基于 hyper MILL 的半开式整体叶轮五轴数控编程与加工技术
2019-1-16 来源: 山东大学 机械工程学院 高效洁净机械制 作者:赵文明,庄 鹏,鞠岗岗,刘战强
摘要: 整体叶轮是航空发动机和各类透平机械的关键零部件。针对整体叶轮因结构复杂而导致数控编程和加工难度大的特点,首先,以半开式整体叶轮为例,在 hyper MILL 软件中进行五轴数控编程。然后,编程得到的刀具轨迹经过内部机床仿真验证,利用后处理器将刀位( CL) 文件转换成机床可识别的 NC 加工代码。最后,在 DMU - 70V 五轴加工中心上对 Al7050 铝合金整体叶轮进行加工。加工过程中没有出现干涉、过切、欠切等问题。结果表明 hyper MILL 可以简化编程的过程,提高编程和加工的效率,为其它同类复杂零件的编程加工提供了依据。
关键词: 整体叶轮; 数控编程; 五轴加工; hyper MILL
0 引言
整体式叶轮已经开始应用于航空发动机、燃气轮机、离心泵等透平机中。叶轮的加工质量对于透平机性能有非常大的影响。然而,由于整体叶轮有复杂的曲面和扭曲的叶片等复杂结构,使得叶轮的加工十分困难,数控编程软件生成的 NC 代码可能存在过切、欠切和干涉等问题,如何快速准确地生成 NC 加工程序成为制约叶轮加工的关键。CAM 软件已经在复杂零件的数控编程方面得到了广泛的应用,为整体叶轮的数控编程提供了很大的帮助。
目前应用较多的数控编程软件中以 UG 最具代表性。利用 UG 加工模块进行叶轮的数控编程,对加工工序进行规划,生成加工的刀具轨迹后在 VERICUT等软件中进行刀具路径的仿真验证。但 UG 加工模块对整体叶轮等复杂零件的数控编程操作较多,难以掌握,且编程效率相对较低。国内外的学者也利用几何分析计算和程序语言编程等方法获得加工区域的刀具路径,并进行仿真验证和误差分析等。实际加工结果证明,此类方法有效可行,但过程较为繁琐。因此,为解决整体叶轮加工数控编程问题,需开发或应用能够针对其复杂结构的软件或方法。
hyper MILL 是德国 OPEN MIND 公司的一款 CAM软件,其中的叶轮加工模块给叶轮类零件的数控编程提供了便利。本文针对整体叶轮数控编程复杂和加工难度大的问题,以半开式整体叶轮为例,在 hyper MILL软件中进行编程。将生成的 NC 代码导入到 DMU-70V五轴加工中心,完成对 Al7050 铝合金叶轮的加工。
1、半开式整体叶轮模型
半开式整体叶轮的典型结构如图 1 所示。叶轮主要由叶片和轮毂组成,若干叶片均匀分布在轮毂曲面上,其中叶片可分为长叶片和短叶片,组成叶片的曲面包括吸力曲面、压力曲面、前缘、后缘和包覆曲面。包覆曲面由包覆曲线绕中心轴旋转得到,它限定了叶片的外边界。
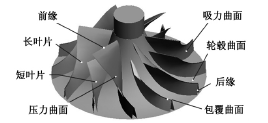
图 1 半开式整体叶轮及其主要结构
本文所采用半开式整体叶轮模型在 hyper CAD 模块中建模得到,如图 2 所示。该叶轮由 7 个长叶片和轮毂组成,没有短叶片。叶片的平均厚度为 3mm,叶片的最大高度为 33mm,相邻两叶片间的最短距离为7. 5mm,叶轮底部的最大直径为 130mm,整体高度为62mm。
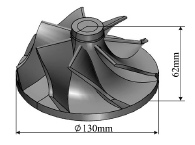
图 2 半开式整体叶轮模型
整体叶轮结构复杂,其数控编程和加工的难点主要体现在: ①相邻叶片间的距离较小,加工时易产生干涉,生成无干涉的刀具轨迹较困难; ②叶片厚度小,在精加工过程中会出现加工变形和振动等问题,使叶片表面的加工质量降低; ③叶片的扭曲度较大,使刀具轴线矢量的计算复杂。
2 、刀具选择
选择合适的刀具材料和刀具类型不仅可以保证加工效率,而且能够满足零件的加工质量。刀具的选择需要充分考虑整体叶轮的形状、材料等各个方面的因素。整体叶轮铣削加工刀具的选取可遵循以下原则:①粗加工时,在流道尺寸允许的情况下尽可能采用大直径刀具,以提高加工效率; ②在满足叶片高度的情况下,为保证刀具有足够的刚度,其悬伸长度应尽可能短; ③半精加工和精加工时选择直径较小的球头铣刀,也可选择带锥度的刀具。
对于铝合金等易加工材料,可选择硬质合金刀。根据整体叶轮的尺寸、材料等,选择平底立铣刀和球头铣刀分别完成各个加工工序。所选刀具的参数如表 1 所示。
表 1 加工中选用刀具的参数
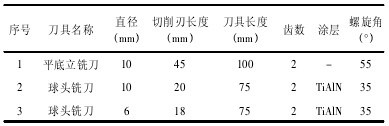
3 、整体叶轮的数控编程
3. 1 hyper MILL
数控编程过程在 hyper MILL 中对整体叶轮加工的各个工序进行数控编程,其数控编程与加工的步骤如图 3 所示。
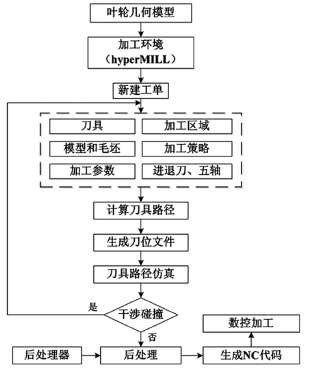
图 3 hyper MILL 数控编程及加工过程
将整体叶轮模型导入 hyper MILL,并进入加工环境; 新建一个加工工单并在此工单中对刀具、加工区域、模型和毛坯、加工策略、加工参数、进退刀以及五轴等进行设置,然后对刀具路径进行计算; 生成刀位( CL) 文件后在软件中对刀具路径进行仿真,若出现干涉碰撞,则需重新对工单的设置进行修改; 验证刀具路径无误后,利用后处理器对 CL 文件进行后处理,得到NC 代码,并导入到机床中进行数控加工。
3. 2 整体叶轮加工工序以及加工参数确定
根据所用毛坯的形状以及整体叶轮的结构特点,将整体叶轮的加工工序分为毛坯面预加工、叶轮粗加工、半精加工和精加工。其中,毛坯面预加工包括毛坯面粗加工和精加工; 半精加工过程包括叶片半精加工和叶轮盖半精加工; 精加工过程包括叶片精加工、流道精加工和叶轮盖精加工。
各加工工序所用刀具以及加工参数如表 2 所示。
表 2 各加工工序使用的刀具及加工参数
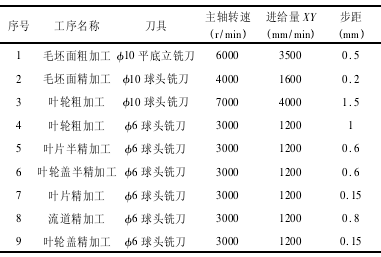
3. 3 整体叶轮数控编程
3. 3. 1 毛坯面预加工
毛坯面预加工的目的是在圆柱形毛坯上加工出叶片的包覆曲面,包覆曲面的加工可以通过车削 或者铣削完成。为了减少工件装夹的次数,均采用铣削完成。首先采用 3D 循环中的“任意毛坯粗加工”的方式进行毛坯面的粗加工,余量 0. 2mm。后在 3D 高级循环中的“等距精加工”方式下,对毛坯曲面进行精加工,选用螺旋进给方式,避免在包覆曲面上形成垂直进刀的痕迹。生成的刀具路径如图 4 所示。
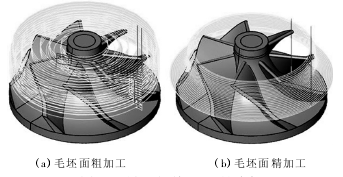
图 4 毛坯面预加工刀具路径
3. 3. 2 叶轮粗加工
粗加工以去除多余材料为目的,加工出叶片的基本形状,所以应优先考虑提高加工效率。本文中的叶轮模型的相邻两叶片间的最小距离为 7. 5mm,若采用直径较大的刀具则无法加工到叶片的根部或者出现过切现象,若采用直径较小的刀具则加工效率太低。综合考虑,可采用不同直径的刀具进行两次粗加工的加工方式。在设置加工策略时,选择“型腔拆分”功能,对于没有短叶片的整体叶轮,导入侧较窄,用小直径的刀具加工,退出侧较宽,用大直径的刀具加工,如图 5所示。
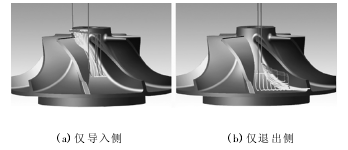
图 5 型腔拆分加工
两次粗加工均采用五轴叶轮循环中的“5X 叶轮粗加工”。第二次粗加工设置加工策略时选择型腔拆分中的“仅导入侧”,只对第一次粗加工未加工到的导入侧狭窄部位进行加工。由于刀具直径较小,所以适当减小切削参数,水平步距设为 0. 5mm,垂直步距设为1mm。两次粗加工中,叶片的余量为 1. 2mm,流道的余量为 0. 5mm。五轴设置可以对加工过程中的刀轴倾斜和刀具避让策略等进行设置。
采用五轴联动的方式进行加工并选择绕 Z 轴的避让策略,以简化刀具的运动,使切削过程保持稳定。两次叶轮粗加工的刀具路径如图 6 所示。
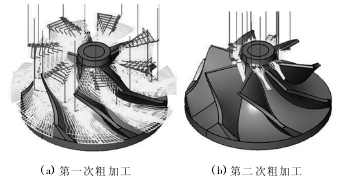
图 6 叶轮粗加工刀具路径
3. 3. 3 半精加工
叶轮的半精加工可以平滑粗加工产生的粗糙表面,减少粗加工留下的误差,包括对叶片曲面和叶轮盖外圆的加工,分别采用“5X 叶轮点加工”和“5X 等高精加工”的加工方式完成。对叶片曲面的加工采用点加工或者侧刃加工的方式完成。侧刃加工使用刀具侧刃对叶片曲面进行加工,如果刀具侧刃与叶片曲面拟合结果在可接受的范围内,则应优先使用此循环。
与点加工相比,侧刃加工所需的加工时间更短。但是,如果叶片曲面扭曲过大,而无法进行侧刃加工时,应优先考虑使用点加工。在点加工方式中,叶片曲面采用刀具点接触法,以连续的、螺旋形的运动进行加工。考虑到本文中采用的叶轮模型的叶片的扭曲度,采用了点加工方式。铣削策略设置为环绕叶片的螺旋刀具轨迹,进刀位置选择退出侧,余量为 0. 3mm。叶片半精加工的刀具路径如图 7a 所示。
叶轮盖外圆的加工采用“5X 等高精加工”的加工方式。选择螺旋进刀方式,A/B 轴的倾斜角度均为20°,并设置外圆面的上下边界以确定加工区域,余量为 0. 2mm。叶轮盖半精加工刀具路径如图 7b 所示。
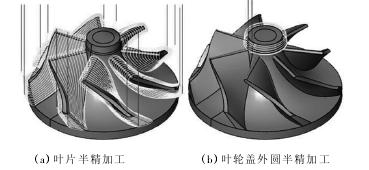
图 7 叶轮半精加工刀具路径
3. 3. 4 精加工
叶轮精加工过程要达到零件要求的尺寸精度和表面质量。该过程分别对叶片曲面、流道曲面和叶轮盖外圆进行精加工,采用的循环方式分别为“5X 叶轮点加工”、“5X 叶轮流道精加工”和“5X 等高精加工”。其中,叶片精加工与叶轮盖外圆精加工的铣削策略和五轴设置等与半精加工过程相同,仅将步距减小,如表2 所示,余量均为 0。流道精加工在叶片之间逐个进行,铣削策略选择全部,对流道的全部区域进行精加工,从导入侧进刀,横向进给策略采用平行双向加工,余量为 0。叶轮精加工的刀具路径如图 8 所示。
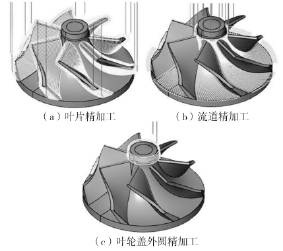
图 8 叶轮精加工刀具路径
3. 4 刀具路径仿真
生成刀具路径后需要对其进行仿真模拟,以检查刀具、工件、机床、夹具和刀柄等各部分之间有无干涉碰撞。在 hyper MILL 中可以采用内部模拟、内部机床模拟和 hyper VIEW 三种方法对生成的刀具路径进行仿真。
表 3 三种刀具路径模拟方式对比
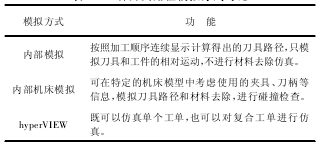
本文采用内部机床模拟验证生成的刀具路径。内部机床模拟需要考虑加工中所用的机床模型及其各部分的运动学信息、刀柄和夹具的外形尺寸等参数,以模拟真实的加工过程,在验证刀具路径的同时,检查各部分是否会出现干涉碰撞。
3. 5 后处理数控编程
生成的 CL 文件不能直接进行数控加工。后处理可以对前置处理中生成的 CL 文件进行转换,生成数控系统能够识别的控制指令。不同于三轴联动机床,五轴联动机床由于回转工作台或摆动主轴的加入,导致机床结构多样,运动轨迹坐标变换算法不尽相同,在加工表面曲率变化较大时,也需要动态调整进给速度以确保加工件表面质量。
在 hyper MILL 中,利用后处理定制工具 hyper POST创建. oma 格式的后处理器,并对生成的 CL 文件和加工信息进行后处理,生成机床可识别的. h 格式的 NC加工代码。图 9 所示为叶轮粗加工的部分 NC 代码。
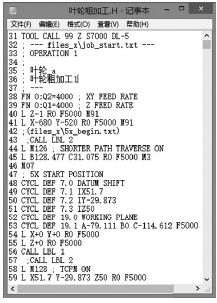
图 9 叶轮粗加工过程的部分 NC 代码
4 、实际加工
在 DMU-70V 五轴加工中心上完成叶轮零件的加工,机 床 的 部 分 参 数 如 表 4 所示。选 用 圆 柱 形 的Al7050 铝合金毛坯进行加工,其直径为 130mm,高度为
180mm。用四爪卡盘固定在机床的工作台上,如图10 所示。
表 4 DMU-70V 五轴加工中心部分参数
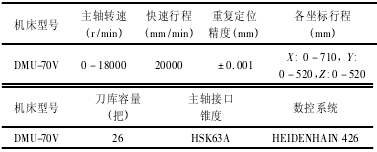
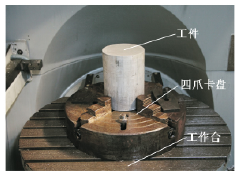
图 10 毛坯在工作台上的装夹
加工过程稳定,没有出现过切、欠切等现象。加工成后利用线切割将整体叶轮与剩余的圆柱毛坯分离,最终的加工结果如图 11b 所示
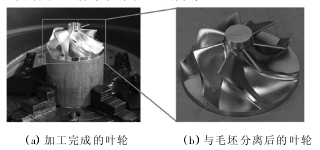
图 11 加工完成的半开式整体叶轮
5 、结论
( 1) 基于 hyper MILL 数控编程软件,利用叶轮加工模块对半开式整体叶轮进行数控编程。将整体叶轮的加工分为毛坯面预加工、叶轮粗加工、半精加工和精加工四个加工阶段,每一阶段包含对不同曲面的加工。其中叶轮粗加工分为两次加工完成,既避免了过切或欠切,又提高了粗加工效率。
( 2) 生成的刀具路径经过内部机床仿真验证后,利用特定后处理器得到相应的 NC 加工代码。
( 3) 在 DMU-70V 五轴加工中心上对 Al7050 铝合金叶轮进行了加工,整个加工过程经过一次装夹完成,避免了多次装夹造成的加工误差。加工过程平稳,加工完成的叶轮没有出现过切、欠切等现象。
研究结果对整体叶轮等复杂零件的编程加工具有一定的意义。
投稿箱:
如果您有机床行业、企业相关新闻稿件发表,或进行资讯合作,欢迎联系本网编辑部, 邮箱:skjcsc@vip.sina.com
如果您有机床行业、企业相关新闻稿件发表,或进行资讯合作,欢迎联系本网编辑部, 邮箱:skjcsc@vip.sina.com
更多相关信息