螺旋电极电火花小孔加工排屑仿真和试验
2015-11-13 来源:数控机床市场网 作者:曹一龙,曹明让,郝岳峰,袁玉成
摘要: 在电火花小孔加工中,排屑困难一直是困扰加工速度的一个重要问题。通过对工具电极改进,用螺旋电极进行电火花小孔加工,使其改变加工过程中间隙流场的流动状态以及电蚀产物的受力,达到增强小孔加工过程中的排屑能力,进而提高加工速度的目的。利用Gambit 软件建立仿真模型,应用Fluent 对小孔加工过程中排屑进行仿真,对其压力场和速度场进行分析,研究其加工机理。在D703F 高速电火花小孔加工机床上进行了试验研究,结果表明螺旋电极电火花小孔加工速度最大提高了20%。
自从1943 年前苏联学者拉扎连柯( Lazarenko) 夫妇发现放电蚀除现象后,电火花加工在之后的70 多年里得到了飞速的发展,它已广泛应用于生产实践,据相关资料介绍,目前电火花加工机床已占世界机床市场的6%。电火花小孔加工是电火花加工的重要组成部分,据统计带孔零件大约占据了零件总数的50% ~ 80%,电火花小孔加工作为目前加工小孔的一种重要手段,因其可加工任何导电材料而不受工件材料硬度限制,非接触式加工,对工具的刚度和强度要求较低,被加工件表面应力变化小等优点,在实际工业中被广泛应用。在电火花小孔加工中,加工速度一直是其研究和应用中存在的主要问题,如何提高加工速度是我们不断探讨的命题。影响电火花小孔加工速度的因素很多,如加工电参数、工作液及其它加工环境等。排屑能力是影响电火花小孔加工速度的一个重要因素,众所周知,电火花加工的电蚀产物如果不能及时排出放电间隙之外,将会导致电极短路和非正常放电,最终使加工速度下降,甚至不能加工。在电火花小孔加工中,为了改善排屑条件,提高加工效率,研究人员做了各种尝试,如采用超声电火花复合加工,通过超声空化作用,提高小孔加工的排屑能力; 采用圆柱电极削边的方法,以增大排屑通道,达到改善排屑条件的目的; 还有从工作液入手,利用特殊工作液,以减小电蚀颗粒的凝聚和沉降,进而增强其排出性等。上海交通大学许加利等人用Fluent分别对圆柱电极和螺旋电极的底部和侧面流场进行仿真,得到了圆柱电极和螺旋电极在不同转速下的加工速度对比,讨论了电极转速对加工速度的影响,得出螺旋电极可以提高电火花小孔加工的加工速度的结论。本文研究了圆柱电极和螺旋电极间隙工作液流场流动状态的区别,利用螺旋电极的方法,意在增大排屑通道的同时,使加工排出物在其排出过程中流动方式改变,进而提高其排出性和提高加工速度。
1 加工间隙流场仿真
1.1 几何模型
结合试验研究中的加工参数,仿真中工具电极外径为3 mm 的黄铜空心圆柱电极和螺旋电极,加工深度为100mm,取放电间隙为100 μm,设工作液为纯水,温度为25℃时,其动力黏度μ = 8. 94 × 10 - 4 Pa·s,运动粘度ν = 8. 97 ×10 - 7 m2 /s。普通圆柱电极和螺旋电极的几何模型,如图1所示。
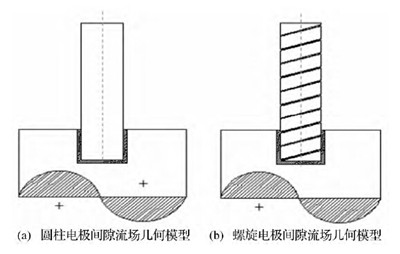
图一:几何模型
利用gambit 有限元软件对圆柱状电极和螺旋电极建立模型并进行网格划分。如图2 所示。
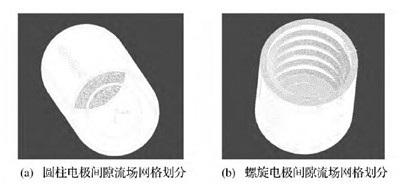
图二:网格划分
1. 2 理论模型
在圆柱电极内,通过雷诺数的计算并与临界雷诺数对比,确认侧向间隙内流体运动状态,雷诺数Re 表示为:Re = vdρμ = vdν( 1)式中: v 为流速,d 为管径、ρ 为动力黏度,ν 为运动粘度。通过计算可知圆柱电极侧向间隙内水流的雷诺数小于2 000,由此可以确定,侧向间隙内工作液的运动状态为层流。在螺旋电极的间隙流场内,螺纹区域边壁变化的局部阻碍为突变,如图3 所示。
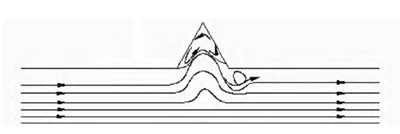
图三:螺纹处流体流动示意图
当流体通过突变的局部阻碍时,由于惯性力处于支配地位,流动不能像边壁那样突然转折,于是在边壁突变的地方,出现主流与边壁脱离的现象,主流与边壁之间形成旋涡区,旋涡区内的流体并不是固定不变的,形成的大尺度旋涡,会不断地被主流带走,补充进去的流体,又会出现新的旋涡,如此周而复始。挤压的力,使得电蚀产物在水流压力和螺纹面反作用力的共同作用下达到水平分力相对平衡的位置。由于螺纹区流体的旋涡作用导致局部能量损失,能量损耗可由方程
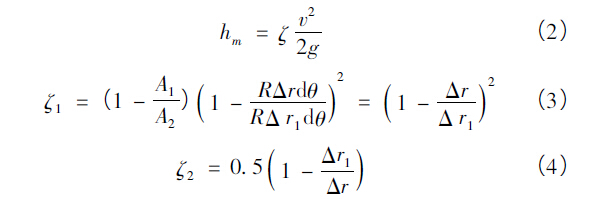
算得:式中: hm为局部能量损失,ζ1和ζ2为管径变化的局部阻力系数,v 为流速,A1为突变前流体截面积,A2为突变后流体截面积,Δr1为螺纹最深位置与被加工件边壁距离,Δr 为非螺纹区域两边壁间隙距离,R 为工具电极半径,由于放电间隙相对于工具电极半径小得多,所以取近似值R≈R + Δr≈R + Δr1。能量损失使得螺纹区及其周边流体流速降低,作用力减小,从而导致电蚀产物、尤其是团聚结构进入螺纹后横向压力减少,使其在螺纹槽内堆积,并在延螺旋线方向分力的作用下顺着螺纹向上移动,这使得放电间隙内沉积物堵塞现象得到缓解,从而减少了排屑不畅而导致的不断抬刀现象,提高加工速度。
1. 3 仿真结果及分析
( 1) 圆柱电极和螺旋电极压力场仿真结果如图4 所示电火花小孔加工底部电蚀产物堆积使其在此处团聚,团聚结构会导致在排出过程中通道堵塞。
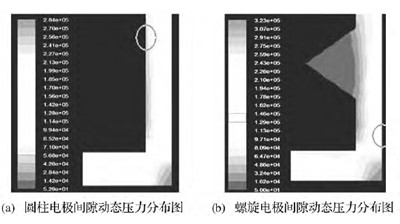
图四:动态压力分布图
从图4 可以看出,圆柱电极和螺旋电极的间隙流场内都会有一定的压力变化,相对于圆柱电极,螺旋电极底部边角压差明显变大。而压差作用于电蚀产物,促使电蚀产物不断向低压区移动,使螺旋电极底部电蚀产物堆积现象得到改善。螺旋电极侧向间隙区域内,螺纹槽及螺纹槽周边范围形成低压区域,使的电蚀产物趋向于螺纹槽流动,在此处形成旋涡区,电蚀产物在压力作用下向螺纹槽内流动,并沿螺线方向向上移动。
( 2) 圆柱电极和螺旋电极速度场仿真结果如图5 所示由图5 可以明显看出圆柱电极间隙流场为层流,而螺旋电极螺纹槽周边间隙流场为紊流。首先螺旋电极在底部边角处速度更大,减少了电蚀产物在此处的堆积。而在侧向间隙区域内,在螺纹槽内形成明显的旋涡区,使得电蚀产物进入螺纹槽,并在螺纹上下面的压力作用下沿螺线方向移动。放电间隙内电蚀产物,尤其是其中的团聚结构减少,进而减少了侧向流场内的堵塞现象,电蚀产物的排出更通畅。
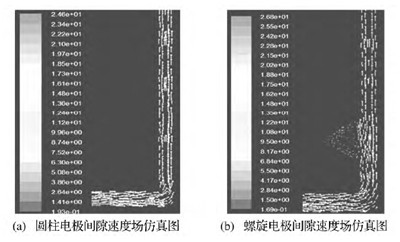
图五:速度场仿真图
2 实验结果及分析
该实验在D703F 高速电火花小孔加工机床上进行,使用正极性加工,工作电压为25 V,脉冲宽度为80 μm,被加工件为厚度10 mm 的不锈钢,工具电分别为Φ3 mm,Φ2. 5 mm和Φ2 mm 的中空黄铜圆柱电极和螺旋电极,螺旋电极的螺纹宽度为0. 2 mm,深度为0. 2 mm,螺距2 mm,图6 为实验用圆柱电极和螺旋电极,小孔加工工作示意图如图7 所示,在其它条件不变的情况下,改变加工电流得到加工速度随电流变化如图8 所示。
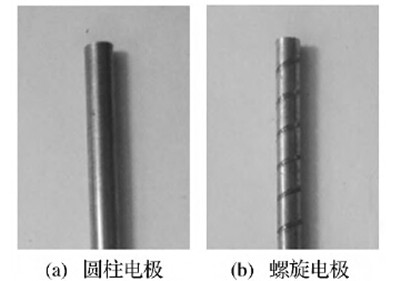
图六:试验用圆柱电极与螺旋电极
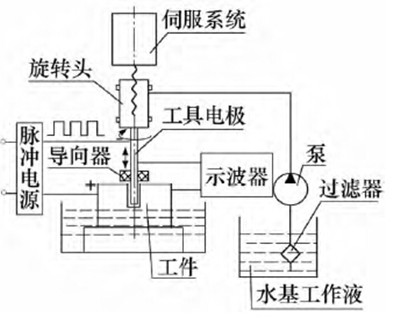
图七:电火花小孔加工工作示意图
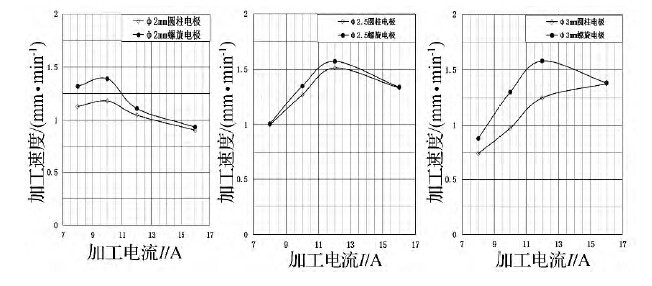
图八:不同直径螺旋电极与圆柱电极速度对比
图8 表明,无论是圆柱电极还是螺旋电极,随着加工电流不断增大,加工速度也增大,但速度增大到一定程度后,随着电流增加加工速度反而下降,其原因是随着电蚀量的增大排屑能力达到了饱和,电蚀产物不能及时排出,从而导致电火花加工速度降低。横向比较Φ3 mm,Φ2. 5 mm 和Φ2 mm三种直径电极的试验结果可知,随着电极直径的减小,排屑能力不断减弱,最大加工速度所处加工电流不断变小。图8还表明,无论Φ3 mm,Φ2. 5 mm 和Φ2 mm 直径的电极,螺旋电极具有更强的排屑能力,所能达到的最大加工速度更大;并且在达到最大加工速度前,加工速度随着电流的增大而提高的更快。这是由于螺旋电极改变了电火花小孔加工间隙流场内流体的流动状态,使得圆柱电极间隙流场的层流变为螺旋电极的紊流。螺纹槽内形成旋涡区,使得电蚀产物进入螺纹槽,而由于流体能量减少,电蚀产物堆积在螺纹槽内,并在螺纹上下两壁面压力下沿螺线方向向上排出,减少了放电间隙内加工废液堵塞的可能性,提高了其排屑速度和最大排屑能力。而当螺旋电极排屑能力达到饱和后,螺纹槽内不能再容纳更多的电蚀产物,而紊流运动使得间隙内流体能量损耗比圆柱电极大,这导致了流体对电蚀产物的冲击力减小,使得间隙内电蚀产物浓度更容易变大,所以在加工速度达到最大后,加工速度随着脉冲电流的增大而降低的更快。
3 结论
( 1) 通过对电火花小孔加工的fluent 仿真和实验研究表明,使用螺旋电极改变了电火花小孔加工间隙流场内流体的流动状态,使得圆柱电极间隙流场的层流变为螺纹电极的紊流。螺纹槽内形成旋涡区,使得电蚀产物进入螺纹槽,流体能量减少,电蚀产物堆积在螺纹槽内,并在螺纹上下两壁面压力下沿螺线方向向上排出,减少了放电间隙内加工废液堵塞的可能,进而提高加工速度,在取得一定电参数的情况下,加工速度最大可提高20%。
( 2) 由于在实际加工过程中,流体在螺纹槽内能量损失过于严重,导致其对电蚀产物的压力减弱,使得电蚀产物在螺纹槽内移动速度过低,并且螺纹槽内部空间较小,不足以容纳过多的电蚀产物,所以导致螺旋电极对最大加工速度的提高较少,且容易达到最大加工速度。所以做出下列预测:可以通过增大螺距来提高电蚀产物沿螺线方向的受力,应用双线螺纹或多线螺纹以增加螺纹槽密度,提高螺纹槽对间隙流场的影响,增加螺纹宽度以提高螺纹内电蚀产物容量,进而提高加工速度。
投稿箱:
如果您有机床行业、企业相关新闻稿件发表,或进行资讯合作,欢迎联系本网编辑部, 邮箱:skjcsc@vip.sina.com
如果您有机床行业、企业相关新闻稿件发表,或进行资讯合作,欢迎联系本网编辑部, 邮箱:skjcsc@vip.sina.com
更多相关信息