大功率激光切割机床远程监控系统设计
2017-4-27 来源:华北科技学院 机电工程学院 作者:卜祥丽,徐 斌,李孝平,黎 冠
摘 要: 针对现有大功率激光切割机床产品网络化不足、维护效率低、维护成本高等问题,结合目前成熟的 GPRS 移动通信技术,提出了基于云服务器的高功率切割机床远程监控系统,构造远程监控平台,能够远程监控多台激光切割机床设备。针对高功率激光切割机床远程监控系统设计了数据采集智能终端,实现了现场数据通过 GPRS 技术传送到云端,为高功率激光切割故障的快速诊断与处理提供了数据支撑。
关键词: 激光切割; 远程监控; 云服务; GPRS; STM32
0.引言
目前,随着激光技术的不断发展,激光加工技术也得到了飞速发展。激光加工已广泛应用于钣金切割、雕刻、打孔、焊接、表面处理等领域。激光切割过程是将激光束聚焦到工件表面,利用其释放的能量瞬间使工件融化并蒸发,从而达到切割和雕刻的目的。激光加工具有切割速度远远高于传统的切割技术,切割精度高,可以实现自动排版加工,且不受切割图案限制,切口平滑等特点,将在切割市场占有越来越多的市场份额[1 - 4]。随着电子、通信以及互联网技术的迅猛发展,激光加工也朝着大功率,高速度等方向快速发展,同时,激光切割机床信息化和智能化技术也得到了越来越多的重视。当前,国内钣金加工车间工作环境相对较差,加工粉尘、辐射、噪声等都会给现场操作人员身体造成不同程度的危害,因此,远程实时监控激光切割机床工作状态和现场环境参数成为激光加工机床制造业重点研究的热点问题之一[5]。文献[6]针对 FANUC 等 3 种不同的数控系统,利用一台服务器,基于通用的通信接口,实时采集数控设备的加工状态和工艺过程参数等信息; 文77第 13 卷第 3 期2016 年 6 月华北科技学院学报Journal of North China Institute of Science and TechnologyVol. 13 No. 3Jun. 2016献[7]利用网络,对数控机床加工工艺参数、系统报警信息、PLC 控制信号、伺服驱动参数、系统故障诊断、机床维护信息等进行远程监控和管理; 文献[8]利用传统的现场总线技术和无线传感网络实时采集数据,采用 ARM Cortex - M3 嵌入式芯片对数据进行处理,实现了基于 Web 环境的数控机床远程监控系统。伴随着 GPRS 技术的不断完善发展,越来越多的应用于机床监控领域[9 - 11]。本文提出针对大功率激光切割机床,利用 GPRS无线通信技术,在激光切割机床现场设置数据传输模块,实时将激光切割机床的加工状态和环境信息传输到云端服务器,从而实现对激光切割机床状态的远程实时监控。
1.总体方案设计
目前一些先进的数控系统具有通信接口,能够将数据参数传送出来,通过数据接口实现对分散的数控设备的远程控制。GPRS 能够实时在线,支持多点数据同传,传输时延小,满足一般监控系统对数据采集和传输实时性的要求。随着国内移动通信技术的快速发展,绝大部分地区已经覆盖了GPRS 网络,因此为大范围的设备在线监控提供了基础条件,系统的传输容量大,能很好满足传输监控数据的需要,且通信费用越来越低,应用方便。随着智能手机的普及,维修人员可以通过应用程序浏览云端数据,进而得知数控机床发生故障前后的数据,为快速诊断奠定了应用的基础。
本文以发格激光切割机床作为控制对象,基于串口通信和 GPRS 移动通信技术构建高功率激光切割机数据采集传输系统,实现对激光切割机床状态的无线远程监控。激光切割机床远程监控系统主要由 6 部分组成: 现场激光切割机床、摄像机、车间环境采集模块、现场智能监控终端模块、云服务器以及远处监控客户端,总体结构框图如图 1 所示。
2.硬件设计
硬件部分主要涉及现场智能监控终端模块,本系统以 STM32 微处理器和 GPRS 无线通信模块为核心,现场智能监控终端通过串口数控机床进行通信,并将数据通过 GPRS 无线通信模块实时传输到云端。云端服务器自动记录上传的数据,任何联网的电脑通过云端均可获取当前机床的工作状态。
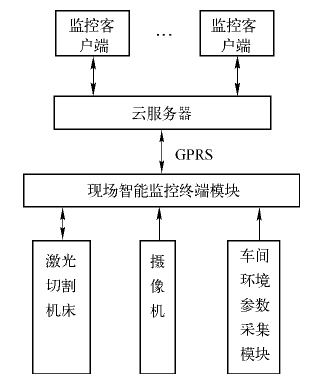
图 1 激光切割机床远程监控系统框图
当激光切割机床出现故障时,现场智能监控终端将故障信息通过短信服务模块发送到预制的手机电话号码。维修人员通过短信即可获取数控机床故障信息,并进行故障诊断。
2. 1 现场智能监控设备硬件设计
现场智能监控模块的硬件由 32 位微处理器、数据显示单元、GPRS 无线数据传输模块、数据采集模块和数据存储模块组成,系统硬件原理图如图 2 所示。
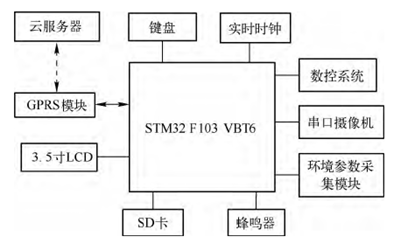
图 2 现场监控设备硬件原理图
微处理器选用 STM32 系 列 单 片 机STM32F103VBT6 作为主控芯片。采用 SIMcom 公司的 SIM800E 模块进行 GPRS 数据传输,SIM800E是一种专门用于 GPRS 数据传输模块,SIM800E 支持多种 TCPIP 连接协议和多种连接方式,单步与多步开发环境,传输模式可选择透明与非透明模式,在服务端或客户端支持 TCP 和 UDP 协议栈,在本系统设计中,SIM800E 模块和 STM32 单片机的串口 2 相连,实现 GPRS 模块与单片机之间的通信。显示单元采用 3. 5 寸真彩触摸屏,实现人机交互。
2. 2 摄像头监控硬件设计
图像采集选用串口摄像头模块,采用成都蓝矩科技生产的 LJ - DSC02 系列串口摄像头,200万像素,该模块内置 0 V 系列高性能 CMOS 传感器,直接输出 JPEG 图片,通过 RS232 或者 RS485进行数据传输,配置 6 颗 850 nm 夜视灯进行红外补光。在本系统中将 LJ - DSC02 和单片机的串口 1 相连,实现摄像头数据的采集。
2. 3 环境采集模块硬件设计
环境参数采集采用 GK - 508F 模块,该模块可以采集 16 路模拟量信号,通信支持 RS232、RS485 和 MODBUS 协议接口。在本系统中,主要采集激光切割机床工作时的环境温度、湿度、压力、电源电压、电流、冷却风机温度等信号。
3.软件设计
在 Keil 开发环境中设计终端控制软件,软件主要分为系统初始化模块、数据采集模块、数据分析模块、触摸屏显示模块、通信模块等。智能监控设备启动后首先进入系统初始化模块,初始化完成后,开始数据采集。数据采集部分主要包括对对数控机床运行参数的采集、对摄像机图像的采集、现场环境参数的采集。数据采集完成后,进入数据分析模块、分析完成后,进行数据显示和存储,最后进入通信子程序进行数据远传。数据传送完成后,进入下一个循环,软件流程如图 3 所示。
系统初始化主要进行时钟、中断、GPIO、串口等初始化工作。完成后依次与数控机床、串口摄像机、环境采集模块和 GPRS 模块依次通信。激光切割机床数控系统的通信采用串口异步通信协议。现场监控设备程序运行时,首先向数控系统发送握手请求,握手成功后,接收数控系统传出的各种参数数据; 握手失败,发送故障显示接口。在数据处理分析模块中,将激光加工机床的工艺参数、NC 程序、螺距误差补偿参数、工件坐标数据等数据进行分类保存,通过 GPRS 传输到云端服务器。当接收到云端服务器更新数据请求的命令时,数控机床通信管理模块通过通知数控机床修改通信参数,进行数据更新工作。
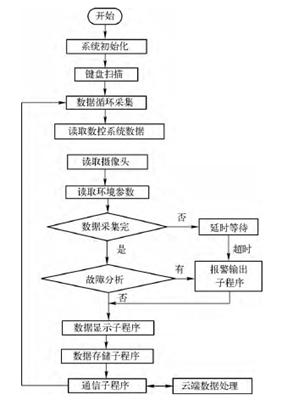
图 3 软件控制流程图
串口摄像机模块通过单片机获取摄像头图像,设备上电初始化时打开串口,设置图像分辨率。正常通信时循环执行开始采集图像、获取图像数据、结束采集图像并上传。数据分析模块对采集的各种数据,与设定值进行比较,符合报警条件时,将信号发送至报警子程序。为了方便人机交互,设置了数据显示模块,采用迪文 4. 3 寸真彩触摸屏,完成数据显示与报警信息查看。
为了避免由于网络产生故障时,数据不能及时上传,现场设置数据存储模块,将采集到的数据及报警信息,本地存储于工业 SD 卡,确保数据的安全性。GPRS 模块通信时,首先进行参数初始化,主要参数有: 手机卡号码、DNS 服务设置、GPRS 服务密码、APN 设置、IP 地址、TCP 端口号等,系统上电后,自动建立一个 TCP 通讯,通信成功后,智能终端模块和云端的数据实现无线交互。
4.结论
实践表明,利用 STM32 单片机和 SIM800LGPRS通信模块设计的现场智能监控终端,体积小、功耗低,可以与激光切割机床数控系统实时对接,通过该终端,能够将激光切割机床现场数据通过无线网络,传送至云端服务器,通过云服务监控客户端,维修人员可以给用户提供方便快捷的技术支持,具有较好的现实意义和推广价值。
投稿箱:
如果您有机床行业、企业相关新闻稿件发表,或进行资讯合作,欢迎联系本网编辑部, 邮箱:skjcsc@vip.sina.com
如果您有机床行业、企业相关新闻稿件发表,或进行资讯合作,欢迎联系本网编辑部, 邮箱:skjcsc@vip.sina.com
更多相关信息