数控机床智能化技术
2018-7-6 来源:-- 作者:--
摘要:本文从传感器出发,将数控机床的智能技术按层次划分为智能传感器、智能功能、智能部件、智能系统等部分,对智能技术进行了总结,指出不足,揭示了发展方向,并对未来进行了展望。
智能机床最早出现在赖特(P·K·Wright)与伯恩(D·A·Bourne)1998年出版的智能制造研究领域的首本专著《智能制造》(Manufacturing Intelligence)中[1]。由于对先进制造业具有重要作用,智能技术引起各个国家的重视。美国推出了智能加工平台计划(SMPI);欧洲实施 “Next Generation Production System”研究;德国推出了“Industry 4.0”计划;中国中长期科技发展对“数字化智能化制造技术”提出了迫切需求,并制定了相应的“十二五”发展规划;在2006年美国芝加哥国际制造技术展览会(IMTS2006)上,日本Mazak公司推出的首次命名为“Intelligent Machine”的智能机床和日本Okuma公司推出的命名为“thinc”的智能数控系统,开启了数控机床智能化时代。
本文从传感器出发,将数控机床的智能技术按层次划分为智能传感器、智能功能、智能部件、智能系统等部分,对智能技术进行了总结,指出不足,揭示了发展方向,并对未来进行了展望。
智能传感器
由机床、刀具、工件组成的数控机床制造系统在加工过程中,随着材料的切除,伴随着多种复杂的物理现象,隐含着丰富的信息[3]。在这种动态、非线性、时变、非确定性环境中,数控机床自身的感知技术是实现智能化的基本条件。
数控机床要实现智能,需要各种传感器收集外部环境和内部状态信息,近似人类五官感知环境变化的功能,如表1所示。对人来讲,眼睛是五官中最重要的感觉器官,能获得90%以上的环境信息,但视觉传感器在数控机床中的应用还比较少。随着自动化和智能化水平的提高,视觉功能在数控机床中将发挥越来越重要的作用。
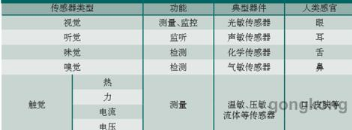
表1 数控机床可用传感器
随着MEMS(微机电系统)技术、嵌入技术、智能材料与结构等技术的发展,传感器趋向小型化。MEMS微传感器、薄膜传感器以及光纤传感器等微型传感器的成熟应用,为传感器嵌入数控机床奠定了基础。
由于制造过程中存在不可预测或不能预料的复杂现象和奇怪问题,以及所监测到的信息存在时效性、精确性、完整性等问题,因此,要求传感器具有分析、推理、学习等智能,这要求传感器要有高性能智能处理器来充当“大脑”。美国高通公司正在研制能够模拟人脑工作的人工智能系统微处理器。将来可通过半导体集成技术,将高性能人工智能系统微处理器与传感器、信号处理电路、I/O接口等集成在同一芯片上,形成大规模集成电路式智能传感器,不但具有检测、识别、记忆、分析等功能,而且具有自学习甚至思维能力[4]。相信随着计算机技术、信号处理技术、MEMS技术、高新材料技术、无线通信技术等不断进步,智能传感器将会在数控机床智能感知方面带来全新变革。
智能功能
数控机床向高速、高效、高精化发展,要求数控机床具有热补偿、振动监测、磨损监测、状态监测与故障诊断等智能功能。融合几个或几种智能传感器,采用人工智能方法,通过识别、分析、判断及推理,实现数控机床的智能功能,为智能部件的实现打下基础。
数控机床的误差包括几何误差、热(变形)误差、力(变形)误差、装配误差等。研究表明,几何误差、热误差占到机床总误差的50%以上,是影响机床加工精度的关键因素,如图1所示[5]。其中,几何误差是制造、装配过程中造成的与机床结构本身有关的误差,随时间变化不大,属于静态误差,误差预测模型相对简单,可以通过系统的补偿功能得到有效控制,而热误差随时间变化很大,属于动态误差,误差预测模型复杂,是国际研究的难点和热点。
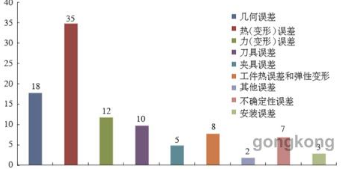
图2 数控机床加工误差来源(百分比)
数控机床在加工过程中的热源包括轴承、滚珠丝杠、电机、齿轮箱、导轨、刀具等。这些部件的升温会引起主轴延伸、坐标变化、刀具伸长等变化,造成机床误差增大。由于温度敏感点多、分布广,温度测试点位置优化设计很重要,主要方法有遗传算法、神经网络、模糊聚类、粗糙集、信息论、灰色系统等[6]。在确定了温度测点的基础上,常用神经网络、遗传算法、模糊逻辑、灰色系统、支持向量机等来进行误差预测与补偿。
在航空航天领域,随着钛合金、镍合金、高强度钢等难加工材料的广泛应用,以及高速切削条件下,切削量的不断增大,刀具、工件间很容易发生振动,严重影响工件的加工精度和表面质量。由于切削力是切削过程的原始特征信号,最能反映加工过程的动态特性,因此可以借助切削力监测与预报进行振动监测。借助测力仪、力传感器、进给电机的电流等,利用粒子群算法、模糊理论、遗传算法、灰色理论等对切削力进行建模和预测[8]。考虑到引起机床振动的原因主要有主轴、丝杠、轴承等部件,也可以采集这些部件的振动、切削力、声发射等信号,利用神经网络、模糊逻辑、支持向量机等智能方法直接进行振动监测。
刀具安装在主轴前端,与加工工件接触,直接切削工件表面,对加工质量的影响是最直接和关键的。刀具磨损、破损等异常现象影响加工精度和工作安全。鉴于直接测量法需要离线检测的缺陷,常采集电流、切削力、振动、功率、温度等一种或多种间接信号,采用RBF神经网络、模糊神经网络、小波神经网络、支持向量机等智能算法对刀具磨损状态进行智能监测。
随着自动化程度的提高,数控机床集成越来越多的功能,复杂程度不断提高。为了高效运行,对数控机床的内部状态进行监测与性能评价、对故障进行预警与诊断十分必要。由于故障模式再现性不强,样本采集困难,因此BP神经网络等要求样本多的智能方法不适合这种场合。状态监测与故障诊断常采用SOM神经网络、模糊逻辑、支持向量机、专家系统和多Agent等智能方法。
研究人员不断探索和研究智能功能的新方法或多种方法的混合,但大部分集中在实验室环境下,缺少实时性高、在线功能强的方法,尚需深入发展简洁、快速、适应性强的智能方法。
智能部件
数控机床机械部分主要包括支撑结构件、主传动件、进给传动件、刀具等部分,涉及到床身、立柱、主轴、刀具、丝杠与导轨以及旋转轴等部件。这些部件可以集成智能传感器的一种或几种智能功能构成数控机床智能部件,如图2所示。
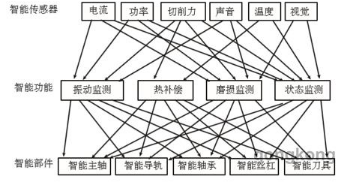
图3 数控机床智能部件
主轴是主传动部件,作为核心部件,直接关系到工件加工精度。由于主轴转速较高,特别是电主轴,发热、磨损、振动对加工质量影响很大,因此,越来越多的智能传感器被集成到主轴中,实现对工作状态的监控、预警以及补偿等功能。日本山崎马扎克研制的“智能主轴”,装有温度、振动、位移及距离等多种传感器,不但具有温度、振动、夹具寿命监控和防护功能,而且能够根据温度、振动状态,智能协调加工参数[13]。瑞士Step-Tec、IBAG等制造的电主轴,装有温度、加速度、轴向位移等多种传感器[14],如图3所示,能够进行热补偿、振动监测等。
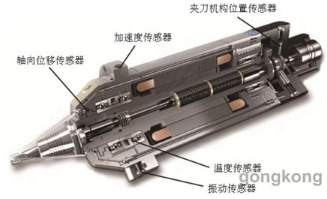
图4 瑞士斯特普电主轴传感器分布
丝杠、导轨是数控机床坐标运动和定位的关键部件,其性能直接影响坐标运动精度和动态特性,对工件加工质量影响很大,因此监测丝杠副、导轨副在加工中的性能变化及寿命预测对数控机床的智能化具有重要作用。通过电机驱动电流信号、功率、切削力、声音等传感器信号,结合进给速度、切削深度、丝杠转速等工艺参数,可对丝杠、导轨的磨损情况进行监控,对剩余寿命进行预测,及时报警,预防重大生产事故。
轴承是数控机床旋转轴的关键部件,起着支撑载荷、减小摩擦系数的作用,其运行状态直接影响机床的运转精度和可靠性。轴承在高转速下摩擦剧烈,发热量大,是最易损坏的部件,因此监测轴承运行状态,可避免因轴承问题而导致设备异常或损坏。瑞典SKF公司生产外挂式智能轴承如图4所示[15],利用应用环境自供电,对转速、温度、速度、振动以及载荷等关键参数进行测量,并利用无线网络发送自身状态信息,实现对轴承状态监测。
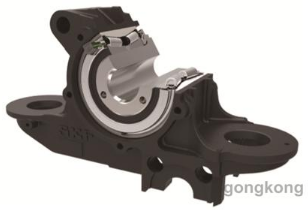
图5 瑞典SKF公司外挂式智能轴承
刀具直接与工件接触,切削工件表面发热量大,容易产生振动,对表面质量的影响很大,因此刀具中融合越来越多的传感器,实现对刀具的磨损监控、振动监测、断裂报警等功能。克里斯托弗、罗伯特等发明的智能刀具夹具如图5所示,集成有力/扭矩、温度、处理器、无线收发器等芯片,能够估计和预测颤动频率、建议稳定的主轴速度、磨损监视以及建议进给速率等[16]。瑞士ACTICUT公司的生产的智能刀具内部由机构、传感器和驱动器构成,用于精密数控车削,可对磨损、速度、温度等进行监控[17]。
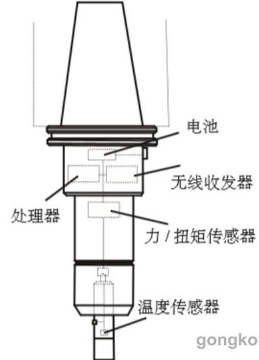
图6 智能刀具夹具
智能系统
数控机床一般由数控系统、驱动系统、辅助系统以及机床本体组成,如图6所示。随着人工智能技术的不断成熟,神经网络、模糊理论以及专家系统等方法逐渐应用到数控系统、驱动系统以及辅助系统中,实现工艺参数优化专家系统、自适应控制、加工过程监控、智能诊断等功能。
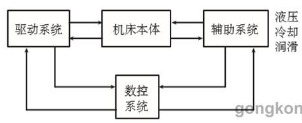
图7 数控机床组成
航空制造领域需要加工的部件含有很多孔、沟、槽、腔等特征,加工工艺复杂,因此在数控机床中嵌入工艺参数优化专家系统成为必然。专家系统利用人工智能技术将某领域内一个或多个专家的知识和经验固化到程序中,模拟人类专家的决策过程,进行推理和判断,以便解决加工中的复杂问题。瑞士米克朗公司汇集了几十年铣削经验的结晶,开发了操作者支持模块OSS(Operator Support System),能够根据加工要求调整相关的工艺参数,优化加工程序,获得更理想的加工结果。
随着数控系统的发展,主流数控系统厂家在产品中嵌入了自适应控制、加工过程监控、智能诊断等实用功能。西门子数控系统具有电机参数自适应运算、自动识别负载、刀具寿命监控、安全集成等功能,与以色列的OMATIVE优铣控制器OMAT-PRO相结合,可对主轴功率进行约束,通过学习和再学习掌握主轴功率的最佳状态,然后在加工过程中,实时监测主轴功率的变化,及时调整进给率[19]。奥地利WFL的Crash Guard防撞卫士系统,利用CNC系统的高速处理能力,实时监控机床的运动,确保机床在手动、自动等各种运动模式下均正常工作,降低运行过程机床突发事故的产生,提高机床工作的安全性和可靠性[3]。GE Fanuc公司的Proficy软件监控和分析机床设备复杂的基本数据,对机床的工作状态、健康状况进行远程诊断。德国ARTIS监控系统是对工作状态进行监控的系统,通过学习,获取监控信号的特征,实现对加工过程中的断刀、刀具磨损、碰撞等异常行为的实时监控。
展望
智能化是数控机床发展的高级阶段,能够实现高度自动化,进一步解放人类的脑力智能。随着技术水平的发展和需求的提高,数控机床出现越来越多智能功能、智能部件以及智能系统。尽管其智能水平还处于发展阶段,但随着人工智能技术、计算机技术、传感器微型化与智能化以及微处理器技术等发展,实现真正意义上的 “自学习、自进化”的具有人类智能水平的数控机床将不再是“梦”。
投稿箱:
如果您有机床行业、企业相关新闻稿件发表,或进行资讯合作,欢迎联系本网编辑部, 邮箱:skjcsc@vip.sina.com
如果您有机床行业、企业相关新闻稿件发表,或进行资讯合作,欢迎联系本网编辑部, 邮箱:skjcsc@vip.sina.com
更多相关信息