变频器在镗床进给系统改造中的应用
2017-7-3 来源:变频器;直流调速系统;镗床;进给;驱动 作者:程海龙 ,王慧
摘要:针对英镗机床存在的滑枕易损坏问题,将机床的进给系统改造成由变频器驱动,提高设备稳定性,降低工人的劳动强度。
关键词:变频器;直流调速系统;镗床;进给;驱动
做为粗加工的 10 英寸铣镗 (下称:英镗) 是50 年代的陈旧设备,设备状态已不稳定,特别是滑枕走刀部分进给传动离合器经常打滑发热,甚至抱死,无法脱开,致使离合器线圈经常烧坏。由于离合器安装空间小,拆装不便,给设备维修带来很大困难。为此笔者结合变频器在其他设备上的使用效果,对英镗进给控制系统进行改造。
1.异步电动机调速原理及选择
1.1 异步电机调速原理
异步电机转动是由定子主磁通和转子电流相互作用产生的。产生转子电流的必要条件是转子绕组切割定子磁场的磁力线。因此,转子的转速 n必须低于定子磁场的转速 n0,两者之差称为转差:
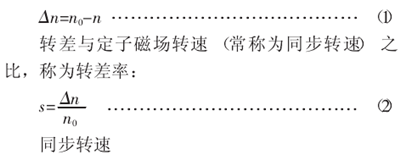
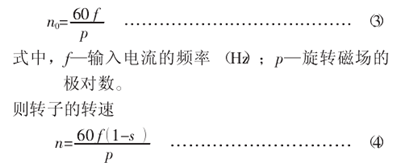
由此可知异步电动机有以下几种调速方法:(1) 改变磁极对数 p; (2) 改变转差率 s; (3)改变频率 f (变频调速)。本次改造利用 ACS510 变频器可连续改变供电电源频率的特性,连续平滑地调节电动机转速。异步变频调速电机具有调速范围广,调速平滑性能好,机械特性较硬的优点,可以方便地实现恒转矩或恒功率调速,其调速特性与直流电动机调压调速和弱磁调速十分相似。
1.2 异步电动机的选择
电机的“扭矩”
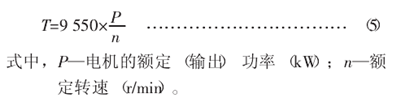
根据对各镗床进给系统对比分析可知,英镗的滑枕横截直径面积为 0.7 m2,德系镗铣床滑枕的横截面积为 0.2 m2,即存在一定差距。
德系镗铣床进给系统的电机功率 40 k W,转速1 500 r/min,电机的转矩 T=254.67 N·m;原英镗滑枕驱动主轴电机功率 100 k W,电机转速为 1 500 r/min,电机的转矩为 636.67 N·m,依据英镗老化程度及上述统计的机床数据,估算英镗滑枕驱转矩约为 350 N·m,由此根据滑枕电机的驱动转矩及进给电机需要的最低转速,算出电机功率为 30 k W,转速 730 r/min,最终选定 YZP250M-8,30 k W 电机。
2.变频器的控制系统
2.1 电气原理图设计
本文所选变频器的频率范围为 0~400 Hz。三相 380 V 交流电压通过断路器 QF1001 和接触器K1001 接到变频器的电源输入端 U11、V11、W11上,变频器输出电压 U2、V2、W2 接到负载电动机 M 上。QF1001 是电源总开关,有短路和过载保护作用,K1001 是送电接触器,当控制回路给出送电指令后,接触器吸合。制动电阻直接接到 R- 与R+端,在电动机制动时,会有部分能量要回馈到变频器内部,制动电阻的作用就是负责消耗这部分能量。对滑枕正反转的快速移动控制是通过K75、 K106、 K107 继电器带动辅助点实现 。 当K75 和 K106 继电器吸合时 , 端 子 DL1、 DL2、DL3 得电,变频器作正向快速运转,当 K75 和K107 继电器吸合时,端子 DL1、DL3 得电,变频器作反向快速运转。对滑枕进给控制是通过变频器的模拟 I/O 端子排,用电位计控制 AL1 端的模拟量输入电压,改变变频电机的输出频率,调节电机速度;当 K75、K106 继电器吸合时,DL1、DL2得电,DL3 失电,电机正方向进给,通过调节RP101 调节电机正向进给速度;当 K75、K107 继电器吸合时,DL1 得电,DL2、DL3 失电,电机反方向进给,调节 RP101 调节电机反向进给速度(见图 1、图 2、表 1)。
2.2 程序和电气回路设计
由于英镗是老旧设备,为了使机床更好地启动,克服滑枕间隙大,启动冲量大,启动矩大的缺点,特设计滑枕停止反向程序,以降低启动冲量 (见图 3)。
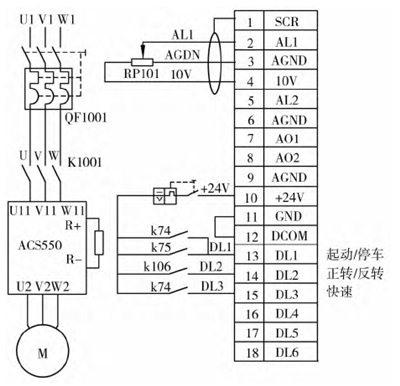
图 1 ACS510 变频器调速原理图 1

图 2 ACS510 变频器调速原理图 2
由图 3 可知,当 SW2B 的滑枕和主轴选出按钮按下,PLC 输入点 I0.09 闭合,在其他条件均满足的条件下,ZW 快速正向 207.01 启动,205.08 中间继电器自锁,205.08 中间继电器吸合;0.8 s 后,TIM023 时间继电器吸合;TIM023 时间继电器动作,带动 ZW 快速反向继电器启动,滑枕停止反向启动;205.08 中间继电器吸合,1.6 s 后 TIM022 继电器动作,滑枕停止。
2.3 变频器参数设置
在变频器的输入项目中有些是电机基本参数,如电机的功率、额定电压、额定电流、额定转速、极数等。这些参数非常重要,将直接影响变频器中一些保护功能的正常运行,一定要根据电机的实际参数正确输入,以确保变频器的正常使用。本文所选电机参数如下:电机型号 YZP-250M-8,
表 1 输入/输出地址表
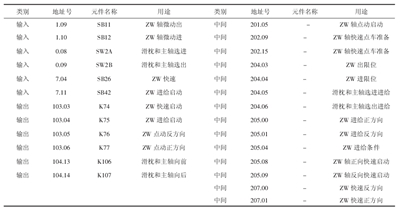
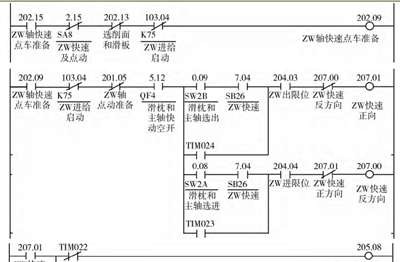
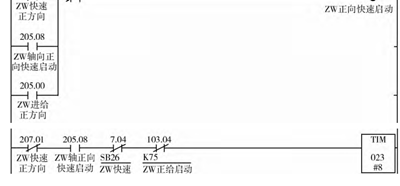
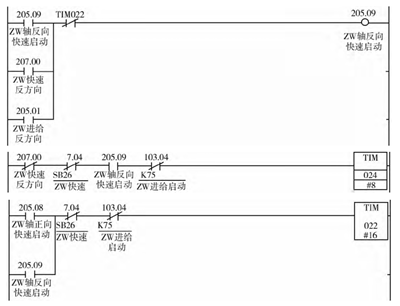
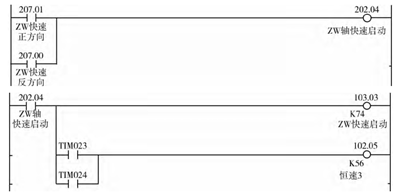
图 3 滑枕停止反向程序
电机 30 k W,额定电压 380 V,额定电流 63.4 A,电机的额定转速 730 r/min。所对应电机的变频器参数:
9901:电机语言选择,参数为 1=中文
9902:应用宏,参数为 1 标准宏
9905:电机额定电压,380 V
9906:电机额定电流,参数为 63.4 A
9907:电机额定频率,参数为 50 Hz
9908:电机的额定转速,设定参数为 730 r/min
9909:电机额定功率,参数为 30 k W
1103:给定值 1 选择,设定参数 1
1104:给定 1 最小值,参数为 0
1105:给定参数最大值,参数为 50
1201:恒速选择,参数为 3
1202,恒速 1,设定恒速 1 为 30 Hz
2101:起动功能,设定参数 1
2210:转矩提升电流,设定参数35.5 A
3.变频器常见故障排除
(1) 过流 (OVERCURRENT)表现为输出电流过大。检查和排除步骤:①电机是否过载;②加速时间是否过短 (参数 2202ACCELER TIME 1 ( 加 速 时 间 1) 和 2205ACCELER TIME 2 (加速时间 2));③电机是否发生故障,具体检查是否电机电缆故障或接线错误。
(2) 直流过压 (DC OVERVOLT)表现为中间回路 DC 电压过高。检查和排除步骤:①输入侧的供电电源发生静态或瞬态过电压;②减速时间是否过短 (参数 2203 DECELER TIME1 (减速时间 1) 和 2206 DECELER TIME 2 (减速时间 2));③过电压控制器是否处于正常工作状态。
(3) 过温 (DEV OVERTEMP)表现为散热器过温,温度达到或超过极限值。其中,R1~R4 :115 ℃,R5/R6:125 ℃。检查和排除步骤:①风扇是否发生故障;②空气流通是否受阻;③散热器是否积尘;④环境温度是否过高;⑤电机负载是否过大。
(4) 短路 (SHORT CIRC)表现为短路故障。检查和排除步骤:①电机电缆或电机是否短路;②供电电源是否发生扰动。
(5) 直流欠压 (DC UNDERVOLT)表现为中间回路 DC 电压不足。检查和排除步骤:①供电电源是否缺相;②熔断器是否已熔断;③主电源是否欠压。
(6) ALI 丢失 (AI1 LOSS)表现为模拟输入 1 丢失。具体为模拟输入值小于参数 3021 AI1FLT LIMIT (AI 故障极限) 的值。检查和排除步骤:①检查模拟输入信号源及其接线;②检查参数 3021 AI1FLT LIMIT (AI 故障极限) 的设置值,并且检查 3001 AI<MIN FUNCTION(AI 故障功能)。
(7) 电机过温 (MOT TEMP)表现为电机过热,根据传动的估算或温度反馈信号。检查步骤:①检查电机是否过载;②调整用于估算的参数 (3 005 ~ 3 009);③检查温度传感器和参数组 35 中的参数设置。
(8) 控制盘丢失 (PANEL LOSS)表现为控制盘通讯丢失,并且传动处于本地控制 (控制盘显示 LOC,本地),或者传动处于远程控制模式 (REM,远程),且起/停/方向/给定值信号来自控 制盘。检查步骤:①通讯链路和接线是否正常;②检查参数 3002 PANEL COMM ERROR(控制盘丢失故障);③检查参数组 10 的参数:控制命令输入和参数组 11 给定选择 (传动单元运行于 REM (远程) 模式) 是否有误。
(9) 电机堵转 (MOTOR STALL)表现为电机或工艺堵转,电机运行于堵转区。检查步骤:①是否过载;②电机功率是否不够。
(10) 接地故障 (EARTH FAULT)具体表现包括在电机或电机电缆处检测到的接地故障;在传动运行或停止时都监控到接地故障;在传动停止时接地故障检测的灵敏度更高,并且能够报告发生故障的位置。检查及纠正步骤:①检查/排除进线接地故障;②确认电机电缆没有超过最大允许长度;③如果输入电源是三角形连接,而且输入功率电缆的电容很大, 则确认是否发生导致传动停止情况下的接地故障误报。如要禁止传动停止时的故障检测功能,可使用参数 3023 WIRINGFAULT (接线故障)。如要禁止所有的接地故 障检测功能,可使用参数 3017。
(11) 欠载 (UNDERLOAD)表现为电机负载低于期望值。检查负载是否被断开。
(12) 电源缺相 (SUPPLY PHASE)表现为 DC 回路的纹波电压太高。检查步骤:①主电源是否缺相;②熔断器是否熔断。
(13) 电机缺相 (MOTOR PHASE)表现为电机回路有故障或电机有缺相。检查步骤:①电机是否发生故障;②电机电缆是否发生故障;③热敏继电器是否发生故障 (如果使用);④内部是否发生其它故障。
(14) 输出接线故障 (OUTPUT WIRING)表现为功率接线错误。当传动停止时,该故障代码监测着传动输入功率电缆和输出 功率电缆的正确连接。检查步骤:①输入电缆连接是否不正确,即电源电压是否没有接到传动输出;②如果输入功率电缆是三角形连接,而且输入功率电缆的电容比较大,则判定有可能出现接地故障误报的情况。
4 与传统调速系统对比分析
4.1 性能比较
英镗原进给部分采用 KSA23-90 A/220 V 数控直流调速系统驱动直流电机,也可以平滑而经济地调速。但是,结构复杂,维修成本高,劳动强度大。经过本次系统改造,采用变频器驱动变频电机,调速性能好,控制精度和调速的平滑性很高,调速范围广,通用性强,能满足任何工况对传动速度范围和精度的要求,能实现平滑无级变速;且电机平衡质量高,电机风扇能有效散热,可实现高速或低速长期运行。同时,变频器对变频电机保护更有效,在电机过载,外部线路出现故障时,能够及时报警,且查找排除设备故障快速、准确;降低设备大故障的发生机率。
4.2 成本比较
传统的直流调速系统控制器的造价成本大约为27 026 元 (机床的主控制系统 13 280 元;电机8746 元;零散配件 5000 元),机床电机寿命大约 5年。每年修 4 次,每次约为 1 500 元左右。变频调速控制系统的制造成本为 19 843 元 (机床主控制系统 5 510 元;电机 9 333 元;零散配件 5 000元)。改造后的进给系统使用至今没有发生故障。
5.结语
通过本次变频调速系统的改造,再次证明变频器在机床进给系统上比传统直流调速系统更有优势。本次改造重点是机床快速传动机构,对 1~7Hz 频率范围电机传动改进效果一般,可在进一步改造中通过降低齿轮啮合传动比来解决此问题,改进后,变频调速系统对机床进给系统的控制将更加完善。
投稿箱:
如果您有机床行业、企业相关新闻稿件发表,或进行资讯合作,欢迎联系本网编辑部, 邮箱:skjcsc@vip.sina.com
如果您有机床行业、企业相关新闻稿件发表,或进行资讯合作,欢迎联系本网编辑部, 邮箱:skjcsc@vip.sina.com
更多相关信息