轨道交通用大型铝材构件数控龙门加工中心研制
2021-2-8 来源: 作者:
摘要:开发了一种适用于轨道交通车辆车厢用大型铝材构件加工的高速、精密数控龙门五轴加工中心。由可行性试验和有限元分析优化了 28m 超长分段床身结构以及由龙门框架、滑板工作台、高速电主轴、多功能刀库等组成的龙门加工中心整体结构,得出了电主轴输出功率、扭矩、转速适配表对控制系统进行二次开发,研发了夹紧位置的智能定位、自动夹紧、多点自动位置优化的智能夹具,提高了机床的高速移动速度和加工精度。
关键词:轨道交通车辆 铝型材构件 数控龙门加工中心
我国轨道交通制造业呈逐年高速增长的态势,新一轮的高铁、动车、地铁的建设项目正在国内外积极展开。其中,为了保证高速行驶平稳性和可靠性等,高铁、动车和地铁等轨道交通车辆用的车厢厢板、底板、裙板以及边梁等长大类零件不允许拼接,均采用整体式结构[1]。例如:如图 1所示的车辆用车厢整体结构;如图 2 所示的动车车厢厢板的大型薄壁型腔结构,其铝合金构件的长度达 23.9m制造车辆车厢用零部件所需的关键加工设备均从国外进口,特别是目前我国引进的车辆车厢用超大型铝材构件加工装备的软件升级、二次开发以及与其他 CAD/CAM 软件的兼容性上都被设置了层层障碍,并且这些产品形成的技术标准也很难与我国现行的行业标准兼容。面对不断发展的轨道交通用车厢等零部件的国际化需求,配套供应商的现有产能远远不能满足市场的需求,严重制约了我国轨道交通车辆的快速发展。市场迫切需要开发一种能替代进口的轨道交通车辆车厢用大型铝材构件的加工装备,以满足我国快速增长的轨道交通装备制造的需求。为此,本文开发了一种适用于轨道交通车辆车厢用大型铝材构件加工的高速、精密数控龙门五轴加工中心。
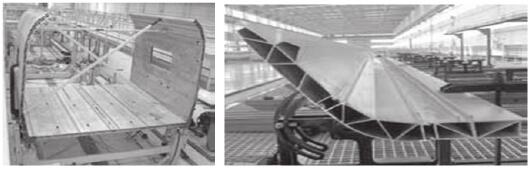
图1 轨道交通车辆 用车厢整体结构 图 2 大型薄壁型腔结构的铝材构件断面
1、数控龙门五轴加工中心总体结构
为满足图 1、图 2 的大型铝材构件的加工,开发的数控龙门五轴加工中心的结构如图 3 所示。它主要由超长分段床身、龙门框架、移动滑板、高速电主轴、多功能刀库、适用于薄壁型腔铝材构件的自动夹紧、多点自动定位的智能夹具以及采用西门子控制器的数控系统等组成。作为加工中心的基础平台,床身左右两侧安装有 X 向导轨和移动齿条。
X 向导轨上安装龙门框架,龙门框架下方的齿轮齿条机构驱动其沿 X 向前后移动。Y 向导轨上安装滑板工作台,Y 轴丝杠驱动下可以沿 Y 向左右移动。滑板工作台的Z向导轨滑块和丝杠驱动电主轴滑板上下移动。电主轴具有可绕 Z 轴旋转的 C 轴和可绕 Y 轴旋转的 B 轴,共同完成双摆运动。在龙门框架的左下方有旋转式多功能刀库。加工中心工作时,电主轴按设定速度完成刀具的旋转主运动,由 X、Y、Z、B、C 这 5 个伺服轴共同驱动双轴摆头的移动和摆转,实现五轴联动,完成全行程范围内空间任意角度和位置的加工。
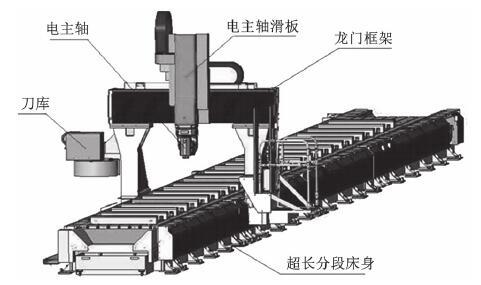
图 3 大型铝材构件数数控龙门加工中心结构示意
2、龙门五轴加工中心的关键零部件结构
2.1 28m 超长分段床身
图 4 是本立项提出的 28m 超长分段床身的结构。为便于床身加工,它分成 4 段节。为了保证床身的强度、刚度和抗扭转能力,研发的主要内容包括:分段床身的加工方法、连接方式及对接精度;如何降低对接装配的难度,减少对接时间;由试验和有限元分析,优化床身的强度、刚度和抗扭转能力,在满足刚性、抗扭钻要求的前提下进行超长床身的轻量化设计。
(1)在实验的基础上,采用有限元(ANSYS)软件分析 28m 床身的强度、刚度和稳定性,检查和鉴定床身结构的合理性。
(2)研发一种分段床身对接方法。在床身的内侧和外侧分别固定一套连接装置,以分段床身的主导轨一侧安装面为定位基准、副导轨为自由浮动的床身定位方法,并通过激光干涉仪、光学准直仪等实时确认多段床身的平行度和重合度。对接后的床身平行度和重合度分别达到了±0.02mm,满足床身导轨的使用要求,表明本文提出的床身对接方法装配精度高且简单可行。
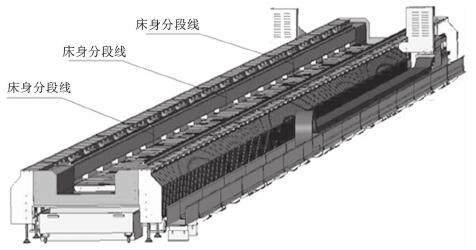
图 4 28m 超长分段对接床身结构图
2.2 龙门框架及其附属的滑板工作台、电主轴等整体结构
除图 4 的加工中心分段床身之外,图 5 的龙门加工中心整体结构主要由龙门框架、电主轴滑板工作台、高速电主轴以及多功能刀库等组成。该加工中心整体位于如图 4 所示的床身导轨之上。由于动车车厢厢板等大型加工件长度大,龙门加工中心工作状态时的固有振动特性等是评价其工作平稳性和提高加工精度的重要指标。因此,对龙门加工中心整体结构进行结构设计和模态分析获得其模态特性,是龙门加工中心整体结构优化设计必要的技术手段。图 6 是建立的龙门加工中心整体结构的有限元模型。有限元网格设定为绑定接触,在接触面或接触边之间不存在切向的相对滑动或法向的相对分离,以使得接触面上网格节点错开,减少网格数量。选定龙门加工中心的双立柱、横梁和电主轴等零部件的材料为结构钢,弹性模量为200GPa,密度为 7850kg/m3,泊松比为 0.3。计算时,考虑到龙门框架及其附属的滑板工作台、电主轴等整体结构自重产生的预应力,采用带预应力的模态分析方法,即先对整个加工中心进行预应力分析,再以该预应力分析结果作为模态分析的初始和边界条件进行了模态分析,得到了龙门加工中心整体结构的前六阶模态频率及振动特性等,图7 和图 8 分别是第 5 阶和第 6 阶模态振型[2]。将上述分析结果与电主轴电机频率比较,可知电主轴电机的频率和模态分析中的第 6 阶模态频率比较接近。因此,为避免高速主轴电机与龙门加工中心整体结构产生共振,有必要对龙门框架、滑板工作台等进行相应的结构改进。改进后的整体结构提高了机床移动速度和响应速度,保证了高速切削稳定性。
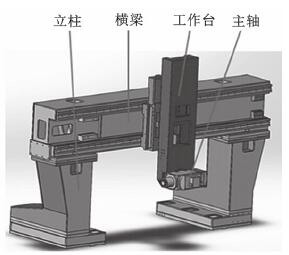
图 5 龙门加工中心整体结构
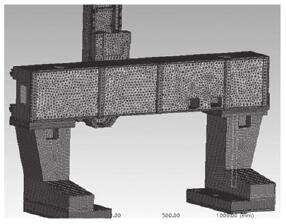
图 6 龙门加工中心有限元模型
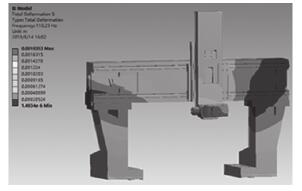
图 7 第 5 阶振型(电主轴振动)
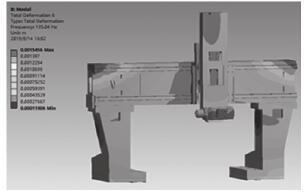
图 8 第 6 阶振型(电主轴振动、双立柱扭摆)
2.3 高速电主轴运转参数
使用三坐标测量仪、粗糙度测量仪以及扭矩仪等检测设备,测定主轴转速、扭矩、进给量之间的配合关系,并通过可行性试验和仿真分析确认高速电主轴运转参数的适配性,得出了表 1 所示的高速电主轴输出功率、扭矩、转速适配表,优化了不同转速下的电主轴输出关系。表 1 中,S1为额定输出,S6为 60% 超载输出。
2.4 自动夹紧、多点自动位置优化的智能夹具
图 9 是研发的适用于薄壁型腔的大型铝材构件的自动夹紧、多点自动位置优化的智能夹具。为防止轨道交通用大型铝材构件由于长度过长造成弯曲变形,有必要采用多组可移动夹具对工件进行支撑。按照工艺要求摆放各组夹具工作效率低,且易造成切削刀具和工作台夹具干涉。为此,针对不同规格的大型铝材构件,在实验验证的基础上,采用 Adams 进行仿真分析,在非加工区域确定最优夹紧点的位置。借助 Simulink 的框图设计环境,对控制系统进行二次开发,由专用软件给出准确夹具位置,由数控系统的X 轴驱动夹紧拨快,拖动每组夹具移动到预定位置,实现根据图纸工艺自动拨动夹具并优化夹具位置的功能。
表 1 高速电主轴输出功率、扭矩、转速适配表

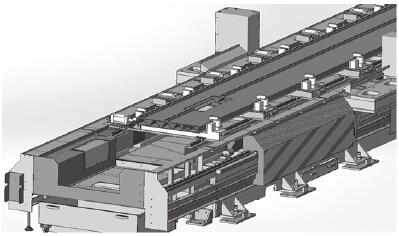
图 9 机床智能夹具结构图
2.5 控制系统的软件二次开发
原有的加工程序是由经验丰富的工艺员依据待加工件图纸手工编制而成。为提高数控加工中心的自动化程度,本文在西门子控制系统基础上二次开发了一种能根据工件图纸自动生成加工程序的软件。针对大型铝型材构件以铣削、钻削为主要加工工艺,加工图元以孔槽、立筋去除为主要技术特征,并且在铝型材多个面都有加工要求的特点,开发了针对大型铝型材构件的任意角度均能实现以上工艺功能的 CAM 软件。将常用的图元及图元组模块化,需要时直接调用,采用填表式参数对话框,对所有切削工艺参数及位置切削参数均采用弹出式图表菜单形式,可直接填写参数,直观易懂,保障了机床较高的工作效率和加工精度。同时,通过软件功能的扩展,提高了机床的操控便利性和人际交互界面的友好程度。
3、结语
本文研发了一种适用于轨道交通车辆车厢用大型铝材构件加工的高速、精密数控龙门五轴加工中心。由可行性试验和有限元分析优化了 28m 超长分段床身结构、由龙门框架、滑板工作台、高速电主轴、多功能刀库等组成的门加工中心整体结构,得出了电主轴输出功率、扭矩、转速适配表对控制系统进行二次开发。通过软件功能的扩展,实现了夹紧位置的智能定位、自动夹紧,提高了机床的高速移动速度、加工精度以及人机交互界面的友好程度。完成的产品主要技术指标如下:分段床身总长度 28m;大型铝材构件加工长度≥ 26m;最大加工宽度为 1100mm;电主轴最高转速为 18000r/m;最大输出扭矩为 20.9/6000N·m;最大切削速度为 5m/min;最大快移速度为 55/30/20m/min。
来源:
周倩刘 新海 亓爱林 闫法义 郑明刚 许伯彦
济南天辰铝机股份有限公司 山东建筑大学 机电工程学院
投稿箱:
如果您有机床行业、企业相关新闻稿件发表,或进行资讯合作,欢迎联系本网编辑部, 邮箱:skjcsc@vip.sina.com
如果您有机床行业、企业相关新闻稿件发表,或进行资讯合作,欢迎联系本网编辑部, 邮箱:skjcsc@vip.sina.com
更多相关信息