用于电火花加工抬刀运动的速度规划算法
2017-2-27 来源:上海交通大学机械与动力工程学院 作者:刘宏达,陈昊,陈默,奚学程,赵万生
摘要:电火花加工时,通过采用周期性的抬刀运动来降低放电间隙中的蚀除物浓度,能在改进有效放电率的同时提高加工的稳定性。目前用于电火花加工抬刀运动的速度规划算法,如常数加加速度S 形曲线速度规划,其加加速度变化是不连续的,常数加加速度由于阶跃变化会引起机床的冲击和振动,使放电间隙状态变得不稳定,从而导致加工的不稳定。提出了一种用于抬刀运动的连续加加速度的速度规划算法,根据抬刀最大速度、抬刀高度及机床Z 轴允许的最大加加速度进行基于连续加加速度的速度规划。通过对该速度规划算法进行的加工比较验证实验可知,运用该速度规划方法可在保证加工效率的基础上,更好地减少对机床的冲击和振动,使加工过程更稳定。
关键词:电火花加工;抬刀运动;S 形曲线速度规划;连续加加速度
电火花加工材料去除是通过在电极与工件之间的绝缘通道中产生一系列放电完成的,放电产生的蚀除物不利于稳定加工[1]。为了提高有效放电率及加工稳定性[2-4],通常采用周期性的抬刀运动将蚀除物从放电间隙中排出,同时使清洁的工作液能进入放电间隙,降低间隙中的蚀除物浓度。
为了减小因抬刀启动和停止时带来的机床冲击, 必须对抬刀运动中的加减速过程进行速度规划, 否则易导致过冲等影响放电间隙状态的稳定,从而影响加工的稳定性[5]。目前主要采用的加减速规划算法有梯形速度曲线和S 形速度曲线[6],这两种速度规划算法都能使速度得到很好的平滑。梯形速度曲线是一种速度最优曲线[7],虽然算法简单,但加速度不连续,在抬刀运动过程中加速度会产生突变,产生的高频谐波将导致机床发生较大的冲击和振动[8-9],不适于抬刀运动速度控制。
Jahanpour 等[10]提出了一种基于指数加加速度的S 形五段速度规划方法,用2 个速度斜率校正系数来控制每个尖角的加减速状态,同时用基于加速度和加加速度非线性约束的模式搜索算法,计算每个尖角的加速状态,使总的加工时间最小。梁速等[11]开发了基于PMAC 运动控制卡的五轴联动电火花加工数控系统, 实现了主轴最高速度达12 m/min、最大加速度约1 g 的稳定高速抬刀性能, 其加工窄缝的性能显著优于普通电火花加工机床;但其使用的基于常数加加速度的S 形速度曲线,在高速抬刀时易带来冲击,导致过冲量大,必须增加缓冲区来减小过冲对放电间隙的影响。而基于正弦加加速度的S 形速度曲线,其速度、加速度、加加速度都是连续的,使系统具有更高的柔度,完全避免了柔性冲击[12]。
为了减少因常数加加速度阶跃变化引起的机床冲击和振动,本文对现有的用于电火花加工抬刀运动S 形曲线加减速规划进行了改进,提出了用于电火花抬刀运动的连续加加速S 形曲线加减速规划方法,并通过实际加工实验进行了验证。
1.基于连续加加速度的S 形速度曲线
1.1 S 形速度曲线
在数控机床伺服系统中,对运动轨迹进行良好的速度规划不仅能提高加工的稳定性及加工质量,还能使插补更易实时实现。在高速切削加工中要求刀具进给速度变化平稳,而常规的梯形曲线加减速过程中存在加速度不连续,因而在运动过程中易使机床及刀具产生冲击和振动。基于S 形速度曲线的加减速方法由于速度变化曲线和加速度变化曲线都是连续的,很大程度上避免了冲击,故在高档数控机床上广泛使用。文献[13]讨论了S 形速度曲线的各种加减速情况,复杂情况下可分为以下7 个阶段:加加速阶段、匀加速阶段、减加速阶段、匀速阶段、加减速阶段、匀减速阶段和减减速阶段。在加速度充分大的情况下,可将速度规划分成5 段。为了简单起见,本文用5 段式速度规划曲线来描述[14]。
如图1 所示,假设加加速、减加速、加减速和减减速的时间都相同,设为T,初始加速度、初始速度和初始位移均为0,最大加加速度为jmax。那么,任何时刻的加速度a(t)、速度V(t)及位移S(t)都能通过对加加速度的积分计算得到:
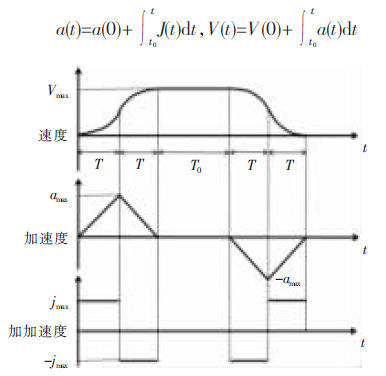
图1 常数加加速度S 形加减速曲线

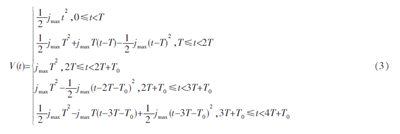
式中:Vmax=jmaxT2 为在最大加加速度jmax条件下,加速时间为2T 情况下能达到的最大速度。
1.2 基于连续加加速度的S 形速度曲线
基于常数加加速度的S 形曲线加减速在很大程度上避免了机床的冲击和振动,但由于加加速度为常数,使机床柔性仍显不足,且易在抬刀即将结束时产生过冲,难以稳定地保证几十微米的放电间隙, 需增加一个距离大于过程量的抬刀缓冲区,使过冲不影响加工区域。针对该问题,本文提出了基于连续加加速度的S 形速度曲线加减速算法。采用正弦曲线加加速度进行速度规划,与前节提到的常数加加速度S 形曲线一样处理, 那么,积分得到的加速度、速度及位移均是连续的。如图2所示,假设加加速、减加速、加减速及减减速的时间都相同,设为T*,初始加速度、初始速度和初始位移均为0,最大加加速度为jmax。那么,任何时刻的加速度a*(t)、速度V*(t)及位移S*(t)都能通过对加加速度的积分计算得到:
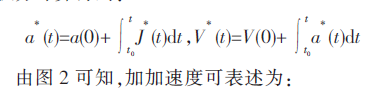
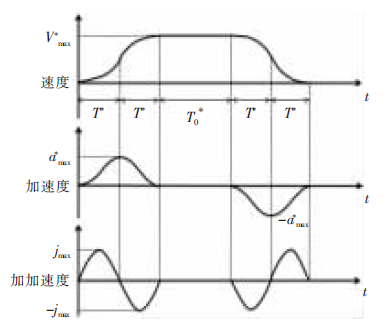
图2 连续加加速度S 形加减速曲线
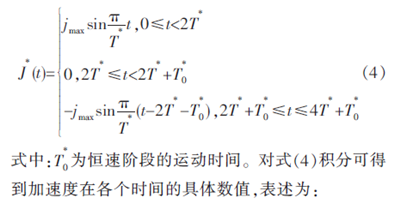




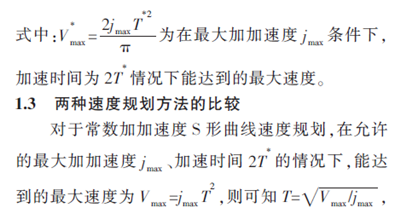
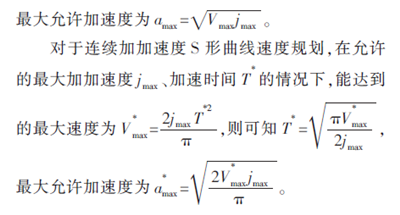
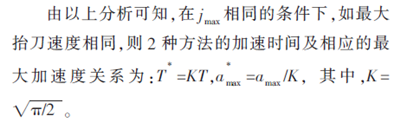
2.MATLAB 仿真结果
对2 种基于不同加加速度的S 形速度曲线进行仿真,设定机床最大加加速度为jmax =80 000 mm/s3,最大速度为Vmax =50 mm/s,加速时间T=0.025 s,由1.3 节的推论可确定相应的T* 。仿真结果见图3,其中直线表示连续加加速度,虚线表示分段常数加加速度。
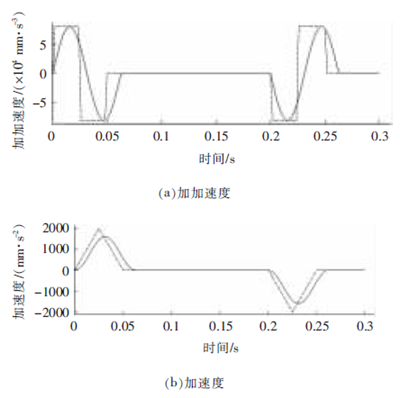
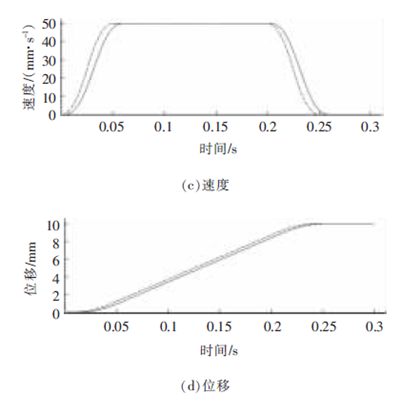
图3 两种加速方法的仿真对比
从仿真结果可看出,2 种方法在加速度、速度和位移曲线上均能保持连续且平稳的过渡。在抬刀高度为10 mm 的加减速过程中, 当速度从0 加速到Vmax=50 mm/s 时,无论是加速度、速度还是位移,常数加加速度方法的快速性都要好于连续加加速度方法,且在加速过程中,常数加加速度方法实际需要的加速度是大于连续加加速度方法的,这也造成其在回退至抬刀起点时易产生过冲,必须增加缓冲区来保证放电间隙状态的稳定。同时,连续加加速度方法的加加速度是连续的,在抬刀启动和停止时能更好地减少机床的冲击和振动, 减少丝杠磨损,延长机床使用寿命,还能有效减少抬刀回退过程中的过冲,保证了放电间隙状态的稳定,有利于加工的稳定。
3.窄槽加工实验
本文提出的改进型S 形曲线速度规划方法主要针对电火花加工过程中的抬刀运动,而深窄槽的加工能很好地验证抬刀性能。为了检验改进的抬刀运动速度规划算法的稳定性和可靠性,本文将其运用HE70 型电火花加工机床,并与PMAC 运动控制卡提供的基于特征参数Ts、Ta及Vmax自行规划S曲线加减速的插补器提供的抬刀速度规划进行对比实验。其中,Ts为S 曲线加减速阶段所需的时间;Ta为整个加减速过程所需的时间;目标速度Vmax为经过S 曲线加速后进入匀速状态的最大速度。
加工实验为Z 轴单轴加工,工件为45 钢,电极为70 mm×20 mm×2 mm 的石墨电极, 加工深度为10 mm,采用正极性加工。具体实验条件见表1。
表1 窄槽加工实验条件
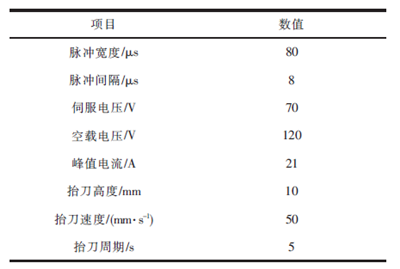
实验发现,采用本文方法加工一个10 mm 的深窄槽平均用时约40.7 min,而采用PMAC 卡提供的S 形曲线规划方法平均用时约40.5 min。可见,本文提出的方法并未明显降低加工效率,但由于连续加加速度方法的加加速度是连续的,在抬刀启动和停止时能更好地减少机床的冲击和振动,最大程度地减少了对机床的柔性冲击。加工的窄槽及微观放大图见图4。
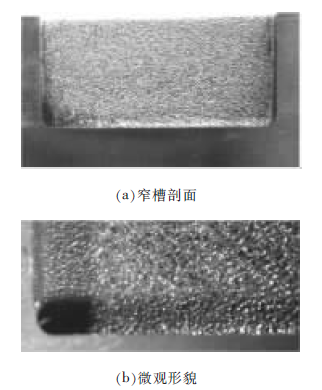
图4 窄槽加工图
4.结束语
针对电火花加工过程中抬刀运动S 形速度曲线加加速度不连续的问题,本文提出了一种用于抬刀运动的连续加加速度的速度规划算法。该方法根据抬刀高度、抬刀最大速度及机床主轴允许的最大加加速度进行基于连续加加速度的速度规划。加速过程与减速过程的时间相同,且加加速度、加速度和速度表达式也相同。为了验证该速度规划算法的性能,对其进行了加工比较实验。结果表明,运用该速度规划方法在保证加工效率的基础上,能更好地减少对机床的冲击和振动, 使加工过程更稳定,且通过多次实验验证了该方法的稳定性与可靠性。
投稿箱:
如果您有机床行业、企业相关新闻稿件发表,或进行资讯合作,欢迎联系本网编辑部, 邮箱:skjcsc@vip.sina.com
如果您有机床行业、企业相关新闻稿件发表,或进行资讯合作,欢迎联系本网编辑部, 邮箱:skjcsc@vip.sina.com
更多相关信息