基于电极切向旋转进给法的低刚度锥杆类零件精密电火花加工
2017-2-20 来源:上海交通大学 作者:梁统生 陈葆娟 朱力敏 顾琳
摘要: 提出了基于圆盘电极切向旋转进给法的低刚度锥杆类零件的电火花精密加工方法。首先介绍了基于等厚损耗原则的圆盘电极设计原理,进而通过电火花加工工艺的三因素全因子实验考察了峰值电流、脉宽、占空比对工件材料去除率(MRR)、相对电极损耗率(TWR) 和表面粗糙度(SR) 的影响, 并对电火花加工工艺参数进行优化从而应用于锥杆类零件的加工。加工出的反馈杆性能一致性高、表面质量好,加工时间短,试验结果表明基于圆盘电极切向旋转进给法的电火花加工工艺对提高低刚度锥杆的加工工艺的可靠性和加工效率、提高电极利用率方面有较大优势。
关键词:圆盘电极;切向旋转进给法;低刚度锥杆;全因子实验;电火花加工
0.引言
航天设备中的某型反馈杆,其关键部分为细长锥杆结构,属于低刚度细长杆类零件。由于该型反馈杆的刚度和精度要求特别高,因此其形状、尺寸精度和表面质量及性能一致性要求极高。通常,此类零件采用精密车削加工,通过反复加工—测量—再加工及大量生产、严格选配的方式来保证尺寸及性能的一致性要求,导致生产效率低下,废品率及返修率高。对此类零件,一般机械加工容易使其受力变形,难以达到加工要求,而电火花加工是利用电火花放电产生的高温来蚀除工件材料,加工过程中,电极和工件不直接接触,没有机械加工宏观的切削力,因此适合低刚度工件及微细轴的加工[1]。最初电火花加工微细轴的方法是块状火花磨削法,亦称反拷块法,如图1所示。
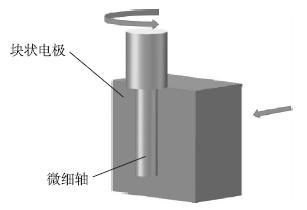
图1 成形块反拷法原理
该工艺方法的电极损耗不能自动补偿,从而难以控制加工尺寸精度,需要反复加工—测量—再加工等较多人工干预,加工成品率很低。采用线电极磨削(WEDG) 技术,如图2 所示,虽然可以实现高精度的加工[2-8],但WEDG加工的效率非常低,并不适于在生产中广泛应用[9]。对此,哈尔滨工业大学的耿春明等提出了块状电极切向进给电火花磨削方法[10-12],既保持了成形块反拷法的高加工效率又可实现电极损耗的自动补偿。然而,利用块状电极切向进给法在磨削锥杆时,由于沿锥杆轴向的材料去除体积并不相同,直径较小的前端去除量远小于直径较大的锥杆根部的去除量,如图3 所示。当锥杆前端达到预定尺寸时,其根部尚有部分余量需要去除。若此时停止加工,会导致锥角偏大,因此电极块需要继续进给,从而增加了加工时间和电极块的使用长度,也降低了电极利用率。针对这些问题,本文基于电极等厚度损耗原则设计了用于锥杆类零件加工的圆盘电极,并采用切向旋转进给的方法实现3J40 材料微细锥杆的电火花精密加工,从而大大提高了电极利用率和加工效率。
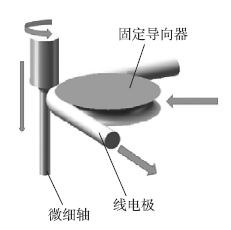
图2 线电极磨削原理
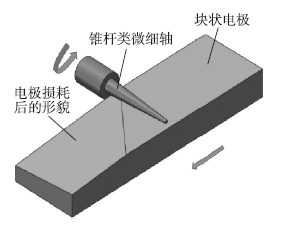
图3 切向进给法原理
1.圆盘电极切向旋转进给电火花加工
1.1 基于等厚度损耗理论的圆盘电极设计
等厚度损耗是指加工时,电极沿锥杆轴线方向的平均损耗厚度ΔHm相同。假定在同一加工参数下,相对电极损耗率沿锥杆轴线不变,电极沿锥杆轴线损耗平均厚度ΔHm和工件沿轴线蚀除厚度Δh 相同。在加工完成时,圆盘电极转过角度为α,在圆盘电极的锥顶处,直径为d,电极损耗的体积微元为:

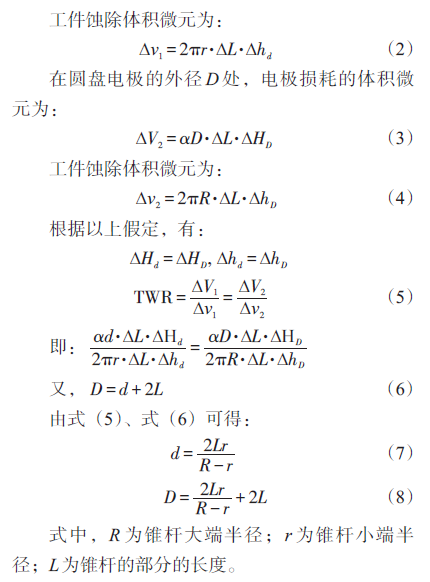
1.2 圆盘电极切向旋转进给电火花加工
圆盘电极切向旋转进给电火花加工的原理如图4 所示,圆盘电极预先加工出所需的锥面,安装在Z轴上,其旋转轴线与Z轴主轴共线,并且可以绕主轴旋转。工件夹持于R 轴并水平放置,工件轴线指向圆盘电极旋转轴线。加工过程中,电极不旋转并进给到指定位置,此时圆盘电极的锥面
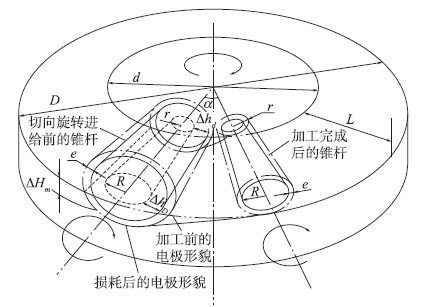
图4 圆盘电极切向旋转进给电火花加工原理图
与工件最终形状的锥面距离为放电间隙e,然后电极开始缓慢旋转,使用未损耗的部分蚀除工件,当无放电产生时结束加工,最终获得的形状即为所需形貌。
2.电火花加工工艺参数探索实验
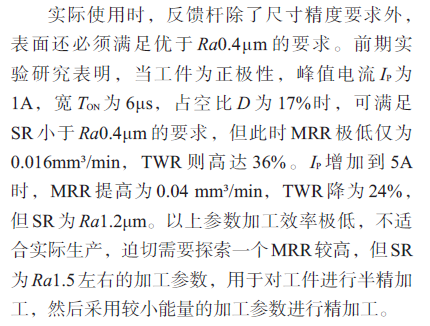
2.1 实验装置
实验在BIEM-Sodick C40 电火花成型机床上实施,工件装夹在精密旋转R 轴上(System 3R 公司:转速范围为200r/min~2000r/min),装置如图5所示。为了方便测量表面粗糙度,工艺参数探索实验时,工件不旋转;探讨这种新型的加工工艺的可行性试验时,工件旋转。表面粗糙度用MitutoyoSJ-210 表面粗糙度仪测量;加工前后,工件清洗烘干并用量程为210g、分辨率为0.001g 的电子称称重。
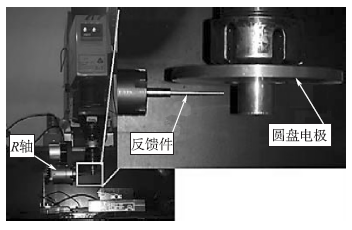
图5 实验装置
2.2 实验条件
实验过程中,电极材料为紫铜,工件材料为高温恒弹性镍铁精密合金3J40。3J40 是常用的精密仪器仪表元件材料,密度为8.2g/cm3。该材料除了具有良好的弹性性能外,还具有硬度高、弹性模量温度系数低和内耗小等性能。本实验采用参数如表1所示。
2.3 实验设计
影响电火花加工参数的参数很多,前期的部分因子实验结果表明Ip、TON、D对MRR、TWR和SR三个响应具有显著作用,因此在全因子实验中选用它们作为考察因素,利用Minitab 软件设计了两水平外加4 个中心点的全因子实验,研究了三个主要参数对MRR、TWR和SR 的影响及其交互作用。实验设计与结果如表2所示。
表1 电火花加工工艺参数
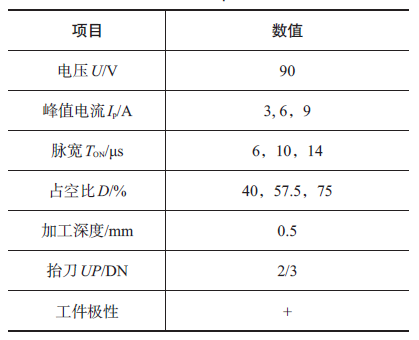
表2 实验设计与结果
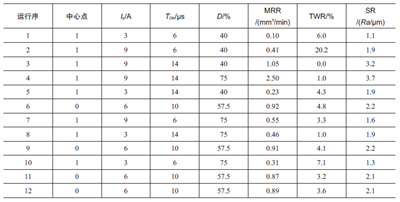
3.实验结果分析与加工验证
3.1 实验结果分析与优化
实验分析显示Ip 、TON 、D和Ip与TON的交互作用对MRR的影响是显著的。在实验所选参数范围内,D越大MRR越大,MRR与Ip 、TON的等值线图如图6 (a) 所示,D一定时,同时增大Ip和TON可以提高MRR;Ip 、TON以及Ip与TON的交互作用对SR 是显著的,而D 对SR 几乎没有影响,SR 与Ip、TON的等值线图如图6 (b) 所示,同时减小Ip和TON 可以减小SR。由此可见要同时获得较大的MRR与较小的SR是相互矛盾的,因此,本文利用Minitab 的优化响应器求解得到一个理想的加工参数,使获得较大的MRR时,SR不至于过大。优化时,设置MRR 为望大,望目为3.0,下限为0.3;SR 为望小,望目为Ra0.4μm,上限为Ra2.0μm;TWR为望小,望目为0,上限为15%。优化结果如下,当Ip为7.97A,TON为6μs,D为75%时,理论MRR 为0.66mm3/min, TWR 为3.5% , SR 为Ra1.68μm,适合半精加工。
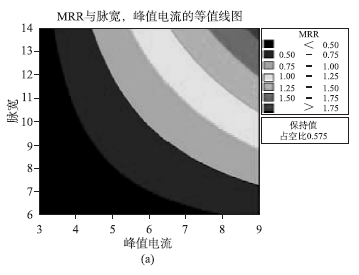
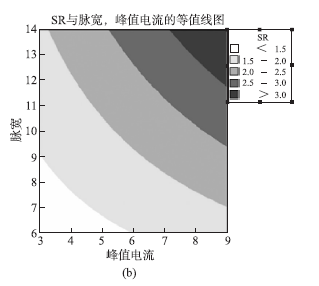
图6 MRR、SR与Ip、TON的等值线图
3.2 加工验证
本文最后采用优化后的加工参数,采用半精加工再精加工的策略,利用圆盘电极切向旋转进给法对反馈杆锥杆进行半精加工,保留单边余量10μm,而后采用Ip为1A,TON为2μm,D为75%进行精加工,加工完成的试件及其表面形貌如图7 所示。对同一批次完成的6 根反馈杆零件进行检测,
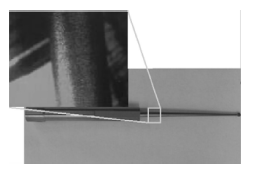
图7 反馈杆样件图
结果如表3 所示,实验结果表明,基于圆盘电极切向旋转进给法电火花精密加工低刚度锥杆类零件的加工工艺方法是可行的,加工出的锥杆刚度等性能一致性高、表面质量好,而且电极利用率高。
表3 反馈杆检测数据
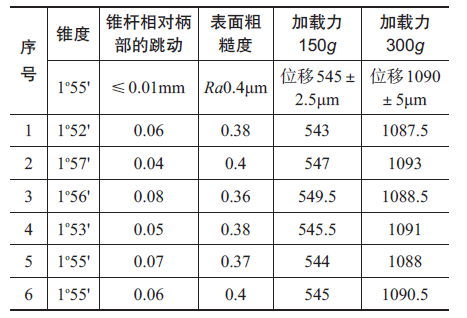
4.结论
本文在理论和实验上研究了基于圆盘电极切向旋转进给法的低刚度锥杆精密电火花加工工艺的可行性,并对加工参数进行了优化。结合实验可得出以下结论:
1) 理论计算表明,采用圆盘电极旋转切向进给法可实现电极等厚度损耗,能缩短低刚度细长锥杆的加工时间。
2) 在实验所选参数范围内,增大占空比、同时增大峰值电流和脉宽均能增大3J40 的MRR,然而同时增大峰值电流和脉宽时,表面粗糙度值SR变大,而占空比对SR几乎没有影响;
3) 基于圆盘电极切向旋转进给法电火花加工低刚度锥杆的加工工艺方法是可行的,加工出的反馈杆性能一致性高、表面质量好,加工时间短,电极利用率高。
对于锥杆头部圆球的加工工艺,目前采用车削加磨削的方法加工。由于电火花磨削法可以加工出质量较好的锥杆,同样可以考虑采用杯形电极电火花磨削法来尝试加工锥杆头部圆球,如果此方法可行,便可实现在同一电火花机床上完成反馈杆的锥杆与锥杆头部圆球的加工,从而大大减少工件装夹次数从而提高生产效率。
投稿箱:
如果您有机床行业、企业相关新闻稿件发表,或进行资讯合作,欢迎联系本网编辑部, 邮箱:skjcsc@vip.sina.com
如果您有机床行业、企业相关新闻稿件发表,或进行资讯合作,欢迎联系本网编辑部, 邮箱:skjcsc@vip.sina.com
更多相关信息