磨床主轴箱有限元分析及优化设计’
2016-8-31 来源:武汉理工大学机电工程学院 作者: 黄继雄 赵黎明 晏少亚
摘要:以某专用磨床主轴箱为研究对象,采用Solidworks建立主轴箱的参数化模型,利用Workbench对主轴箱原模型进行静力分析和模态分析。根据分析结果初选12个尺寸参数作为设计变量,并对其进行灵敏度分析,筛选出对主轴箱主轴孑L部位变形影响最大的六个参数。在此基础上进行多参数多目标优化,并对优化结果予以校验。最终实现在保证主轴箱静动态特性的前提下,降低主轴箱质量,提高优化效率。
关键词主轴箱;静力分析;模态分析;灵敏度分析;优化设计
1、引言
主轴箱用以支撑并传动主轴,是机床的关键零部件。主轴箱的静动态特性直接影响到磨床的加工精度、机床的可靠性[1~2]、抗震性能等,对主轴箱进行动静态特性分析变得越来越重要。周孜亮[3]等对高速立式加工中心进行有限元分析,并据此对主轴箱实现多目标多尺寸优化,显著提高主轴箱的静动态特性。王禹林[4]等对某大型旋风铣床主轴箱进行模态分析找出薄弱环节,利用力热耦合分析进行综合优化,提高了主轴箱动静刚度。牛颖‘53等人对HDBS-63高速卧式加工中心主轴箱进行静动态特性分析,选取优化参数,进行优化设计,提高了主轴箱刚度,降低了质量。
2、有限元模型
2.1箱体结构
某专用磨床主轴箱分为前后两个部分。前箱体主要用来安装自动夹紧装置,与主轴卡盘一起实现对工件的定位夹紧;后箱体定位、安装在转塔头上,其内部的传动元件构成主运动传动链,实现主轴传动。前后箱壁上的主轴孔实现对主轴的定位与支撑。
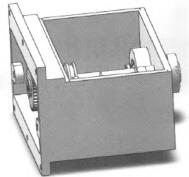
图l主轴箱装酉B图
2.2有限元模型
网格质量的好坏直接决定分析计算的效率和结果的可靠性[3]。因此在有限元建模时须对箱体模型进行必要的简化,去除模型中的倒角、圆角、小尺寸孔等。另外主轴部件的轴向位移是由主轴箱前箱壁和前端盖限制的,主轴部件和自动夹紧装置对主轴箱前后箱壁的刚度影响不大,故有限元模型中去除主轴部件和自动夹紧装置。将实体模型导人ANSYS Workbench,进行网格划分,最终生成74261个网格,节点数为339061。
主轴箱毛胚采用铸造成型技术,材料为HT200,密度为7200kg/m3,弹性模量为1.48E+11Pa,泊松比为0.27。
2.3边界条件
边界条件包括约束条件和载荷条件。由于主轴箱安装在转塔台上,用螺栓进行固定,故对六个螺栓孔采取固定约束,对主轴箱安装配合面采取位移约束。机床工作过程主要有两种工况:工况一是磨削过程中主轴箱承受的载荷,此时自动夹紧装置处于自锁状态,夹紧驱动力消失,主轴箱主要受磨削力、齿轮啮合力及箱体内部安装部件重力作用;工况二是夹具夹紧过程中主轴箱所受载荷,此时主轴箱主要受夹紧装置驱动力和箱体内部安装部件重力作用。
3、动静态特性分析
3.1静力分析
静力结构分析是用来计算结构在给定静力载荷作用下的响应[5]。静力分析结果是评价结构性能的重要指标。主轴箱的静态特性直接影响到主轴工作状态。同时主轴箱由于受自身材料限制,其抗拉、抗压强度有限。因此须对静力分析结果进行针对性查看。
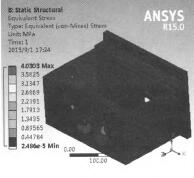
图2工况一主轴箱应力云图
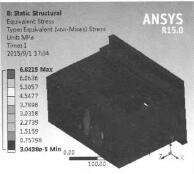
图3工况二主轴箱应力云图
由图2、图3可知,工况一、工况二时主轴箱最大应力分别为为4.03MPa、6.82MPa,最大应力都在前箱壁中部。这是由于主轴箱在主轴孔和电动推杆安装孑L受载荷作用造成的。主轴箱材料HT200能承受的极限应力为200MPa,远大于主轴箱在承受的最大应力。
工况一时主轴孔变形量(如图4)直接影响机床加工精度。此时主轴孑L各方向的最大变形量为:X轴0.22ffm,Y轴0.81tzm,Z轴1.44ffm。为保证机床加工精度,主轴孑L X轴、Z轴最大变形量不得超过0.5ffm,Y轴(非敏感方向)不得超过1_um。主轴孔Z轴方向变形明显超过允许的最大值。
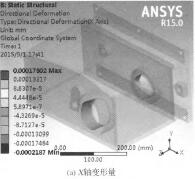
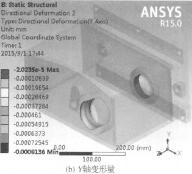
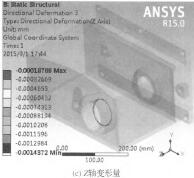
图4主轴孔各方向变形量
3.2模态分析
模态分析可以确定结构的固有频率和振型,寻找结构的薄弱环节,避免共振[6]。模态分析分为自由模态和约束模态[7]。本文采用约束模态分析,考虑了螺栓、定位销以及主轴箱安装面的影响,对其施加了相应的约束。
表1为主轴箱前4阶固有频率。主轴是由一对齿轮啮合传动,主轴工作转速为166rpm,故齿轮啮合频率为105.1Hz,因此主轴箱受到的激振频率范围为0~105.1Hz。主轴箱的一阶固有频率为593.28Hz,在其受到的激振频率范围以外,不会引起共振。
表l主轴箱前4阶固有频率

4、尺寸参数灵敏度分析
4.1优化参数选择
主轴孔Z轴变形超过允许值,X轴、y轴变形量及一阶固有频率却有一定的富余。在保证主轴箱静动态特性的前提下,为降低主轴箱质量,故需要对主轴箱进行优化。主轴孑L变形过大主要是由主轴箱前箱壁刚度不够造成,可以通过以下方法提高前箱壁刚度:缩短主轴箱前箱壁跨度、增加主轴箱前箱壁厚度以及添加加强筋。因此根据优化尺寸独立原则选取如图5所示的12个优化参数。
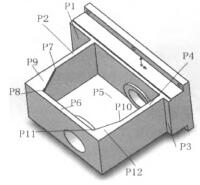
图5:优化参数选取
根据主轴箱结构尺寸及内部安装尺寸要求,在不影响主轴箱基本性能的前提下,选择合适的优化参数变化范围,如表2所示。
表2优化参数初始值及变化范围
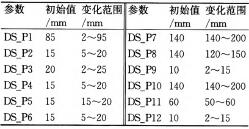
4.2灵敏度分析
灵敏度分析是通过一定的数学方法和手段,计算出结构的静动态性能参数随设计变量变化的大小和正负[8]。根据选取的优化参数建立参数化模型利用Spearman[9]相关性判定方法,确定各变量对主轴箱静动态特性的影响。图6反映了初选的12个优化参数对主轴箱的主轴孔X轴、y轴、z轴三个方向变形量的影响。由图可知,DS—P1、DS—P2、DS_P3、DS—P4、DS—P5、DS—P6对主轴孑L各个方向变形量影响较大。
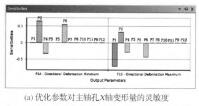
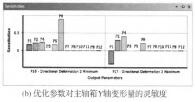
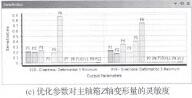
图6优化参数灵敏度分析
5、优化设计
5.1尺寸优化设计
Workbench优化设计须具备三要素:设计变量、约束条件和目标函数。其数学模型如下式所示。
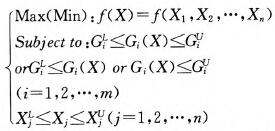
式中,X一(X1,X2,...,Xn)是设计变量,厂(X)是目标函数,G(X)是约束函数。其中GL和Gy分别是约束函数的下限与上限,XL和Xy分别是设计变量的下限和上限。
根据灵敏度分析结果,最终选取六个尺寸参数为设计变量,并以主轴孑L X轴、y轴、Z轴三个方向的变形量为约束条件,质量最小化为目标函数进行优化设计,进行响应面优化[10]。最终优化结果圆整后如表3所示。
表3参数优化结果
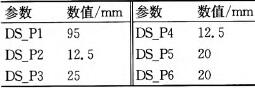
5.2优化结果校验
按照最终的尺寸参数优化结果对主轴箱模型进行再生,并以此建立有限元模型,分析其静动态特性。再生后的主轴箱的主要静动态特性参数如表4所示。
表4优化后主轴箱主要静动态特性参数
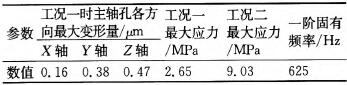
优化后主轴箱的主轴孔在X轴、y轴、Z轴三个方向的变形均符合要求,特别是Z轴方向的变形量降低到0.5/,m以下。主轴箱在工况一的最大应力有所降低,在工况二下的最大应力却增大到9.0373MPa,但仍远远低于HT200所能承受的极限应力。主轴箱的一阶固有频率有所提高,远离激振频率范围。优化后的主轴箱总体质量从45.504Kg降低到42.552Kg,减少了2.952Kg。
6、结语
通过对主轴箱进行静力分析和模态分析,得到主轴箱的静态特性参数。根据分析结果选取12个尺寸优化参数作为设计变量,利用灵敏度分析,找出对主轴孔各方向变形量影响较大的六个参数。运用响应面优化,确定最终的尺寸参数大小,实现对主轴箱结构快速改进,提高了优化设计效率。同时在保证主轴箱静动态特性满足要求的前提下,降低了6.49%的质量,实现主轴箱轻量化。
投稿箱:
如果您有机床行业、企业相关新闻稿件发表,或进行资讯合作,欢迎联系本网编辑部, 邮箱:skjcsc@vip.sina.com
如果您有机床行业、企业相关新闻稿件发表,或进行资讯合作,欢迎联系本网编辑部, 邮箱:skjcsc@vip.sina.com
更多相关信息