考虑切削力干扰的多轴联动伺服系统仿真分析
2018-10-10 来源:天津大学机械工程学院 作者:张全彪 王国锋 宋庆月 吴丽蕊 杨星焕
摘要:基于机床伺服系统性能分析需求,建立了 X 轴、Y 轴的伺服控制系统模型。在此模型的基础上,将四象限插补算法引入到控制系统模型的仿真中,研究了多轴联动情况下 PID 参数对圆弧插补指令偏差的影响。考虑加工过程中切削力因素的影响,将加工过程中采集的实际力信号添加到多轴联动仿真模型中。仿真结果表明:实际的切削力因素对控制系统特性的影响显著,在 PID 参数优化时考虑实时切削力的影响具有一定必要性。
关键词:四象限插补;多轴联动;切削力;指令偏差
0、引言
近年来,随着机床伺服系统相关技术的不断发展,许多学者通过数学建模的方式对伺服进给系统的性能进行分析,从而为伺服系统的调试提供参考。王志刚研究了永磁同步电机理论模型的建模方法,建立了 PMSM 电机系统电流环的仿真模 型,利 用 MATLAB/Simulink 仿 真 阶 跃 响应,通过不断矫正控制器的相关参数,使系统的各项指标达到了很好的效果。孙明佳等针对西门子机床伺服系统,研究各个环节的建模方法,建立了各个环节的精确模型,利用 MATLAB 进行仿真研究,对电流环和速度环进行了频率响应分析和实测对比,仿真结果和实测结果性能一致。金凤鸣研究了机床的闭环控制系统,建立了该系统各个环节的动态结构分析图,通过仿真直线轨迹,分析伺服系统的相关误差,仿真结果显示,增大位置环增益可以减小跟随误差,但增益过大会造成伺服系统位置响应震荡,所以,位置环增益必须控制在合理的范围内。PENG 等基于稳态设计,建立了闭环进给系统的仿真控制模型,利用经验公式对系统的 PID 参数进行调整,减小了该模型阶跃响应的超调量,有效提高了系统响应稳定性。訾斌等基于等效简化的电路模型,并考虑摩擦非线性环节和弹性振动等干扰因素,建立了交流伺服驱动系统的动态模型。
目前,人们对伺服系统研究的一般做法是,通过对伺服系统进行数学建模,使用仿真的方法分析系统的动态特性。首先,大部分学者一般在单轴的伺服控制系统基础上进行仿真分析。其次,理想状态下的伺服系统建模与仿真,和加工状态下多轴相互耦合作用 的伺服系统 有 较大的差异。针对以上不足,笔者将四象限插补算法与控制模型结合,在多轴联动的情况下对伺服控制系统的指令偏差进行深入分析。考虑加工过程中的实际切削力的影响,采集实际切削过程中的切削力信号,并将实际切削力添加到仿真模型中,分析切削力对伺服控制系统指令偏差的影响。
1、伺服仿真模型
1.1 伺服系统的组成环节
机床伺服系 统 主 要 由 位 置 环、速 度 环、电 流环、电动机及检测机构等构成,分为全闭环和半闭环两种控制方式,本文研究对象为全闭环结构。位置环是为了保证静态精度和动态的跟踪性能,速度环可以提高系统响应的快速性,电流环的作用是限制电流的范围并抑制内部电流干扰,提高快速响应特性,属于三环中的内环。全闭环的三环控制系统原理如图1所示。
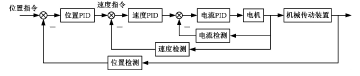
图1 三环控制的系统原理
1.2 伺服系统的数学建模
实际的数控机床伺服系统,无论是在结构方面,还是在系统的控制方面都是非常复杂的。我们要想对其建立数学模型并进行研究分析,就必须对其进行简化,忽略不必要的环节,保留主要的环节,将控制系统简化为交流伺服电机环节、机械传动环节及伺服控制器环节几部分,并对每一部分进行数学建模。本文以汉川 XK714D 机床为研究对象,对机床伺服进给系统各个部分参数进行查询和计算,结合研究对象的特点,在数学模型的基础上分别建立了 X、Y 两个进给轴的伺服仿真模型,其中,X 轴仿真模型如图2所示。
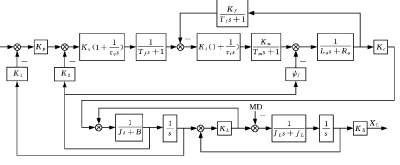
图2 X 轴伺服仿真模型
2、基于四象限插补程序的伺服系统特性及指令偏差分析
2.1 四象限插补程序与伺服系统联合模型
插补是数控机床加工工件时,为了使刀具按照一定的轨迹行走,将轨迹离散成一系列数据点的过程,一般有直线插补、圆弧插补和复杂曲线插补。插补性能是衡量数控机床性能的重要指标。本节将对四象限插补与伺服系统的联合仿真过程进行研究,通过 MATLAB 四象限插补程序获得X、Y 方向各自的插补轨迹,并将 X、Y 两个方向的插补轨迹作为伺服进给系统控制模型的输入指令;通过分析伺服控制系统的仿真输出轨迹,并将输出轨迹与输入指令对比,得到 X 轴、Y 轴多轴联动情况下伺服系统的指令偏差,进一步地研究控制器 PID 参数对多轴联动下伺服系统的影响。图3为基于四象限插补程序的伺服系统仿真流程框图。
2.2 基于四象限插补程序的多轴联动轨迹及指令偏差分析
基于四象限插补轨迹进行多轴联动仿真,将典型的圆弧轨迹作为仿真对象。本节对圆弧插补仿真进行研究,将插补程序的结果作为伺服进给系统控制模型的输入指令,分析输出特性及指令偏差情况。运 行 MATLAB 四 象 限 圆 弧 插 补 程序,分别输入圆弧轨迹起始点坐标(0,0)、终止点坐标(0.5,0.5)、圆弧半径50mm,圆心靠近原点,顺时针插补,插补步长为 0.5mm,得到 X 轴、Y轴的插补位移及圆弧插补轨迹,如图 4 所示;将X 轴、Y 轴 的 插 补 位 移 作 为 伺 服 运 动 系 统 的 输入,仿真得到控制系统模型的实际输出圆弧轨迹,如图5所示。
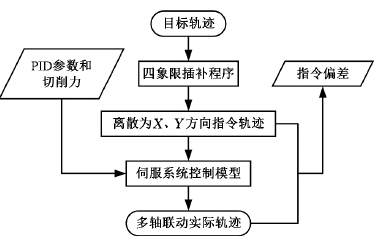
图3 四象限插补与伺服系统联合仿真流程框图
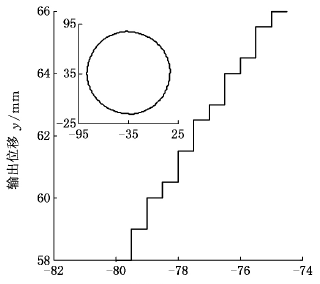
图4 四象限圆弧插补轨迹及其局部放大图
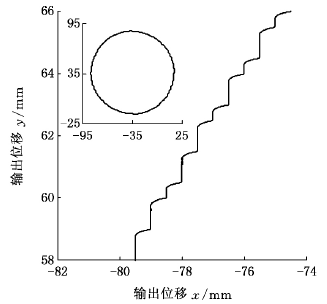
图5 控制模型输出圆弧轨迹及其局部放大图
根据上述圆弧插补数控指令轨迹与控制模型实际输出轨迹,分析图4中圆弧插补轨迹及局部放大图,可以看到,指令轨迹呈现明显的阶梯状,当插补步数取较大值即插补步长较小时,指令轨迹阶梯趋势变小,直至趋近于圆弧;指令轨迹经过控制系统之后,得到图5所示的控制模型实际输出圆弧轨迹及局部放大图,对比图4可以发现,控制模型输出的圆弧轨迹更为平滑,使得指令轨迹产生偏差,分别对比 X 轴、Y 轴指令轨迹与输出轨迹,得到 X 轴、Y 轴控制系统的指令偏差,如图6、图7所示。
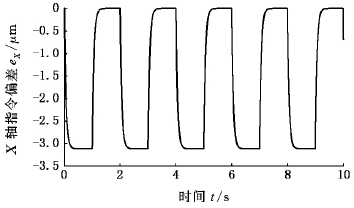
图6 X 轴控制系统指令偏差
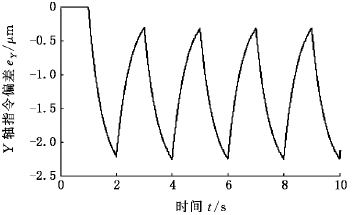
图7 Y 轴控制系统指令偏差
2.3 控制器增益参数对指令偏差的影响
现以圆弧 插 补 为 例,针 对 X 轴 伺 服 进 给 系统,研究位置环及速度环的增益对伺服进给系统指令偏差的影响,进行起始点为(0,0)、终止点为(10,10)、半径为60mm、步长为0.5mm 的圆弧仿真。首先,保证速度环增益不变,将位置环增益由6000增加到6050,得到图8所示的位置环增益调整前后指令偏差的变化曲线。然后,以起始点坐标(0,0)、终止点坐标(10,10)、半径60mm、步长0.5mm 的圆弧仿真为例,针对Y 轴进给系统,保证位置环增益不变,将速度环比例增益由 240 增加到 260,可以得到速度环比例 增 益 调 整 前 后 的 指 令 偏 差 曲 线,如 图 9所示。由图8、图9可以看出,位置环比例增益和速度环比例增益的变化都会使系统的指令偏差产生变化,从而影响伺服控制系统的输出轨迹。所以,伺服控制器的 PID 参数需要进一步优化,以减小控制系统的偏差,提高伺服系统的精度。
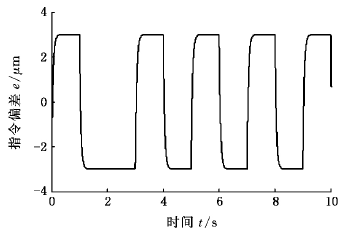
图8 位置环增益改变前后的指令偏差变化曲线
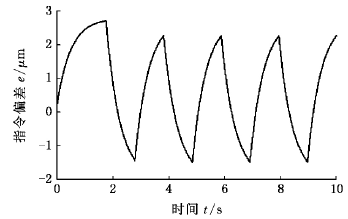
图9 速度环增益改变前后的指令偏差变化曲线
3、切削力对伺服控制系统响应分析
目前的研究一般仅在理想状态下对控制参数进行优化分析,或者仅采用切削力仿真信号模拟外界干扰,没有考虑实际加工状态下伺服系统与工件的耦合作用对伺服控制系统的影响。切削加工是一个非常复杂的过程,仿真信号与实际切削力信号有较大的差异。为说明切削力对控制系统的真实影响,在机床上进行了4组切削实验,采集切削过程中的力信号,将实际切削力信号作为外界干扰应用于模型仿真分析,研究切削力对伺服控制系统的影响。
3.1 实验设计
本文 以 汉 川 XK714D 机 床 为 研 究 对 象,将Kistler 9257A 三向测力仪作为实验中切削力信号(经 Kistler 5070电荷放大器进行信号处理)的采集 仪 器,采 样 频 率 为 1kHz;测 试 工 件 选 用T6061铝合金,实验刀具为直柄立铣刀 HSS16。为了获得不同状态下的切削力信号,设计了不同加工 参 数 下 的 4 组 实 验 (主 轴 转 速 n 均 为1500r/min,切削深度ap均为20mm),不同切削宽度和不同每齿进给量情况下的实验切削参数如表1所示

表1 实验切削参数
3.2 切削力对伺服控制系统的影响
机床伺服进给系统在切削加工的过程中始终受切削力的作用,为了更为真实地研究分析伺服进给系统,以 X 轴伺服进给系统为例,将实验获得的切削力加到仿真模型,分析切削力对伺服系统的阶跃响应输出,仿真结果如图10所示.
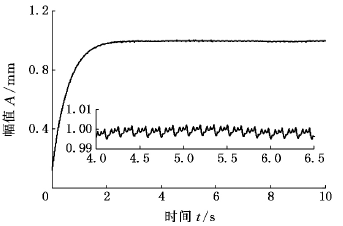
图10 切削力干扰下的伺服系统阶跃响应
通过分析图10中切削力干扰下的伺服系统阶跃响应输出曲线,可以明显看出,系统达到稳态时,输出曲线仍然存在微小的波动,说明切削力对伺服系统的输出精度会产生一定影响,使多轴联动情况下的圆弧插补过程产生指令偏差。
3.3 切削力对多轴联动伺服系统的插补精度分析以起始点
(0,0)、终止点(10,10)、半径80mm、步长0.5mm 的圆弧仿真为例,研究切削力对多轴联动伺服系统插补精度的影响。针对 X 轴、Y轴的控制模型,分别加入实验采集的切削力信号,经过模型的仿真计算,可以得到图11、图12所示的偏差曲线和图13所示的位置变化曲线。
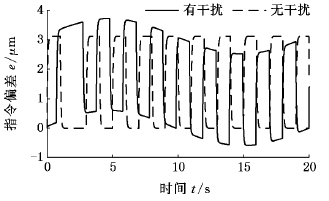
图11 有无切削力干扰的 X 轴偏差对比曲线
对比图11、图12中的偏差曲线可知,在有无切削力的情况下,数控系统位置指令偏差的幅值和波形都是不同的,并且指令偏差是时变的;由图13可以看到,在有无切削力的情况下,数控系统位置输出也是不同的。总的来说,切削力的干扰对控制系统的指令偏差是不容忽视的。因此,在考虑切削力因素情况下,对机床控制器的增益参数进行优化更符合实际并且也是十分必要的,这也是进一步深入研究的方向。
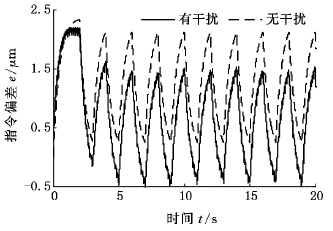
图12 有无切削力干扰的Y 轴偏差对比曲线
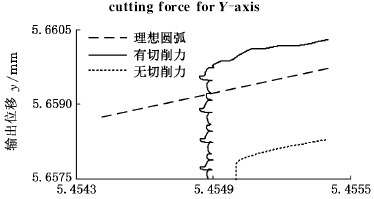
图13 有无切削力影响的位置变化曲线
4、结论
(1)以汉川 XK714D 机床伺服进给系统为研究对象,建立了该机床X、Y 两个方向伺服进给系统的仿真模型。
(2)在伺服系统仿真基础上,将四象限插补算法引入到控制系统模型中,实现了多轴联动圆弧插补仿真,并研究了 PID 参数对伺服系统圆弧插补指令偏差的影响。
(3)通过实验获得了真实的切削力信号,并将切削力信号加到伺服系统阶跃响应仿真与圆弧插补仿真中,结果表明切削力对伺服系统的指令偏差影响显著,在伺服系统参数优化过程考虑切削力影响具有一定必要性。
投稿箱:
如果您有机床行业、企业相关新闻稿件发表,或进行资讯合作,欢迎联系本网编辑部, 邮箱:skjcsc@vip.sina.com
如果您有机床行业、企业相关新闻稿件发表,或进行资讯合作,欢迎联系本网编辑部, 邮箱:skjcsc@vip.sina.com
更多相关信息