齿轮加工数控系统监控技术的研究
2019-2-13 来源: 河南工学院机械工程系 作者:刁修慧,陈韵
摘要: 在齿轮加工的过程中,为了便于操作者实时了解机床运行状况,对齿轮加工的监控系统进行了研究。分析齿轮加工数控系统监控模块的总体框架,将监控系统划分为以下 3 个模块: 在齿轮加工图形监控模块中,从轨迹仿真和跟随误差监控方面进行分析和实现; 在报警信息监控模块中,对报警信息监控设计、实现和自诊断进行分析和实现; 在机床状态监控模块中,详细分析了其实现流程。
关键词: 齿轮加工; 数控系统; 监控技术
齿轮是机械领域常用的重要传动零件,在工业领域起着至关重要的作用。在齿轮加工的过程中,为了便于操作者实时了解机床运行信息和正确使用机床,进而加工出满足使用要求的齿轮,文中对齿轮加工的监控系统进行了研究。在此研究中,将齿轮数控加工监控系统分为加工图形监控模块、报警信息监控模块和机床状态监控模块。
1 、齿轮加工数控监控系统的总体设计
机床状态的监控是通过检测、测量和监视以及系统历史信息,对机床的运行状态进行测评,进而判断它是否正常运行,若有异常,监控系统做警报处理,另外,测评数据也可作为故障分析诊断的部分依据。为了对机床工作状态中的数据进行采集,这里采用了不同形式和不同精度的传感器,来测量加工中的相关数据,并对这些数据进行处理,然后传至数控系统。此监控系统是基于 ARM、DSP 和 FPGA 实现的,如图1 所示。
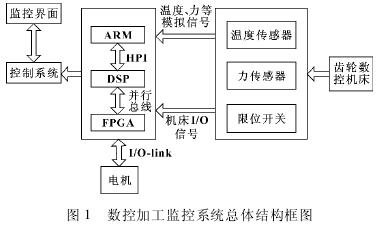
DSP 负责实时监控任务,ARM 负责管理和显示,FPGA 负责对机床 I/O 信息进行采集。在此系统中,FPGA 采集开关量信号,并将其传至 DSP 进行处理,然后将信息发给 ARM 显示。而温度和压力等模拟信号则由 ARM 从传感器缓存中直接读取,并在ARM 中计算,判断它们是否超出标准范围,若超出标准范围,就要通知 DSP 完成报警动作并显示,若未超出,则在 ARM
上显示其正常状态。
2 、齿轮加工图形监控模块
为了便于实时观察刀具的运动轨迹,设计了加工图形仿真这一模块,可以直观方便地观察刀具是否有少切、过切或者撞刀现象。在开发图形界面时,选用Open GL 图形开发工具,它功能强大且调用方便,和C 语言密切关联,具有很好的移植性和图形渲染力。
另外,此系统是嵌入式系统,因此选择了 Open GL ES来开发。为了能够顺利使用 Open GL ES
进行图形开发,需要对一系列库文件进行正确的路径设置和配置工作,还需要在 VS2005 的编译环境中进行一系列设置。完成上述设置便可以 进入 程 序 开 发,首 先 对Open GL ES 进行初始化操作。
2. 1 轨迹仿真设计
加工轨迹仿真是指在坐标系中绘制出刀具的运行轨迹。此系统采用机床坐标来绘制刀具轨迹,当机床空运行时,采用程序坐标值来绘制。
2. 1. 1 建立坐标系
若将 DSP 中的程序坐标和机床坐标数据直接用于加工图形的绘制,则会出现坐标值过大,超出屏幕范围。因此,可考虑将程序坐标和机床坐标数值映射为纹理坐标,也就是说,要建立坐标系。文中以数控插齿为例。如图 2 所示,把工作台的中心设置成图形坐标系的原点,根据屏幕上图形显示范围来恰当确定机床零点位置,并计算其纹理坐标值。
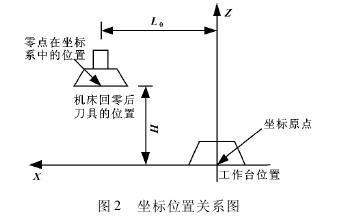
计算方法如下: 首先开启机床并回零,测量工作台中心和零点的距离,利用线性插值法把刀具的轨迹坐标值转换成纹理坐标值,如公式 ( 1) 所示:

式中: XM是纹理坐标值; XW是机床零点位置对应的纹理坐标值; X 是刀具轨迹坐标值; L0是工作台中心和机床零点的距离。
2. 1. 2 加工轨迹监控仿真
为了保证能够实时地读取机床坐标和程序坐标数据,要设置一个定时器,将机床坐标或程序坐标值赋给坐标显示控件的变量,并把相应代码放在定时器的函数中,这样在执行程序的过程中,会不断刷新图形界面的绝对坐标和相对坐标,在预定窗口上绘制出加工轨迹图。
2. 2 跟随误差监测实现
由于数控加工精度要求较高,因此,操作者需要实时了解加工误差的变化情况,并以此来适当调整控制参数以达到减小加工误差的目的。
在此系统中,建立了示波器模型来显示每个轴的随机误差,然后每隔0. 01 s 从 DSP 中读取其误差值,并将其转化为纹理坐标值,并设置一个数组用以存储一个周期的误差值;在下一个周期,将其赋给上一周期,不断循环。用户可以通过操作面板来调取并显示轴的跟随误差曲线,以判断误差情况。
3 、报警信息监控模块
3. 1 报警信息监控设计
在加工过程中,通常需要对机床进行监控,当出现异常情况时发出警报声音和屏幕显示。同时,为了对报警信息进行诊断,还需将报警信息存储下来。在此监控系统中,主要对机床、PLC 和预处理指令 3 个方面进行监控和报警分析,具体内容如图 3 所示。
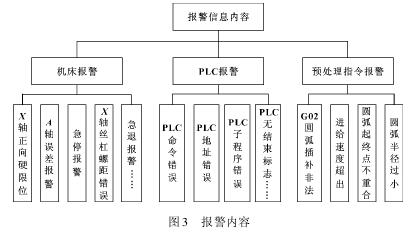
3. 2 报警信息监控实现
3. 2. 1 底层
首先,如图 3 所示,将报警内容分为三大类; 然后,为了标志特定的报警内容需要在 DSP 中分配固定地址,地址中的每一位分别标志一个报警内容,当出现报警后,对应位置为 1,另外,需用一变量来保存当前报警号,并将此变量存储在 DSP 特定的地址中。
液压是否正常和扫描电机是否过载等非紧急报警代码,在背景程序中进行编写; 而扫描急停、急退和限位报警灯紧急报警代码,在插补程序中进行编写,还要上传紧急报警号。除此之外,若是急停报警,则需将所有伺服关闭; 若是限位报警,则对应轴的伺服需要关闭,防止意外的发生。
3. 2. 2 上层
为了实时读取 DSP 中的报警号,可在主界面的源文件中设置一个定时器。若出现报警号,主界面的特定位置会显示并报警。但是,当界面上有报警时,屏幕上显示报警号,若是用户想查看详细的报警内容、时间等更多信息,需将界面切换到信息界面来。
3. 3 自诊断
在此设计中,采用故障树分析法对报警信息进行诊断。其过程 ( 见图 4) 是: 将出现的报警信息作为顶事件,即分析目标; 然后,逐层分析、查找其中间事件和间接事件,即直接原因和间接原因; 最后,用恰当的逻辑连接词将顶事件、中间事件和间接事件联系起来,进而构成故障树。
当出现报警信息时,用户将界面切换到 “信息”界面,点击 “当前报警”会显示出机床所有故障信息,而且以 TXT 文件格式存储详细的报警信息,比如报警号、原因、内容、时间等。

4 、机床状态监控模块
在此设计中,底层控制程序负责响应机场操作面板,上层负责显示。具体实现流程如图 5 所示。
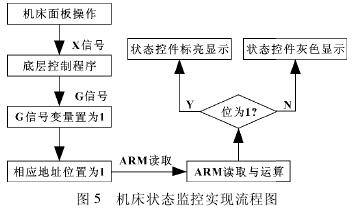
当按下机床面板上的相应键时,向控制系统发送X 信号,底层控制程序将接收到的 X 信号变为
G 信号,然后将相应的变量设置为 1。并在固定地址中相应位设置为 1,表示状态有效,然后由
ARM 读取此变量并对其进行运算分析,根据分析情况确定显示控件是否标亮,标亮表示状态有效。
5 、结论
首先分析了齿轮加工数控系统监控模块的总体框架,接下来对系统进行了模块划分、研究和实现
。在齿轮加工图形监控模块中,从轨迹仿真和跟随误差监控方面进行研究和实现; 在报警信息监控模块中,对报警信息监控设计、实现和自诊断进行了研究和实现; 在机床状态 监控模 块中,详 细 分 析 了 其 实 现流程。
投稿箱:
如果您有机床行业、企业相关新闻稿件发表,或进行资讯合作,欢迎联系本网编辑部, 邮箱:skjcsc@vip.sina.com
如果您有机床行业、企业相关新闻稿件发表,或进行资讯合作,欢迎联系本网编辑部, 邮箱:skjcsc@vip.sina.com