数控机床切削性能测试和评价体系
2013-12-15 来源:数控机床市场网 作者:马晓波 孙名佳 仇健
摘 要:详细说明了进行数控机床切削性能测试和评价的意义,以及测试评价体系的研究内容和流程。依据数控机床切削负荷能力、工作精度、切削状态和加工表面质量等指标对数控机床进行切削性能考核,得出机床的加工适用范围、工作精度等级以及加工表现。有助于为机床制造商了解和掌握机床的真实应用性能,进行面向用户需求的数控机床开发和进一步对机床产品进行试制和优化;同时有利于为机床用户进行机床的采购和验收, 找出机床工作精度问题并进行定期精度检查,寻找机床最佳精度范围,减少机床应用中问题的判断和维修时间。
关键词:切削性能;性能测试;机床评价;负荷试验;切削精度
数控机床的水平、品种和生产能力直接反映了国家的技术、经济综合国力。数控机床作为国防军工的战略装备,是各种武器装备最重要的制造手段,是国防军工装备现代化的重要保证。数控机床的综合性能水平,决定了国家工业制造水平。为了满足典型行业用户对数控机床的应用,机床制造商除了提供功能完备、易用和易于维护的机床产品外,还应根据用户零件的加工工艺特点,重点在机床的几何精度、加工精度、加工效率、设备利用率等性能指标上满足用户对零件加工的要求。
1 、切削性能测试和评价意义
数控机床的实际应用性能,主要表现为:静态特性、动态特性、运动特性、热特性、可靠性、切削加工的加工效率、精度和应用水平等,对其进行测试和评价,可在机床的运动学和动力学等方面,对机床的运动和动力学性能进行深入了解,并可进一步有针对性地提出改进意见,优化机床性能。
了解和掌握数控机床的应用性能可通过性能测试和切削加工两种方式。性能测试可以获得机床全面的几何精度、运动精度、热力学性能、动态性能、承载和变形、以及机床可靠性情况。而切削加工可以综合获得机床的工作精度、负荷能力、加工质量和包含几何精度、运动精度、热力学性能、动态性能、承载和变形等性能的综合表现。
在进行数控机床性能测试时,由于试验测试是通过应用先进的测试仪器进行数据的采集和处理,与用户处使用机床的真实环境存在区别,测试过程中一般没有载荷,并且不存在刀具与工具之间的相互作用,切屑和切削过程中的各种状态量无法体现,导致仪器测试得到的数据与真实切削存在差异。另外,数控机床的性能测试需要大量专业仪器,多数制造商和用户不具备完善的测试条件。因此,最直接和最真实的检测评价方法是通过切削加工和零件的检测来实现。
对于机床用户来说,开展数控机床的切削性能测试和评价研究,可以:
有利于进行机床的采购和验收
找出机床工作精度问题或在使用中进行定期精度检查
寻找机床最佳精度范围,以便获得良好加工品质
减少机床应用中问题的判断和维修时间
核心是帮助用户进行机床选型和应用
对于机床生产厂商来说,开展数控机床的切削性能测试和评价研究,可以:
了解和掌握机床的真实应用性能
进行面向用户需求的数控机床开发
有利于机床新样机试制和优化
获得更高的加工精度、更大的加工效率
核心是提供给用户更优质的机床产品
2 、评价体系研究内容和流程
依据数控机床切削性能的测试和评价两个主要阶段,对数控机床切削性能测试流程划分如图1所示。首先,需要确定评价的对象和体系适用范围,一般可依据测试目的分为新型数控机床样机的检测评价、新出厂样机的例行检验、以及用户处长期使用的数控机床的定期检验。随后需要进行具体的测试和评价,主要针对数控机床的工作精度、承载能力、切削加工表现等几个方面开展测试和评价研究。并依据具体的测试方法和测试流程进行测试,与单纯的切削加工不同,进行数控机床切削性能测试除了需要进行必要的机床、试料、刀具、夹具等工艺系统准备,还需要对测试仪器进行调试安装,此外,对切削试验的方案、方法和参数进行规范化执行。试验中,需要记录必要的数据,并进行数据结果的统计和分析。最后依据有关国际国内标准和企业内部规范,确定设计目标和评价标准,并将试验获得的数据指标与评价标准比较,综合进行机床真实切削性能的评价,给出机床适用的范围。
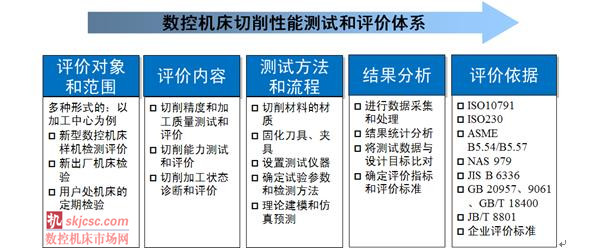
图1. 数控机床切削性能测试和评价体系流程
现行数控机床切削性能测试和评价方法包括:空运转实验、切削负荷试验、国标件或NAS件的切削和检测等。这样的现状存在的问题和弊端主要有:
只关注工作精度和切削负荷,这样的测试和评价并不全面。
负荷试验对机床有一定破坏作用,容易在机床未磨合应用前造成早期破坏,从而影响后期的实际应用。
根据这样的现状,沈阳机床高档数控机床国家重点实验室通过大量的机床样机定型检验和机床产品出厂检验,提出数控机床切削性能测试和评价的内容除上述负荷试验和精度试验检测外,还应该包括,如图2:
多种单一精度的检测评价;
切削能力评估;
切削状态评价;
加工质量评价等内容。
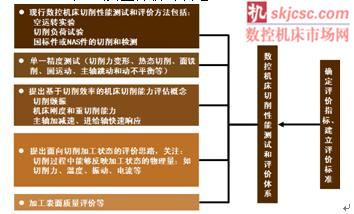
图2. 数控机床切削性能测试和评价体系内容
3、切削性能测试
(1)切削负荷测试
切削负荷试验包括主轴空运转试验、主传动系统的最大扭矩、最大功率和最大轴向抗力试验,以及机床刚性攻丝试验、镗削能力试验等,如图3所示。有关的参考依据为国家标准和企业根据用户需求提出的企业内部标准。
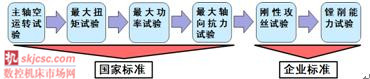
图3. 切削负荷试验内容和流程
1)空运转试验
进行空运转试验是为了得出主轴在不同转速下的实际功率,确定对应功率损耗。由于主轴的实际切削功率=总功率-空运转功率损耗。试验中需要主轴在五个不同转速范围进行测试,即主轴最高转速的20%,40%,60%,80%,100%。
2)主传动系统最大扭矩测试试验
主传动系统最大扭矩测试的目的是为了确定机床在不同加工方式下的实际切削参数是否达到设计参数,验证机床在最大切削负荷下的材料去除率。
试验需要在机床主轴恒扭矩调速范围内,选择一适当的主轴转速,采用铣削方式进行试验。通过改变进给速度,使机床主传动系统达到设计规定的最大扭矩。试验中需要记录:
出现最大扭矩时的主轴功率和对应进给量,计算材料去除率
主轴和工作台的振动量
观察加工表面是否出现振纹
3)主传动系统最大功率测试试验
主传动系统最大功率测试是为了确定机床在不同加工方式下的实际切削参数是否达到设计参数,验证机床在最大切削负荷下的材料去除率。
同样,试验需要在在机床主轴恒功率调速范围内,选择一适当的主轴转速,采用铣削方式进行试验。通过改变切削深度,使机床主传动系统达到设计规定的最大功率。记录:
出现最大功率时的主轴扭矩和对应切深,计算材料去除率
主轴和工作台的振动量
观察加工表面是否出现振纹
4)主传动系统最大轴向抗力测试试验
主传动系统最大轴向抗力测试是为了验证机床能够承受设计要求的最大轴向切削抗力。
试验在机床主轴恒扭矩调速范围内,选择一适当的主轴转速,采用钻削方式进行加工,并注入水基冷却液,通过改变进给速度,使机床达到设计规定的轴向抗力。记录:
相应主轴负荷率下的进给速度,并计算材料去除率
主轴轴向切削抗力,用以比对设计指标
5)刚性攻丝测试试验
刚性攻丝测试是为了评定机床设计规定的螺纹加工表现。对于给定直径丝锥,选择一固定主轴转速和切深,依据螺纹设计导程和进给量进行攻丝,评价螺纹孔加工精度是否达到设计要求。
(2)切削精度检测
切削精度检测主要是通过典型验收检验零件的加工和检测来实现。依据可实现的不同加工型面分为三轴检测零件和五轴检测零件两类,典型的三轴检测零件由ISO标准零件、美国NAS三轴检测零件和ASME检测零件,德国的NCG检测零件等。典型的五轴检测零件由NAS圆锥台,日本的四角锥台,德国的NCG 2005试件,以及我国的S型检测试件,如图4。
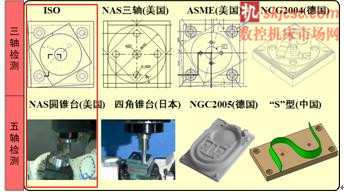
图4. 标准试验系统结果曲线
以ISO检测零件和S型检测零件为例分别对三轴和五轴检测零件的检测内容,代表零件的型面特征进行说明:
1)ISO 10791标准试件
ISO检测零件形式如图5所示,零件由底座正方向、菱形凸台和圆形凸台三个阶梯型面组成,在其上分别有位于中心的中心孔,四个直角出的位置孔以及底座相邻两个边上的3o角斜面。表1为ISO标准试件检测内容和评价允差。
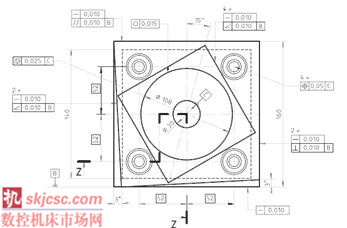
图5. 标准试验系统结果曲线
表1 ISO标准试件检测内容及评定标准
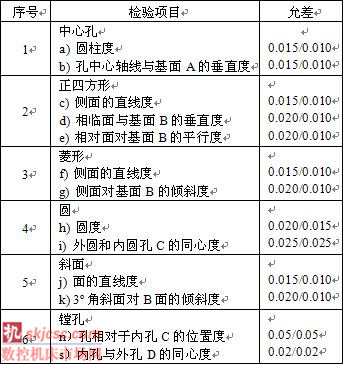
2)“S”型检测试件
“S”型试件是成都飞机工业(集团)有限责任公司提出的用来评价与检验五轴机床性能的数控机床验收检验零件,其测量结果可作为评价五轴机床工作精度的重要依据。研究“S”型试件的加工对于机床制造企业研究机床精度与性能具有极其重要的意义,其型面如图6(a)所示。“S”型检测试件主要由底座和S型缘条组成,如图6(b),其中底座特征包括:安装定位孔、基准孔;S型缘条包括:上下两条S型曲线、直纹母线。
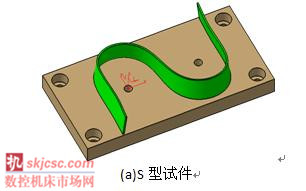
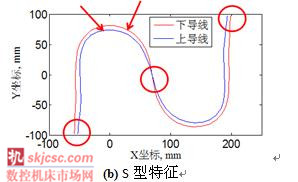
图6. 标准试验系统结果曲线
零件曲率变化剧烈,上下两条S型曲线在零件中心实现穿越,要求机床具有更好的换向和轴间转换能力,并且由于零件属于薄壁结构,要求机床刚性高,并且具有良好的动态性能。该零件可综合反映数控机床的几何精度、动态性能、加减速性能、摆角换向能力、轴间转换能力和机床刚度。
(3)单一精度测试
上述ISO零件和S试件的工作精度测试主要是针对典型验证零件加工和精度检测,参考国际标准和我国标准和规范。典型的测试零件、加工方法、流程等还可依据NAS标准、ASME标准、日本标准和德国标准分别对图5所示各种零件进行切削和检验。
除此之外,还可以针对机床的实际应用需求进行若干单一目标的切削精度检验,包括:
切削热态精度
圆运动切削精度
主轴不平衡精度
刀具磨损等
面铣削精度检测
切削力变形检测
4、结论
以往在进行数控机床切削有关测试和评价主要是针对数控机床切削负荷能力和切削精度进行检验和评价。
现在,沈阳机床集团依据用户需求和企业对产品的更高要求,对数控机床检验和评价除包含切削负荷检验和切削精度检验外,还进行多种单因素切削精度检测,提出切削能力预测和评价概念,引入数控机床切削加工状态监测和评价私下,并且对加工获得的表面质量进行评价,可以更全面和系统地反映数控机床的实际应用性能。
将来,将注重在数控机床的工序复合能力,即在一台机床上完成全部工序的能力、切削加工振动抑制和加工误差控制能力、节能和高效加工能力、应用和维护便易性等体现数控机床集成性、智能化、绿色性和易维护性等方面进行更为综合的检测和评价。(文自:沈阳机床(集团)有限责任公司)
投稿箱:
如果您有机床行业、企业相关新闻稿件发表,或进行资讯合作,欢迎联系本网编辑部, 邮箱:skjcsc@vip.sina.com
如果您有机床行业、企业相关新闻稿件发表,或进行资讯合作,欢迎联系本网编辑部, 邮箱:skjcsc@vip.sina.com