异形零件四轴数控加工技术研究与应用
2021-3-2 来源: 天津航空机电有限公司 作者:王旭,钟洪彬,冯绍富
摘要:通过对异形零件的整体结构分析,明确加工难点,制定合理的加工工序,结合精益生产理念完成加工过程。外型加工采用四轴数控加工方法,利用CATIA-CAM数控编程模块完成前置处理加工轨迹创建,生成APT文件,利用机床后置处理技术将刀位轨迹转换成机床识别的数控加工程序,再利用VERICUT软件对加工程序刀具路径进行仿真,最后在四轴数控机床上完成加工验证。
关键词:异形零件;精益生产;四轴数控;VERICUT
本研究涉及的异形零件用于通过测量流体压差而确定流量的装置,其结构是由等直径入口段、收缩段、喉道、扩散段组成,是先收缩而后逐渐扩大的管道,测量其入口截面和最小截面处的压力差,再利用伯努利定理求出流量。目前在航空航天产品、船舶、热电、电力等领域应用广泛。具备对流体产生的阻力小,压差大、精度高、测量范围宽,稳定性好、有平滑的压差等特性。异形零件属于典型的薄壁铝合金零件,腔体壁厚为 2mm,材料切除率高达 80% 以上 , 在加工过程中极易产生变形 , 且在残余应力作用下零件很容易发生整体的弯、扭以及翘曲变形。
前期整体加工验证采用五轴数控机床完成,为对提升核心零件加工能力的整体要求,五轴整体加工周期较长,机床占用率较高。经研究改变了零件加工方案,在加工方法上进行创新,利用四轴数控编程技术代替原有的五轴加工,对三轴数控加工中心进行了改造升级成为四轴联动机床,结合多台数控车床设备将零件的加工工序进行分解,依据分解工序建立精益单元加工工位,按照精益单元的生产模式进行节拍式、动态加工和管理,形成异形零件流水加工生产线。与传统的五轴加工过程相比较,以小批10 件加工模式为例效率提升 75% 左右。其中异形零件精益单元加工过程的关键技术、难点问题集中在四轴曲面加工,异型零件腔体外表分布着形状各异的支柱接口,其尺寸精度、外观表面要求较高。同时四轴数控机床与五轴数控机床相比,机床的结构、运动特性发生改变,导致四轴机床刀具摆动、工作台旋转受限,编程难度增加。
1、异形零件结构特点描述
异形零件作为流量温度传感器的一部分,零件包含曲面、异形槽、异形安装座、圆周分布的联接螺柱和安装孔、高低压接口等特征。结构特点如图 1 所示。
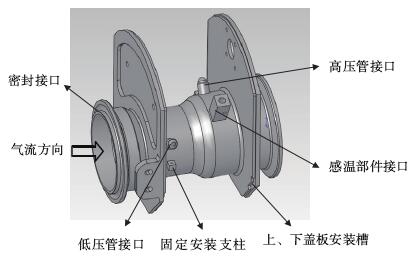
图1 异形零件结构图
①高、低压管接口 异形零件外形曲面上分布着高、低压管接口,由于气流从等直径入口段进入,经过孔径收缩变小、吼道阶段过渡,气体通过吼道的速度越大,产生的气体流量压力越小。相反经过孔径扩张变大,吼道阶段过渡,气体通过吼道的速度越小,产生的气体流量压力越大。
②固定安装支柱 高压区、低压区各一个固定安装支柱,结构尺寸一致,中心位置进行保险孔位加工,起到固定配合部件的作用。
③感温部件接口 接口尺寸与感温部件连接,内孔进行螺纹加工,支柱高度及螺纹深度与感温部件结构相关,且在感温部件接口侧后方 45°位置有保险孔位加工。起到固定配合部件的作用。
④密封接口 密封接口分为入口端和出口端,且均与密封圈连接,加工尺寸精度要求较高,确保气体流量在入口端、出口端无泄漏现象,否则会对内腔气体流量压力产生失压现象,导致高、低压管接口输出端气流压力不准确。
⑤上、下盖板安装槽 异形零件正反面平台内侧均匀分布 U 型槽,局部位置与焊接支柱连接,通过焊接加工工艺方法固定,成型后螺钉拧紧上、下盖板零件,封闭与文丘里管连接的零部件及其它测试产品。
2、精益加工过程
本研究涉及到的异形零件在加工过程中按照先粗后精,先内后外,先关键基准后其他的原则,以内孔中心轴线作为各工序的基准,减少加工过程中定位基准变换。加工工艺方法分为普车粗加工,数控车加工型腔内孔及轮廓外形曲面,四轴数控铣加工外形曲面及分布的支柱接口,工艺路线划分为:5 工序备料→ 10 工序车加工→ 15 工序数控车→ 20 工序数控车→ 25 工序数控车→ 30 工序数控铣→ 35 工序数控铣→ 40 工序数控铣→ 45 工序数控车→ 50 工序数控车→ 55 工
序钳工→ 60 工序洗涤→ 65 工序检验,加工过程示意如图 2 所示。
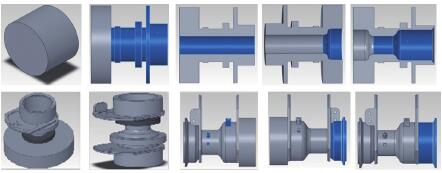
图2 加工过程示意图
精益单元加工中涉及到普通车床、数控车床CS200/66、数控车床 CS150、数控车床 CS200、立式四轴数控加工中心共 5 种设备。并创建工位动态流程如图3 所示,共计划分 6 个工位,工位 1 为普车加工、工位 2至工位 4 为数控车加工,三台设备完成 5 道数控车加工工序,工位 5 为四轴数控曲面加工,工位 6 为钳工螺纹加工等。单工序工位间以节拍间隔 3 小时开展水加工。
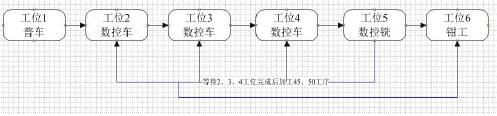
图3 工位动态流程图
3、 加工难点分析及编程创建
针对异形零件外形曲面分布的支柱接口特征,采用四轴数控编程方法加工,利用 CATIA-CAM 数控编程软件进行前置处理程序编制,在试验件加工过程中对零件的外形结构难点分析见表 1 内容:
表1 外形难点分析表
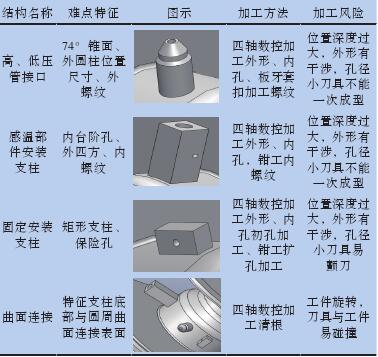
四轴数控铣加工过程装夹方式采用芯轴定位,芯轴夹紧在旋转工作台上,由 A 轴旋转带动零件在加工过程中与主轴发生联动。芯轴的定位基准参考零件回转中心轴线,依据异形零件内腔结构及尺寸公差要求,确定芯轴工作面与异形零件内壁贴合良好保持圆跳动≤ 0.01,同轴度≤ 0.02。在功能方面芯轴通过静摩擦力提供扭矩,保证切削加工稳定性;芯轴提供径向支撑力,避免切削力引起异形零件薄壁处变形。同时芯轴工作面粗糙度要在 Ra0.8 以上,表面圆滑过渡,不会对异形零件内壁划伤。其次芯轴容易安装、拆卸,四轴数控铣加工过程中与刀具无干涉问题,芯轴结构特点如图 4 所示。
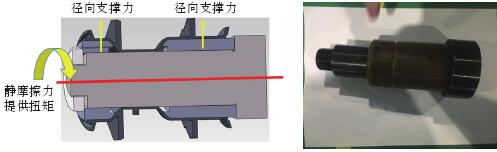
图4 芯轴结构示意图
将零件模型导入 CATIA-CAM 加工环境后,进入多轴数控加工操作界面。首先设置机床结构、加工坐标原点、零件几何体、毛坯几何体、加工安全平面[3]。其次异形零件外形曲面铣加工方法主要应用轮廓铣削、沿面铣削、4 轴定向铣削。参数设置主要包括加工参数、几何参数、刀具参数、速度参数、进退刀参数[4]。四轴曲面加工主要参数设置见表 2。参数设置完成后生产模拟加工路径,此加工过程默认工件是静止的,刀具相对于工件是运动的。通过对前置处理刀具路径模拟加工,可以分析零件加工后是否有切伤工件、过切、欠切情况,模拟验证无问题后生成前置 APT 文件,模拟加工如图 5 所示。
表2 四轴加工参数表
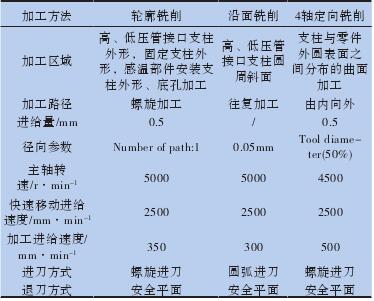
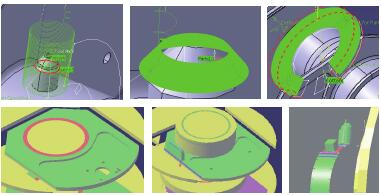
图5 模拟加工示意图
4 、 VERICUT 仿真及四轴加工验证
异形零件在四轴数控机床实际加工前增加了仿真模拟技术,利用 VERICUT 仿真软件对数控加工过程进行模拟,此过程可以消除数控程序中的错误,如切伤工件、过切、欠切、机床碰撞、刀具干涉等,还可以减少实际切削验证,提高加工效率,改善工件质量,降低生产成本。目前随着数控加工技术的发展,数控仿真技术的应用十分重要,仿真模拟加工过程可以确保数控程序的正确性和合理性[5]。
参考四轴数控机床的结构特点和运动特性 , 创建机床后置处理转换程序 , 将 CATIA-CAM 数控程序前置处理刀位文件转换成机床能够执行的 NC 数控程序 , 再导入 VERICUT 仿真模拟软件中进行验证。打开 VERICUT 仿真软件,需要在新建项目树环境中进行设置,单一工位自定义命名可验证一道数控程序。首先设置数控机床,数控机床设置包括机床控制系统,机床的结构和运动方式,行程极限与碰撞设置等参数,在VERICUT 仿真软件中系统默认若干个可以直接选用的类似机床控制系统。
机床结构要与实际加工四轴数控设备保持一致,若 VERICUT 软件中系统默认的机床结构不符合要求,需要重新创建机床机构,设置 X 轴、Y 轴、Z 轴、A 轴旋转、刀具轴、工作台及装夹、需要加工的毛坯零件,并设置运动方式将主轴连接起来,形成虚拟的运动机床结构,将需要验证加工的毛坯零件装夹到工作台面上装夹固定。然后在项目树中设置加工坐标系,此加工原点要与 CATIA-CAM 中数控编程加工的坐标原点保持一致,参考转换执行的 NC 数控程序进行坐标系偏置,在设置完成的加工坐标系右键增加偏置坐标系设置,其中 Fanuc 和 Siemens 控制系统需要在寄存器中输入 G54 ~ G59 指令。再将数控程序中需要的刀具添加到项目树中的刀具库中,刀具使用顺序与数控程序保持一致,并调整刀具补偿设置对刀点 ID 序号与刀具顺序号相同。最后将需要验证的 NC 数控程序导入到项目树中,进行验证加工。项目树结构、模拟加工后三维动态显示如图 6 所示。
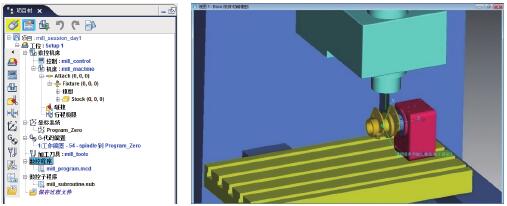
图6 仿真加工示意图
将 VERICUT 仿真验证的数控程序导入四轴数控机床,装夹好毛坯零件,设置好加工原点,刀具补偿参数实际加工验证数控程序。通过精益生产的加工过程对此类异形零件加工验证,实现了加工工艺合理化、数控程序最优化,工装夹具通用化。也为其它类型零件加工积累经验。
5、 结论
异形零件作为流量温度传感器产品的核心零件,整个加工过程难点问题主要集中在外形曲面、异形槽、异形安装座、圆周分布的联接螺柱和安装孔、高低压接口等特征,结合数控机床的结构和运动特性采用四轴数控编程技术,利用 CATIA-CAM 数控编程模块完成四轴数控铣加工程序创建,再利用 VERICUT 数控模拟仿真软件完成验证过程,保证零件过程中数控程序的准确性和合理性,最后通过四轴数控机床实际验证完成加工过程。
投稿箱:
如果您有机床行业、企业相关新闻稿件发表,或进行资讯合作,欢迎联系本网编辑部, 邮箱:skjcsc@vip.sina.com
如果您有机床行业、企业相关新闻稿件发表,或进行资讯合作,欢迎联系本网编辑部, 邮箱:skjcsc@vip.sina.com
更多相关信息