基于 FANUC 数控系统的智能制造单元设计
2022-4-26 来源: 湖南三一工业职业技术学院 作者:陆 雄
摘要 : 提出了将工业机器人与 FANUC 系统数控机床相结合,构成基本的智能制造单元的设想。主要分析和研究工业机器人自动上、下料的工作过程,运用 FANUC 数控系统的宏程序完成上、下料程序的编制,提升数控机床的智能化水平。
关键词 :FANUC 数控系统 ; 机器人 ; 智能制造 ; 程序设计
1.序言
本文选用三一汽车起重机械有限公司现有的一台 NBP-1000A 友嘉立式加工中心和一台 ABB工业机器人,构造成一个基本的智能制造单元,运用工业机器人完成工件的上料、下料及搬运工作。所有控制流程,在 FANUC 数控系统通过编程来实现。
2.智能制造单元的基本组成
NBP-1000A 型加工中心是一台三轴控制数控机床,采用 FANUC 0iMD 数控系统,配备机械手自动换刀装置,盘式刀库容量为 22 把。在加工中心工作台上配置气动精密平口钳,用于工件的装夹。选用型号为 IRB2400 的 ABB 工业机器人,其承重能力 10kg。机器人侧配备有工件装夹手爪,具有夹紧、松开、有无料检测功能。料架上设有毛坯位和成品位两个仓位,每个仓位设有传感器和状态指示灯,传感器用于检测该位置是否有工件,状态指示灯分别用不同的颜色指示工作状态。设备平面布置如图 1 所示。
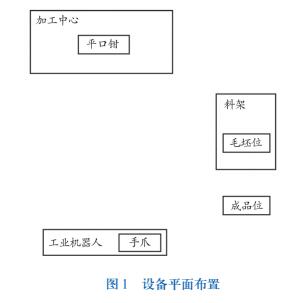
3.程序设计
整个加工过程是由数控系统通过编写程序来实现的。自动上、下料的全过程是由加工中心与机器人之间通过上、下料宏程序相互配合来完成的。上、下料动作,毛坯及成品的搬运都由机器人完成。平口钳、机床门及机器人手爪动作都是由数控系统 PMC 程序控制。平口钳的装料位置由加工中心 X、Y 轴,通过数控系统与数控机床PMC 的 G 代码实现信息交换。
3.1 工作流程
程序设计之前,首先要将各部件的工作流程弄清楚,才能设计出完好的程序。上料是由工业机器人从料架的毛坯位置搬运毛坯到数控机床中,加工前将毛坯装到平口钳中。加工完成后,将成品从平口钳上卸下,送至料架成品位置。上料工作流程如图 2 所示。
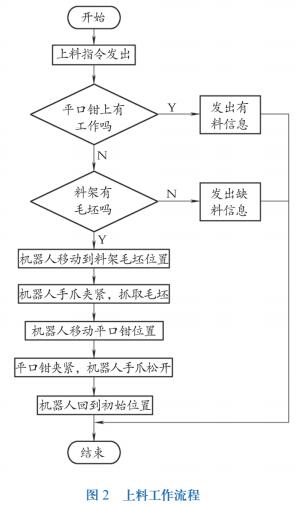
下料是由工业机器人将加工好的成品从数控机床上搬运到料架成品位置,下料工作流程如图3 所示。
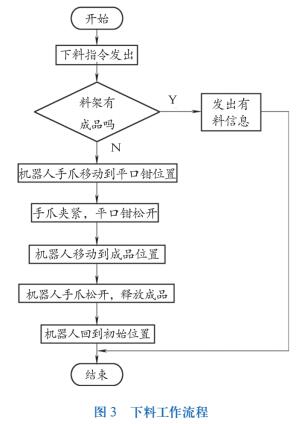
3.2 上、下料宏程序的编写
(1)M 代码定义上、下料各环节的控制采用辅助功能 M 指令来实现,M50、M51 通过宏程序来完成,M52~M57 各指令需要在数控系统中编写相应的 PMC 程序,M 指令设置见表 1。
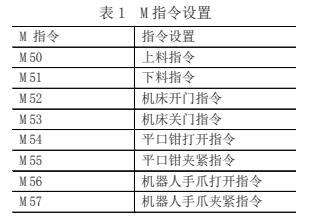
(2)接口信号变量定义上、下料宏程序采用了接口信号变量,定义见表 2。接口输入信号变量在宏程序中 “读取” 系统输入信号的状态,从而在程序中直接获得相应的检测信号,#1008~#1010 为接口输入信号变量。接口输出信号变量在宏程序中 “改变” 系统输出信号状 态,#1108~#1109 为 报 警 输 出 信 号 变 量,#1110~#1113 输出信号变量控制数控机床的执行元件向机器人发出工作指令。
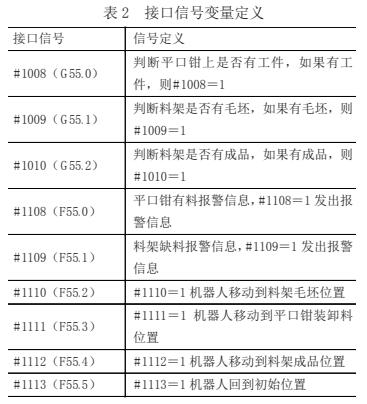
(3)系统参数设定 要通过 M50、M51 指令在数控程序中调用宏程序,必须对相关参数进行设定。设定 P1195=1,使用 M 代码调用宏程序 ;设定 P6075=50,使用 M50 调用 O9005 宏程序 ; 设定 P6076=51,使用 M51 调用 O9006 宏程序。上料宏程序设计如下。
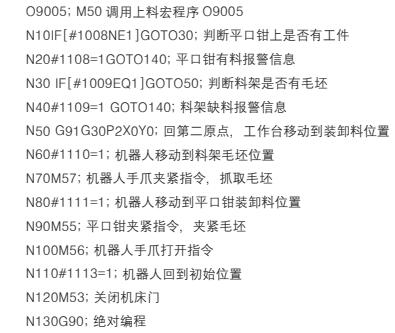
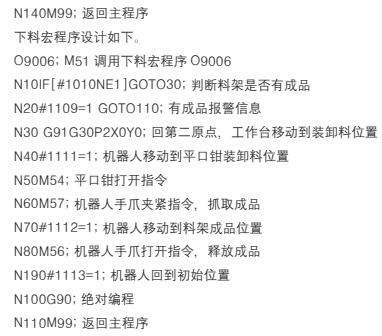
4. 结束语
通过对智能制造单元工业机器人自动上、下料工作过程的分析和研究,运用 FANUC 数控系统编写上、下料程序,不仅提升了数控机床的智能化水平,满足了生产车间智能化制造的需求,而且减少了工人的劳动强度,提高了生产效率。通过进一步研究,可以考虑将一台工业机器人与多台数控机床配合,实现自动上、下料功能,提高工业机器人的利用率,更大范围地提升工厂的智能化生产水平。
投稿箱:
如果您有机床行业、企业相关新闻稿件发表,或进行资讯合作,欢迎联系本网编辑部, 邮箱:skjcsc@vip.sina.com
如果您有机床行业、企业相关新闻稿件发表,或进行资讯合作,欢迎联系本网编辑部, 邮箱:skjcsc@vip.sina.com
更多相关信息