一种伺服电机驱动的断路器操动机构
2017-7-31 来源:国网湖北省电力公司电力科学研究院 作者:朱世明 ,陈隽 ,夏天 ,唐诚
摘要:介绍了高压断路器驱动技术与智能化技术的发展现状,提出了一种由伺服电机驱动高压断路器的操动机构型式,其具有传动部件少、结构简单可靠、可以预先设置动触头行程-时间曲线等优点,满足真正意义上的智能化断路器的需求。
关键词:伺服电机;断路器;操动机构
0.引言
高压断路器在电力系统中承担着控制和保护的双重重要任务,而其主要功能体现在动触头的分合闸操作上,分合闸操作又是通过操动机构来实现的。因此,操动机构的工作性能和质量的优劣,对高压断路器的工作性能和可靠性起着重要的作用[1]。目前比较常用的操动机构主要有电磁操动机构、弹簧操动机构[2]、气动操动机构和液压操动机构[3]等。传统高压断路器目前存在着以下几类问题:(1)固有机械特性,在不同的应用场合(如同期合闸、容性负载开断等)和不同应用工况(开断额定短路电流、额定电流和空载操作等)下无法进行运动特性的过程控制,只能以单一的速度特性进行分闸和合闸的操作控制,灵活性差;(2)现场实际应用中,长期静置的高压断路器还存在因机构粘滞、卡涩造成的动作时间分散性大,难以满足运行标准要求的问题,传统操动机构对此类问题缺乏有效的防范措施和补偿手段[4];(3)传统机构运动特性离线调整范围有限,调整过程较为复杂,当面对部分特殊场合时,往往需要更换操动机构才能满足应用需求,造成产品线过长,不利生产和维护;(4)传统机构进行分合闸操作,多次操作过后机构会产生应力松弛[5];(5)此外,从检修安全性考虑,传统操动机构均采用机械储能方式,因机械储能释放异常引起的故障往往存在人身安全风险。为满足生产、维护和应用的需求,有必要积极展开具有在线补偿能力、结构简单、可靠性高、动作冲击小、运行维护安全等特点的新型操动机构研究。
通信技术应用到高压开关设备上,实现设备外围的测量与控制。受操动机构限制,现行高压断路器尚无法对高压断路器的核心控制功能进行智能化;此外,目前智能开关设备中的关键机械状态参量只能在分合闸操作过程中量测,难以满足“状态维护”所需要的预判性要求。为满足坚强智能电网建设要求,有必要积极开展具有柔性控制能力的新型操动机构研究。
国内外对电机驱动断路器已开展了大量研究,20 世纪 40 年代 ABB 就曾经提出应用电机驱动断路器运动的概念,但受电机功率密度、瞬时加速能力和控制技术的限制,这一想法始终难以实行。随着现代稀土永磁电机技术、电力电子技术、电机矢量控制技术和机械设计技术的快速发展,新型伺服电机及其控制系统在转矩输出能力、转子惯量、响应时间和随动能力上越来越接近断路器操动的要求,输出转角、转速和能量的控制性能越来越高,这就为应用于高压断路器的新型电动机操动机构奠定了基础。由于其内在的行程控制能力和反馈能力,基于电机操动机构的新一代智能断路器可以补足智能控制上的短板,实现真正意义上的智能化断路器。
1.目前行业内电机驱动研究进展
电机驱动断路器的原理即将电动机与高压断路器直接连接,从而控制断路器动触头分合闸操作。目前国内尚未生产配有电动机操动机构的高压断路器投入运行 ,但ABB公司已有成套产品(LTB-D 系列 72.5~145 k V 单相操动或者三相机械联动断路器)投放市场。ABB 公司从 2000 年起应用于单相操作和三相操作瓷柱式断路器、罐式断路器、PASS 紧凑型开关设备、GIS 及发电机断路器。截至2005 年,已有 100 多台配电动机操动机构的高压断路器在瑞典、丹麦、意大利、澳大利、新西兰、阿根廷等 17 个国家投入使用(见图 1)。
2007 年,泰国购买了一台 ABB 生产的配电动机操动机构的高压断路器,也是亚洲实际运行的第一台电机驱动高压断路器(见图 2)。国内方面,尽管没有 72.5 k V 及以上电压等级的电机驱动高压断路通过器投运,但各大厂商都积极投入研究。目前,国内已有 40.5 k V 和 126 k V 电压等级的电机驱动断路器样机研制成功 。 其中 ,平高集团研制 的LW0-126 电机驱动断路器分闸速度已达到 5.2 m/s 并顺利通过短路开断型式试验,是国内首个在 126 k V电压等级上通过型式试验的电驱断路器,代表国内在该领域内的领先水平。
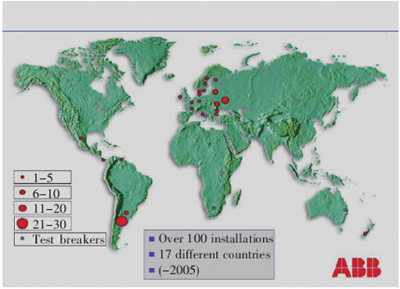
图 1 ABB 电动机操动机构的应用情况
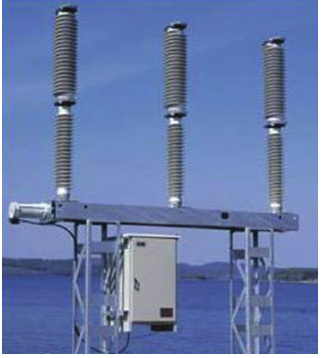
图 2 ABB 配电动机操动机构的高压断路器在泰国的应用
电机驱动断路器虽然目前通过了型式试验,但仍存在一定问题,具体体现在以下几个方面:(1)该断路器伺服系统所用的核心设备分别是欧洲生产的伺服驱动器和永磁同步电机,尚未实现国产化;(2)该伺服系统是风电、光伏专用设备,与断路器驱动应用差异较大,由于不掌握底层核心技术,设备不能从底层进行二次开发,仅从应用层面去适配断路器驱动需求非常困难;(3)该伺服系统价格昂贵,影响电机驱动断路器的推广应用;(4)系统性能还需进一步提高,瞬时转矩输出能力需进一步提升,以实现 126 k V SF6高压断路器分闸操作的灵活控制与系列化应用;(5)该操动机构辅助控制功能和可靠性设计尚不完善,难以适应智能开关设备系统集成要求。
2.伺服电机驱动的断路器操动机构
及其优势由于电机的机械特性具备可控性,因此电机驱动操动机构为不同速度特性的断路器分合闸操作提供了技术条件。电动机直接驱动高压断路器原理图如图 3 所示,系统由交(直)流电源、储能电容器、逆变电路、控制电路、永磁式同步电动机组成。
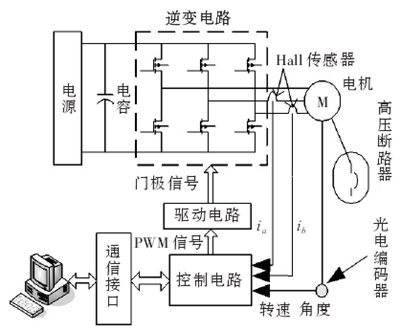
图 3 电动机直接驱动 SF6高压断路器控制原理图
电容器作为电动机操动机构中的储能元件。断路器在进行分合闸操作时,驱动系统需要较大的瞬时电流,这时电动机所需能量将由电容器提供,不会对电源产生大的冲击;当电容器电压下降到某一值时,由交(直)流电源对其进行充电。
逆变电路由智能功率模块(IPM)构成,电动机的电流信号通过霍尔传感器进行测量,反馈给控制电路。电动机的转速和转子位置由安装在转轴上的传感器测出,断路器动触头的行程可由电动机转子位置间接获得。永磁式同步电动机结构简单、体积小、重量轻、损耗小、效率高,和直流电机相比,它没有直流电机的换向器和电刷等缺点。和异步电动机相比,它由于不需要无功励磁电流,因而效率高,功率因数高,力矩惯量比大,定子电流和定子电阻损耗减小,且转子参数可测、控制性能好;但它与异步电机相比,也有成本高、起动困难等缺点。和普通同步电动机相比,它省去了励磁装置,简化了结构,提高了效率。永磁同步电机矢量控制系统能够实现高精度、高动态性能、大范围的调速或定位控制,因此永磁同步电机矢量控制系统可以满足高压断路器的动作控制。驱动器作为电机驱动操动机构的核心部件,由于断路器分合闸操作的特殊工况,要求其驱动单元要有大的输出功率,不同于一般的小功率伺服驱动器。驱动器采用短时工作制,一次开断只需要几十毫秒的时间。驱动器要求短时输出大功率,因此对于控制算法有特殊要求,属于特殊定制型,驱动器控制采用高性能数字信号处理器,功率回路采用PWM 控制的逆变器,控制策略采用矢量控制。交流电机伺服控制器硬件上大体上可以分为控制电路和功率逆变电路两大部分。驱动器整体功能框图如图 4 所示。
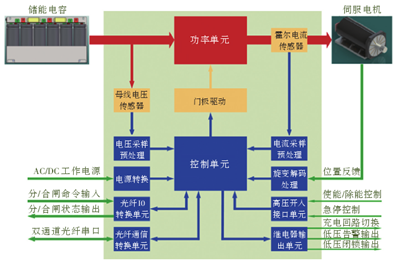
图 4 驱动器整体功能框图
电动机操动机构与传统操动机构相比,具有以下优点:(1)传动部件少,结构简单可靠;(2)可以预先设置理想的动触头行程-时间曲线;(3)动触头的动作特性和断路器的老化、环境温度的变化无关;(4)本身具备状态监测的条件,不需要额外的传感器;(5)对电源要求低,不会引入大的暂态载荷,适用于交流或直流电源。
3.电机驱动的难点
高压断路器的分合闸操作,是在短时内进行一个大操作功释放的过程,实现分、合闸的过程极短,仅为几十毫秒。应用伺服电机驱动断路器分合闸,(1)首先需要电机具备高速下的大功率输出能力和高瞬时转矩输出能力;(2)为使电机出力尽可能的作用于推动断路器负载,电机本身转子惯量应当尽可能小;(3)驱动电机直接连接断路器的转轴,驱动电机处于刚起动即制动的暂态过程,需要电机具有极快的动态响应能力;(4)驱动电机需要实现对动触头运动过程的精确控制,需具备良好的伺服性能;这些要求对电机设计提出了挑战。设计出适合高压断路器驱动应用的具有响应速度快、转动惯量小、动态时间短、瞬时输出力矩大等特点的伺服电机,是电机驱动断路器操动机构的关键点和核心难点。
4.结论
(1)随着电网的快速发展、断路器的装用量越来越大,传统操动机构的断路器在生产、运维、操作和检修环节中存在一些固有的问题,迫切需要一种新型的、具有智能化操动机构型式的高压断路器。
(2)目前国内、外的伺服驱动系统暂不适合断路器的分合闸操作要求。针对高压断路器的驱动需求,研制具有高动态响应能力、高精度控制方法的伺服系统,是实现高压断路器电机驱动智能操动机构的难点和关键。
(3)本文介绍的采用伺服电机驱动断路器的操动机构,可以预先设置理想的动触头行程-时间曲线;满足状态监测要求,不需要配置额外的传感器;对电源要求低,广泛适用于交流或直流电源。对提升一次设备智能化水平、提高断路器的技术经济水平具有重要意义,有实际应用前景。
投稿箱:
如果您有机床行业、企业相关新闻稿件发表,或进行资讯合作,欢迎联系本网编辑部, 邮箱:skjcsc@vip.sina.com
如果您有机床行业、企业相关新闻稿件发表,或进行资讯合作,欢迎联系本网编辑部, 邮箱:skjcsc@vip.sina.com