基于EAKI 辨识策略的机床振动试验研究
2016-9-22 来源:清华大学机械工程系等 作者:黄子凌 刘成颖 李铁民
摘要: 机床振动是制约机床加工精度及效率的核心因素,文章基于EAKI 策略在多台机床上开展振动试验研究。针对强迫振动及自激振动信号辨识问题,首先提出EAKI 振动信号辨识策略; 为有效构建振动信号备案知识库,提出信号特征分量提取算法; 最后在国内外多台数控机床上进行了全转速状态下的振动试验研究。试验结果有效地验证了EAKI 策略的可行性与实用性,同时为机床性能评估及设计完善提供了良好借鉴。
关键词: EAKI 方法; 信号辨识; 振动试验; 特征提取
0 .引言
机床振动是制约机床加工精度及效率的关键因素之一,其可分为强迫振动及自激振动。二者由于产生原因不同,对应的抑制措施也有差异,因此对其进行辨识分离具有重要的研究意义。
机床的强迫振动是指由外激振源引起的振动。如由机床基座引入的外界振动、机床不平衡部件( 电机等) 或磨损部件( 齿轮和轴承等) 引起的振动。机床自激振动( 颤振) 往往由外作用源引发( 工件磨损点等) ,但由加工系统内部激励产生[1]。
在机床设计时,强迫振动就应设法消除或避免。对于高精度机床,强迫振动的影响是较小的,因此在一般研究中并未引起特别注意及重视。国内外学者针对强迫振动及自激振动信号辨识的研究工作并不多。在对强迫运动的研究中,Kegg 等人给出了对强迫振动原因的判定方法,该方法在机床试验或加工准备过程中较为实用,但不适用于在线监测评估; 值得注意的是,Weck[2]提出了从切削力信号的功率谱中将铣削刀齿通过频率辨识滤除的方法,但并未系统性地介绍强迫及自激振动的一般辨识方法。多数研究工作集中于自激振动监测辨识、稳定性分析以及基于振动信号的故障诊断领域。Zhang C L 等[3-4]学者对多信号的监测能力分别进行了实验分析,以选定最为适合的颤振监测方式; Altintas 等[5]基于再生颤振模型对颤振稳定性进行了深入研究,在实践上获得良好应用。国内于俊一[6-9]等学者也在颤振监测、稳定性分析等领域做了大量工作,为推动机床技术进步作出重要贡献。
然而从国内机床的使用经验来看,当前面临的一个突出问题是机床材料选用、设计制造以及安装布置尚存在不足,由此产生的强迫振动不容忽视。在机床加工过程中,强迫振动的影响往往甚至会处于主导地位,因此将强迫及自激振动相结合进行研究更具有实际意义。
1. EAKI 机床振动信号辨识策略
在实际加工过程中,从观测到的振动信号中往往难以区分出强迫振动及自激振动分量。然而,强迫振动的不确定性较小,可通过前期实验等确定机床的强迫振动分量,在评估机床性能的同时形成先验知识,以在实际加工信号中将其与自激振动信号区分开来,达到辨识以及分别采取抑制策略的效果; 同时,在加工前评估机床的强迫振动信号,也有利于在前期对机床性能不断进行完善。
基于上述思想,提出EAKI 方法,对机床的振动信号进行辨识。具体包括以下步骤:
( 1) 强迫振动试验( Experiments on forced vibration): 在空载工况下对机床振动进行试验分析,以获取在多转速条件下机床主轴的振动信息。
( 2) 振动信号分析( Analysis of forced vibration signal) 对试验采集到的强迫振动信号进行分析处理,旨在提取出起主导作用的强迫振动信号特征。
( 3) 备案知识库构建( Knowledge Base formation) :基于信号分析处理结果,并结合相关判定规则,形成相应振动信号备案知识库。
( 4) 辨识评估( Identification of vibration signal) : 基于知识库,对实际加工过程中监测到的振动信号进行对比分析,从而辨识出自激振动分量,并对其影响程度进行评估,识别出起主导作用的因素,为后续抑制方式奠定基础。
在EAKI 方法中,强迫振动试验及振动信号分析是该方法最为重要而基础的部分,也是决定该方法是否可行的关键,后文即通过多机床试验及信号特征提取算法等,探究EAKI 方法的可行性。
2 .关键设备及试验方案
根据EAKI 方法,强迫振动试验是进行信号辨识分析的前提。强迫振动试验主要包含信号采集分析软硬件设备以及试验机床等。
本试验采用实验室自主研发的主轴振动测量系统,能完成信号采集监测、时频域分析、状态报警等多种功能。设备安装及试验现场如图1 所示。
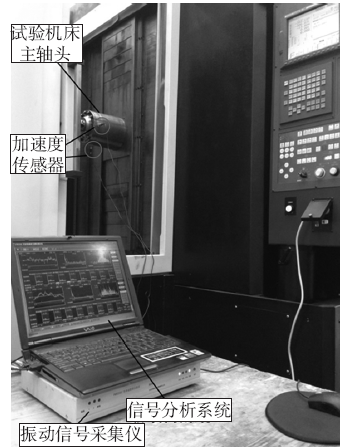
图1 试验现场图
为综合全面地验证EAKI 方法并分析比较各机床的差异性,选取了四台机床作为试验对象,基本涵盖了国内外典型机床类型( 其中D 为德国机床) 。各机床的主要参数如表1所示 。
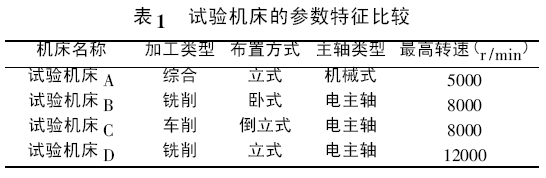
具体试验过程如下:
( 1) 安装试验设备。试验采用两支ICP 加速度传感器,安装在主轴头处,分置于X、Y 方向。
( 2) 设置试验参数。主要包含测量频次、采集频率、信号耦合方式、滤波方式以及信号对应的测量转速等信息。
( 3) 试验信号采集。设定数控机床运转至所需转速,待信号稳定之后实时采集并存储。
( 4) 改变转速,重复采集试验。根据每台机床的额定转速或最高转速,选取一定的转速间隔,分别测定在不同转速情形下的振动信号。
3 .振动信号特征分量提取算法
试验采集到的加速度信号描述了机床主轴在相应转速下的振动特征。信号分析的目的在于获取该转速下强迫振动特征分量信息,该特征分量包括频率及信号幅值等信息。本文提出特征分量提取算法如图2 所示。
在进行信号分析前,已对试验机床在各转速条件·44· 组合机床与自动化加工技术第2 期
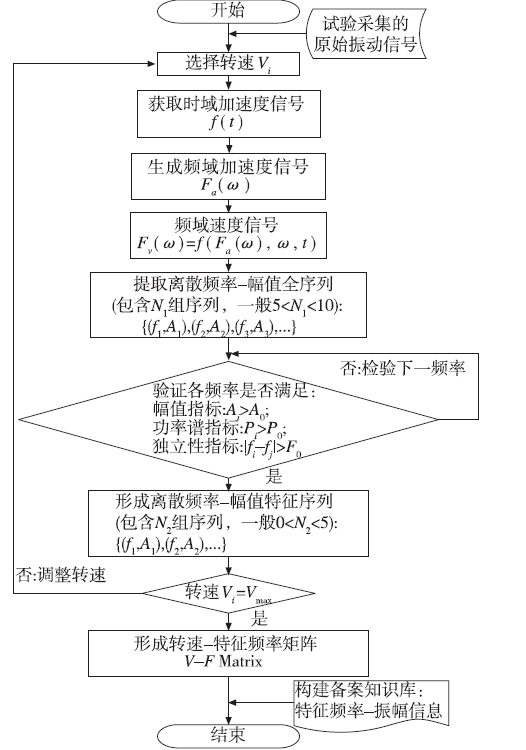
图2 振动信号特征分量提取算法
在进行信号分析前,已对试验机床在各转速条件下的振动信号进行了采集存储。原始信号是加速度传感器输出的电压时域信号f( t) ,经傅里叶变换等算法处理后,易于生成频域信号。加速度信号Fa( t) 在反映信号瞬态变化时较为有效,但在描述强迫振动源频率特征时,不能对各频率下振动信号的能量分布进行很好的区分; 经处理获取的速度信号Fv( t) ,能够更好地对振动特征进行描述。以试验机床A 在5500r /min时的振动信号为例,图3、图4、图5 分别描述了时域加速度信号、频域加速度信号及频域速度信号特征。
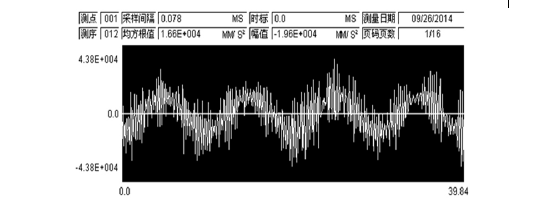
图3 时域加速度振动信号特征
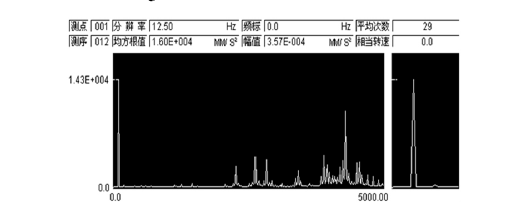
图4 频域加速度振动信号特征
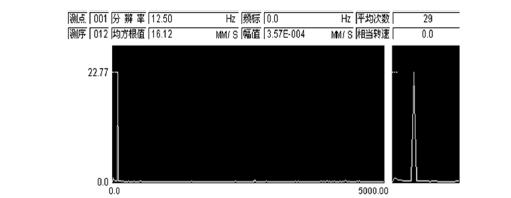
图5 频域速度振动信号特征
经处理得到的频域速度信号具有明显的峰谷特征,可以用频率-幅值序列来描述每一振动信号的频率特性,幅值反映出该频率基准信号的振动烈度。通常情况下,可分离出5 ~ 10 组频率-幅值序列,以此来近似表征该转速情况下的振动信号。
初步分离提取出的频率-幅值序列不能直接用于进行后续分析,因其包含较多的冗余或无效信息。为此,需对该序列进行进一步地筛选过滤。考虑到信号分离的目的,主要采用三个指标来对频率-幅值序列进行筛选,分别为幅值指标、功率谱指标以及独立性指标。幅值指标及功率谱指标用来表征基准信号的烈度及功率密度,其中幅值指标最为直观,对于较低幅值的序列予以过滤,幅值阈值A0参照ISO2372 旋转机械振动烈度标准进行设定,为保证信息完整,此处选取0.1
mm/s。独立性指标用来对频率对应的振动源的独立性关系进行表征。由于采样频率限制及信号处理时分辨率制约,频率序列会出现频率接近的情况。为更准确真实地表征信号对应的强迫振动源,将频率值相近的序列对进行合并。用频率间距值F0 来刻画各序列对之间的独立性关系,根据经验,采取5Hz 或10Hz 作为间距阈值。
对所有转速下的振动信号按照上述方法进行处理后,便可得到转速-特征频率矩阵。以试验机床D 为例,经上述流程得到的典型转速-特征频率矩阵如表2所示。
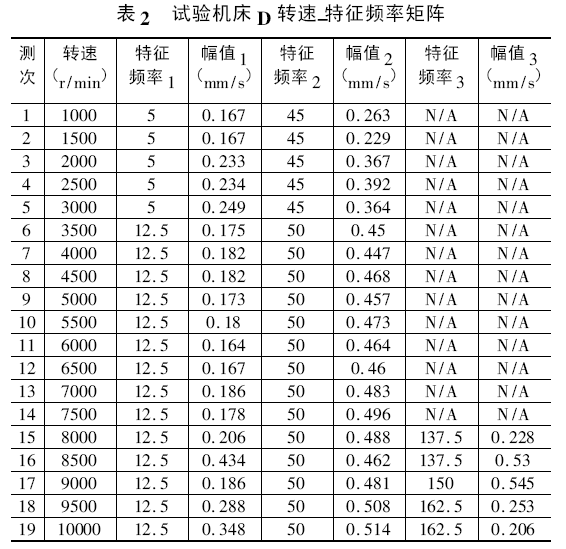
对其他机床进行试验分析得到与此相近的结果,该结果作为信号分析的输出成果,形成备案知识库。
4. EAKI 策略有效性分析
经上述算法得到振动特征分量信息,须对该结果进行分析,以验证EAKI 方法的可行性与有效性。验证的关键在于通过本次试验及信号分析能否观察到稳定存在的强迫振动源,同时需验证该类型强迫振动是否产生重要影响。机床强迫振动按激振源类型可分为两类,一类由自身回转引起,一类由外激振源引起。下面分别进行分析研究。
4. 1 机床主轴回转对应的强迫振动分析
主轴自身回转形成的强迫振动激励是重要而的强迫振动激振源,其对应的频率可称之为转速频率。理论转速频率与转速正相关,即f = n /60。
将试验测定的强迫振动转速频率与理论强迫振动转速频率进行对比,如图6 所示。
由图6 分析发现,各机床理论转速频率与实际监测出的振动频率吻合度很高,反映出机床回转形成的强迫振动不容忽视,同时也验证了该监测方法以及信号特征提取算法的有效性。
另一方面,转速频率对应的强迫振动对各机床产生的影响各不相同。首先,该类型强迫振动产生显著影响的时刻不同。试验机床A 从最低转速500r /min时便可明显观测出转速频率造成的影响,试验机床B、C、D 分别在5200r /min、3300r /min 及8000r /min 时方可观测到转速频率造成影响。其次,各机床回转型强迫振动烈度也各不相同,这将在4. 3 节进行分析。
综上分析可得出,试验有效地验证了回转型强迫振动广泛存在于各机床中,往往对机床产生较大影响,因此可将其作为典型强迫振动频率予以备案,形成知识库中的重要知识。
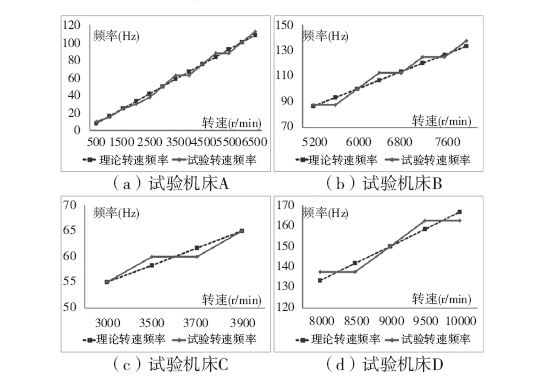
图6 各机床理论与试验转速频率对应关系
4. 2 其他外激振源强迫振动分析
除转速频率之外,试验还发现,各机床普遍存在其他一些可持续监测到的强迫振动频率,剔除转速频率之后,每种转速下对应监测到的强迫振动频率如图7所示。
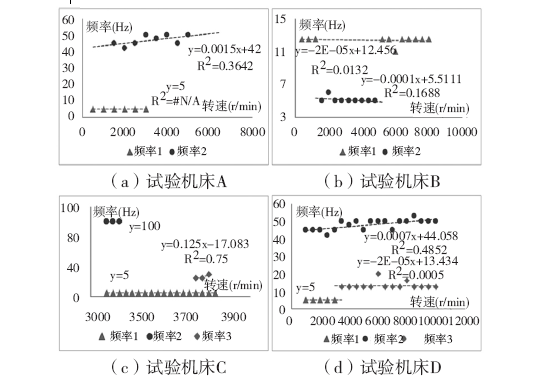
图7 各机床外激振源强迫振动频率
由图7 分析得出,各机床在一定转速范围内均可观测出一些典型外强迫振动频率。机床A 在低速范围内监测出5Hz 及42Hz 强迫振动信号; 试验机床B在0 ~ 1000r /min 及5000 ~ 8000r /min 的范围内监测出较为稳定的频率为12. 5Hz 的振动信号,在1000 ~5000r /min 的范围内监测出频率为5Hz 的振动信号;试验机床C 在全转速范围内均监测出频率为5Hz 的振动信号,在低速范围下还监测出较高频率的振动信号; 试验机床D 在各个转速下均监测出至少两种较为稳定的振动信号,分别为10Hz 及45Hz 左右。
上述结果表明基于EAKI 策略能够有效识别出各机床在全转速范围内存在的典型外激振源强迫振动类型; 同时由于工况环境不同,外激振强迫振动的分布也有差异。
4. 3 各典型强迫振动幅值分析
本试验除监测备案各机床典型强迫振动频率外,还可对各机床各类强迫振动的幅值进行分析,以更全面地表征机床强迫振动状态。结果如图8 所示。
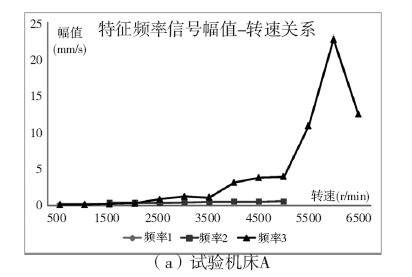
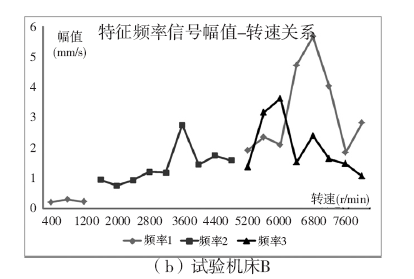
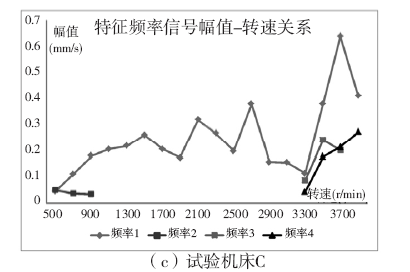
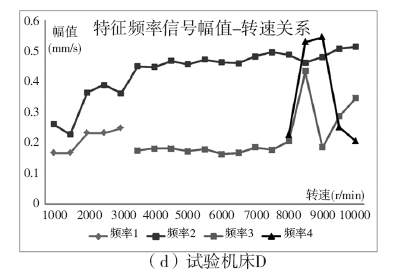
图8 各机床典型强迫振动幅值-转速关系
根据4. 2 节的分析,回转型强迫振动是一类典型振动形式,图8 中机床A、B 的频率3、机床C、D 的频率4 分别对应该类强迫振动在全转速情形下的振动幅值。图8 反映出: 第一,各机床强迫振动的主导类型不同。对于机床A,回转型强迫振动在全转速范围内均处于主导地位,对于机床B、C、D,不同转速范围内起主导作用的强迫振动类型不同; 第二,各强迫振动的影响程度不同,对应机床加工精度也有差异。机床A 回转型强迫振动幅值达20mm/s,对机床C、D 而言,在加工范围内强迫振动的幅值均小于1mm/s。
由上述结果可得出,依据EAKI 策略能够有效监测各机床强迫振动类型、幅值及影响范围,可综合全面地反映机床强迫振动状态,进而为针对每台机床构建强迫振动信号知识库形成良好基础; 同时各机床强迫振动形式各异也反映了采用EAKI 方法进行振动辨识的必要性。
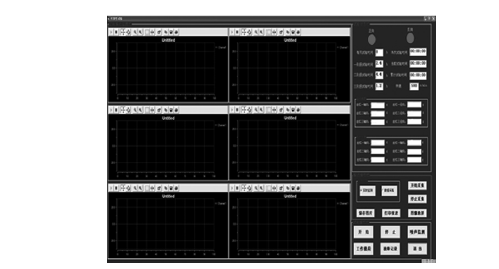
图12 试验振动监控界面
4. 4数据处理软件
本测控系统的数据处理软件采用Access 数据库设计了滚珠丝杠副可靠性信息数据库以及数据库管理软件[10],用来保存试验过程中的原始数据、数据分析结果,能很好的帮助试验人员完成试验。
5.试验台设计成果
如图13 所示,为滚珠丝杠副可靠性试验台,在机械结构的基础上,运用上文所设计的测控系统,试验台面已经可以模拟实际工况的往复运转。加载系统最大加载力为2t,拖动电机最高转速3000r /min,各传感器信号正常,能很好的完成试验的要求。
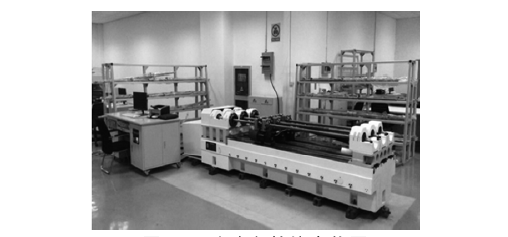
图13 试验台整体实物图
6.结束语
本文针对滚珠丝杠副可靠性试验台所需要实现的功能问题,对其测控系统进行了研究。结合试验装置,提出了试验台测控系统的设计方案,用以模拟实际工况下,被测丝杠的运转以及参数的检测功能。本文提出的滚珠丝杠副测控系统的设计方案,有利于完成丝杠的可靠性试验,为滚珠丝杠副可靠性的参数分析提供试验基础。
投稿箱:
如果您有机床行业、企业相关新闻稿件发表,或进行资讯合作,欢迎联系本网编辑部, 邮箱:skjcsc@vip.sina.com
如果您有机床行业、企业相关新闻稿件发表,或进行资讯合作,欢迎联系本网编辑部, 邮箱:skjcsc@vip.sina.com