低速单向走丝电火花线切割钛合金 TC4 表面粗糙度试验研究与建模
2017-4-1 来源:东北大学 机械工程与自动化学院 作者:巩亚东,孙瑶,刘寅
摘要: 低速单向走丝电火花线切割在钛合金加工领域有着不可替代的作用和地位,但微观放电的复杂性决定了其难以建立有效的表面粗糙度数学模型,同时现有机床系统中并没有针对钛合金材料的加工参数。以钛合金 TC4 为试验研究对象,采用 Design-Expert 设计 Box-Behnken 试验并通过三维轮廓仪和扫描电子显微镜对加工后的表面形貌、功率频谱和重熔层进行分析。观测结果表明: 电火花加工表面没有明显纹理,为各向同性,不同于磨削加工表面; 当峰值电流为 40 A,开路电压为 100 V,脉冲宽度为 18 μs 时,裂纹延伸至 TC4 基体。利用响应曲面法通过模型选择和显著性检验得出三维表面粗糙度的 2 阶数学模型,能正确地映射出低速单向电火花线切割钛合金的工艺规律。为了提高模型预测精度和泛化能力,引入 BP 神经网络建立组合模型,试验验证结果表明: 样本内相对误差均值由 4. 33% 降低到 3. 26% ,样本外相对误差均值由 13. 31% 降低到 8. 50% ,为电火花加工工艺仿真提供新的方法和途径。
关键词: 机械制造工艺与设备; 低速单向走丝电火花线切割; TC4; 三维表面粗糙度; 响应曲面; BP 神经网络
0 引言
低速单向走丝电火花线切割的非机械接触、加工精度高和表面质量好等特点使其成为微细复杂三维结构制作的主流技术,有着不可替代的优越性[1 - 2]。低速单向走丝电火花线切割加工的工件表面因受火花放电的瞬时高温和工作液快速冷却的影响使其表层的化学成分和组织结构会发生很大变化,这将严重影响工件使用性能、密封性、配合精度和使用寿命等[3]。因此为了提高低速单向走丝电火花线切割加工表面质量,国内外的学者对其表面形貌做了许多研究。Sarkar 等[4]对电火花线切割加工钛合金进行参数优化得出表面粗糙度 Ra与切割速度之间关系。Kiyak 等[5]发现减小脉冲宽度和增大脉冲间隔能有效减小 40Cr Mn Ni Mo864 的表面粗糙度 R. Mahapatra 等[6]用田口方法对电火花线切割放电参数进行优化,并建立表面粗糙度 Ra的非线性回归模型。李凯等[7]认为电火花加工工件的表面粗糙度不应沿用切削加工表面粗糙度的评定方法和测量手段,建议用方形的评定面积代替评定长度。张志航等[8]通过小波变换方法,准确提取了电火花线切割加工表面三维粗糙度的基准面并更新了三维粗糙度评定体系。
钛合金 TC4 因具有高温力学性能优异、比强度高和失稳临界值高等优点而被广泛应用于航空航天领域,但其导热性差和易变形特点使其成为一种典型难加工材料。对于单向走丝电火花线切割而言,其加工钢、铜和硬质合金等材料的技术和针对这些材料的多次切割工艺都已相当成熟,但对于其他材料的加工研究相对较少,目前单向走丝电火花线切割机床系统中没有针对 TC4 材料的加工参数和多次切割工艺。此外,在航空航天的产品中,承力构件一般采用单次切割。因此,本文以 TC4 单次切割为研究对象,通过对比磨削加工表面和单向走丝切割加工表面的特性,确定采用三维表面粗糙度 Sa代替二维表面粗糙度 Ra. 应用 Design-Expert 设计 Box-Behnken 试验,得出三维表面粗糙度 Sa的数学模型,通过响应曲面法分析得出峰值电流、开路电压和脉冲宽度对表面粗糙度的影响规律及优化区间。首次提出引入 BP 网络建立组合模型,该模型预测精度高,泛化能力强,为电火花加工工艺仿真提供了新的方法和途径。
1 低速单向走丝电火花线切割 TC4 表面形貌
本文采用基于白光干涉原理的法国 STIL 三维图 1 三维表面轮廓和功率频谱Fig. 1 The profile and power spectrum of 3D surface轮廓仪进行三维表面形貌分析和测量。图 1( a) 和图 1( b) 分别为 TC4 低速单向走丝电火花线切割和磨削加工的三维表面轮廓 X、Y 和功率频谱 Z. 低速单向走丝电火花线切割加工的表面是由无数无规则的放电凹坑和凸边叠加而成,磨削加工表面出现较规则的沟痕和隆起。两种加工的频率能量都集中分布在中心附近,其中低速单向走丝电火花线切割加工表面的能量分布近似圆形,表面没有明显的纹理为各向同性; 磨削加工表面则不同,具有明显的方向性为各向异性。二维表面粗糙度参数是在各向异性9501
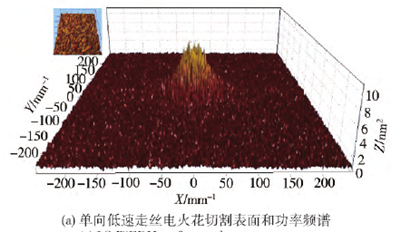
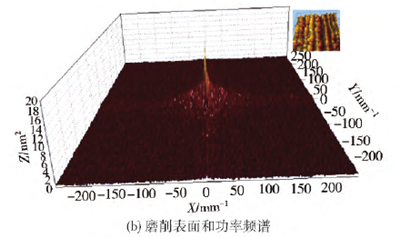
图 1 三维表面轮廓和功率频谱
表面基础上建立的,对于各向同性的电火花加工表面,二维表面粗糙度具有很大的局限性,因此采用三维表面粗糙度 Sa.
2 试验设计
试验采用阿奇夏米尔 CA20 低速单向走丝线切割机床,如图 2 所示。黄铜丝以一定的走丝速度通过切缝加工区,工作液为去离子水,冲液方式为全浸入下冲液; 工作液的导电率越大,电解反应越明显,因此选择较小的导电率; 为了减小电极丝的受迫振动,保证加工精度,上下导丝嘴距工件上下表面分别为0. 1 mm. 工件的厚度对加工区域工作液的进入和流出、蚀除产物的排除、消电离等有很大的影响: 如果厚度过大,工作液难进入放电区域,影响排屑和消电离,使加工稳定性变差; 如果厚度过小,会造成放电集中且容易断丝。结合机床设计的标准加工厚度范围,试验选取厚度为 10 mm ± 0. 01 mm 的钛合金试件,试验的具体加工条件见表 1. 选取峰值电流imax开路电压 U 和脉冲宽度 T 为加工工艺参数,每个参数的低、中、高三水平的因素代码分别记作 - 1、0、+ 1( 见表 2 ) ,基于 Design-Expert 设计的 Box-Be-hnken 试验和测量结果见表 3.
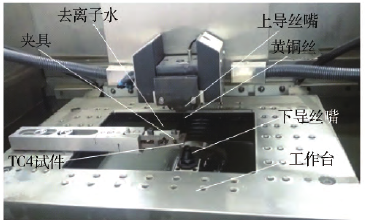
图 2 试验加工过程
表 1 试验加工条件
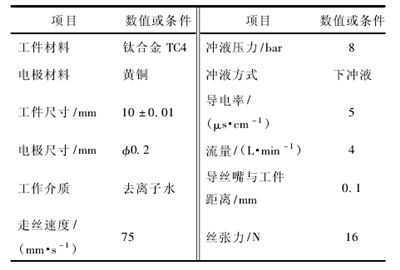
表 2 试验因素和水平
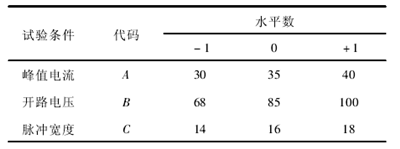
表 3 Box-Behnken 试验结果
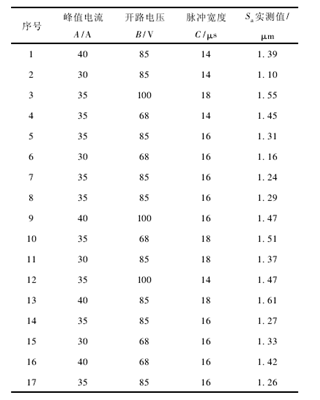
3. 实验结果与讨论
3. 1 模型的建立
Design-Expert 提供多种模型,通过表 4 中多种模型的方差分析和表 5 中 R2( 判定系数) 综合分析并根据尽量选择高阶模型的设计准则,可得出低速单向走丝电火花线切割 TC4 表面粗糙度 Sa的最优二次方响应模型,对确立的二次方模型进行置信度分析,如表 6 所示。由此可得各响应因子与表面粗糙度的数学模型:
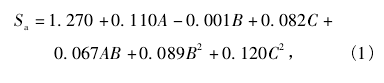
表 4 多种模型方差分析
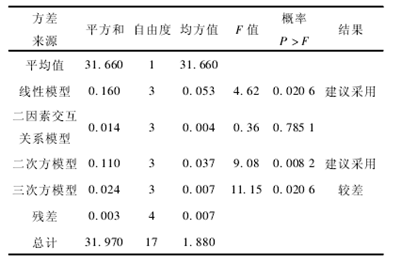
表5 R2综合分析
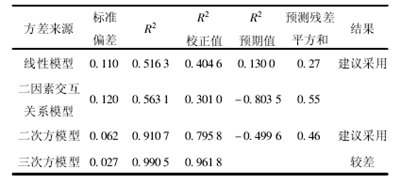
表 6 二次方模型置信度分析
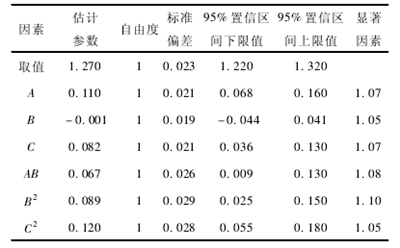

(1) 式为因素代码形式、( 2) 式为 实际 因素。由(1) 式的回归系数模型也可得出,峰值电流最大,脉冲宽度次之,开路电压为最小。
3. 2 响应曲面分析与优化
响应曲面法是采用多元二次回归方程拟合因素与响应值之间的函数关系来寻求最优工艺参数的一种统计方法[9]。取峰值电流、开路电压和脉冲宽度中任意一个因素为中水平值,利用( 2) 式绘制的三维表面粗糙度的响应曲面及等高线见图 3. 从图 3( a) 可看出: 在峰值电流 30 ~ 40 A 之间,表面粗糙度随着峰值电流的增大而增大; 当峰值电流为30 A 时,表面粗糙度先是随着开路电压的减小而减小,在达到最小值后,随着开路电压的减小而增大,图 3 各因素对表面粗糙度的响应曲面图Fig. 3 Effects of various factors on responsesurface of Sa这是由于开路电压减小,电源内阻不变,峰值电流会随之减小进而得到较小的表面粗糙度,但如果开路电压过小会减小放电间隙,不利于介质的消电离和1601
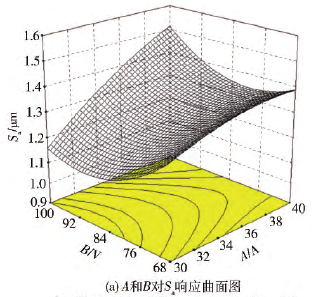
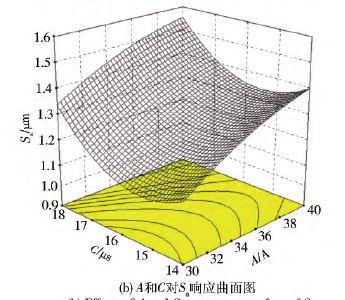
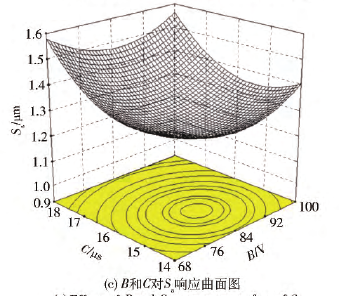
图 3 各因素对表面粗糙度的响应曲面图
蚀除产物的排除,加工过程不稳定,因此表面粗糙度变大; 表面粗糙度随着峰值电流和脉冲宽度的减小而减小,这是由于峰值电流和脉冲宽度的减小会使脉冲放电能量减小从而使表面粗糙度减小,见图 3( b) ; 开路电压和脉冲宽度的交互作用不显著,见图 3( c) 。通过响应曲面分析得出当峰值电流为30 ~ 32 A,脉冲宽度为 14. 5 ~ 16 μs,开路电压为80 ~ 88 V 时,可得到较好表面粗糙度 Sa为 1. 1 ~1. 2 μm. 对表面粗糙度影响的先后顺序为: 峰值电流、脉冲宽度和开路电压。与( 1) 式的回归模型得到的分析结果一致。图 4 TC4 试件表面形貌 SEM 图Fig. 4 SEM micrographs of LS-WEDMed TC4 surface图 4 为采用 JSM-7001F 扫描电子显微镜( SEM)观察的不同峰值电流下钛合金的表面形貌,和机械
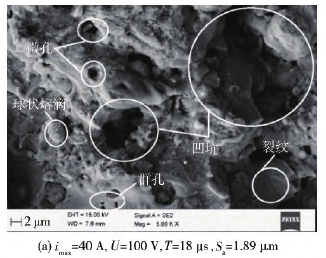
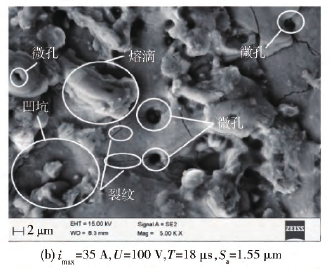
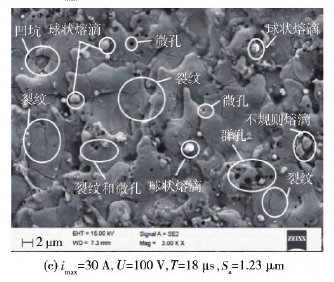
图 4 TC4 试件表面形貌 SEM 图
加工不同,其表面随机分布着放电凹坑、显微裂纹、球状熔滴、不规则状熔滴、微孔和群孔,这是由于每次脉冲放电后会使钛合金试件表面金属局部熔化和气化,部分金属被抛离工件表面,其余的则在熔潭中重新凝固形成一个有凸边的放电凹坑[10 - 11],完全熔化或气化的金属在重新凝固时由于本身张力作用形成球状的熔滴; 钛合金的导热系数小,部分金属还未熔化就被抛出,形成了不规则的熔滴也有一些在凹坑入口处形成翻边。从图 4( a) ~ 图 4( c) 可知: 随着放电凹坑的直径和深度减小,表面粗糙度也随之减小; 钛合金表面材料的瞬间熔化、冷却产生的热应力和拉应力超出其极限屈服强度导致了裂纹的产生,同时很多裂纹通常起始于工件表面的微孔边缘,这是由于微孔的出现会减小其周围的抗拉强度并改变其表面的曲率半径; 微孔的产生是由于溶解在熔融金属中的气体在金属凝固过程中没来得及逸出所致,由于去离子水的冷却速率大,所以形成的微孔尺寸较小。
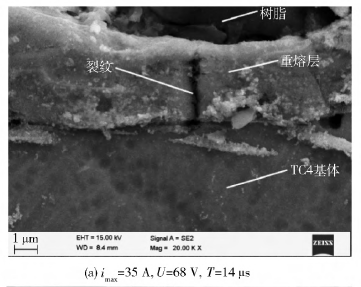
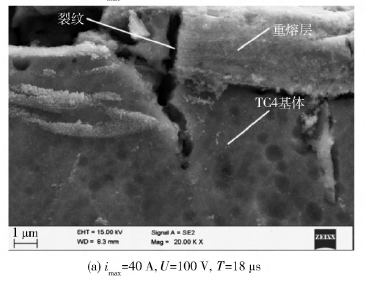
图 5 TC4 试件截面 SEM 图
图 5 为 TC4 试件经过抛光和腐蚀后得到的截面SEM 图,从中可以看出: 重熔层与基体连接不牢固,分
界面处存在微孔; 裂纹一般只出现在重熔层,但随着电参数的增大,裂纹会伸延至钛合金基体材料。3. 3 模型的预测与改进为了验证数学模型的预测能力,设定 6 组试验,其中前 3 组为参数范围内但又不同于表 3 的试验,后 3 组为表 3 中的第 15、16 和 17 组,如表 7 所示。计算值根据数学模型( 2) 式得到,实测数值是通过法国 STIL 三维轮廓仪测得,数值相对误差的计算如( 3) 式。从表 7 的相对误差可看出,该数学模型对样本内的预测精度比较高,但对样本外其预测精度并不高。为提高该数学模型的预测精度和泛化能力,本文引入 BP 神经网络建立组合模型,将数学模型建模简单、快速的特点和 BP 网络非线性处理能力强的特点进行人为的有机组合,相互补充。将 Sa数学模型的输出作为 BP 神经网络的输入,再用神经网络仿真,具体流程如图 6 所示。由 Sa数学模型计算得到的前 14 组预测数据为组合模型建模所用,见表 8.
表 7 验证试验电参数和分析结果
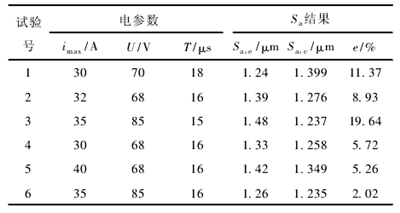
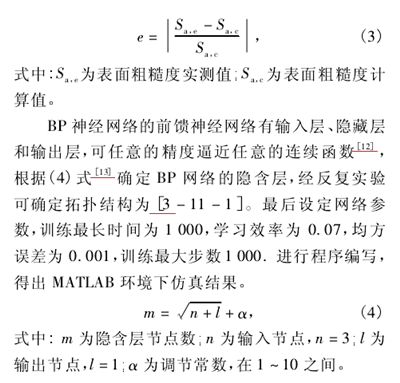
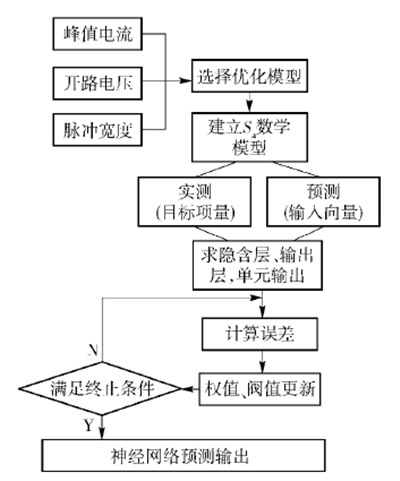
图 6 流程图
表 8 建模数据

从图 7 可知,当训练步长到 75 步时就达到精度要求 0. 001. 实测曲线和拟合曲线如图 8 所示,两曲线趋势相似,几乎重合,说明该模型的拟合精度很高。从图 9 可以看出,最大相对误差为 3% ,最小相对误差为 0. 001% ,相对均值误差为 0. 493% ,其中

3. 4 模型的试验验证
衡量一个模型的好坏除了高的拟合精度外,还应具备一定的泛化能力即能正确的映射出学习样本外的三维表面粗糙度值。因此,用组合模型对表 7的 6 组试验进行预测,对比分析了组合模型和数学模型的相对误差,其结果如表 9 所示,引入 BP 神经网络后的数学模型的样本内相对误差均值由4. 33% 降低到 3. 26% ,样本外相对误差均值由13. 31% 降低到 8. 50% ,模型的预测精度大大提高。图 10 为数学模型和组合模型的预测结果与实际数据柱形图。由此可见,该组合模型可以应用于电火花线切割加工领域,并为电火花工艺仿真提供了新的途径和方法。
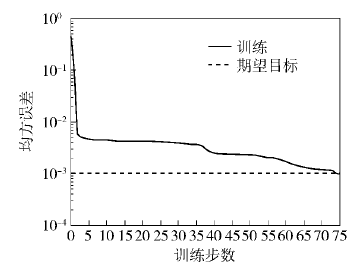
图 7 训练误差曲线
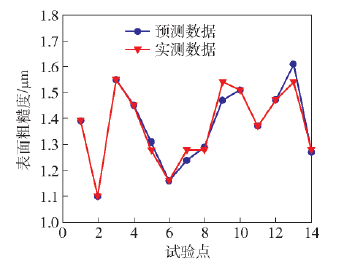
图 8 表面粗糙度实测值与拟合值曲线
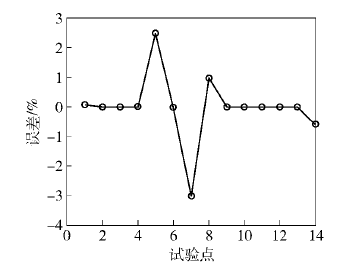
图 9 误差曲线图
4 结论
1) 采用 Design-Expert 设计 Box-Behnken 试验,通过多种模型方差分析、R2综合分析和二次方模型表 9 模型的相对误差表9
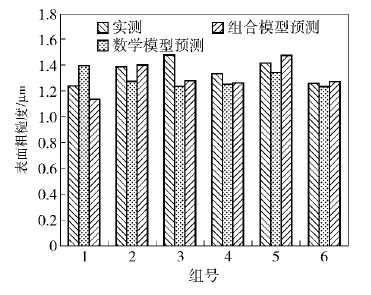
图 10 实测值与预测值对比柱形图
置信度分析确定了表面粗糙度 Sa的数学模型,通过响应曲面分析得出各参数对 Sa的影响规律及优化区间即当峰值电流为 30 ~ 32 A,脉冲宽度为 14. 5 ~16 μs,开路电压为 80 ~ 88 V 时,可得到较好表面粗糙度 Sa为 1. 1 ~ 1. 2 μm. 裂纹一般存在重熔层内,但当峰值电流为 40 A,开路电压为 100 V,脉冲宽度为 18 μs 时,裂纹延伸至 TC4 基体。2) 为了提高模型的预测精度和泛化能力,引入BP 神经网络建立组合模型,使样本外相对误差均值由 13. 31% 降低到 8. 50% ,样本内的相对误差均值由 4. 33% 降低到 3. 26% ,不仅实现电火花线切割表面粗糙度 Sa的有效评估,还为电火花工艺仿真提供了新的途径和方法。
投稿箱:
如果您有机床行业、企业相关新闻稿件发表,或进行资讯合作,欢迎联系本网编辑部, 邮箱:skjcsc@vip.sina.com
如果您有机床行业、企业相关新闻稿件发表,或进行资讯合作,欢迎联系本网编辑部, 邮箱:skjcsc@vip.sina.com
更多相关信息