摘要:齿轮加工工艺方案直接影响着齿轮的结构形状、生产难度、生产批量、生产精度等因素,不同齿轮种类需要采用不同的工艺方案。由于不同精度等级对齿轮工艺方案选择有着决定性影响,因此,加强对齿轮工艺方案的研究有着重要意义。基于此,本文重点对不同的齿轮工艺方案进行研究,探究各类齿轮工艺方案的特点与优劣势。
0、引言
对于齿轮来说,由于所要求的精度、使用寿命、耐磨性都有着极大的差异。并且还要分析齿坯的几何精度、形位公差、尺寸精度等问题。因此,在齿轮加工过程中通常要比平常器件加工高出1-2个等级。由于齿坯精度是保障齿形加工决定因素,因此,需要技术人员重点加强对齿坯加工精度。下文我们就针对齿轮工艺不同的方案进行研究。
1、普通精度齿轮加工方案
1.1 工艺过程分析
第一加工阶段。该阶段主要是将齿坯进入到机械加工的阶段。由于齿轮的转动精度取决于齿形精度和齿距分布均匀性,这对滚齿同时采用的定位基准精度有着直接的联系,因此,该阶段主要是基础性加工阶段,主要是为后续的机械加工奠定基础,保障端面和内孔精度能够满足实际的设计需求。再者,该阶段除了保障齿形的精基准,同时也需要对齿形外的次要表面进行加工,需要在该阶段的后期完成。
第二阶段。对于不需要淬火的齿轮,则该阶段是最后一项加工工艺,在该阶段需要加工出符合设计图的齿轮。而对于需要硬淬的齿轮来说,必须要能够保障在该阶段中加工出足够满足齿形的精度标准,因此,该阶段是保障齿轮精度的重中之重,需要技术人员特别注意。
第三阶段。该阶段主要是进行热处理工艺。也就是对齿面进行淬火加工,从而提高齿面的硬度,保障其硬度能够满足设计标准。
第四阶段。该阶段主要是精加工阶段。在该阶段加工中需要将淬火后的齿轮进行加工,从而进一步提高齿形精度以及降低表面的粗糙程度,保障其最后成型产品能够满足精度要求。该阶段加工中,需要对定位基准面进行修整,由于淬火后的齿轮内孔与端面都会出现一定程度上的变形问题,如果在淬火后直接应用孔和端面作为基准进行加工,非常难以达到齿轮的精度要求。但通过修整过后的基准面定位则能够实现齿形的精度加工,保障定位的精准性,并且余量分布也更加均匀。
1.2 确定定位基准
由于定位基准会直接影响齿形的加工精度,轴类的齿轮齿形加工通常需要采用顶尖的孔定位技术,一些大模数的轴类尺寸则会选择齿轮轴颈和一端面进行定位;盘套类齿轮齿形加工通常都是采用两种定位基准。其主要包括:
第一,内孔和端面定位。需要选择不仅是设计基准,同时也能够实现测量和装配基准的内孔作为主要的定位基准,这样不仅能够保障基准原则的重合性,同时也能够保障齿形加工工序基准的统一性。由于在严格控制内控精度的条件下,专用芯轴在定位上不需要进行找正,因此会大大提高齿轮的生产率。
第二,外圆和端面定位。齿坯内孔在通用的芯轴上安装,并且采用正外圆来决定着孔中心位置。因此,需要保障齿坯外圆对内孔径向跳动要足够小,由于该种方法找正效率较低,通常应用在小批量生产当中。
1.3 齿端加工
齿轮齿端加工主要有倒棱、倒尖、倒圆以及去毛刺等。其中,倒尖、倒圆加工后的齿轮,会沿着轴向滑动从提高啮合度;倒棱工艺能够有效去除齿端的锐边,这些锐边在经过碳淬火后变得非常脆,在齿轮传动中很容易造成崩裂问题。在再用铣刀进行齿端倒圆过程中,铣刀在急速旋转的过程中会沿着圆弧做出往复摆动,通常是每加工一齿则往复摆动一次。在加工完毕过后,工件会沿着径向推出,之后在传送到下一个齿端当中。值得注意的是,齿端加工必须要能够赶在淬火工艺之前,通常都是在滚齿工艺完毕后在进行齿端加工。
1.4 精基准修正
由于在齿轮淬火过后,其精准孔会产生一定的变形问题,为了能够保障齿形加工质量,则需要对基准孔进行修正工作。
第一,外径定心花键孔齿轮通常应用花键推刀进行修正。在修正过程中,推孔需要避免产生歪斜现象,可以采用加长的推到进行引导,这样能够有效避免产生歪斜问题,并且修正效果非常明显。
第二,修正圆柱孔可以采用推孔或磨孔技术,其中,推孔会提高生产效率,主要应用于未经过硬淬工艺的齿轮;磨孔精度高,但其生产效率有待提高,如果齿轮淬火后内孔变形严重、硬度高、内孔大、厚度薄的情况,则可以采用该项技术。在进行磨孔过程中,需要以齿轮分度圆定心,这样即可保障磨孔后的齿圈径向跳动较小,对后续加工工艺非常有益。为了能够有效提高生产率,可以采用金刚镗代替磨孔,生产效率提升明显。
2、高精度齿轮加工方案分析
2.1 加工工艺的特点
高精度齿轮(见图1)相比普通精度齿轮的施工更加复杂,并且所需要确定的参数也非常多。其特点表现在:
第一,定位基准精度要求高。通过分析图 1 可以了解到,其定位基准内孔尺寸精度为准85H5。并且基准端面的粗糙度要求非常高,为Ra1.6μm,端面对基准孔的端面圆跳动为 0.014mm,这几项数据均比普通精度齿轮要求更高。因此,在进行齿坯加工过程中,除了加强端面与内孔垂直度外,也需要预留一定的空间开展精加工。在精加工过程中,其加工孔和端面主要采用磨削工艺,首先以齿轮分度圆与端面作为主要的基准磨孔,再通过磨孔定位的形式来确定基准磨端面,加强对端面调控的控制工作,这样才能够保障齿形加工精度能够满足实际要求。
第二,齿形精度加工要求较高。为了能够保障加工精度要求,其应该选择磨齿的加工方案,也就是通过滚齿——齿端加工——高频淬火——基准修正——磨齿的一系列加工方案,该种的加工方案规定精度为 4 级,但生产率相对较低。因此,在齿面进行热处理过程中,如果必须要采用高频淬火工艺,为了能够降低变形率,可以将磨余量缩小道 0.1mm,这样能够在一定程度上提高磨齿效率。
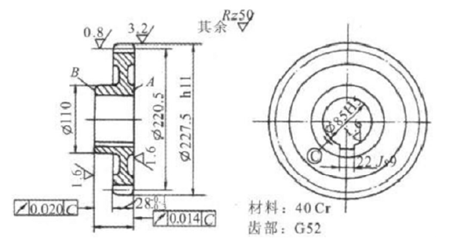
图1 高精度齿轮
2.2 高精度齿轮拉键槽加工中的注意事项
拉键角度需要在显微镜下进行测量,待到合格之后才能够进行拉键。该中施工方法精度非常高,角度检测非常精准,但由于是采用显微镜进行计量,因此,操作起来相对复杂、检测时间长,每检测一个齿轮需要花费25分钟的时间,不适用于大批次的生产,同时也会受到齿端倒角影响,容易产生键槽角度拉键调整问题。为了能够避免上述出现的问题,可以从定位夹作为切入点。需要保障拉键夹具的精度能够满足实际要求。在加工方面,需要制定相应的操作流程标准,尽最大的可能降低人为因素影响。如操作人员是否将工件表面擦干净、拉键定位是否存在杂物、工件定位是否紧靠夹具定位面等,通过多方的考虑才能够保障键槽拉键角度。为了能够保障键槽角度检测的精准性与便捷性,可以需要采用能够将角度误差转变为百分比形式的检测仪器,这样能够提高数据检测的精准性,快速判断拉键槽角度是否精准,从而提高了生产效益,保障键槽角度的精确度。
3、结束语
综上所述,本文重点探究了齿轮工艺方案,主要包括普通精度的齿轮加工工艺和高精度齿轮加工工艺,其中,高精度齿轮加工工艺需要注意定位基准内控精度、基准端面粗糙度、端面对基准孔端面跳动等,其余工艺与普通精度齿轮加工工艺大相径庭,需要根据齿轮实际加工要求合理选择工艺方案。
如果您有机床行业、企业相关新闻稿件发表,或进行资讯合作,欢迎联系本网编辑部, 邮箱:skjcsc@vip.sina.com