TA2 表面电火花沉积 Zr / WC 复合涂层特性及界面行为研究
2017-3-22 来源:河南科技大学 作者:吴公一,张占领,孙凯伟,于华,邱然锋,石
摘要: 目的通过在 TA2 表面进行电火花沉积改变其表面性能。方法 采用电火花沉积技术,在基体TA2 表面制备 Zr / WC 复合涂层,然后分别用扫描电镜( SEM) 、能谱分析仪( EDX) 、X 射线应力分析仪、显微硬度计和摩擦磨损试验机分析涂层的微观组织、化学成分分布、残余应力、显微硬度分布以及涂层的耐磨性。结果 复合涂层连续、均匀,厚度约为 50 ~ 80 μm; 涂层表面不平整,存在很多小坑和粘连,涂层内部有少量气孔和裂纹; 复合涂层与基体的主要元素 Ti、Zr、W 之间发生相互扩散,并发生冶金反应; 经过电火花沉积后 TA2 表面存在较大的残余应力,通过改变工艺参数可有效控制残余应力; 复合涂层表面显微硬度值最高能达到 960. 5HV200g,约为基体的 4 倍; 经过电火花沉积 Zr/WC 复合涂层的试样磨损量远远小于 TA2 试样,εw= 4.1,沉积层的耐磨性比基体材料提高了3.1倍,经电火花沉积制备复合涂层后表面的耐磨性显著提高。结论 在 TA2 表面电火花沉积 Zr/WC 复合涂层可以改善其表面性能。
关键词: TA2; Zr; WC; 电火花沉积; 复合涂层; 界面行为
电火花沉积( ESD) 是利用高电流使旋转的焊材与被焊工件产生动态短路,通过在工件上堆积产生冶金结合点,对工件表面进行强化处理的一种表面工程技术。电极材料与工件金属接触放电产生高能量脉冲,电极熔化过渡到工件表面微熔的熔池中,从而形成合金化的表面强化层,改变了工件表面的耐磨性、耐蚀性、疲劳强度等,大大提升了工件的寿命[1]。与其它涂层技术相比,电火花沉积技术具有独特的优点,例如沉积工艺过程简单、基本不变形、沉积层结合强度高、修复工件的成本低、热输入量低、设备小巧便于携带、维修方便等[1],近年来越来越多地应用到航空航天、核工业、军事、医疗机械等各个领域。钛的比强度高而密度小,机械性、韧性和抗蚀性能好,在高温下仍具有较好的力学性能,对人体无任何辐射,因此被广泛应用于航空航天工业、核能发电、海洋科学、汽车工业和医学领域。但是钛的硬度较低、导热系数小、不易导热,很容易与对磨材料发生粘着磨损,导致零件的磨损失效[2—3]。为了改善其耐磨性,本文研究 TA2 表面电火花沉积 Zr/WC 复合涂层的微观特征及性能。
1.试验
采用 DZ-4000 Ⅱ型电火花堆焊机,输出电压为AC 220 V、单相 50 /60 Hz,输入功率为 4000 W,放电频率为 1400 Hz。电极夹紧在沉积枪上,处于中心位置绕电极轴线旋转,电极伸出长度在 20 mm 以内,电极材料为 Zr、WC 电极。沉积基体 TA2 样尺寸(长、宽、高) 为: 15 mm × 15 mm × 10 mm。先分别用 400#、600#、1000#砂纸打磨试样,再用丙酮和酒精清洗待沉积表面,然后按表 1 中的工艺进行沉积。
表 1 电火花沉积工艺
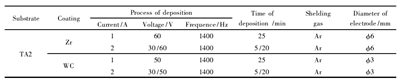
用日本 JSM-560LV 型扫描电镜观察涂层形貌; 用美国 EDX 型能谱分析仪分析复合涂层元素; 用日本理学 MSF-3M 新型 X 射线应力分析仪检测分析复合涂层的残余应力; 用 HV-1000 型显微硬度计检测涂层、过渡层、基体的显微硬度,加载 200 g,15 s; 在 MH-600 型摩擦磨损试验机上进行室温干摩擦磨损试验,对磨试样为直径 6 mm 的 YG8 硬质合金球,转速为1200 r / min,载荷为 10 N,时间为 30 min,再用精确到0. 1 mg 的 AEL-200 型电子分析天平称量试样。
2.结果分析
2.1 涂层形貌分析
2.1.1 表面形貌
图 1 为涂层的表面 SEM 形貌。涂层表面有很多凹坑( A 点) ,是由沉积脉冲产生的强放电力使合金化的熔滴飞溅形成,电火花沉积时产生很大的放电力,使加工表面产生凹坑轮廓。同时在涂层表面还存在粘连现象( B 点) ,这是由于在火花放电过程中电极和基体材料同时熔化,熔化的电极材料向基体过渡,熔化的基体材料也向电极过渡,在电极与基体不断分离与接触的过程中两者熔为一体,随着放电次数的增加,粘连的形貌遍布涂层的表面。强化时间较短时,热输入量低,电极与基体粘连现象不明显,粘连层比较薄; 随着强化时间增加,热输入量的增加,粘连现象变得严重,会形成具有一定厚度的粘连层[4—5]。
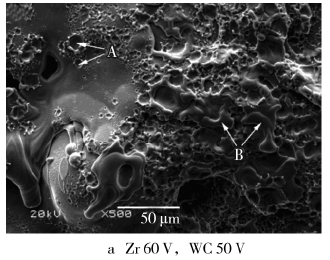
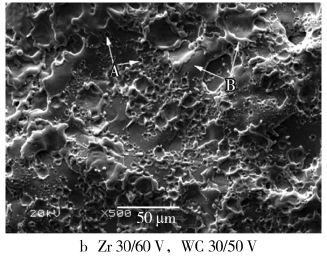
图 1 涂层表面形貌
2.1.2 断面形貌
图 2 为涂层的断面 SEM 形貌。涂层厚度约 50 ~80 μm。涂层与基体相互熔合,二者之间存在一个熔渗扩散区,有利于提高涂层与基体的结合强度。涂层内有气孔( A 点) 与裂纹( B 点) 。产生气孔的原因可能是受电极和基体表面不洁净和周围环境的影响,气孔使强化层变得疏松。产生裂纹的原因,一方面是受电极材料和基体材料成分以及强化环境的影响,使强化层中存在夹杂物和气孔,降低了强化层的机械强度; 另一方面是由于沉积过程中产生的热应力导致,沉积过程中熔化的金属材料遇冷急剧冷却而凝固,沉积层内存在着热应力作用,在无数次放电作用下,沉积层反复受到热冲击,最终产生显微裂纹[6—7]。
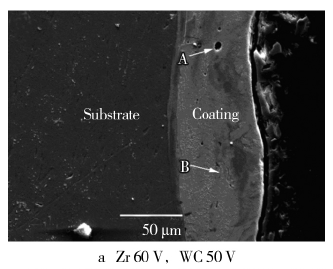
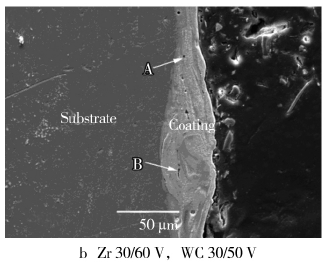
图 2 涂层断面形貌
2.2 元素分析
图 3 为涂层的元素分布,可以看出,涂层与基体结合面处有一个很窄的成分熔渗扩散区,基体与涂层之间发生了元素的相互扩散,基体中的 Ti 由基体向涂层扩散,涂层中的 Zr、W、C 由涂层向基体扩散。但由于沉积过程中高温时间短,元素扩散不充分。C 和Zr 的含量在沉积层和靠近沉积层的基体中含量较均匀,说明 C 和 Zr 容易扩散。Ti 元素在基体中含量较多,由基体到涂层 Ti 元素含量呈下降趋势[8—9]。从基体到涂层,W 元素含量逐渐增加,而在涂层中某些部位 W 元素含量较多,可能是沉积过程中硬质合金WC 随着电极的旋转作用直接进入了涂层内部所致,对于 W 元素在涂层内部部分区域大量聚集的原因有待做进一步的研究。涂层与基体之间发生了元素的扩散,基体 TA2 中的 Ti 元素进入复合涂层内部,电极材料中的 Zr、W 元素也进入涂层内部,说明电火花沉积是电极与基体材料的相互熔渗过程[10]。
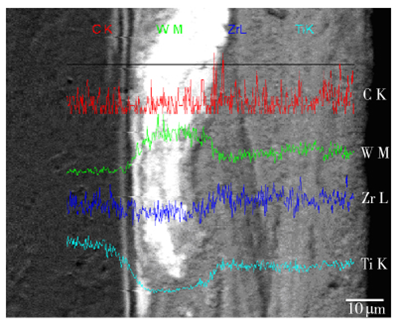
图 3 涂层到基体元素分布
2. 3 试样残余应力分析
由表 2 可知,电火花沉积后的试样表面有较大的残余应力,这种残余应力的产生是一个非常复杂的过程,主要有两方面的原因: 一方面,在电火花沉积过程中,熔化的工件材料在空气中遇冷而凝固,工件表面温度分布不均匀,存在温度梯度,形成了热应力,热应力的存在使涂层表面有产生残余拉应力的趋势; 另一方面,在工件材料急热、急冷过程中,工件材料的组织发生相变会产生相变应力,这会松弛电火花沉积过程中产生的残余拉应力,并可能向压应力产生逆转[11]。
电火花沉积是一个多次重复的过程,对于某一个加工点来说,它的应力情况是多次放电作用的最终结果,这取决于哪个影响因素占主导地位[12]。若热应力占主导地位,则产生残余拉应力,若相变应力占主导地位,则产生残余压应力。而通过改变电火花沉积规范可以控制残余应力的性质,如试样 1 表现为残余拉应力,试样 2 表现为残余压应力。
表 2 涂层残余应力
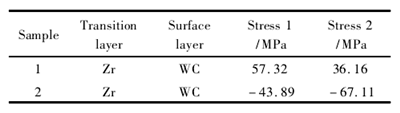
2.4 涂层的耐磨性能
图 4 是同一个涂层断面处不同位置的 3 条显微硬度分布曲线。可以看出,3 条线走势大致相同,涂层表面的显微硬度值远高于基体材料 TA2,最高处可达 965HV200 g; 随着与涂层表面距离的增加,即由涂层到过渡层,显微硬度值逐渐下降,而基体的显微硬度约为 220HV200 g; 涂层表面的显微硬度约是基体的 4 倍。沉积层之所以有这么高的显微硬度主要是由于经过电火花沉积后表层组织得到了细化,又引入了较高的残余压应力,同时由于沉积层具有高硬度的碳化物 W2C 所致[13]。

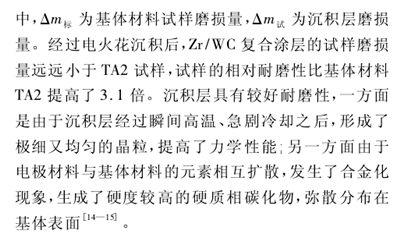
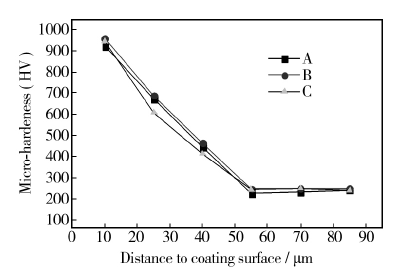
图 4 距涂层表面的显微硬度分布曲线
表 3 磨损失重结果
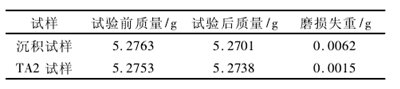
3.结论
1) 利用电火花沉积技术,分别以 Zr、WC 棒为电极,在 TA2 基体表面电火花沉积制备出了连续、均匀的 Zr/WC 复合涂层,复合涂层厚度约为 50 ~ 80 μm,涂层表面较平整,存在较多凹坑和粘连,涂层断面有少量气孔和裂纹。
2) Zr / WC 复合涂层与基体间各主要元素发生了相互扩散,涂层中的 Zr、W 主要向基体扩散,基体中的 Ti 元素向复合涂层扩散,过渡层中存在 Zr、W 与 Ti的相互扩散,部分区域硬质合金 WC 大量进入涂层内部。
3) 电火花沉积表面的残余应力随加工工艺的不同,可能产生残余拉应力或残余压应力,改变工艺参数可控制残余应力。4) Zr / WC 复合涂层的表面显微硬度值最高达965HV200 g,约为基体的 4 倍,沉积层的相对耐磨性比基体增加 3.1 倍,基体表面性能已经发生改变。
投稿箱:
如果您有机床行业、企业相关新闻稿件发表,或进行资讯合作,欢迎联系本网编辑部, 邮箱:skjcsc@vip.sina.com
如果您有机床行业、企业相关新闻稿件发表,或进行资讯合作,欢迎联系本网编辑部, 邮箱:skjcsc@vip.sina.com
更多相关信息