发动机动、静叶片激光电火花复合制孔加工工艺技术研究
2017-2-9 来源:中航工业西安航空发动机(集团)有限公司 作者:陈阳,朱红钢,王增坤,王辉明,石银喜
摘要:激光、电火花制孔这两种加工方法有一个共同的、主要的应用范围,即可经济而高效地对复杂的身体形状作精细加工,且可应用于难加工材料,已成为航空工业一种不可取代的加工工艺新方法。由于这两种加工方法有非凡的加工能力和互补优势,当今已稳定地用在现代航空制造业中。
关键词:激光制孔;电火花制孔;复合加工工艺;动静叶片
在航空发动机中,各类型的动静叶片在气膜孔加工中,由于叶片铸造型面不一致、加工工艺欠优化、可达性差等问题,存在气膜孔位置、孔径超差、连孔等诸多质量问题,造成激光、电火花都无法单工艺实现本工序加工。且各自工艺的短板,成为影响发动机片动静叶片质量的瓶颈及交付。通过优化工艺及加工参数, 同时采用激光、电火花复合加工的方式, 对加工工序进行合理调配,对零件型面进行探测研究,减少零件型面误差对加工的影响。
1.激光、电火花打孔的优缺点
1.1 激光打孔
激光打孔的缺点:被加工孔的精度和表面粗糙度尚不够理想。激光打孔的优点有:
(1)激光不仅能对置于空气中的工件打孔,而且也能对置于真空中或其他前提下的工件进行打孔。
(2)因为加工过程与工件不接触,故加工出的工件清洁。因为加工时间短,故对被加工的材料氧化、变形、热影响区域均较小,不需特殊保护。
(3)可加工各种材料的微孔。一般机械钻头只能钻出直径大于250 μm 的孔, 而激光则能加工出10 μm 以下的孔。就加工种类来看,不仅可对金属而且可对非金属甚至橡胶等进行钻孔。从深径比来看,用激光打出的孔,其深度与孔径之比,可高达50以上,这是用其他加工方法难以达到的。如用一般方法在极硬的氧化铝陶瓷上加工小孔所得到的深径比为2,超声波法只有4,而激光可达25。
1.2 电火花打孔的优缺点
电火花打孔的优点有:
(1)加工孔径范围一般在0.3~3 mm 之间,深径比能达200∶1 以上。这是其相比于其他工艺非常重要的一个优点,即对小径深孔的加工。由于高速电火花小孔加工技术使用水基工作液作为加工介质,因其电导率大,在极间电压作用下会产生介电系数与水不同的氢气,从而导致放电间隙增大,增加击穿延时,提高效率。另外,由于在加工过程中,脉冲间隔很小,使脉冲频率大大增加,脉冲电源的有效利用率大大增加,进一步提高了效率,获得了高效的生产率。
(2)加工速度一般能达20~60 mm/min,且加工深度对其影响相对不大,是电火花加工第一次在速度上能与机械加工相比拟。与常规电火花小孔加工技术相比, 由于水基工作液高速地流过工作间隙,将放电间隙中的蚀除物迅速排出间隙,并有良好的冷却性能,因而整个过程速度快,消电离过程快,精度高。
(3)直接从斜面、曲面穿入,加工盲孔、深孔、斜孔及异形孔等。
(4)不受材料的硬度及韧性限制,除了能加工一般的导电材料以外,还能顺利加工不锈钢、淬火钢、硬质合金、钦合金、淬钢等难加工材料。而普通加工方法手材料还有刀具的硬度和韧性限制较大。
(5)加工孔的尺寸一致性,一般能在0.03~0.05mm 之间,圆度在0.02~0.03 mm 之间,表面粗糙度Ra3.5 μm 左右,能满足一定的垂直度要求。电火花打孔的缺点有:
(1)放电间隙狭窄。电火花放电加工中工具电极与工件间的绝缘工作介质有一定的介电常数,放电加工时有一定的击穿间隙(放电间隙),因此放电加工后工件的尺寸与工具电极的尺寸并不完全一致。且放电间隙是随电参数、电极材料、工作液等因素的变化而变化的,从而影响了加工精度。间隙越大,则复制精度越差,特别是对复杂形状的加工表面。如电极为尖角时,而由于放电间隙的等距离,工件则为圆角。因此,为了减少加工尺寸误差,应采用较弱小的加工规准,缩小放电间隙,另外还必须尽可能使加工过程稳定。
(2)易出现加工锥度和圆角。由于工具电极下面部分加工时间长、损耗大,因此电极变小,而入口处由于电蚀产物的存在,易发生因电蚀产物的介入而再次进行的非正常放电(即“二次放电”),因而产生加工斜度。这就要求高压水质工作液必须有一定的速度,且持续工作。
(3)工具电极损耗严重。电火花加工是靠高温熔化气化金属实现对工件的加工,工具电极必须是导电金属用来传导电能,所以在高温和带电粒子的撞击作用下工具电极也存在损耗,特别是在电参数选择不当的情况下,电极的损耗更加明显。
2.实验过程及加工工艺方法
2.1 激光加工实例
某机的高压涡轮导向叶片加工组合件需加工排气边1 排(8-φ0.7+0.1 0),进气边3 排(25- φ0.4+0.1 0)共4 排33 个气膜孔(图1)。

图1 高压涡轮导向叶片加工组合件气膜孔分布示意图
以前工艺方案为电火花加工,效率低。零件为铸件,铸件型面公差大,叶片型面一致性差,孔位置度难以保证。按照要求的叶片型面线轮廓度为0.2mm,由于逐渐的加工难度较大,只能保证叶片型面在0.4 mm 左右,严重影响了气膜孔加工的位置度。通过对现有工艺分析,进气边3 排孔中,两排气膜孔壁薄,孔出口距型腔内壁较远,可塞保护材料进行有效保护,故改为激光加工,因激光加工无法有效控制加工深度, 另一排距型腔内壁很近,无法添加保护材料,存在击伤内壁的隐患,所以这排仍采用电火花加工。排气边孔为型腔内角度斜孔,加工深度大,加工空间狭小,无法采用激光加工,故仍采用电火花加工。通过加工工艺的改进(图2),由以前的电火花加工优化为激光-电火花复合加工,从而使加工效率得到很大提高。
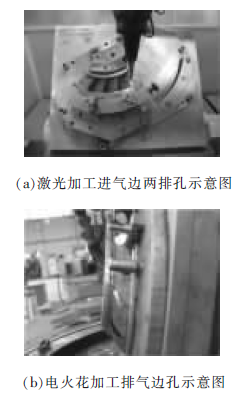
图2 激光-电火花复合加工示意图
存在问题:
(1)零件型面对加工的影响。零件为铸件,型面公差大且一致性差,加工中需根据零件型面调整孔位,加工效率低。型面公差大还影响到加工深度,4排孔的出口都在狭小的型腔内,空间小(图3),加工中存在击伤内腔的隐患。加工时无法设定一个固定的加工深度, 只能根据加工情况手动调整加工深度,以保证孔径,避免击伤零件。
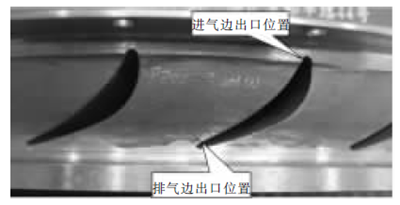
图3 零件型腔示意图
为降低零件型面对孔位置度的影响,加工时需根据零件型面情况对孔位进行调整。孔位调整步骤为:标准样件确定加工孔位→编制加工程序→加工试件→测算试件和标准件型面差异对孔位的影响量→调整孔位→修改加工程序→加工正式零件。
(2)排气边孔加工效率低。排气边孔为型腔内的斜孔,加工中选用细长杆导向器,避免与夹具发生干涉。所用电极为400 mm 长的铜管电极,因选用细长杆导向器,使电极的有效使用部分变小,加工效率低。孔的入口位于型腔斜面上,加工可靠性差,加工时电极沿型面滑动,孔位确定困难。加工时选用合理的加工参数,改善加工时的冲液状况,以提高加工稳定性和加工效率。
2.2 电火花加工实例
使用ZT-017 型电火花小孔机床加工, 电极材料为黄铜,直径分别为0.25、0.35 mm,长300 mm,加工前找正夹具外圆跳动在0.01 mm 以内。用去离子水作为工作介质,电导率为0.1×103 μs/cm。
2.2.1 加工过程与步骤
(1)装夹电极,校正电极基准面与工作台的位置精度,保证装夹可靠。
(2)以榫齿和侧平面为定位基准面装夹工件,加工时将工件以定位面为基准,装夹后校正与电极的相对位置。机床可建立及变更坐标系统原点,利用高灵敏度和快速响应速度的置零功能,能实现电极对工件的定位、找正。校正电极与工件的相对位置后将工件固定,移动主轴头,使电极下端面与工件上平面保持合适的距离。
(3)打开工作液泵,将压力调到8 MPa,工作液由循环系统进入密封夹头,再通过电极中部毛细管孔进入加工区,启动脉冲电源与控制系统,调出编制好的加工程序,准备进行加工。
(4)加工时根据加工稳定状态调节进给速度、冲液压力等。通过参数显示屏随时观察孔的加工深度、电极损耗及加工时间等。加工过程中应抽查孔的尺寸和加工表面情况,以保证零件的加工品质。
2.2.2 试验结果
试验加工参数见表1,试验现场见图4。利用电火花工艺进行高压涡轮叶片气膜孔加工,产品品质明显改善,效率与叶片加工合格率大幅提高,零件合格率提高到80.7 %,加工成本显著降低。加工品质与效率的提高使发动机的按时交付得到了保证。
表1 气膜孔电加工参数
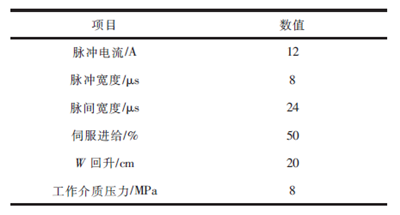
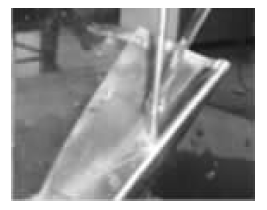
图4 工作叶片加工现场
2.2.3 加工工艺难点分析与对策
在试验过程中发现,采用小孔机加工气膜孔的难点主要表现在加工深度控制、加工设备稳定性与精度的提高、加工中硬件故障的判断与排除等。在分析原因的基础上, 结合实际情况来制定解决措施,取得了良好效果。
2.2.4 加工深度的控制
由于目前使用的电火花加工设备使用半闭环系统,加工深度信号没有反馈,所以无法准确控制加工深度。高压涡轮叶片, 内腔距离仅为0.198~0.215 mm。如何保证既把孔打通又不打伤或打穿叶片内腔对面基体的难度非常大。现采取以下措施来解决问题。
(1)软阻断。计算出所有孔各截面穿头深度,根据电极长度消耗值,按尺寸公差偏上差计算加工深度,并将深度值固化在程序中,控制电极加工深度。
(2)硬阻断。将一个长80 mm、宽1.85 mm、厚0.8 mm 的铜条插入叶片腔体, 用来阻挡电极损耗,防止打伤或打穿叶片。
(3)补加工工艺方案。当遇到叶片壁厚不均匀、电极品质不好、机床故障等特殊情况,造成孔没有打通时,分别编制了直径0.3、0.5 mm 孔的补加工程序,对通孔位进行补加工。
2.4.5 加工设备稳定性与精度的提高
试验发现,电火花设备的B 轴、旋转头、泵、电器等设备易出现故障。B 轴刚性差, 易出现位置偏移,造成第6~9 排孔的位置度极易不合格;旋转头不转、碳刷接触不好及导向器同心度不好等;高压泵正常使用压力为6 MPa 以下,而加工需8 MPa 的高压,这就使高压泵超常运行,再加上设备全天不间断运行,使高压泵的许多部件疲劳运行,其故障必然频繁发生,主要损伤的部件有过滤器、节流垫、节流阀、滚珠、电动机等。另外,由于疲劳运行,工作液里含有电蚀物及部分金属微粒,再加上某些泵的品质问题,使低压泵也常有故障发生,严重影响电火花机床的效率。实践证明,通过下述措施可有效解决故障问题。
(1)重新编制一个新程序,对6~9 排孔单独加工,以保证其空间位置不受机床缺陷的影响。
(2)新旋转头采用陶瓷轴承,防止了锈蚀和电蚀,一般寿命提高3~6 倍。
(3)通向电极的电流直接连接碳刷,减少电流流经的中间环节,降低了故障率,也提高了系统加工的稳定性。
(4)优选高、低压泵,通过多品牌、多型号泵的运转试验,选择寿命长、参数和性能稳定的泵进行加工。
(5)对主要损伤部件增加了库存量,使设备可进行长时间、不停机加工,提高紧迫生产任务的应变能力。
(6)定期对高、低压泵进行检查,如发现异常情况立即更换, 并对更换下来的高压泵进行检查、维护、修理。
(7)对计算机系统软件进行修改和升级,对原时间当量由原来的30 s 改为10 s,有效降低了超差品的概率和机床故障率。
3.成效及结论
激光打孔不论材料的种类和硬度都可进行,故应用范围较广,但因精度较差,重复精度也较低,所以用量、规模都不是很大。但对一些特殊零件,采用激光打孔却取得了很大的效益。涡轮叶片气膜孔的加工采用激光旋切,尽管在孔壁局部范围尚存在重熔层,最大厚度<0.05 mm,个别孔存在微裂纹,但不进入基体。另外,激光打孔对高硬度、非导体材料的微小孔、孔数量很大的零件进行加工也很有优势。电火花打孔最突出的特点是其重熔层厚度仅为激光打孔重熔层厚度的一半, 可控制在0.02 mm以内,能满足所有发动机动、静叶片的冶金质量要求。对于某些位于叶身型面的气膜冷却孔,可使用高速电火花打孔机床, 重熔层厚度一般在0.04 mm以内。
激光打孔工艺不需工作电极,在数控工作台上安装零件不需制作复杂的工装,气膜冷却孔的尺寸可任意调节,最适宜作为新机研制时打孔的工艺方法。电火花打孔成本低,加工质量比激光加工重熔层薄。在加工气膜孔的过程中,将电火花及激光工艺共同融入其中,合理地调整加工工序,会大大地提高零件的加工质量及效率,同时也会降低其加工成本。通过采用电火花加工、激光加工两种工艺方法,对零件工序进行合理调配,并对工艺方法和加工参数进行优化。
随着先进制造技术的发展,新的气膜孔加工工艺不断被开发出来,对带有陶瓷涂层叶片的气膜孔加工,公司内部现正在使用的加工工艺是先加工冷却气膜孔,再涂覆陶瓷,最后用微型钻头在相应的孔位处去除陶瓷涂层,其工序复杂、效率低、质量不易控制。现在使用激光电火花复合加工技术,可在相应的打孔位置上精确地用激光去除陶瓷涂层,再使用高速电火花精确打孔, 缩短了零件的加工周期,确保了加工质量。同时,为公司各类型动、静叶片零件的加工摸索出可行的工艺方案, 此方法也可在其他机种的零件中应用, 拓宽了该方法的用途。因此,激光、电火花复合加工工艺的研发,对航空发动机的制造有着深远意义。
投稿箱:
如果您有机床行业、企业相关新闻稿件发表,或进行资讯合作,欢迎联系本网编辑部, 邮箱:skjcsc@vip.sina.com
如果您有机床行业、企业相关新闻稿件发表,或进行资讯合作,欢迎联系本网编辑部, 邮箱:skjcsc@vip.sina.com