面向加工中心动态特性的立柱分析及优化设计
2020-3-11 来源: 沈阳理工机械工程 沈阳机床( 集团) 作者:史安娜 刘斯妤 曹富荣 马晓波
摘要: 针对加工中心机床 VMC850B 的立柱进行结构优化设计,提出了一种基于神经网络和遗传算法优化的结构设计方法。基于有限元设计方法,建立立柱的三维模型,并运用 ANSYS 软件对立柱进行静力学分析和模态分析,采用不同的遗传算法优化结果对立柱进行优化设计,对优化结果进行静动态特性分析。结果表明,在保证立柱刚度和稳定性的前提下,优化后立柱的一阶固有频率有不同程度的提高,有效改善了立柱的动态性能,提高了整机的稳定性,为机床的进一步优化提供了有效的理论依据。
关键词: 立柱; 特性分析; 结构优化
0 引言
如今机床动态特性的研究,已将动态特性的优化作为机床设计的主流趋势。立柱是加工中心机床的基础部件之一,它的动态特性将直接影响加工中心机床的加工精度和稳定性。因此有必要对立柱的结构进行优化,以获得更好的动态特性。徐春华等运用有限元法分析机构的动态特性,大大缩短了研究周期。刘成颖等利用拓扑优化获得了立柱的外形,并在此基础上进行了筋板的选型、优化。拓扑优化理论上可以提高结构的性能,但是其结果很难直接应用于工程实际中,使得拓扑优化设计实际应用比较狭窄。郑文标等人以轻量化设计为目标,在保证立柱刚度的情况下对立柱进行拓扑优化设计。
以上的研究人员均对立柱的结构优化设计提供了良好的参考,但以上的研究均对立柱进行单目标的优化,立柱的综合性能的优化,还值得研究。本文以加工中心机床的立柱为研究目标,利用有限元法对立柱进行静动态分析,针对立柱的静动态特性,以轻量化为目标,进行灵敏度分析和遗传算法寻优,对立柱进行多目标优化。分析结果表明,优化后的部件提高了立柱的一阶固有频率并减轻了质量,有效改善了机床的动态特性。
1 、模型建立
1. 1 有限元模型的建立
本文研究的 VMC850B 加工中心立柱模型,如图 1所示。根据图纸 1: 1 绘制出立柱的三维模型,并设置材料属性,该滑座材料选用 HT200,杨氏模量为1.45 ×1011Pa,泊松比为 0. 27,材料密度为 7. 3 × 1013kg / m3,由于立柱有许多细微的结构,不利于网格的划分,因此对局部特征如倒角、小螺纹孔等细节进行简化,后经 step 格式导入到 ANSYS 中。

图 1 有限元模型的建立
1. 2 划分网格
网格精度影响有限元计算的精度,网格划分的过多,计算速度就变慢,结构力学仿真要求更高效率的网格划分,因此应该在保证计算精度的情况下,减少划分网格的数量。使用高度自动化的网格划分工具 Me-chanical 对立柱进行网格划分,采用 Automatic 自动网格划分,保证有限元模型的计算精度。
1. 3 边界条件的设定
立柱底部通过四个螺栓和床身连接,立柱的质量为1240kg,通过四个 M30 螺栓与床身相连,拧紧力矩为2000N·m,根据公式( 1) 可得轴向预紧力,Q = 34188N。

d —螺栓的公称直径; K —拧紧力矩系数取 0. 3。由于螺栓结合面承受立柱的重力和螺栓预紧力的作用,因此由式( 2) 可得单个螺栓结合面的压力。

G—立柱的重力; n—螺栓个数最终求得 P = 213. 22MPa,施加在立柱的螺栓上,达到准确模拟边界条件的目的,进行静动态分析。
2 、滑座静态特性分析
2. 1 静力分析基础
立柱的静态特性分析是分析立柱在受自身重力时产生的响应,例如应力、应变、位移等。静态特性分析可以确定立柱的静刚度,保证机床的整机结构和加工精度不受影响。根据经典力学理论,立柱的动力学方程是:

式中,[M]是质量矩阵,[C]是阻尼矩阵,[K]是刚度矩阵,{ x} 是位移矢量,在分析中{ F( t) } 是在不考虑质量、阻尼等惯性载荷的情况下的静态载荷,与时间 t 相关的量将被忽略,于是式( 1) 变为:

2. 2 ANSYS 静力分析
在 ANSYS 中,静力分析是研究立柱在定载荷作用下的响应,如等效应力、等效应变等。由于主轴箱的质量约为 50kg,所以给立柱的 Z 方向施加 500N 的均布面力,在立柱和主轴箱接触面的 X 向、Y 向、Z 向的三个面上,分别施加 90N、140N、280N 的均布面力,再将 4个螺栓的预紧力、立柱自身的重力加载到螺栓孔上,模拟仿真实际工况状态下立柱受到的力,得到立柱的应力和位移云图,如图 2 所示。

图 2 位移、应力云图
经过应力云图分析可以得知,立柱的最大应力出现在立柱的上端位置,最大应力为 1.568MPa,远远小于立柱材料本身的屈服极限应力,因此我们可以通过多目标优化的方法进行立柱的优化设计。在立柱的位移云图得知,最大位移出现在立柱前端与主轴箱相连接的部位,立柱的最大位移量为0.007842mm,原因是由于刀具的切削力通过主轴箱传到了立柱上,因此为了提高立柱的刚度,并且实现减重的目的,立柱结构还需优化。
3 、模态分析
立柱的固有频率是机床动态特性的主要参数,提高立柱的固有频率,可以提高立柱的动刚度,从而提高机床整机的抗振性和稳定性。模态分析是研究结构动力特征的主要方法。模态主振型描述了部件在不同频率下的变形大小和方向。使用 Ansys Workbench 计算立柱前 6 阶模态和主振型,由于篇幅限制,只列举前三阶振型图,如图3 ~ 图 5 所示,固有频率和主振型的分析见表 1 所示。
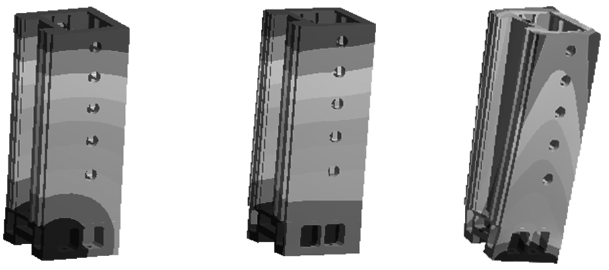
表 1 立柱前三阶固有频率和主振型
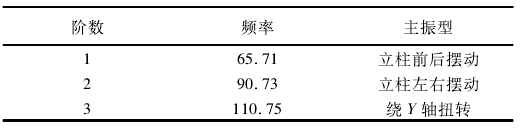
根据模态分析的固有频率和主振型等参数,可知立柱一阶固有频率较低,可能发生共振,影响加工中心的整体精度。因此说明立柱的整体结构比较薄弱,可通过 MATLAB 遗传算法优化立柱参数,提高立柱的一阶固有频率。
4 、立柱优化方案及其验证
4. 1 立柱灵敏度分析
由于该立式加工中心的立柱中有多个尺寸参数,为了减少计算量,需要在分析立柱的模型后,选取表 2 中的尺寸进行分析,选择灵敏度较大的设计变量作为优化对象。灵敏度分析是尺寸优化的前提,利用灵敏度分析得出影响较大的参数,通过回归分析拟合出响应曲面。零刻度线以上的部分表示结构性能随着设计尺寸正变化, 零刻度线下的与其相反,图 6、图 7 是灵敏度分析图。
表 2 设计变量的优化范围
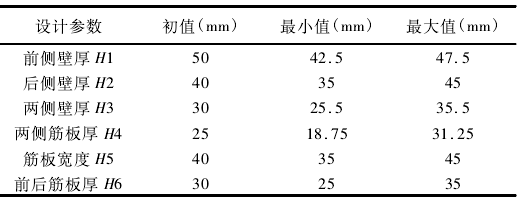
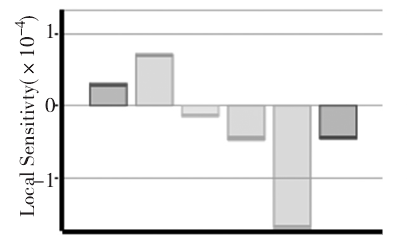
图 6 设计参数对一阶固有频率的灵敏度
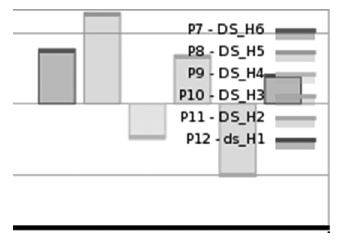
图 7 设计参数对立柱质量的灵敏度
在图 6、图 7 中可以发现,影响立柱质量和一阶固有频率的主要尺寸是后侧壁厚 H2、两侧筋板厚 H4 和筋板宽度 H5,因此选这三个尺寸对立柱进行最终的多目标优化。
4. 2 BP 神经网络模型
BP 神经网络可通过样本数据,便可实现对参数空间的非线性化映射。由于 BP 网络进行结构设计的速度比有限元分析快几个数量级,因此进行结构优化时采用 BP 神经网络优化。而遗传算法( GA) 是通过模仿自然界生物进化机制发展起来的一种优化方,需要进行大量的计算量,因此应用在结构优化的方面上比较少。对于该立柱我们可将两种方法相结合,进行结构优化,即 BP-GA 法。BP-GA 优化的主要思想是,先利用 BP 神经网络,对结构影响较大的参数与一阶固有频率、立柱质量建立关系,再进行遗传算法优化。为了减少神经网络的误差,在尺寸参数样本较少的情况下,形成样本点可采用均匀设计法,如表 3 所示。
表 3 BP 算法的训练与测试数据
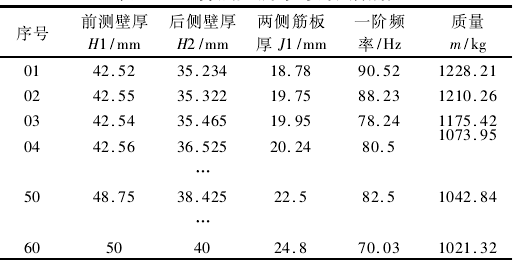
将表 3 中的数据导入到 MATLAB 中进行神经网络建模,为了保证得到合适的模型,使用测试数据对模型进行测试,根据测试结果得知模型的误差在 5% 之内,可以进行遗传算法分析。
4. 3 遗传算法 GA 工具箱优化
对于该立柱可以选择一阶固有频率最大并且质量最小为目标进行多目标优化,多目标优化的问题可描述为:


式中,fi( x) 为目标函数; x 为自变量; ub,lb为自变量的最大值、最小值。该立柱只对三个设计变量进行了最大值、最小值约束,取值范围与灵敏度分析时相同。通过 BP 神经网络模型建立优化的目标方程,利用 MATLAB 的 GA 工具箱进行优化求解,求得最终的优化方案,并将其优化结果应用到 ANSYS WORKBENCH 中分析结果,如表 4 所示。
表 4 立柱优化前后性能的对比
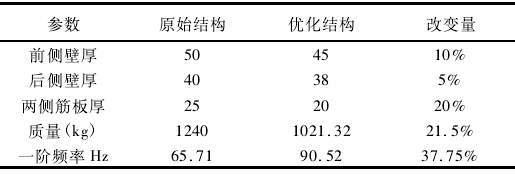
将原始结构与优化结构进行对比后可知,一阶固有频率提高了 37. 75% ,质量减轻了 218. 68kg,并且立柱符合轻量化、高精度的要求,说明该立柱优化方案合理,优化结果有效。
5、 结论
应用三维建模软件 UG 对立柱进行参数化建模,并导入到 ANSYS WORKBENCH 中进行有限元分析,并将立柱的螺栓预紧力计入到边界条件中。经过灵敏度分析后,得到对立柱一阶固有频率、立柱总质量影响较大的参数。并以此参数为基础,基于神经网络算法采用均匀设计法对样本点进行选择,再进行遗传算法的优化。在保证立柱总体性能的基础上,得到立柱的新模型,实现了立柱结构的优化,为机床部件优化提供了参考。
投稿箱:
如果您有机床行业、企业相关新闻稿件发表,或进行资讯合作,欢迎联系本网编辑部, 邮箱:skjcsc@vip.sina.com
如果您有机床行业、企业相关新闻稿件发表,或进行资讯合作,欢迎联系本网编辑部, 邮箱:skjcsc@vip.sina.com
更多相关信息