发动机深孔加工技术
2019-6-3 来源:转载 作者:-
深孔加工向来是金属切削加工难点,采用传统工艺会造成枪钻崩刃、折断等问题。通过改进枪钻结构形式——可转位刀片+带导条式高强度刀杆,采用带断屑槽刀片,使得排屑更顺畅,彻底解决折断及崩刃类异常,提升加工质量。
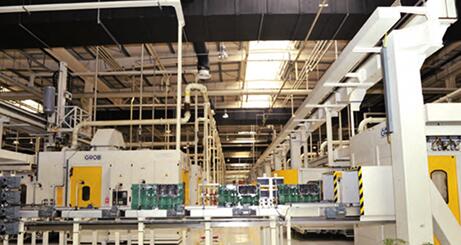
近年,我国东部某厂自主研发了一款油耗低、动力强、可靠性高的重型柴油机,深得用户青睐,其气缸体上有诸多用于冷却水道或润滑油道的深孔需要加工,其中底面φ26mm×275mm就是其中之一。为提升设备利用率,减少投资成本,在设计方案时放弃了传统的专用机床方案,而采用德国进口GROB(格劳博)高速加工中心加工,但经常会出现可修磨枪钻寿命低、断刀率高等问题。
1. 加工条件
加工设备:德国GROB G700加工中心
枪钻:单刃焊接枪钻φ26mm×546mm
刀柄:GUHRING HSK100-A侧固锁紧
切削液:FUCHS水溶性乳化液ECOCOOL 68CF2W,乳化液浓度:8-10%
内冷流量压力:75L/min,4MPa
切削参数:底面油孔,孔直径26mm,孔深275mm,转速1041r/min,线速度85m/min,进给量240mm/min,每齿进给量0.23mm
工艺要求如图1所示。
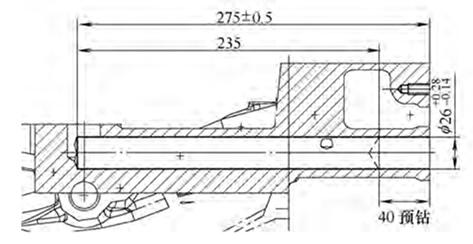
图1 底面深油孔加工工艺要求
2. 实际使用中存在的问题
该生产线投入使用后,为保证此类深孔加工质量稳定性,枪钻刀具为德国生产。但在实际使用中经常出现崩刃和断刀(见图2)等问题,造成刀具损耗和零件报废。
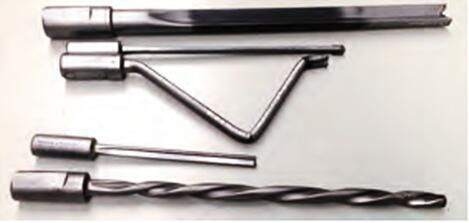
图2 枪钻断刀
统计该工序近半年时间内刀具使用情况得知:累计使用该枪钻230次,其中断刀15次,断刀率达到6.4%,刀具异常损耗达数万元。此外,为了减少发动机自重,缸体采用精密薄壁铸造工艺,实测该深油孔加工完后其厚度不足5mm,故在断刀发生后,由于铁屑和硬质合金刀头挤压,很容易造成孔壁破坏,从而造成整个气缸体报废,近半年造成工废6件。
3. 原因分析
通过组织技术人员分析排查刀具寿命情况和异常断刀状态,同时通过机床自带的主轴监控系统,分析其加工过程情况,进一步分析排查该深油孔加工断刀原因,主要为:
(1)枪钻刃口磨损严重。通过对换下的枪钻进行观察,发现枪钻主切削刃、侧刃和后刀面磨损情况比较严重,轴向磨损量超过2mm,增大了枪钻钻削过程中的切削阻力,增加断刀风险。
枪钻刀头磨损严重,与枪钻没有涂层有很大关系,缺少涂层对刀头硬质合金基体隔热和润滑保护,其磨损会急剧加快。而枪钻由于刀头和枪身需要焊接,加之两种材料高温变形量不同,决定了其无法在精磨后实施涂层工艺。
(2)排屑不畅。在对机床设备监控系统数据进行分析排查时发现,按照刀具布置图要求机床内冷流量/压力:75L/min、4MPa,但近半年出现多达20次以上的内冷高压报警,伴随该报警信息之后就会出现主轴负载报警以及断刀的发生。
之后,进一步对机床主轴负载曲线分析,并比较正常加工和断刀件的负载监控曲线后发现(见图3),正常加工的工作主轴负载新刀的上下波动范围35-55%,整个加工过程是一个线性均匀变化曲线,前后两个工件间的波动幅度小于5%;而断刀件负载监控图形,则会在内冷堵塞的时候不断升高,一般达到70%时,枪钻刀头焊接部位会扭断,该过程中其负载上下波动范围在45-70%,幅度达到25%;断刀工件孔内的大量铁屑也证实,排屑不畅,存在铁屑堵塞现象是该枪钻断刀的主要原因之一。
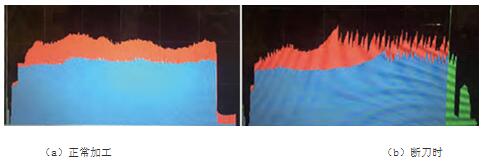
图3 主轴负载监控图形
4.优化改进方案
针对上述排查,刃口没有涂层保护、加工过程中存在堵屑问题是两个主要原因,确定后续改进优化方向和措施:
(1)提升排屑性能。通过增大内冷压力或流量方式,提升排屑性能。
(2)增加刀具耐磨性。在刀具材质不能改善的情况下,实施涂层工艺。
(3)加强刀杆强度。采用强度等级更高的刀杆,提高枪钻刚性,防止加工时刀杆断裂。
(4)改善断屑效果。优化切削刃口形式,改变铁屑形状,使其更利于排屑。
其中提升排屑性能方案,若提升内冷压力至6MPa,需要更换螺杆泵,成本较高,故考虑通过改善刀具结构来提升排屑效果。
在和德国技术专家讨论后,结合其实际应用案例,决定采用可转位刀片+带导条机夹式刀杆的刀具方案来进行刀具优化,具体结构如图4所示。
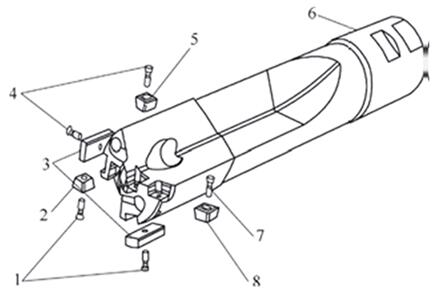
图4 1、4、7-螺钉 2、5、8-转位刀片 3-导条 6-刀杆
5.刀具试验过程
在试验刀具完成到位后,立即组织刀具试验,在第一次按照原参数和寿命试验,正常达到原强制换刀寿命后,为进一步挖掘刀具潜力,尝试开展极限寿命试验,从试验结果来看,刀具寿命有一定程度提升。
新转位刀具特点如下:
(1)刀杆采用高强度合金钢代替普通钢管精制而成,强度提升50%,刀杆成为可反复使用的耐用品。
(2)采用两段30mm磨制高精度硬质合金导条,保持加工过程中刀具支撑和平衡,利用导条自导向后续加工,保证深孔具有较好的孔径和直线度。
(3)采用3片带有复合TiAlN涂层、断屑槽可转位刀片组成主切削刃,耐磨性更好,错齿式布置,将26mm内铁屑分为6段,相比原枪钻的4段,铁屑更短,加之刀片前有压制断屑槽,更有利于排屑。
具体刀具及切削部位如图5所示。
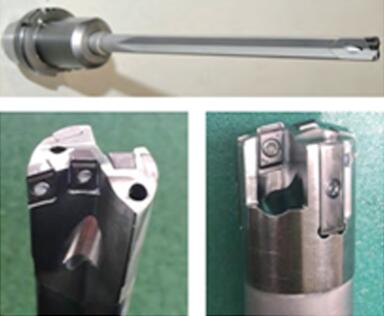
图5 优化后转位刀具及切削部位
6.持续改进
在试验取得初步成功后,继续对刀片存在微崩的异常情况进行分析、排查发现,该深孔在中间部位有一个φ10mm相贯孔和底部贯穿孔,加工至该部位时存在破孔和单边切削冲击,通过对NC程序优化,采取分段式进给。通过对使用后刀片观察发现,刀片失效形式正常。
结语
新可转位刀片式枪钻,经过半年时间合计201次的换刀验证,平均可加工孔数达到118,未出现过断刀,杜绝了因断刀问题造成的工件报废。同时,可转位刀片装调方便快捷,省去修磨环节;加工节拍也由之前的69.5s降至59.5s,单台刀具消耗成本节省约1.05元,提效降本明显。
来源:《世界制造技术与装备市场(WMEM)》
投稿箱:
如果您有机床行业、企业相关新闻稿件发表,或进行资讯合作,欢迎联系本网编辑部, 邮箱:skjcsc@vip.sina.com
如果您有机床行业、企业相关新闻稿件发表,或进行资讯合作,欢迎联系本网编辑部, 邮箱:skjcsc@vip.sina.com
更多相关信息