基于稳定域叶瓣图的加工中心铣削参数优化
2020-2-7 来源: 大连职业技术学院 作者:孟祥忠
摘要: 以某柴油发动机缸体生产线的精基准定位面加工工序为研究对象,针对加工过程中存在的表面振痕明显、精度不足的问题,提出一种基于稳定域叶瓣图的加工中心铣削参数优化方法。分别进行了模态锤击实验和铣削力仿真实验,以获取加工中心的特征参数和铣削力系数,进而构建铣削稳定性叶瓣图,并实验验证了叶瓣图的准确性。在此基础上,以“金属去除效率”为评价指标,优化选取了加工中心铣削参数。该方法有助于提高加工系统的稳定性、加工质量和加工效率。
关键词: 模态实验; 铣削力仿真; 稳定域叶瓣图; 铣削参数
0 引言
发动机缸体面的铣削加工属于平面加工,对加工表面的精度要求比较严格,尤其是对于与缸盖接触的加工面 。铣削过程中过大的振动不仅会影响加工表面精度和产品质量,还会导致系统稳定性和可靠性的降低,甚至带来安全事故,故铣削过程中的颤振是必须要避免的。对于已经投产的发动机缸体生产线,加工工序已被确定,且专用夹具和专用刀具无法更改,则通过合理的选择铣削参数以减小颤振的发生,是比较直接和简便的解决方案,而加工过程中切削颤振稳定域的分析则为铣削参数的优化选取提供了参考和依据。
Altintas 等首先提出了零阶解析法( ZOA,zero-order analytical) ,建立了基于切削厚度再生效应的动态铣削力模型,为选择稳定切削状态的切削参数提供了理论依据。Altintas 等在此基础上继续完善了线性再生型颤振理论方法。Liu 等基于 ZOA 方法获得了车削、铣削加工过程中平头刀、球头刀等的稳定域叶瓣图,并分析讨论了切削参数和模态参数对叶瓣图的影响程度。而加工中心主轴-刀具系统特征参数( 固有频率、阻尼比、刚度) 的识别及铣削力系数的获取是构建基于 ZOA 方法的颤振稳定域叶瓣图的关键问题。
为解决某柴油发动机缸体生产线的精基准定位面加工过程中存在的表面振痕明显、精度不足的问题,本文提出一种基于稳定域叶瓣图的加工中心铣削参数优化方法。为构建准确的铣削稳定性叶瓣图,分别进行了主轴-刀具系统的模态实验和铣削力仿真实验,并以“金属去除效率”为评价指标,优化选取了加工中心铣削参数。该方法有助于提高加工系统的稳定性、加工质量和加工效率。
1、 加工中心特征参数识别
针对加工中心的刀具-主轴系统的复杂性,基于仿真实验很难获得其准确的模态参数,这里通过模态锤击实验方法实现。对安装于加工中心主轴上的刀具锤击起振,以获取其频率响应数据,然后基于 PolyLSCF频响曲线处理算法识别出系统的固有频率、刚度和阻尼比,最终获得刀具系统模态参数。实验对象为缸体生产线上的精基准加工工序,加工中心及其主轴的整体外形如图 1 所示,实验用刀具为镶片铣刀,刀齿数3,刀片材质为金属陶瓷。
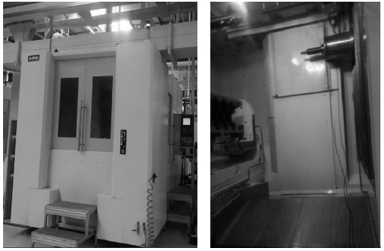
图 1 加工中心及其主轴外观
实验所用设备: NI-9234 数据采集仪、PC 计算机、DASP 模态测试软件、PCB 力锤及加速度传感器,基于前期的研究基础,平台搭建方案如图 2 所示[6]。图 3a所示为搭建的数据采集分析系统,图 3b 所示为力锤敲击和传感器的布置位置,主轴轴向( Z 向) 刚度相对于X、Y 方向的振动影响可以忽略不计[7],因此分别放置传感器于 X、Y 方向刀尖处。进行多组次采集测试实验,将测试所得的频响函数曲线分 X、Y 方向进行平均拟合计算,结果如图 4 所示。
利用东方所 DASP 模态分析软件,基于 PolyLSCF频响曲线处理算法,对频响函数数据进行分析处理,最终获得刀具系统 X、Y 向的模态参数,如表 1 所示。
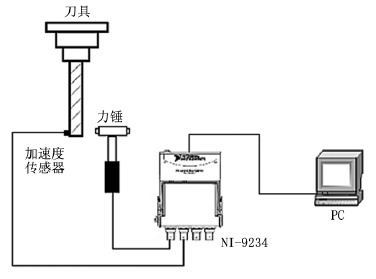
图 2 模态实验的测试装置示意图
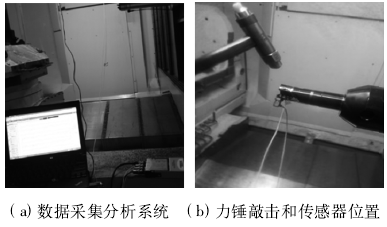
图 3 模态实验平台
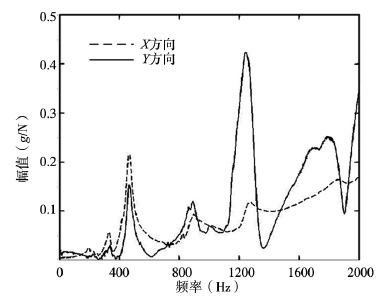
图 4 刀具频响函数曲线
表 1 刀具系统模态参数
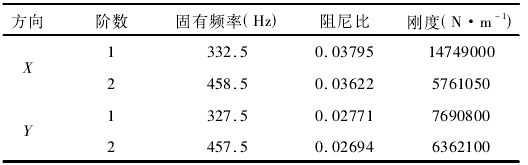
2 、铣削力系数的获取
2. 1 铣削力系数辨识理论
上文已知,主轴轴向( Z 向) 刚度相对于 X、Y 方向的振动影响可以忽略不计,因此,本文铣削实验对象可简化为二维铣削力模型,即正交切削模型。该模型将动态变化的切削力分解为两个垂直正交方向上的切向力和径向力,且两个力之间具有线性关系,每个方向
的铣削力对应一个铣削力系数,其基本公式为:
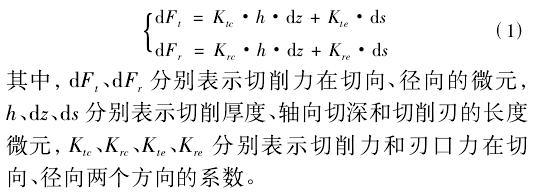
将公式( 1) 进行坐标变换和积分运算,得出每齿周期平均铣削力:
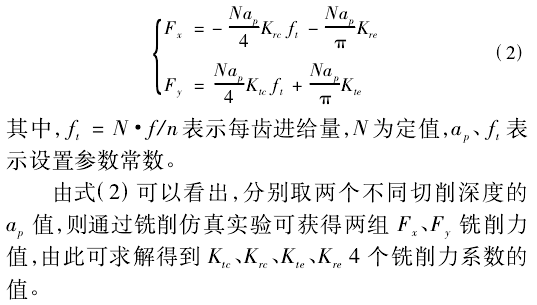
2. 2 铣削力仿真及铣削力系数求解
为求解铣削力系数,首先进行基于 DEFORM 有限元分析软件的铣削力仿真实验,以获得不同切削深度ap下的 Fx、Fy铣削力值。所用刀片材料为金属陶瓷,工件材料为 HT250,材料性能参数如表 2 所示。
表 2 刀具与工件热-力学参数
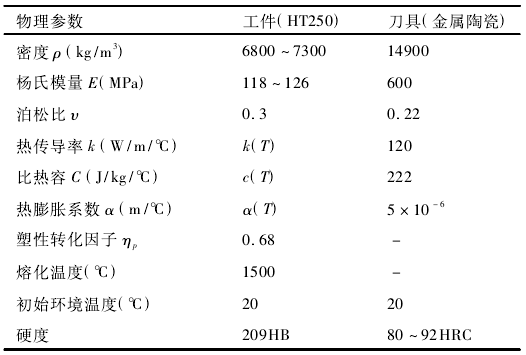
在 DEFORM-3D 软件中设置实验切削参数,进行铣削模拟,仿真得到的铣削力曲线如图 5 所示。将所获得的仿真信号曲线小波分解重构去噪后,求取其有效值,计算出的铣削系数如表 3 所示。
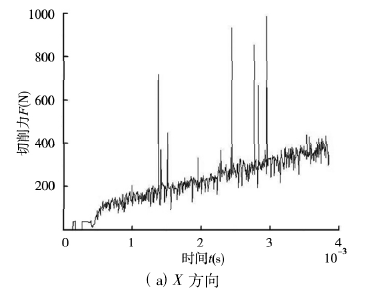
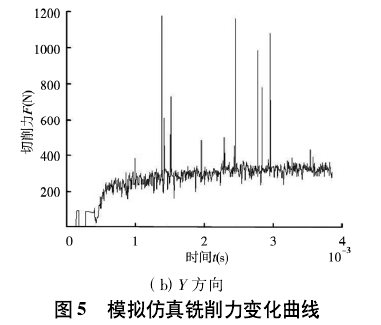
图 5 模拟仿真铣削力变化曲线
表 3 铣削系数

3 、铣削稳定性叶瓣图的构建
铣削稳定性叶瓣图表示了轴向临界切深相对于主轴转速的二维关系[,可直观看出铣削稳定性的切削极限,相关表达式为:
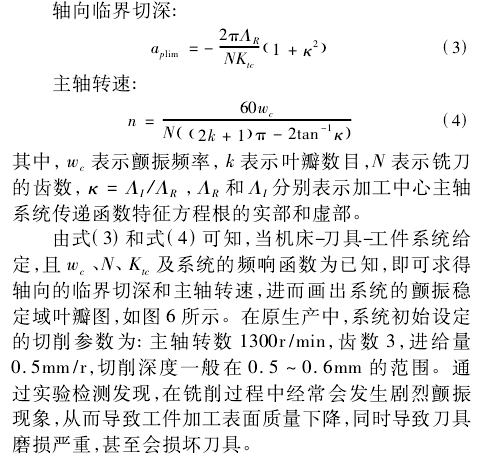
针对上述存在的问题,由叶瓣图可直观看出,在切削用量给定的前提下,主轴转速选择在 800r /min ~1100r /min 的范围可避开颤振区域,且在该范围内切深的选择也更加广泛,这对实际加工过程中切削参数的选择具有现实的指导意义。
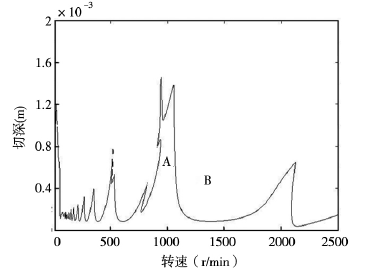
图 6 HT250 铣削稳定性叶瓣图
4 、实验验证及铣削参数优化
4. 1 实验验证
加工中心铣削参数的优化建立在叶瓣图构建的准确性上,为此,需要进行实际切削实验验证,验证选取点的位置如图 6 所示,参数如表 4 所示,同时采用观测器实时监测切削过程是否发生颤振。
表 4 验证实验切削参数
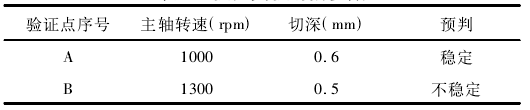
首先,从叶瓣图中可看出,A 点在理论上应处于稳定切削区域内。对实验采集到的信号做 FFT 变换,通过频谱可获取各频率在振动中的幅值大小,由切削参数可知,对应的转频为50Hz,同时频域中会出现50 /3Hz的倍频。验证点 A 的加速度振动频域信号如图 7 所示,可以看出,最大幅值出现在频率为 300Hz处,且该频率为转频的倍频。转频的倍频所对应的幅值较大说明了加工中心处于正常的切削状态,该过程未发生颤振现象。
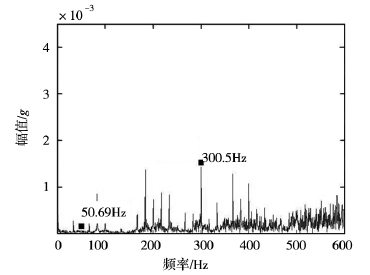
图 7 A 点加速度振动的频域信号
由叶瓣图可初步看出,B 点从理论上应处于切削颤振域。在该点的切削参数下,对应的转频为 65Hz,同时频域中会出现 65 /3Hz 的倍频。验证点 B 的加速度振动频域信号如图 8 所示,相较于 A 点,其振动幅值明显较大,且最大幅值出现在频率为 496. 1Hz 处,可以看出,该频率并不是转频的倍频,它处于加工中心主轴2 阶固有颤振频率附近。除此之外,铣削参数选择的不合理,也同时致使加工中心的不对中等原因引起的振动更加明显。通过分析可知,基于 B 点切削参数进行的铣削加工,会导致加工过程中颤振问题的发生,从而验证了叶瓣图构建的准确性。
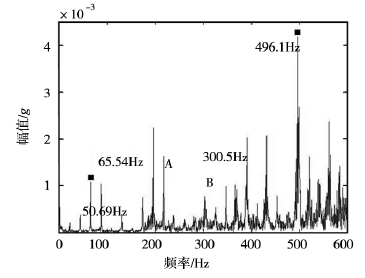
图 8 B 点加速度振动的频域信号
4. 2 铣削参数优化
前文已经验证了叶瓣图的正确性,并基于叶瓣图可直观看出稳定切削和颤振区域的界限,为寻求实际加工过程中的最佳切削性能,在此基础上进行加工中心的铣削参数优化。为描述最佳铣削参数的选取,这里采用金属去除效率的概念,其表达式如下:
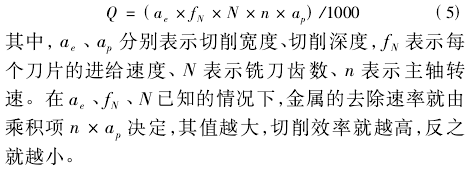
以 Q 值为评价指标,叶瓣图曲线上部分是颤振切削区域,下部分是稳定切削区域,1000rpm、2000rpm 附近有较大的选择范围,2000rpm 虽然转速高,但是可供选择的切深范围 ap太窄,Q 值较小,而在 1000rpm 附近切深选择范围宽,最大允许切削深度达到 1. 4mm。因此,建议以 1000rpm 转速为中心,选取合适的切削深度。
5 、结论
( 1) 基于刀具的模态锤击实验及铣削力系数辨识方法,构建了加工中心铣削稳定性叶瓣图,并选取不同的验证点,进行实际的切削实验,验证了叶瓣图的正确性,该叶瓣图为铣削参数的选择提供了有益参考,有助于提高加工效率,增加系统的稳定性。
( 2) 以“金属去除效率”为评价指标,基于叶瓣图进行 了 加 工 中 心 铣 削 参 数 的 优 化,最 终 建 议 以1000rpm 转速为中心,选取合适的切削深度。
( 3) 在制定加工工艺参数时,应综合考虑切削深度、切削速度等因素,在稳定切削区域内选择最优的参数搭配,这既能保证加工系统的稳定性,又能提高加工质量和加工效率。
投稿箱:
如果您有机床行业、企业相关新闻稿件发表,或进行资讯合作,欢迎联系本网编辑部, 邮箱:skjcsc@vip.sina.com
如果您有机床行业、企业相关新闻稿件发表,或进行资讯合作,欢迎联系本网编辑部, 邮箱:skjcsc@vip.sina.com
更多相关信息