数控插齿机传动链误差对齿轮加工精度的影响分析与研究
2019-9-9 来源:宜昌长机科技有限责任公司 作者:王晓丽
摘要:分析数控插齿机传动链误差对齿轮加工精度的影响,对诸因素中传动链产生的传动误差进行了具体的分析,对各种传动误差的产生来源及其传动链精度影响的大小进行了分析从而找出减少加工误差的措施, 提出了避免和减少误差、提高插齿机传动链精度的方法和改进齿轮加工精度的措施。
关键词:数控插齿机;传动链误差;加工精度
0 引言
随着机械工业的发展,目前各行各业对插齿机加工精度的要求愈来愈高,插齿机传动链精度问题亦就成了数控插齿机设计与研究的重要课题之一。 笔者就数控插齿机的传动链精度对加工齿轮精度的影响方面来进行分析研究。
1 、数控插齿机传动链误差的概念与来源
齿轮的加工精度主要由传动元件的运动精度即插齿机的传动链精度来实现。 传动链是插齿机的重要组成部分,它具有传递运动、传递动力和传递误差等功能。 如何减少各种因素对加工精度的影响,就需提前考虑分析。
插齿机传动链一般由圆柱齿轮、锥齿轮、蜗轮、蜗杆、刀轴、丝杠与螺母等传动元件组成,它们也是传动误差的来源,每一传动链精度及其合成运动精度是齿轮加工精度的保证。 数控插齿机内部传动链中的传动齿轮,一般均要求达到 6 级或更高精度等级,两套蜗轮副的精度一般均要求四级或更高精度等级。
用渐开线法加工齿轮等工件时,必须保证工件与刀具间有严格的运动关系,这种运动关系是由刀具与工件间的传动链来保证的,这种方法的加工精度和生产率都较高。插齿机的主运动(刀具往复)是由主电动机的转动通过各传动件传给主轴,并带动装在主轴上的刀具上下往复运动,通过变频器控制,改变主电机的频率,从而获得不同的主运动速度,实现主运动(如图 1 所示)。 主运动链的两端件是主电动机和主轴。可以用如下的传动系统结构式,来表示主运动的传动路线:

图 1 主运动的传动路线图
传动链中的各传动元件,如齿轮、蜗轮,蜗杆、刀轴、丝杠等,因有制造误差(主要是影响运动精度的误差)、装配误差(主要是装配偏心)和磨损而破坏正确的运动关系,使工件产生误差。传动链的传动误差是指内部传动链中首末两端传动元件之间相对运动的误差。 它是按展成原理加工齿轮时影响加工精度的主要因素。
2 、数控插齿机传动链误差分析
传动链误差一般可用传动链末端元件的转角误差来衡量。 由于各传动件在传动链中所处的位置是不同的,其影响传动精度的大小也不同。 例如,当传动链是升速传动,则传动元件的转角误差将被扩大;反之转角误差将被缩小。
(1) 数控插齿机主要是由各种传动传动元件组成不同的传动链,再由几个传动链的合成运动实现齿轮加工,最终通过末端刀具与工件间的运动来保证齿轮加工精度。 假设插齿机 C1 轴(工作台) 传动链的末端转角误差为△ ¢ 1,C2 轴(刀架体) 的末端转角误差为△ ¢ 2,则根据△ ¢ 1、△ ¢ 2 误差的大小与正负,所得的合成运动误差是不相同的,当△ ¢ 1、△ ¢ 2误差方向相反时,则对齿轮加工精度的影响最大。
机床传动链传动误差的检测方法有间接法和直接法两种,下面是用直接法利用传动链检测仪模拟加工状态对某台插齿机刀架体、工作台蜗轮副传动链进行检测的检测图形,如图 2
所示。
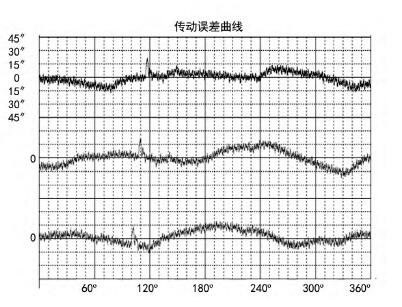
图 2 蜗轮副传动误差图
由图可见在 120 采样点处有一固定高点,将两套蜗轮副(刀架、工作台蜗轮副)拆下后, 利用 HS-900对工作台蜗轮进行检测,检测结果,如图 3 所示。
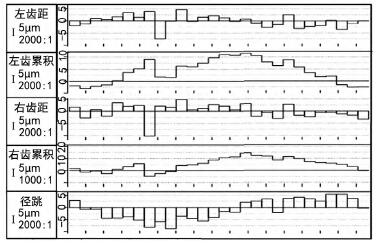
图 3 蜗轮检测图
C1 轴(工作台) 回转精度蜗轮表现有一个齿的偏差较大,在周节累积、偏差曲线上明显呈周期性波形误差。 通过特征频率查找传动链中各误差源的部位,经过分析,此台插齿机短周期误差的误差源为工作台蜗轮,蜗轮齿面有高点和磕伤,蜗轮下端有毛刺。
(2) 在加工齿轮的循环过程中,伺服电机的联动是按照加工程序里所写的步骤一步一步的来实现的C2 轴(刀架体刀轴)旋转的度数等于 C1 轴(工作台)旋转的度数乘以工件齿数与刀具齿数的比值。
但在实际的加工过程中,伺服电机本身的运动特性就存在误差,电机旋转带动工作台的旋转和刀轴的旋转会出现偏差或不稳定,这样会形成在加工过程中加工精度有切削振纹或表现为单齿距偏差比较大,齿轮综合精度达不到要求。
利用英国雷尼绍(Renishaw) ML10 激光干涉仪分别对 C1 轴(工作台)、C2 轴(刀架刀轴) 两套传动链分别进行测量,从而分析整个传动链上各元件的综合误差。
如图 4 所示为激光干涉仪对刀架体的检测结果、其定位误差较大,由图可看出在 0° ~ 360°区间,分别出现一个高点( 在 90° 时)、一个低点( 在 150°时),根据曲线呈现出的规律分析,由于装配误差造成刀架蜗轮副转动偏心或蜗轮副本身存在误差。
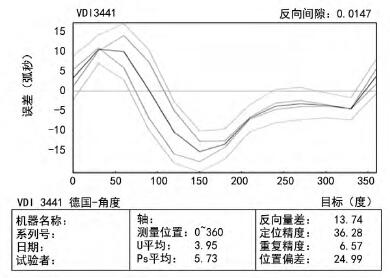
图 4 利用 ML10 激光干涉仪对 C2 轴的检测图
(3) 在齿轮加工完成退刀的过程中,由于前面的因素,另外还有电机在加工完毕时,是一个运动减速的过程, C2 轴(刀轴)和 C1 轴(工作台)停止旋转是否同时进行,假若停止的时间或是停止的位置不同步(比如某个轴的阻力偏大),从而造成一个轴旋转的度数在实际过程中相应的与另一个轴的旋转度数比例有细小的差别,即前面提到的传动链转角误差,从而也会导致切削精度误差,影响齿轮的加工精度。
3 、减少数控插齿机传动链误差的措施
从上面的分析可以看出传动链的两个末端的转角误差对加工精度至关重要。 数控插齿机主要是由几个传动链的合成运动实现齿轮加工的,通过刀具与工件间的传动链来保证齿轮加工精度,为了获得正确的分齿精度,必须保证每一传动链精度及其合成运动精度。 这就为我们研究如何减少插齿机传动链误差,提高加工精度指明了方向。
(1) 尽可能减少传动元件的数量,缩短传动链,尽量采用直联,即主运动电机、蜗轮副直联的形式进行驱动。
(2) 提高每个关键传动元件的精度,减少各传动元件装配时的几何偏心,完善蜗轮副的装配工艺和作业指导书,提高装配精度。
(3) 提高传动链关键部件及末端件的制造精度。在一般降速传动链中,末端元件的误差影响最大,特别对于数控插齿机来说本身属于内联系传动链,传动链的两个末端转角之间有严格的比例关系要求,工作台(或刀架) 蜗轮不能存在较大累积误差,故插齿机的分度蜗轮、刀轴的精度就应最高。 也可采用转台轴承减少摩擦力,提高工作台寿命和传动平稳性。
(4) 从优化电机运动特性入手,采取误差补偿。调整电机运动参数,从而使电机的运动定位和电机间的联动性能得到更好的提升。 在确保插齿机几何精度合格,装配完整的情况下利用英国雷尼绍( Ren-ishaw) ML10 激光干涉仪自动误差补偿软件进行自动误差补偿。
误差补偿的实质就是在原传动链中人为地加入一误差,其大小与传动链本身的误差相等而方向相反,使之相互抵消,从而提高传动链的合成运动精度,到提高齿轮加工精度的目的。
4 、结论
在分析数控插齿机传动链影响齿轮加工精度的基础上,通过数控插齿机传动链误差对齿轮加工精度的影响,找出进一步改善单个传动链与传动链合成运动精度的一些方法与措施,
达到了提高齿轮加工精度的目的,对解决齿轮实际加工精度的问题有重要意义。
投稿箱:
如果您有机床行业、企业相关新闻稿件发表,或进行资讯合作,欢迎联系本网编辑部, 邮箱:skjcsc@vip.sina.com
如果您有机床行业、企业相关新闻稿件发表,或进行资讯合作,欢迎联系本网编辑部, 邮箱:skjcsc@vip.sina.com