基于嵌入式齿轮加工数控系统的探讨
2019-5-23 来源: 中山迈雷特智能装备有限公司 作者:林守金
摘 要:伴随着社会经济的快速发展,齿轮的生产对于社会经济发展有着显著的影响。对此,为了更好的优化齿轮的加工效果,本文提出了一种关于嵌入式系统的齿轮加工数控系统,并简单分析系统的整体结构,同时对该系统进行任务的划分,设计多个工作的具体功能模块。希望能够借助本文所提供的嵌入式齿轮加工数控系统,改进今后齿轮加工效益。
【关键词】嵌入式;齿轮加工;数控系统;探讨
引 言
制造领域是我国经济的支撑性产业, 对于我国国民经济的增长有着显著意义,同时也是我国综合实力的一种展现,对于国家发展有着明显的推动作用。 近年来随着数控加工技术不断发展,其应用的作用以及效果也显得越发明显。
高效率的数控加工技术能够展现优质、低成本、高效率、绿化等工业制造的产业效果。 对此,探讨嵌入式的齿轮加工数控系统具备显著意义。
1 、嵌入式系统的特点
本文所探讨的齿轮加工数控系统是嵌入式系统, 这里所指的嵌入式系统主要是指以生产和应用为核心的专用型计算机系统,这一系统能够按照用户的实际需求对硬件设备、软件资源等进行针对性的定制和调整, 从而促使产品的成本、性能、可靠性以及体积、功耗等获得保障。
嵌入式设备的组成一般是包括嵌入式 CPU、外围硬件、操作系统以及针对用户需求的专用型应用程序等, 主要是应用在对于设备的控制以及监控场景当中。
嵌入式系统的特点有以下几点:
①嵌入式系统所应用的 CPU 一般都是特定的,所以具备功耗低、体积小以及高集成度等优势,同时还可以通用 CPU 中板卡实现功能集成到某一个处理器芯片当中,进而实现移动性的工作能力;
②一般情况下, 嵌入式系统的应用软件并不是单独储存在某一个载体上的,而是固定在某一个内存储存器的芯片当中的,这一种特点显著提升了软件的运行速度及其可靠性;
③嵌入式系统和特殊的应用相结合,能够面对更为广泛的用户,升级和转型也相对及时,所以使用周期比较长;
④对于用户而言,嵌入式系统具备较高的透明度, 用户需要了解内部的设计细节以及编程操作, 只需要根据相应的步骤便可以完成嵌入式系统的编程;
⑤嵌入式系统的实用性非常高,嵌入式系统和大多数工业生产之间有着较高的关联性, 普遍都是将嵌入式系统当做实时控制系统来应用。
2 、嵌入式齿轮加工数控系统的整体设计
2.1 、嵌入式齿轮加工数控系统的硬件设计
因为 Windows CE 操作系统非常简单,具备较高的开放性以及较高的稳定性等优势,所以数控系统选择在 Win CE6.0 操作平台当中进行研发,系统主要由 DSP 以及 FPGA 组成。
其中,ARM 微处理器主要负责完成关于人机交互的任务模块,例如加工参数的输入显示以及储存等功能。
除此之外,还需要负责一些借助网络通信模块传输工作信息的任务;DSP 则是负责处理数控系统的信息预算任务, 例如插补处理以及伺服位置的控制等, 同时将人机交互模块以及运动控制模块进行独立的管理, 一方面促使软件的研发以及调整更具灵活性和模块化,同时还能够更好的优化控制的性能、效率以及齿轮加工时的精度;FPGA 则是采用并行总线的运行方式, 主要完成机床方面 I/O 的信息传递。
2.2 嵌入式齿轮加工数控系统的软件设计
根据齿轮加工数控系统对于可扩展性以及可移植性的需求, 考虑到模块之间繁琐的数据交换以及程序在运行过程中的效率需求、开发难度等,结合齿轮加工的特点,本系统的软件主要划分为三个模块, 分别为 ARM 的界面管理模块、DSP的数值运算模块以及机床的 I/O 控制模块。
齿轮数控加工的特点以及软件功能模块的划分原则,设计系统软件框架较为复杂, 其主要是由显示接口、 网络控制板、机床 I/O 等多个结构构成。 齿轮加工数控系统在 ARM 上完成主要的参数设置、代码编码、自动编程以及加工状态的监控等非及时性的任务, 而在 DSP 上则是完成一些关于 NC 代码的指令分析、插补计算以及伺服位置控制等及时性的任务。
其中,ARM 可以进行代码的翻译和处理, 并生成 DSP 能够计算的数据结构,同时储存在 G 指令包当中。
与此同时,所编译的 PLC 程序也需要借助相应的转化之后存放在 PLC 指令当中。
除此之外,在 ARM 上输入的 DSP 初始化参数、显示编码参数以及螺距补偿等参数, 都可以以动态或静态的参数储存在之前设计的结构体当中, 这一些指令报以及参数的结构体在数控系统当中运行以及开启时, 可以借助相应的通信形式发放到 DSP 当中,DSP 便可以进行控制和运算。
3 、嵌入式齿轮加工数控系统的功能模块设计
嵌入式齿轮加工数控系统需要根据任务划分的工作特点,从任务以及功能两个方面进行区分
,任务的区分不仅能够让功能模块之间的通信更加合理和快速, 同时软件的结构也更加简单明了, 并且还可以促使系统设计更具扩展性以及开放性。
借助对齿轮加工数控系统的功能要求分析,可以发现本系统应当具备控制以及管理两个方面的任务。 控制任务主要是翻译编码,机床 I/O 控制、位置的显示与控制、电子齿轮箱以及插补处理等。
管理任务则可以划分成为自动编程、界面管理、文件管理以及加工监控等等。 控制任务和齿轮的加工有着密切的关联性,将会直接决定加工的精度以及效率。 对此,对于控制任务的及时性以及准确性要求相对较为苛刻。 管理任务则是负责齿轮加工的整体支撑, 所以子任务并没有较高的及时性以及准确性需求。
3.1 自动编程模块
因为齿轮的结构具备较高的相似性, 所以在齿轮数控加工当中,主要的参数只有三个,分别为齿轮的参数、刀具的参数以及工艺的参数。 从机床操作界面可以直接输入上述三相参数, 然后自动编程模块便会根据输入的参数进行计算和处理,并获得刀具的具体运行轨迹,之后生成数控加工的代码,形成 DSP 能够理解的数据信息,从而达到机床的控制目的,完成齿轮自动加工任务。
3.2 电子齿轮箱模块
电子齿轮箱模块主要是以软件、 电路的形式替代传统的机械式传动链,从而完成多个数目的,根据定向的运动关系计算,从而保障每一个轴之间的运动关系保持同步性。 除此之外,为了确保工件轴和刀具轴之间的运动速度保持协调性,工作轴的速度需要由刀具轴、其他进给轴等速度进行联合控制。
3.3 通信功能模块
通信功能模块的主要任务是将 ARM 当中的数据通过转换之后发放给 DSP。 例如,PLC 程序数据、NC 程序数据以及动静态参数等的信息传输。
与此同时, 通信模块还需要负责把DSP 当中的编码器信息数据进行反馈 ,并借助 PLC 进 行执行 ,检测执行状况, 并根据执行状况以及报警参数等对信息数据进行及时处理。
3.4 加工监控模块
加工监控模块主要可以划分为加工图形监控、 报警信息监控以及机床状态监控三种。 加工图形监控主要是包含对坐标数据、每一个数控轴的工作误差等进行监控。 报警信息监控则是包括报警信息、 报警之后的自我诊断以及历史报警信息的查询等。 机床状态监控是对机床及其附件环节的项目监控。
4 、嵌入式齿轮加工数控系统的编程探讨
齿轮加工当中滚齿加工是最为常见且常用的一种方式,有着径向、轴向、径向轴向、切向以及对角等多种加工方式。 其中, 轴向滚切的方式主要是应用在加工圆柱齿轮以及圆锥齿轮等外齿轮当中, 所以后续以轴向滚切的方式作为案例进行探讨。
①建立数学模型。 明确滚齿的对刀点。 为了保障工件的加工精确度,规避切入时间和空行程时间过长等问题,对于对刀有着方便、准确的要求。 在加工过程中,需要将滚刀对准齿胚上的顶面,然后在 Z 方向的位置明确 X 轴的具体方向和位置。在对刀的过程中,在滚刀进到齿胚的时候,需要先让齿胚运动一周之后再进行进刀,从而确保运动的正确性;
②明确滚刀的加工轨迹以及计算具体坐标。 以轴向滚切法为例,运动轨迹见图 1。 从图 1 可以直接发现,滚刀的运动轨迹是根据 0、1、2、3、
4、1 的方式进行
滚刀的起点位置在机床的零点 ,之后快速移动到 1,并切除全齿宽 2,滚刀轴向运动位置到 3;②退刀位置到 4,一次性进给刀完成加工。 对此,可以发现轨迹位置主要有 5 个。 但是,在实际加工过程中,会因为加工齿轮类型的不同,在关键位置及其数量也会存在明显的差异
,需要按照实际情况选择。
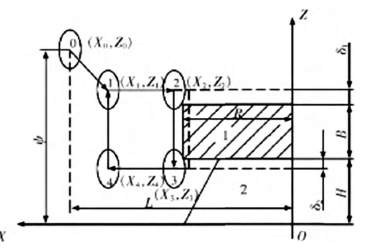
图 1 轴向滚切法的滚刀运动轨迹
一般情况下, 需要在加工之前对滚齿加工过程中的功能需求进行分析和总结,基本明确编程模块的主要参数、参数检查以及参数处理等过程。 首先, 需要建立齿轮参数的输入界面、滚刀参数输入界面以及工艺参数界面等信息的准确性,以便于操作人员能够及时对齿轮参数进行核对。 为了确保输入的参数能够满足齿轮加工的需求, 自动编成编程模块可以在操作者输入参数之后自动检查参数是否存在错误, 并且这一功能模块还能够及时提醒用户数据是否存在错误以及错误的原因,直到操作者能够输入正确的参数为止。
参数的处理主要是滚刀加工轨迹以及加工关键点的处理以及分析, 并将处理的结果生成数控代码,同时对程序的代码进行翻译,生成能够应用到 DSP 的信息数据, 并借助通信模块翻译之后发送到DSP 的缓存区 ,为后续的刀具运行提供准备 。
5 、结 语
综上所述, 嵌入式的齿轮加工数控系统具备非常多的优势,其在制造业的应用中能够展现许多的特点,可以实现降低材料的去除率、降低加工时间以及控制加工成本等效果。 在实际的应用中, 嵌入式的齿轮加工数控系统仍然可能因为各种因素而遭受影响,例如在滚齿自动编程方面需要持续改进,将自动编程技术真正应用到滚齿的加工环节当中, 为今后齿轮加工控制系统的精度提供相应基础。
投稿箱:
如果您有机床行业、企业相关新闻稿件发表,或进行资讯合作,欢迎联系本网编辑部, 邮箱:skjcsc@vip.sina.com
如果您有机床行业、企业相关新闻稿件发表,或进行资讯合作,欢迎联系本网编辑部, 邮箱:skjcsc@vip.sina.com