基于行星滚柱丝杠副的机电作动器动态特性分析
2017-5-5 来源:西北工业大学 作者:乔冠,刘更,马尚君,佟瑞庭,周勇
摘要: 以舵回路系统中机电作动器为研究对象,考虑机电作动器的安装和舵面负载连接,建立了基于行星滚柱丝杠副的机电作动器数学模型。采用 AMESim 进行仿真对比分析,探讨了机电作动器中结构刚度、摩擦和间隙等非线性因素对系统动态性能的影响。结果表明: 相比传动刚度,结构刚度中固定刚度的提高对于系统动态响应的改善作用更明显; 行星滚柱丝杠副间隙量越大,系统的阶跃响应波动幅值越明显; 在给定舵控指令下,机电作动器的仿真位移输出响应误差最大为 1. 8 mm,相对误差为 1. 2% ,从而较好的反映了模型的有效性,为功率电传机电作动器的进一步结构优化和控制提供理论依据。
关键词: 机电作动器; 行星滚柱丝杠副; 动态特性; 结构刚度; 间隙非线性
机电作动器( Electro-Mechanical Actuator,EMA) 是功率电传作动系统的一个分支,由于其具有重量轻、工作效率高、系统可靠性高和便于维护[1 - 2]等优点,广泛应用于飞行舵面控制、推力矢量控制、飞机刹车和工业过程控制等军民领域。国外在 EMA 动态特性研究方面起步较早,建立了EMA 系统级功率键合图模型和基于 AMESim 环境的EMA 仿真模型,对采用反向式行星滚柱丝杠副的 EMA进行动态性能测试,通过力矩和转速干扰实验验证模型的有效性[3]。Karam 等[4]讨论了力控制的基于行星滚柱丝杠副的 EMA 中摩擦、转子惯量和测试平台刚度等因素的影响,这些因素都会改变 EMA 的稳态和动态特性。Mare 等[5 - 6]提出基于仿真模型的 EMA 率传递初步设计准则,以确保测试平台结构与目标动态性能的一致,考虑了结构部件的静态与动态性能的限制,从而使得控制器设计更简单。Habibi 等[7]分析了控制飞机舵面的 EMA 动态特性,表明由空程和静态摩擦产生的死区是限制 EMA 输入输出特性的重要因素,并通过使用内环控制策略减小死区对系统的影响。国内 20世纪 90 年代初才开始研究包括机电作动器和电动静液作动器( Electro-Hydrostatic Actuator,EHA) 在内的功率电传作动器,已证实该技术的可行性和有效性。齐海涛等[8]基于 AMESim 对 EHA 进行了建模和仿真分析,仿真结果表明所设计的 EHA 动态性能良好,达到了预定的性能指标。马尚君等[9]建立了 EMA 中的标准式行星滚柱丝杠副有限元模型,基于显式动力学有限元算法对其动态特性进行仿真分析,为研究 EMA 整体性能的提高提供参考。国内学者多数的研究工作集中于 EMA 的复合式余度控制[10]、混合作动系统研究[11]等方面,然而对基于行星滚柱丝杠副的 EMA 中结构刚度、摩擦和间隙因素对 EMA 动态特性影响研究较少涉及,鲜有文献报道考虑 EMA 的安装和舵面负载连接并建立数学模型。
本文考虑 EMA 的安装、EMA 与舵面负载的连接,建立了基于行星滚柱丝杠副的 EMA 数学模型。采用AMESim 仿真分析,分别探讨了舵回路系统中 EMA 的结构刚度、摩擦和间隙等非线性因素对系统的动态性能影响。在相同给定的舵控指令下,对比本文 EMA 与传统伺服油缸的位移跟踪精度,结果表明建立的 EMA模型是有效的。
1.EMA 系统组成
1. 1 EMA 结构形式
典型的 EMA 在飞行器舵回路系统中的组成见图1,EMA 主要由无刷直流电机、控制器( 主要包括速度、位置控制器和功率变换器) 、齿轮减速器( 或者带传动) 、滚珠丝杠副( 或者行星滚柱丝杠副) 这四部分组成。其中,滚珠丝杠副( Ball Screw Mechanism,BSM) 和行星滚 柱丝 杠 副 ( Planetary Roller Screw Mechanism,PRSM) 作为 EMA 中的执行机构,用来传递扭矩、进行运动变换。PRSM 用滚柱作为中间传动体,用滚动摩擦取代滑动摩擦,具有效率高、寿命长、承载能力强等特点。其中,标准式行星滚柱丝杠副( Standard PlanetaryRoller Screw Mechanism,SPRSM) 主要传动装置有丝杠、螺母和滚柱,其基本结构见图 2。本文以基于 SPRSM 的EMA 为对象建模并进行其动态特性研究分析。
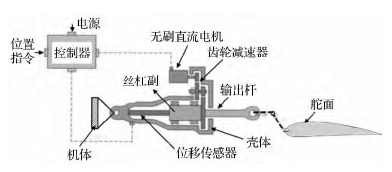
图 1 舵回路系统中的 EMA 结构
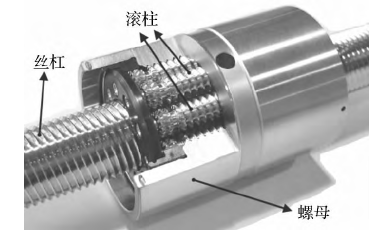
图 2 SPRSM 基本结构
1. 2 EMA 在舵回路系统中的工作原理
EMA 通过铰链安装于机体,并由其输出杆带动摇臂等连接机构,最终实现舵面的位置控制( 见图 1) 。控制器接受来自飞控计算机的舵控指令,驱动无刷直流电机做正反向运动,再通过齿轮装置减速增扭,把丝杠的旋转运动转化为输出杆相对于壳体的直线运动,驱动舵面实现相应的动作。同时,电机中的电流信号,电机输出轴的转速信号和舵面的位置信号都通过反馈参与到控制器的运算实现闭环反馈控制。
2.EMA 系统建模
结合图 1,在 AMESim 中建立的 EMA 整个系统模型见图 3,部分子模型采用超级元件封装。EMA 的建模主要包括: “a”为正弦或给定的信号指令输入; “b”和“c”分别为电机控制器和无刷直流电机数学模型;“d”和“e”分别为齿轮副和 SPRSM 的机械传动模型;“f”和“g”为考虑作动器固定机构和连接机构的等效刚度和阻尼; “h”为舵面及气动力负载模型。
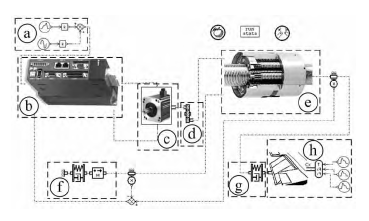
图 3 EMA 系统模型
2. 1 控制器模型
控制器是 EMA 的重要组成部分,为防止电枢电流过载,保证电机的响应速度和动态特性,控制器采用电流、速度双闭环,两环均采用 PI 控制; 位置环采取简单的比例控制( 见图 4) 。该模型还包括信号采样、电压电流限幅以及力闭环反馈等。
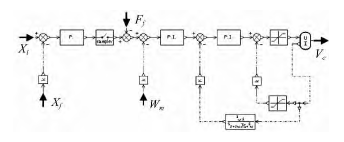
图 4 控制器模型
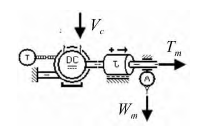
图 5 电机模型
2. 2 电机模型
采用 270 V 永磁无刷直流 电 机,选 用 AMESim电机及驱动库中的直流电机模型( 见图 5) 。参照表1,电机的电枢电流 Ic与输入电压 Vc的关系通过一个一阶传递函数 Ge描述
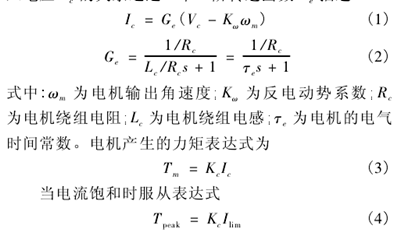
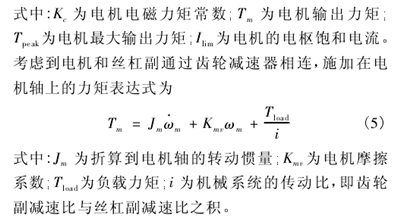
表 1 电机的相关参数设置
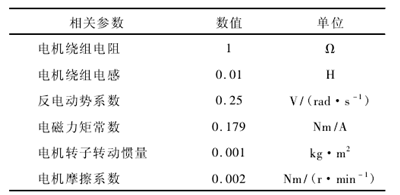
2. 3 SPRSM 模型
SPRSM 模型考虑了部件的移动和转动部分,并综合计入了摩擦和间隙非线性因素。EMA 中的摩擦非线性影响是降低系统控制性能因素之一。由于单独分离
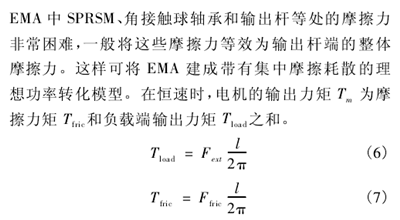
式( 6) 和式( 7) 中的 l 为 SPRSM 的导程,Fext为负载端承受的外力,Ffric为输出杆端的整体摩擦力。EMA的整体摩擦力是外力和电机转速的函数。为了简化复杂的因果关系,可通过式( 8) 对整体摩擦力进行建模,该模型考虑了负载端承受的外力。
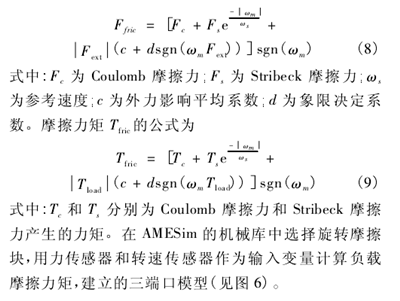
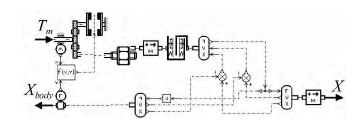
图 6 SPRSM 的三端口模型
2. 4 舵面模型
AMESim 是面向对象的液压 / 机械系统建模、仿真及动力学分析软件。本文在建立舵面模型时,选用其平面机构库中的模型模拟舵面的实际情况。包括舵面安装铰链、舵面质心、加载位置及摇臂的建模等,提供了更丰富的力与力矩加载( 见图 7) 。这样不仅可以仿真舵面的负载特性,还可以通过三维可视化功能AMESim-Animation 观察舵面的实际运动情况。
3.EMA 动态特性分析
设置控制指令为 0.1 s 时刻的 0.1 V 阶跃信号,经转化比例系数,即为 1 mm 阶跃信号,系统仿真时间为10 s,在 5 s 时加入 10 000 N 的阶跃冲击力,参数见表 1和表 2。
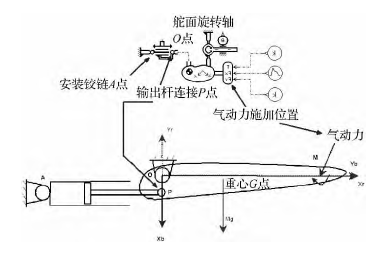
图 7 舵面模型
表 2 EMA 系统的相关参数设置
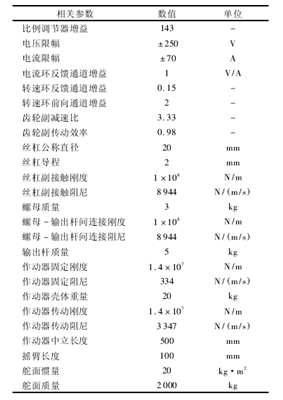
3.1 传动间隙非线性因素影响
间隙是限制速度与位置控制性能高低的最重要非线性影响因素之一。EMA 的间隙主要包括 PRSM 中丝杠侧与螺母侧的轴向间隙,齿轮传动中的齿侧隙和轴承轴向间隙等。间隙的存在使得 EMA 在反向作动时产生作动器位置输出误差,影响作动器位置输出精度。由于传动链中尺寸误差、安装误差和长期磨损,间隙不能完 全 消除。间隙非线性 可以 采用 Physical 模 型、Phase plane 模型Dead zone 模型和 Rubber 模型来表示。Dead zone 模型是 Physical 模型的简化,在转轴无阻尼 或 小 阻 尼 时 Dead zone 模 型 是 一 种 有 效 的 模

此时轴的模型假设为纯弹簧,不计惯量和内部阻尼,并且在不接触时处于稳定状态( 见图 8) 。如果考虑轴的内部阻尼,修正的 Dead zone 模型如式( 13) 。
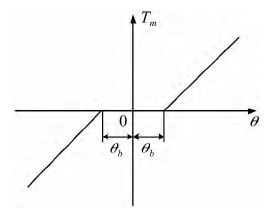
图 8 Dead zone 模型
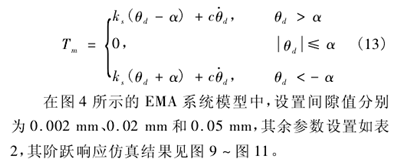
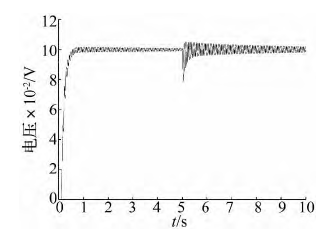
图 9 间隙值为 0. 002 mm 的系统阶跃响应
对比图 9 ~ 图 11 的三条系统响应曲线可知,不同大小的间隙值对系统的影响程度不同,间隙量越大,系统的阶跃响应波动幅值越明显。在 EMA 中,间隙影响的不仅是控制精度,还对系统的稳定性产生重大影响。为改善 EMA 的动态输出响应,从机械方面,采用消隙齿轮结构,对 PRSM 预紧; 从材料方面,采用抗磨损材料; 从控制方面,通过软件和控制策略 进行间 隙 补偿等。
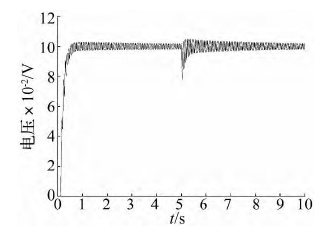
图 10 间隙值为 0. 02 mm 的系统阶跃响应
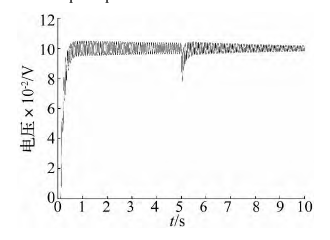
图 11 间隙值为 0. 05 mm 的系统阶跃响
3. 2 摩擦非线性因素影响
采用前述图 6 建立的 SPRSM 摩擦模型,由式( 9) 可求得摩擦力矩,图 12 比较了考虑摩擦和不考虑摩擦模型的系统阶跃响应,此时假设机械传动中不存在间隙。
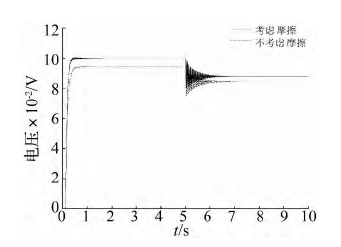
图 12 考虑摩擦和不考虑摩擦模型的响应对比图
可见,考虑摩擦的系统存在更大的误差,应通过力闭环反馈改善。在 AMESim 模型中的等效连接结构与舵面间加入力传感器,将测量到的力信号反馈到控制器形成闭环( 见图 13) 。同时在反向通道内加入一阶低通滤波器,结构为
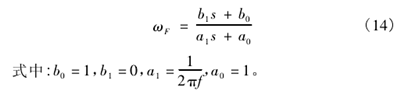
从图 14 可知,加入力闭环反馈后,响应曲线的振荡幅值小于无力闭环反馈的工况,同时系统的静态误差减小。同样,常用减小机械系统中摩擦的方式可改善运动部件的润滑条件,采用抗摩擦材料以及软件进行摩擦补偿等
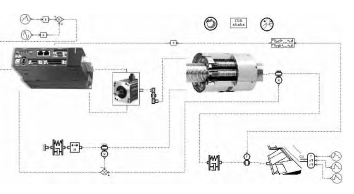
图 13 加入力反馈的 EMA 模型
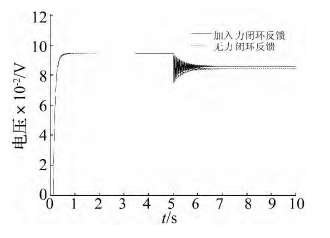
图 14 考虑力闭环反馈的系统响应对比图
3. 3 固定刚度和传动刚度的影响
实际舵回路系统中,机体和被控舵面的刚度并不是无限大。本文在 EMA 系统建模时采用集中参数法考虑了壳体与机体间和输出杆与舵面负载间的弹簧效应。由于负载系统中含有以柔性结构相连的多级共振性负载,因此 EMA 壳体和舵面不能简单采用单质量 -单弹簧系统近似,而应考虑输出杆与被控舵面间的传动刚度和固定壳体的固定刚度( 统称为结构刚度)[13]。KZ1为固定刚度; KZ2为传动刚度。从图 15 ~ 图 16 可知,结构刚度对 EMA 的动态性能影响较大。当固定刚度和传动刚度均为 1 × 107N / m时,系统的阶跃响应存在小幅值振荡,在 5 s 时刻施加10 000 N 的阶跃冲击力会使系统振荡的幅值更剧烈,不利于系统的快速稳定。从图 17 可知,此时的谐振频率为 7. 75 Hz,此振荡频率由 2 000 kg 的舵面质量,与一条等效弹簧串联得到。
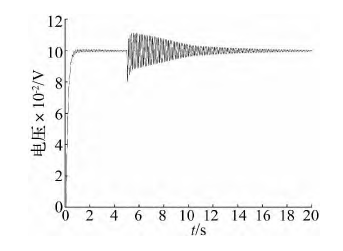
图 15 固定刚度和传动刚度均为 1 × 107N / m 时系统阶跃响应
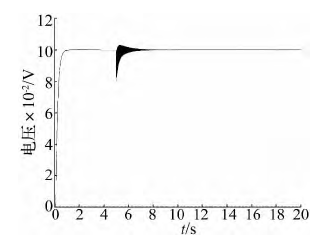
图 16 固定刚度和传动刚度均为 5 × 108N / m 时系统阶跃响应
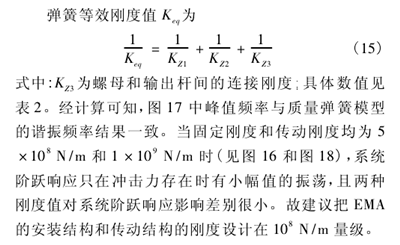
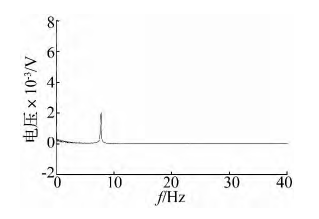
图 17 固定刚度和传动刚度均
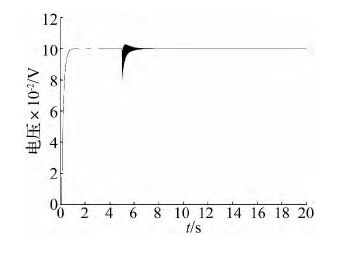
图 18 固定刚度和传动刚度为 1 × 109N / m 时系统阶跃响应
另一方面,从图 19 ~ 图 22 可知,当传动刚度为 1 ×107N / m 时,提高固定刚度可以明显提高系统的动态响应,而当固定刚度提高到 1 × 109N / m 时,已经和固定刚度为 5 × 108N / m
时的系统动态响应无明显区别。同样,当固定刚度为 1 × 107N / m 时,提高传动刚度也可以在一定程度上提高系统的动态响应,但即使当传动刚度为 1 × 109N / m,系统的阶跃响应依然存在大范围的振荡。通过以上分析可知,固定刚度的提高对于系统动态响应的改善作用更明显。为保证 EMA 在工作过程中的信号跟踪能力,除采用必要的控制策略外,在结构方面应适当优先提高固定刚度。
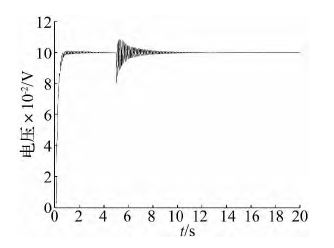
图 19 固定刚度为 5 × 108N / m 传动刚度为 1 × 107N / m 时系统阶跃响应
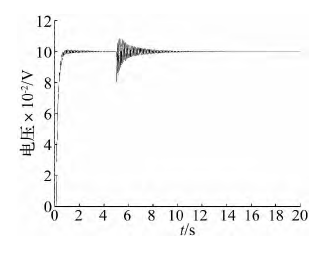
图 20 固定刚度为 1 × 109N / m 传动刚度为 1 × 107N / m 时系统阶跃响应
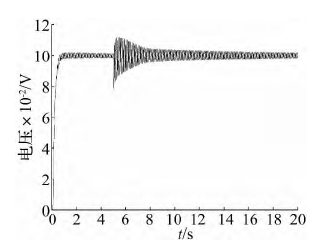
图 21 固定刚度为 1 × 107N / m 传动刚度为 5 × 108N / m 时系统阶跃响应
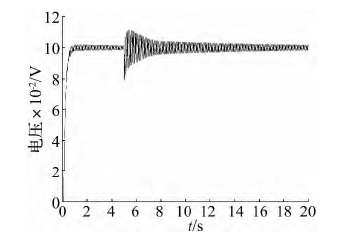
图 22 固定刚度为 1 × 107N / m 传动刚度为 1 × 109N / m 时系统阶跃响应
3. 4 EMA 系统动态仿真
根据 EMA 实际舵控经验,给定位移信号,参数如前述表 1 和表 2,设置仿真时间为 200 s,仿真步长为 0.001 s,得到的仿真结果见图 23。从图 23 ~ 图 24 可知,系统的响应时间能够满足要求,系统动态跟踪性能良好。
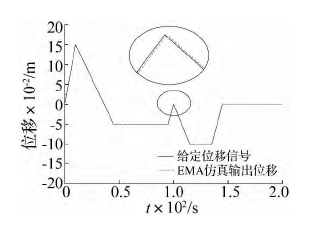
图 23 EMA 仿真输出位移跟踪曲线
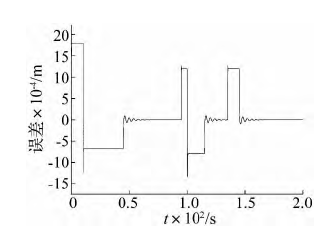
图 24 位移跟踪误差曲线
在 200 s 的时间内,EMA 的输出位移与给定位移信号的误差最大为 1. 8 mm,相对误差为 1. 2% ,从而较好的反映了模型的有效性。同时,对比本文中 EMA 与文献[14]所述的传统阀控液压作动器,在给定相同舵控指令下,这两种作动器都能跟踪给定位移信号,但就跟踪效果而言,传统的阀控液压作动器要优于 EMA,这也正是目前液压作动器存在的主要原因。然而,在重量、体积、系统效率和可维护性等方面,EMA 有绝对优势。
4.结论
采用 AMESim 图形化建模方法,建立了基于 PRSM的 EMA 模型,对其在舵回路系统中的动态特性进行了仿真分析,得出以下结论:( 1) 传动间隙和摩擦特性是限制系统精度和稳定性的重要非线性影响因素。间隙的存在使得系统振荡不利于快速稳定,间隙量越大,系统的阶跃响应波动幅值越明显; PRSM 中的摩擦使得系统存在静态误差,可通过力闭环反馈减小其对系统的影响。( 2) 固定刚度和传动刚度对 EMA 动态阶跃特性有不同程度的影响,建议把安装结构和传动结构的刚度设计在 108N / m 的量级; 通过对比可知,固定刚度的提高对于系统动态响应的改善作用更明显,在结构设计方面应适当优先提高固定刚度。( 3) 在给定舵控指令下,机电作动器的仿真位移输出响应误差最大为 1. 8 mm,相对误差为 1. 2% ,从而反映了模型的有效性
。
投稿箱:
如果您有机床行业、企业相关新闻稿件发表,或进行资讯合作,欢迎联系本网编辑部, 邮箱:skjcsc@vip.sina.com
如果您有机床行业、企业相关新闻稿件发表,或进行资讯合作,欢迎联系本网编辑部, 邮箱:skjcsc@vip.sina.com
更多相关信息