摘要:连杆裂解技术中,连杆大头孔应力槽深度的一致性对裂解质量而言至关重要。通过研究设计出一种用于电火花线切割机床加工连杆的机构,采用电压电流检测电路判断电极丝初次碰到工件的位置,并结合单片机计数功能保证连杆应力槽深度的一致性,且槽深不受连杆毛坯内孔尺寸、电极丝与连杆初始位置变化的影响。此外,添加快速辅助进给功能,加快空行程运行速度。实验证明该方法提高了连杆裂解加工的质量和效率。
裂解技术在经济性和质量方面的优势显著,目前在连杆加工中已广泛应用。在整个裂解工艺中,连杆大头孔裂解槽的尺寸精度对裂解质量有着重要影响[1]。在连杆裂解加工技术中,为了利于裂纹开启、迅速扩展并发生脆断性断裂,要求初始裂解槽的应力集中系数要大[2]。在一定程度上,裂纹深度与断裂强度成反比,当断裂纹大于临界深度时裂纹失
稳; 但由于裂解后需进行连杆大头孔的精加工,故断裂槽深度不能太深,否则在最后精镗大头孔时会留下残痕,因此槽深一般小于0.6 mm。此外,大头孔中心两侧的裂解槽深应严格一致, 保证同时裂开,以获得两侧一致的高质量断裂面。
裂解槽的加工方法有拉削加工、激光加工及电火花线切割加工等。拉削加工时,拉刀会随着时间而磨损,使槽宽变大,影响裂断效果,故该方法已逐渐被淘汰。激光加工的优点是高效、质量好,但加工设备价格昂贵,使用维护成本高;在某些情况下,切口处会残留高硬度的再凝固硬质点,影响后续精镗加工。电火花线切割加工弥补了上述缺陷与不足,在裂解槽加工中脱颖而出。
然而,现有的连杆裂断应力槽线切割机床缺少快进功能,导致辅助进给工时较长,加工效率低;此外,当连杆大头孔尺寸存在误差时,每次切出来的槽深不同,导致后续加工时废品频出,必须进行二次加工或直接报废工件。为了解决这些问题,本文设计了一种具有恒切深控制功能的电火花线切割机床控制系统,且兼具快速辅助进给功能,可保证槽深的一致性,提高加工效率。
1 、控制系统的组成
电火花线切割机床控制系统主要由脉冲电源、控制单元、检测电路及运动单元组成。系统各部分组成见图1。其中,脉冲电源为加工工件和电极丝提供高频能量;间隙电压检测电路是对工件和电极丝的加工间隙电压取值,判断间隙状态,并将间隙状态反馈到控制单元[3]。控制单元采用dsPIC 单片机控制电极丝向工件的快速进给,并接收来自于间隙电压检测电路的信号,对其进行分析,进而控制电机转动。
图1 控制系统的组成
2 、运动控制基本策略分析
往复走丝电火花线切割加工时,交替出现的空载、短路和正常火花放电等3 种加工状态使电极丝与工件的间隙状态随之交替。其中,短路状态对加工不利,可能导致流过电极丝的电流超过其承受范围而被熔断,所以在控制方案中需对加工状态实时检测,并对加工中出现的短路现象及时进行处理。控制系统的基本策略见图2。为了便于连杆的放置和拆卸,电极丝的初始位置应与连杆留有一定的距离。在辅助时间里,控制器时刻检测加工间隙状态。当开始执行加工指令时,电极丝快速从位置1移动到位置2;在位置2 到位置3 之间,电极丝以工进速度进给(此时电极丝未和连杆接触);随着进给的继续,当电极丝接触到连杆时(位置4),间隙检测电路会给单片机发出一个加工开始的信号,单片机识别其为首次火花放电, 单片机控制器开始计数,直至发出期望的脉冲数, 实现期望的槽深加工;然后快速返回初始位置1。在切割过程中,需对电火花线切割加工中的状态信号进行检测,如因短路原因执行了电极丝的回退操作,则需对回退的脉冲数进行补偿。
3 、检测电路的设计
控制系统中的电压取样电路能检测电极丝的初始加工状态和加工短路状态[4]。图3 是间隙全值平均电压检测电路。其中,R1、C1、C2构成低通滤波电路。滤波电路近似于一个惯性环节,其滞后特性有助于加工的稳定。这是因为加工中不断随机地出现空载、短路、火花放电等状态,仅凭单个脉冲或某个状态不能确定加工是否正常,只有在连续观察一系列状态后,才能做出准确的判断。此外,R2、R3为分压电阻。二极管VD1能在脉冲间隔期间阻止滤波电容向前级电路放电。
图2 电极丝运动轨迹 图3 电压取样电路 图3 电压取样电路
短路状态的检测电路见图4。U1为电压比较器,在电极丝与工件之间采集到的电压U 从U1的正输入端进入,设定值与U1的负输入端相连;当采样电路采得的间隙平均电压值U 比设定值Vcc·R6R5 +R6小时,则认为是短路状态。此时,比较器的1 脚输出低电平,光耦U2的发光二极管有电流流过,光敏三极管导通,端口shortcut 输出低电平,给单片机短路外部中断端口发送一个低电平信号。单片机接收到中断信号后,进入短路中断程序,控制运动单元中的步进电机回退相应的步数。
图4 短路状态信号采样电路
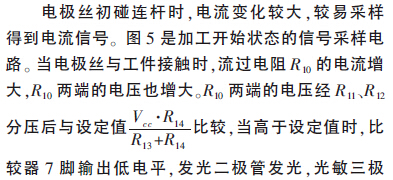
管导通,端口Start 给单片机相应的中断发送一个低电平信号。单片机接收到开始加工的外部中断信号后,内部计数器开始计数,直到与已设定的槽深值相等时,则认为加工到预定深度,单片机停止计数,并快速返回。
图5 加工开始状态的信号采样电路
4 、软件程序的设计
本设计选用步进电机,并利用步进电机驱动器驱动电机工作。因为用于驱动步进电机的脉冲信号只与频率有关,与占空比无关,因此产生驱动步进电机的脉冲只需一个定时计数器。采用dsPIC30F 单片机,让定时计数器工作在定时模式,每次进入计数溢出中断时, 相应的脉冲输出端口电平翻转,发出脉冲,并根据所采集到的间隙电压状态确定该如
何记录输出脉冲。具体实施过程如下:根据工厂的实践,应力槽深度为0.4~0.6 mm。在单片机中设定计数器的值N,使其切割深度为0.6 mm。刚开始单片机控制电极丝快速向工件进给, 并未接触到工件,单片机记录脉冲数在变量A 中;当电极丝与连杆开始接触,记录工进脉冲数在变量B 中,直到计数值B 与设定值N 相等,单片机停止计数。步进电机开始回退,回退的步数为(A+B);进而实现恒切深。当加工过程中发生短路时,电极丝回退一个固定的距离,所对应的脉冲数为C;在步进电机回退C步的同时,变量B 减去C。单片机程序流程见图6。
图6 运动控制程序框图
5 、实验
利用电火花线切割机床对连杆做切割实验,以此验证恒切深控制系统。实验选用加工电源电压为90 V,电源频率为10 kHz,占空比为0.3。设定深度参数为8000,该值为控制器的控制脉冲数。理论切割深度的计算表达式为:
电火花线切割加工的槽深尺寸见表1。定义槽深尺寸差为实际槽深与理论槽深的尺寸差值,槽间尺寸差为槽与槽之间的尺寸差值。从表1 可看出,切割出的槽深误差较小,证明所设计的具有恒切深控制功能的电火花线切割机床控制系统是可行的。
表1 切割槽深数据 μm
6 、结语
本文针对连杆裂解槽加工提出的特殊要求,应用disPIC 单片机开发了一套专用电火花线切割控制系统,具有快速进给、回退功能,并利用间隙电压检测电路对加工状态进行判别,检测到的变化信号发送到单片机,由单片机对其进行识别处理,发送相应的脉冲信号给步进电机驱动器使电机动作,实现恒切深功能。实验证明本系统稳定可靠,达到预期设计要求。
如果您有机床行业、企业相关新闻稿件发表,或进行资讯合作,欢迎联系本网编辑部, 邮箱:skjcsc@vip.sina.com