提高提供了新思路。现场加工试验表明:
(1) 通过合理布局自动上下料系统,可有效地节省人力资源及企业用工成本,提高中小企业加工效率;
(2) 自动上下料系统具有较高的重复定位精度,成品件一致性较人工作业得到大幅度提高;
(3) 系统采用西门子 S7-1500PLC 作为主控制器,通过 MODBUS-TCP 通信协议,实现了工序间的信息流、工序转换的自动化,布局简单,调试方便。
投稿箱:
如果您有机床行业、企业相关新闻稿件发表,或进行资讯合作,欢迎联系本网编辑部, 邮箱:skjcsc@vip.sina.com
如果您有机床行业、企业相关新闻稿件发表,或进行资讯合作,欢迎联系本网编辑部, 邮箱:skjcsc@vip.sina.com