大型齿轮加工精度受齿坯自重变形影响的研究
2019-5-23 来源: 武汉大学动力与机械学院 江铃汽车 作者:肖华 曹安全 陶毅 刘青岳 徐科扬
摘要: 大型重载开式圆柱齿轮( 简称大齿轮) 广泛应用于矿山机械、冶金机械各种大型机床中,尺寸大且加工精度要求高,加工过程中齿坯的自重变形会对齿轮精度产生一定的影响,但目前相关研究较少。
先从理论上分析齿坯自重导致的径向变形和周向变形对齿轮精度的直接影响; 然后,从滚齿切削力入手,分析自重变形对齿轮加工精度的间接影响;最后,结合有限元仿真,对比分析在相同工艺方案下 7 个不同规格大齿轮的加工误差,验证了理论分析的合理性。
关键词: 大齿轮; 自重变形; 加工精度
0 引言
在矿山机械、冶金机械及各种大型机床中,大齿轮被广泛用作传动机构。较于其他齿轮,大齿轮一般具有以下特点: 重量大、开式传动、转速低、传动功率大、传动比大及工作寿命长。低精度的大齿轮会造成设备异常振动、噪声及齿面过早磨损,导致齿轮损坏,传动副失效,设备损坏甚至无法运,所以齿轮制造精度往往直接影响设备的运转状况及使用寿命,因此,在加工中要求尽可能地提高齿轮加工精度。
对大齿轮加工精度的影响,就加工过程中的应力变形、热变形、切削力、进给量及振动等因素已有较为深入的研究,但齿坯自重变形对加工精度影响的研究还比较少。
1 、齿坯变形对大齿轮精度的直接影响
齿坯自重变形对加工精度的影响主要发生在最终的滚齿阶段,由于支撑均布在齿坯外圈,在重力作用下,齿坯内圈和支撑两侧会下垂,支撑面处由于两侧下垂会有一定的凸起,齿坯自重变形如图 1 所示。
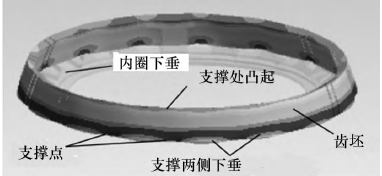
图 1 齿坯自重变形
以支撑面中线与齿坯外圆的交点为原点,以外圆切线方向为 X 轴,径向并指向圆心为 Y 轴,向上为 Z轴,建立右手坐标系,齿坯变形分析坐标系如图 2所示。
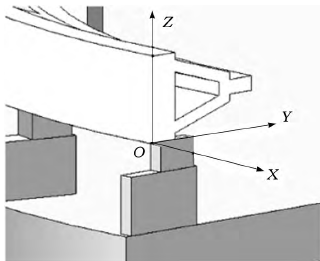
图 2 齿坯变形分析坐标系
1. 1 齿坯径向变形对加工精度的影响
先只考虑齿坯内圈下垂变形对齿形加工精度影响,不考虑支撑两侧下垂以及支撑处凸起变形,不考虑其他影响因素。
由于齿坯内圈下垂,齿坯外圈会向内侧倾斜,滚齿加工时会产生锥齿现象。齿坯径向变形如图 3 所示,在 yz平面内,虚线为理论齿坯形状,实线为实际齿坯截面形状。
设齿坯外缘 OA1与 Z 轴夹角为 α,滚刀按预定轨迹 T1T2T3进行滚齿切削,OABC 为理论齿形,OA1B1C 为 实际加工出来的齿形。
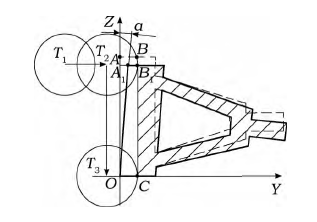
图 3 齿坯径向变形
由于坯自重变形为弹性变形,在实际安装使用过程中可以自动恢复。以齿坯位置为参考,齿坯变形角α 相当于滚刀进给路径反向偏转 α 角,以齿坯为参考的径向变形如图 4 所示,刀具路径为 T11T21T31,T21T31与 Z 轴夹角为 α,OA1B1C 为实际加工齿形。
该变形在齿轮圆周方向基本没有差异,不影响齿轮齿顶圆的加工尺寸,主要影响其齿形误差。加工时在上端面处对刀,径向进给量以上端面齿顶圆为准,由于上端面处齿顶圆最小,所以滚齿时会有少量过切,且过切量沿着齿长方向增加,并在下端面处达到最大值。齿形整体向内移动,轮齿变薄,移动距离为过切量,最大过切量即上下两端面齿顶圆半径之差。
变形齿坯加工出来的端面齿形如图 5 所示,图 5a 为上端面处齿形,是理想齿形; 图 5b
为下端面处齿形,实线为实际齿形; 虚线为理论齿形; 细实线为实际加工齿形的理论齿顶线。
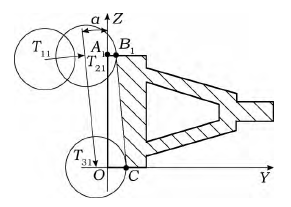
图 4 以齿坯为参考的径向变形
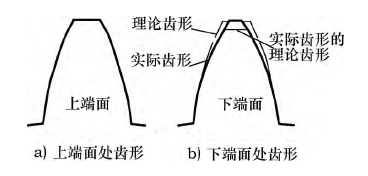
图 5 变形齿坯加工出来的端面齿形
上端面齿顶圆与下端面齿顶圆半径之差为:ΔR = OA1sinα
当齿形加工完成,由于轮齿上端面为标准齿形,而齿厚沿齿长方向逐渐变薄,导致同一轮齿的齿厚不均匀,轮齿齿厚不均匀如图 6 所示,以及齿侧间隙不均匀,进而影响齿轮的使用寿命和传动精度。
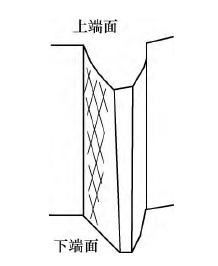
图6 轮齿齿厚不均匀
1. 2 齿坯周向变形对加工精度的影响
在 XZ 平面内,支撑点 O 处向上凸起,两侧下垂,齿坯呈波浪形,设齿坯外缘边线切线与 X 轴最大夹角为 β,滚齿加工时滚刀沿 - Z 轴方向运动,齿坯周变形如图 7 所示。考虑支撑中间凸起对加工精度的影响,忽略其他因素,由于大齿轮直径较大,只考虑局部少数几个齿时可以将之近似作为齿条分析。支撑两侧下垂变形的影响与支撑处凸起变形影响相反。
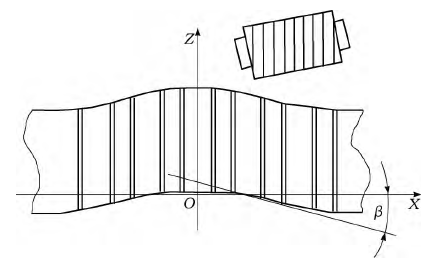
图 7 齿坯周变形
由于大齿轮自重变形为弹性变形,在实际安装使用时,波浪形齿轮端面会恢复成平面。以齿坯为参考,滚刀竖直运动加工倾斜 β 角的齿坯相当于滚刀轴和滚刀路径反向旋转 β 角,以齿坯为参考的周向变形如图 8 所示,图 8 中实线为实际加工齿形,虚线为理论齿形。
由于滚刀相对于理论位置倾斜了 β 角,所以滚切出来的轮齿为斜齿,且 Z 轴两侧轮齿的倾斜方向相反。斜齿直接会影响齿轮的齿距累积误差,影响齿轮传动的准确性。设理论齿宽为
B 由支撑两侧下垂变形引起的齿距累积误差为:

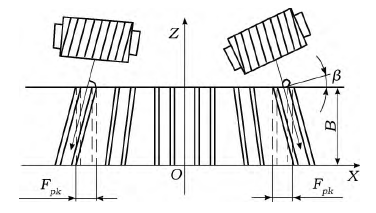
图 8 以齿坯为参考的周向变形
由于产生了斜齿,上端面齿形与下端面齿形在水平面上投影不完全重合,齿侧间隙变窄,齿隙减小量ΔL = Btanβ,变形对齿侧间隙的影响如图 9 所示。同时,斜齿还会导致传动啮合时不能与对应齿轮完全接触,影响载荷分布的均匀性。齿轮啮合局部斜齿接触不良如图 10 所示,阴影面积为斜齿与理论直齿轮啮合时的实际接触区域。齿坯的周向变形会导致加工时产生相反方向的斜齿,增大齿距累积误差,直接影响传动精度,同时会影响齿侧间隙和载荷分布均匀性,使齿轮在传动时接触不良过早磨损,影响齿轮传动的平稳性和使用寿命。
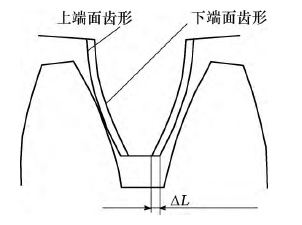
图 9 变形对齿侧间隙的影响
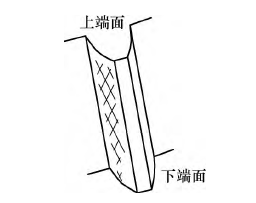
图 10 齿轮啮合局部斜齿接触不良
2 、齿坯自重变形对齿形精度间接影响
齿坯自重变形使滚刀与齿坯相对位置发生改变,影响齿轮滚刀的切入角度和切削深度,进而影响齿轮切削过程中切削力的大小。当切削深度增大时,切削力也随之增大,并且切入角度的改变对刀具的稳定状态也会产生一定的影响。
径向切削力的反作用力会使滚刀刀杆产生一定的挠性变形,使得滚刀与齿坯的中心距增大。而在滚齿过程中,切削力的变化会使变形量发生 改 变,从 而 使 滚 刀 与 齿 坯 的 中 心 距 发 生改变。齿坯的径向变形使整个齿坯呈锥形,进入稳定切削状态后,滚刀从上到下切削深度逐渐增加,切削力逐渐增大。
齿坯的周向变形会使得相邻两齿的切削力不同,在滚齿切入时,支撑处向上变形的部分切削力大,非支撑处向下变形,切削力小,滚齿切出时,向上变形的支撑处切削力小,非支撑处切削力大,滚齿切削力会交替增大或减小。滚齿切削力增大会增大滚刀刀杆的弯曲变形量,增大滚刀与齿坯的中心距,使齿形轮廓整体向外偏移,切削力变大的齿形如图 11 所示,实线为实际齿形,虚线为理论齿形。分度圆直径变大,齿高变小,齿厚增加,啮合时齿侧间隙变小。
滚齿切削力变小会减小滚刀刀杆的弯曲变形量,滚刀与齿坯的中心距减小,滚刀切深增加,齿形轮廓整体向内偏移,切削力变小的齿形如图 12 所示,图 12中实线为实际齿形,虚线为理论齿形,分度圆直径变小,轮齿变薄,则齿侧间隙变大。
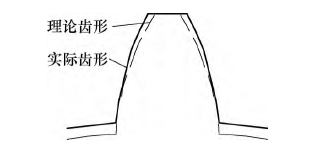
图 11 切削力变大的齿形
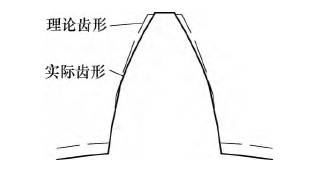
图 12 切削力变小的齿形
由于切削力的增大或减小也会沿着齿长方向改变,齿厚会随之沿着齿长方向改变,增大了齿形误差,降低了载荷分布的均匀性和传动的平稳性以及传动精度。由于齿坯的周向变形呈周期性,切削力会呈现周期性波动,产生周期性误差,影响切削过程的平稳性,使齿廓表面出现波纹,增加了轮齿的表面粗糙度,降低齿形精度。
切削力的周期性变化还会导致机床的强迫振动,对滚齿加工产生较大影响。当激振频率等于或者与机床固有频率相接近时,将可能会引起机床共振,共振严重的时候甚至还会破坏刀具以及机床结构部件,且在齿轮表面会留下振刀纹。在大型数控滚齿机对大型齿轮进行加工时,由切削力而引起的振动将更为明显。会使滚刀、工件主轴及两主轴中心距位置产生较大振动位移,不单影响机床精度更降低齿轮的整体加工质量,并且还会加剧刀具磨损,降低滚刀使用寿命。滚齿本身是一个断续切削的过程,切削力会出现振动,但由于齿坯自重变形导致的切削力变化会进一步加强或减弱这种振动,使得齿形误差波动更大。
3 、实验分析
为验证之前的分析,收集了 7 个实际加工的矿山磨机大齿轮数据,其实验齿轮参数如表 1 所示,材料均为 ZG45。由于齿厚误差可以综合反映齿形精度和齿侧间隙,对大齿轮使用寿命影响较大且容易测量,所以实际生产中选取齿厚误差作为检验标准。实际生产中为了提高检测效率,只在齿轮各分瓣中间以及分瓣结合处取 12 个齿测量轮齿中部实际加工齿厚,选取3 个任意圆,用齿厚卡尺测量相应齿高的弦齿厚。
表 1 实验齿轮参数
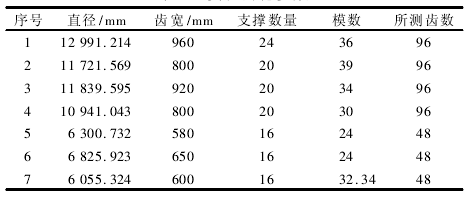
注: 32. 34 为国外标准换算,故有两位小数
3. 1 齿厚误差与齿坯外圈最大变形量之间的关系
由于齿坯外圈变形量在实际加工中难以测量,所以通过 ANSYS 软件对 7 个齿坯分别进行仿真,材料选用铸钢,弹性模量 EX = 2 × 1011Pa,泊 松比 PRXY =0. 3,得到各个齿坯外圈的最大变形量,齿坯外圈变形量仿真如图 13 所示。
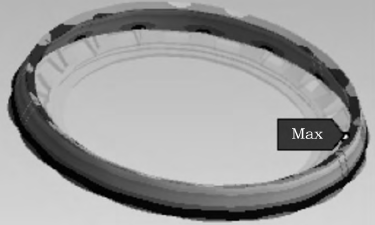
图 13 齿坯外圈变形量仿真
最大变形量发生在相邻两支撑正中间内侧,在径向截面 YZ 内。计算轮齿测量处相应的理论齿厚,用实际齿厚减去理论齿厚取绝对值,得到绝对齿厚误差,再除以理论齿厚得到相对误差。用 Matlab 软件计算各齿轮齿厚误差的平均值和均方差,并计算绝对误差的均值和均方差,所得结果如表 2 所示。
为验证齿厚误差与齿坯自重变形的相关性,用Matlab 求出 7 个齿轮齿厚误差与齿坯外圈最大变形量之间的相关系数,如表 3 所示。
由表 3 中数据可以看出,绝对齿厚误差的各项统计参数与齿坯外圈最大变形量之间有一定的相关性,均方差相关系数最大,为 0. 347 6。相对误差均值与外圈最大变形量之间没有明显的相关性,但均方差有一定的相关性。由前面分析可知,齿坯自重变形会使部分轮齿齿厚增大,部分减小,综合起来对齿厚平均误差影响较小,但会影响齿厚误差的均方差,实验结果验证了这一理论分析。
表 2 各齿轮外圈最大变形量及加工误差
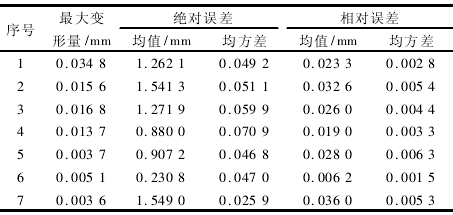
表 3 齿厚误差与外圈最大变形量之间的相关系数

3. 2 齿轮各处齿厚误差与外圈变形量之间的关系
大齿轮在滚齿加工时,为了减小变形量,各瓣结合处放于两个支撑中间,齿坯放置位置及齿厚测量位置如图 14 所示。
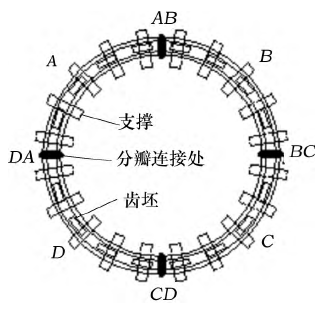
图 14 齿坯放置位置及齿厚测量位置
因此,对于有 20 个支撑的 2 号、3 号、4 号四瓣齿轮,每个齿轮所测的 8 组数据各有
4 组( AB、BC、CD、DA) 位于无支撑的齿瓣结合处和 4 组( A、B、C、D) 位于有支撑的齿瓣中间处。
无支撑处的齿坯外圈最大变形量相对较大,对齿厚误差的影响可能也更大。用ANSYS 对 2
号、3 号、4 号三个齿坯分别进行建模仿真,得到齿坯外圈支撑处和无支撑处的最大变形量。将各个齿轮所测数据分为有支撑和没有支撑的两组,用 Matlab 分别求取均值和均方差进行比较分析( 由于3 个齿轮直径、齿厚相近,所以只考虑绝对误差) 。3个齿轮有支撑和无支撑处的外圈最大变形量以及齿厚误差均值与均方差如表 4 所示。
表 4 外圈最大变形量与齿厚误差
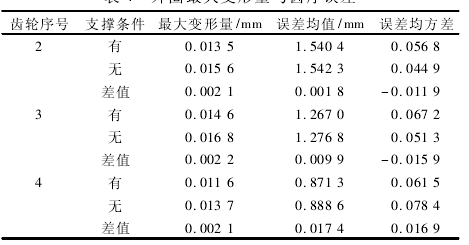
从 3 个大齿轮各处误差数据看,齿坯无支撑处均比有支撑处变形量大,同时变形量大的地方齿厚误差均值整体偏大。而且对不同的大齿轮,变形量差值越大,齿厚误差均值的差值也越大。但均方差值与齿坯外圈最大变形量之间没有明显关系,可能因为齿坯外圈变形量最大值一般不超过 0. 04mm,相对于齿轮直径和齿厚都非常小,在加工过程中机床振动、刀具磨损、工作台误差及温差等因素都会影响齿轮的加工精度,实验数据中齿厚误差均方差与齿坯变形量之间的关系不是特别明显。
4 、结语
加工大齿轮时,齿坯自重变形会导致锥齿和斜齿以及振动现象,使大齿轮轮齿沿齿长方向齿厚不均,影响齿侧间隙、齿距累积误差、齿形误差进而影响大齿轮的传动精度和传动平稳性和载荷分布的均匀性,影响大齿轮的使用寿命。在加工过程中尤其是滚齿阶段应采用较多的支撑减小齿坯自重变形,以提高齿轮加工精度。
投稿箱:
如果您有机床行业、企业相关新闻稿件发表,或进行资讯合作,欢迎联系本网编辑部, 邮箱:skjcsc@vip.sina.com
如果您有机床行业、企业相关新闻稿件发表,或进行资讯合作,欢迎联系本网编辑部, 邮箱:skjcsc@vip.sina.com