船用螺旋桨叶片五轴联动砂带磨削方法研究4
2016-8-5 来源:重庆理工大学机械工程学院 作者:张明德 王加林 苏占领 谢乐
摘要:针对大型船用螺旋桨叶片型面的高精度抛光打磨难题,基于零件的结构特点与加工要求提出了一种五轴联动数控砂带磨床磨削加工手段。为极力减小桨叶型面的波纹度,根据零件的三维几何模型设计了一种适应于该零件型面特点的连续加工轨迹线,加工过程中为避免接触轮与桨叶底盘发生碰撞,提出了一种动态调整磨削工具位姿的方法。最后,进行了相关实验,磨削后桨叶型面的尺寸精度偏差低于0.095ram且表面粗糙度降低明显,整体加工效果优于手工磨削,较高程度上提高了桨叶型面的磨削质量与效率。
关键词:船用螺旋桨;轨迹规划;数控砂带磨床;磨削加工
0、引言
螺旋桨是各类大型舰船的核心零/部件之一,在推动船只前进的过程中其所起作用至关重要。螺旋桨叶片主型面是由吸水面、压水面、导边与随边等组成,其对水体压缩与膨胀动作的实现与桨叶主型面的弯扭变化有着紧密的关系。为提高螺旋桨的推重比,其型面的抛光打磨工序极为重要。磨削加工一般作为快速提升工件表面质量的最终加工手段之一,砂带磨削是磨削加工领域里极具代表性的一类分支。得益于其柔性磨削、低磨削残留应力、工作效率高及刚性冲击小的特性,故在磨削机理与工作性能层面较砂轮磨削加工相比差异性较大。对于复杂曲面类零件表面的光整加工,砂带磨削主要有研磨与抛光的作用,辅以附着于布基载体上磨粒微刃的高速旋转动作,其兼有材料去除的作用。
对于螺旋桨叶片(以下简称叶片)表面的精整加工,受限于加工质量、工作效率、加工环境及加工成本等原因,普通的手工磨削方式已不能完全胜任。近年来,国内对于叶片表面的精整加工方法虽已得到不同程度的迭代更新,但较国外发达国家相比还有不小的差距。德日美等发达国家已率先引入数控砂带磨床对叶片型面进行抛光打磨,并且取得了高质量的磨削效果[1圳。数控砂带磨床有加工效率高、成本低、柔性大及零件加工一致性高的优点,用数控砂带磨床代替工人手工作业将是未来复杂曲面加工的发展趋势旧引,对保障人身安全、改善工人劳动环境、减轻劳动强度、提高劳动生产率、节约原材料消耗以及降低生产成本有着十分重要的现实意义。
本文以大型船用螺旋桨叶片为研究对象,运用五轴联动数控砂带磨床辅以浮动压力磨头机构对其表面进行抛光打磨,加工过程中使工件型面与砂带保持局部贴合状态以保证磨削过程的持续进行。通过实际的加工实验证明,磨削后叶片表面的粗糙度明显降低,尺寸精度也提升明显。
1、五轴联动数控砂带磨床磨削系统
本文研究的数控砂带磨床磨削系统如图1所示,主要由浮动压力系统、叶片型面余量检测系统等子系统组成。考虑到叶片主型面弯扭变化较大,四轴数控机床难以保证其加工精度,故采用五坐标加工方式。为保证磨削加工动作的持续进行将叶片装夹在可360。回转的工作台上,叶片的单次装夹可实现数控机床对其吸水面、压水面等主型面的连续磨削加工,此过程的实现较大程度上可规避由于装夹误差而影响机床的整体磨削加工精度。数控砂带磨床首先由3个直线轴(x轴、y轴、z轴)组成,其中y轴可实现螺旋桨叶片的左右移动,x轴可实现磨削工具相对于叶片的上下移动,z轴可实现磨削工具相对于叶片的前后移动。若单纯依靠以上3个直线轴的运动,那么数控机床末端磨削工具无法适应叶片型面的弯扭变化,故其必须增设2个旋转轴(曰轴、C轴)以提升磨削工具的可达性。砂带磨床磨削系统原理如图2所示,其中瓦为x轴上限行程,以为x轴下限行程,其余轴以此类推。数控砂带磨床主要性能指标如表1所示。
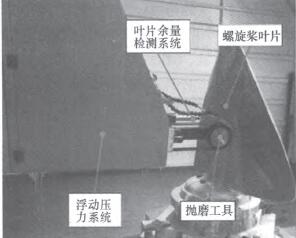
图1数控砂带磨床磨削系统
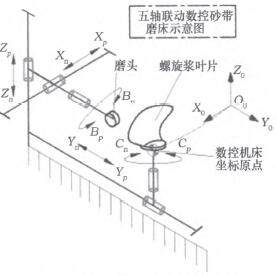
图2数控砂带磨床磨削系统原理
表1 数控砂带磨床主要性能指标
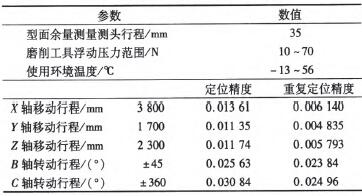
2、叶片型面砂带磨削轨迹规划及浮动压力系统
船用螺旋桨叶片主型面主要是由成组空间复杂曲面组成,空间复杂曲面可定义为空间域内的参数曲面,是由一些样条曲线通过一定非线性映射关系得出的拓扑曲面。与航空发动机叶片不同的是其中间部位呈鼓形,较边缘部位相比较厚,并且体积庞大、加工时间较长,船用螺旋桨叶片的组成结构如图3所示。
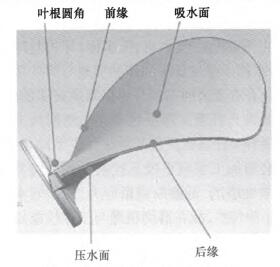
图3船用螺旋桨叶片的组成结构
2.1 砂带磨削轨迹规划与刀位点计算
大型船用螺旋桨叶片传统的加工工艺路线通常需要经过铸造、铣削、磨削、检验与滚花等几个主要的加工阶段。由于叶片主型面为复杂曲面且铣削后磨削前叶片型面残留铣削纹路较大,故刀具磨削轨迹布排方式的合理与否对于叶片表面加工质量与加工效率的提升至关重要。根据叶片结构与铣削纹路特点,将砂带磨削方式设置为横抛并从叶片根部逐次向上平移开始多个切削行的加工,以此可以得到迂回连接的砂带加工轨迹线,次之,将加工轨迹离散成均匀分布的磨削加工刀触点,如图4所示。
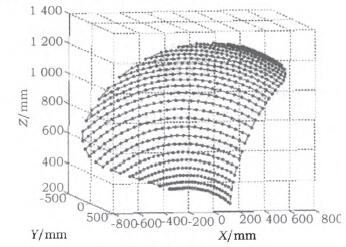
图4数控机床磨削加工刀触点
较普通数控机床加工刀具不同的是砂带磨床中磨削工具的刀位点Q位于接触轮中心(如图5所示)。若给定磨削刀触点P,结合刀触点处的法向矢量,v,接触轮半径R及砂带截面厚度日,可以得到理论刀触点矢量P与刀位点矢量Q坐标分量之间的位置关系表达式:

但实际加工过程中式(1)并不适用,究其原因可归结为一方面由于接触轮是柔性材料,其与工件表面接触时必定会产生一定程度上的变形;另一方面随着磨削动作的持续进行,附着于砂带表面上的磨粒随着磨削时间t的增加会逐渐磨损而间接影响砂带厚度日。设定砂带的初始磨损(快速磨损阶段)厚度为丁,磨损系数d∈(0,1),则磨损后砂带厚度日’为:

兼顾到以上两方面因素产生的影响,设定机床作业过程中接触轮的变形量R.∈(0,尺),以式(1)为基函数结合式(2),并在此基础上作出相应变形:
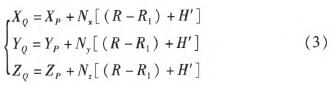
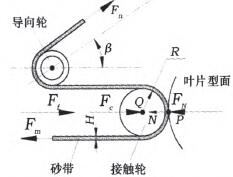
图5砂带磨床刀位点坐标及磨削工具局部受力
2.2浮动压力磨头系统
为减少实际加工过程中由于磨削压力过大而引起的过切或者表面残留波纹度过大现象(如图6所示),此数控砂带磨床配以浮动压力磨头系统。浮动压力系统结构如图7所示,主要由张紧气缸、接触轮、比例阀等重要部件组成。通过控制系统输入适应于叶片表面的磨削压力,比例阀可调节张紧气缸2以改变施加于接触轮上压力的大小以达到“随动磨削”的效果,并可有效降低机床磨削过程中的刚性冲击现象,张紧气缸2亦可完成磨削工具的进、退刀动作。浮动压力系统中,张紧轮可改变砂带包角的大小辅以张紧气缸1可有效避免作业过程中的砂带打滑现象。
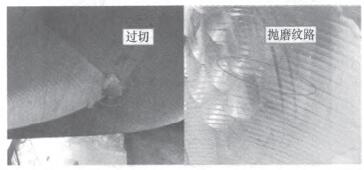
图6叶片表面加工缺陷
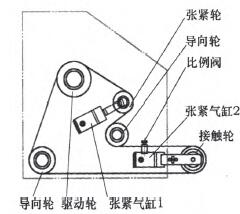
图7浮动压力系统结构
图5中,砂带的张紧力F。、F。、砂带与导向轮之间的摩擦力与气缸内壁之间摩擦力总和F,、气缸的张紧力P、接触轮与工件接触时产生的反向磨削压力n之间有着紧密的关系,其数学表达式为:

为避免磨削过程中易出现的欠抛现象,浮动压力产生的位移实则非常小,亦可以得出砂带的张紧力F。与F。所在平面之间产生的夹角p变化幅度非常小并可忽略不计,若输入张紧气缸2中的气体压力为卸,其有效工作面积为S,则机床作业过程中变化的气缸张紧力△F,=aps,磨削工具运动到任意位置时的摩擦力总和为B7,式(4)经变形可得到变化的磨削压力:

3、磨削工具位姿叶片根部动态调整方法
螺旋桨叶根圆角部位即叶片主型面与底座过渡部位,由于其空间结构过于紧凑及磨削工具轮廓尺寸大等原因,磨削工具运动至叶片根部时易发生不同程度的干涉碰撞现象,磨削工具易发生干涉部位如图8所示。
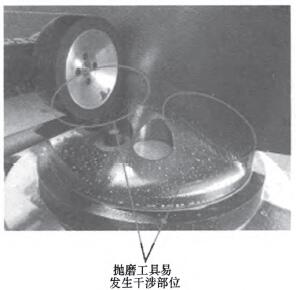
图8磨削工具易发生干涉部位
若采用减小磨削工具轮廓尺寸的方法来避免干涉,必然会影响机床加工效率以增加叶片加工成本。基于此现状,本文采用了动态调整磨削工具位姿的方法,如图9所示。计算出叶片主型面与叶根圆角部位的相交线2:与第i。。条u向参数线f,之间的距离,依据计算出来的距离动态调整绕刀触点处法向矢量n旋转的u向切向矢量t的角度θ。
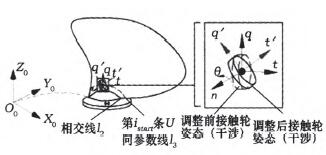
图9磨削工具位姿动态调整过程
抽取相交线f:与u向参数线f3作出分析。考虑到实际叶片根部型面弯曲变化较均匀,所以将其映射X00。Zo平面以便于分析,参数线f,与相交线z:之间的几何关系如图10所示。设定搜索方向为.,及凰轴为基线f。,并设定搜索容差为M,将Z,离散成均匀分布的刀触点,其中厶离散精度根据叶片型面实际磨削精度拟定。依据搜索方向l,,搜索所有被离散出来刀触点列中的峰值点P。,即峰值点P。处皿值最大,以上搜索过程中亦可以得到所有刀触点处与f3之间的最短距离D。,将所有刀触点处的最短距离用数列形式表示出来:

寻求数列D中的最小值D。,利用仿真软件可以得到该刀触点处的最佳转动角度巩,结合以上分析过程可以计算出任意刀触点所需要旋转的角度θi:

其中Oi的正负须结合峰值点P。综合考虑,若刀触点Pi处于R左边,那么结合实际叶片根部型面特点取Oi的符号为正,反之为负。设定n’为单位化之后刀触点处的法向矢量,结合微分几何相关知识可以得到任意刀触点处旋转之后的u向参数线切向矢量t7:

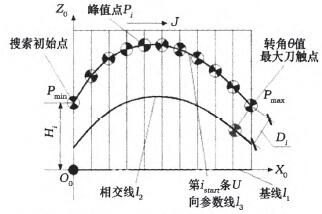
图10参数线f3与相交线f:之间的几何关系
磨削工具位姿调整分析流程如图1 1所示。
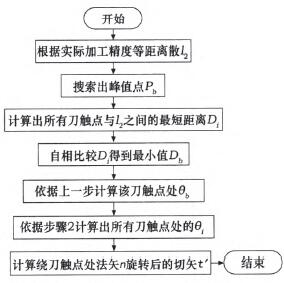
图11磨削工具位姿调整分析流
4、加工实验
实际叶片表面残留铣削纹路较大,为验证五轴联动数控砂带磨床实际磨削效果,所以将磨削加工实验分为粗磨、半精磨和精磨进行。
待加工工件为某机械厂生产的西2 500mm侧推螺旋桨叶片,材料为锰青铜,叶片表面最厚处达40ram,叶片实际磨削参数如表2所示。
表2叶片实际磨削参数

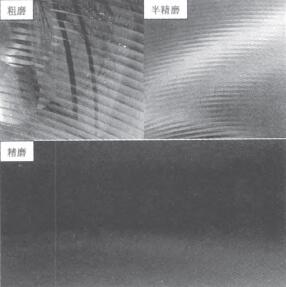
图12叶片经过各加工阶段之后表面质量效果
叶片表面经过粗加工、半精加工、精加工3个加工阶段之后表面质量效果如图12所示。
由图12可以看出半精磨较粗磨相比,表面刀具纹路明显变小,精磨后表面波纹度改善明显。
为了解实际磨削之后叶片表面尺寸精度与粗糙度数值大小及分布情况,由下至上均匀抽取叶片压水面上具有代表性的5条u向参数线,分别提取20个刀触点进行分析,固定x轴与z轴坐标分量,利用海克斯康三坐标测量仪将磨削加工后刀触点处y轴坐标分量所反映的偏差在MATLAB平台上进行输出,l,轴坐标分量尺寸偏差如图13所示,随着磨削时间的增加,表面偏差波动值逐渐趋于平缓,叶片型面
总体偏差与粗糙度测量结果如表3所示。
表3磨削实验后测量结果

叶片理论要求重量为383.45kg且重量偏差不超过原有重量的±4%。叶片铣削后磨削前称重为383.98kg,磨削后称重为378.20kg,偏差为一1.37%,符合实际加工要求。加之,本文动态调整了叶根圆角区域的接触轮位姿,使磨削工具的可达磨削区域提升约9%,并且整体磨削效果较好。
5 、结语
1)本文针对螺旋桨叶片型面结构复杂、表面精整加工后尺寸精度难以把控的特点,创新性地提出了运用五轴联动数控砂带磨床对其表面进行高效高精度打磨,机床的工艺灵活性与加工适应性均得到了较高程度的提升。最后进行了实际加工实验,结果证明叶片型面磨削效果与磨削效率远高于现阶段高强度且磨削质量难以管控的手工作业方式。
2)本文在不牺牲数控砂带磨床原有加工效率的前提下优化了磨削工具进入叶根圆角难加工区域的位姿形态,使磨削工具的可达磨削区域得到了一定程度上的提升。
投稿箱:
如果您有机床行业、企业相关新闻稿件发表,或进行资讯合作,欢迎联系本网编辑部, 邮箱:skjcsc@vip.sina.com
如果您有机床行业、企业相关新闻稿件发表,或进行资讯合作,欢迎联系本网编辑部, 邮箱:skjcsc@vip.sina.com
更多相关信息