GMCu系列桥式五轴加工中心的研发与应用
2021-1-21 来源:沈阳机床集团沈阳中捷航空航天机床有限公司 作者: 白旭 姜楠
一、概述
近年来,我国航空航天事业发展迅猛,但受加工装备的限制,部分核心关键零部件仍需依赖进口,而提高基础加工装备水平是减小进口依赖的关键环节。航空航天行业最新的发展趋势是采用先进的整体结构件和大型复材结构件设计,相关结构件具有尺寸大、壁薄、易变形,零件精度高,切削中刀路线复杂、协调面、交点孔多等工艺特点,对机床的加工范围、加工效率、动态性能都提出极高的要求。因此,必须采用五轴联动加工,尤其大行程高精度五轴联动加工,用以满足对航空航天结构件高效、高精的加工需求。桥式五轴加工中心以其独具的结构特性,在众多五轴机床中脱颖而出,桥式加工中心具有优异的动态响应能力,在保证高加速、高进给的同时,机床精度也能够严格控制,因此桥式五轴加工中心成为广泛应用于高精尖航空航天大型结构件加
工的行业重器。
我公司针对航空航天大型复杂结构件的加工需求,开发了GMCu系列桥式五轴加工中心,解决了客户最大加工宽度5.5m,最大长度22m的结构件加工难题。GMCu系列产品机型种类齐备,采用模块化设计,便于组织生产和缩短供货周期。产品可根据客户需求做选配定制,可选配超大行程、高性能配置、护顶吸尘、配套组线等。可替代国外同类别进口产品。GMCu系列桥式五轴加工中心对口航空航天、复材加工、轨道交通等行业,彻底打破了国外设备在此类领域的垄断地位,为国产机床占领高端机床市场、掌握制造核心技术做出了贡献。
二、GMCu系列桥式五轴加工中心介绍
1.机床简介
GMCu系列桥式五轴加工中心桥梁(见图1)采用采用高架桥式框架结构,主轴箱侧挂布局。设备床身,工作台固定,横梁在床身上沿水平方向前后移动(X轴),滑板在横梁上沿水平方向左右移动(Y轴),滑枕沿滑板上下移动(Z轴)。铣头为叉式结构,能绕X轴摆动(A轴)、绕Z轴转动(C轴),实现五轴联动。
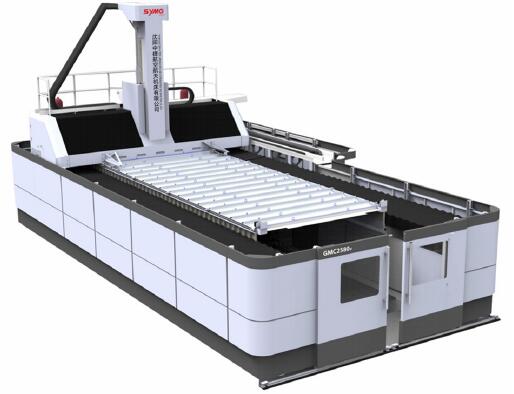
图1
机床整体结构对称布局,受力均匀,赋予机床更高的稳定性和抗载能力,驱动部件重量与刚性匹配合理,机床基础件(桥梁\工作台)全部采用优质铸铁,强度高且吸震效果好,横梁及主轴箱移动采用双电机驱动,精度高加速度大。滑枕两侧布置双平衡油缸,与蓄能器相连接,平衡比例90%,惯量匹配可达到1,加速度达到3m/s2,动态响应极高。机床布置温控系统,包括各向丝杠的轴承座的控温、丝母座控温、A/C轴电机的冷却和电主轴的冷却,温控系统控制集成在数控系统内,由可调温的水冷机控制机床所有关键部件温度在合理变化范围。
2.机床技术参数(见附表)
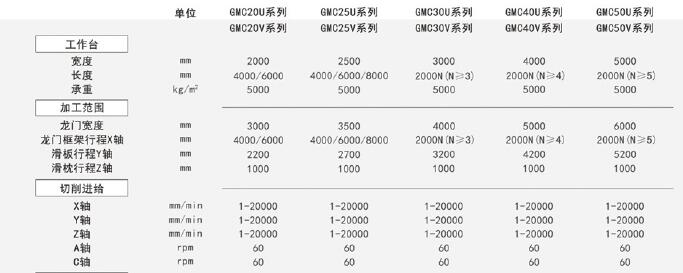
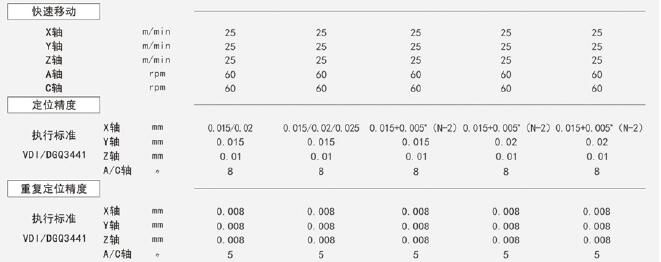
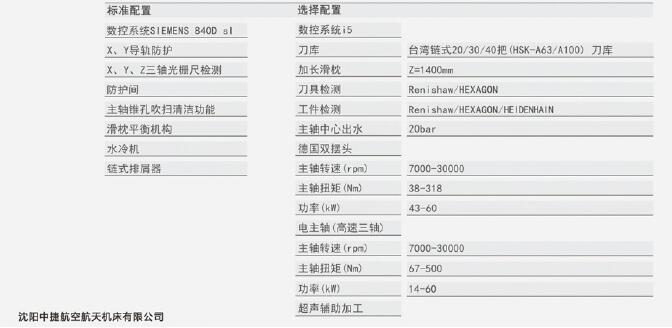
三、机床先进技术与应用情况
1.桥式横梁挠度补偿的研究
随着机床跨距的增加,横梁部件的挠度变形愈加突出,直接关系到零件加工质量及可靠性,尤其是加工航空航天领域结构件时,由于零件的尺寸大且壁薄,横梁的变形会对零件加工质量的影响无限放大,横梁的挠曲变形很可能导致零件成为废品。为此,有必要着力对横梁进行仿形研究,评估其变形曲线,进而选择合适的材质、最优的结构布局、合理的温度控制、反向仿形加工以及系统补偿等措施尽可能地消除横梁的自身变形,保证整机加工时横梁的可靠性。
在确定材质结构等条件后可通过对比横梁虚拟仿真计算和实际检测结果,得出与变形曲线趋势相反的实际导轨加工曲线,以实现抵抗横梁自重及负载变形,即通过预先计算好的加工“变形量”抵抗其承载作用变形;通过实测数据,对虚拟计算模型进行了反复的修改,并最终保障计算模型的准确性和通用性。最终在优化仿真过程中得到横梁最优的筋型布局,图2为横梁有限元分析示例。
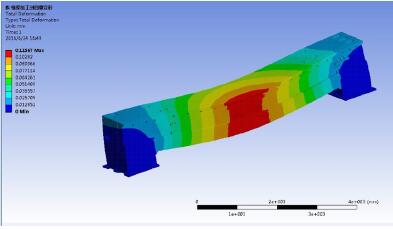
图2 横梁分析
2.整机的热稳定性研究
由于数控机床各组成部件的材料不同,热膨胀系数不同,因此在环境变化的过程中升温就不同,产生的热膨胀量也就不同;由温度变化所引起的机床零部件热变形导致机床精度受到影响,这一直是大型数控机床所面临的难题。大型桥式五轴加工中心热变形补偿技术的难点之一在于数控机床热变形分析:在加工零部件的过程中,需要认真分析机床在运行过程中产生的热变形,例如:轴承高速运转过程中的热量传递到丝杠,电机高速运转产生的热量传递到丝杠,丝杠与滚珠直接摩擦所产生的热量,都会导致丝杠受热变形,从而影响丝杠传动精度,导致加工精度偏差;难点之二在于热变形位移数据的采集:机床热变形引起的加工误差不能直接测量获得,需要将传感器放置机床各结构件随温度变化的敏感处,将获得数据录入材料库以方便对数据进行收集比
对;难点之三在于热变形量的补偿:需要采用将热变形误差补偿到系统中,通过补偿平台的搭建,根据机床的实际情况,反复试验测定过的温度差与机械的形变值关系,利用系统将机床运行坐标定位精准,使加工精度得以保证。
整机的热稳定性研究的主要包括影响整机热源分析、机床大型零部件热变形分析、各部件温度采集分析、整机热变形误差补偿技术研究等内容;整机的热稳定性研究涵盖整机热源、传导、变形效果采集的全过程,进一步对数据进行分析,最终通过热变形误差补偿技术消弱整机受热变形的影响,进而提高整机精度性能指标。
3.护顶防护及吸尘装置的研究
加工复合材料时,会产生大量飞末及粉尘,影响零件加工精度,破坏车间环境,同时对机床性能及稳定性产生不利影响。这就要求复合材料加工时配备完备的密封系统及除尘系统。相对密闭的防护间、全程除尘,防油处理等是复合材料数控加工的装备的关键点。国际上,加工复合材料的设备大多来自德国和美国,而国内企业进口此类尖端设备往往受到技术限制。GMCu系列复合材料桥式五轴加工中心采用桥式框架结构,配置超大跨距护顶防护,护顶拉罩选择先进的防静电材料防止粉尘吸附,护顶配置自动吸合随动开闭机构,做到完全自动化。开发摆头随动吸尘、正压密封、随动监控等新技术,解决了复合材料加工的"痛点"。示例如图3所示护顶示意。
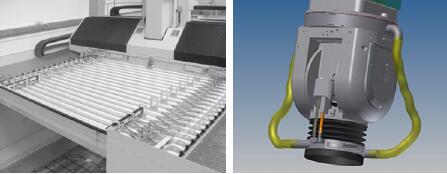
图3
4.桥式五轴空间综合误差补偿研究
高精度桥式五轴加工中心包含X、Y、Z三个直线轴和A/C两个旋转轴(见图4),存在多达数十项几何误差,根据其各项误差值,计算并反映出运行时刀具中心点 (TCP) 的空间总误差。在机床运行时,根据补偿范围对应的各个已知的几何偏差,将各独立位置的偏差数值进行统计汇总,运用数控系统计算出运行时刀具中心点(TCP)的总误差。根据总误差的数值,通过数控系统更改要临近的设定点坐标,补偿计算出的偏差,使刀具中心点尽可能精确地到达数控程序中预设的设定位置,从而能够大幅提升机床及加工的精度。
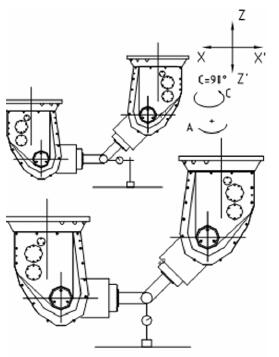
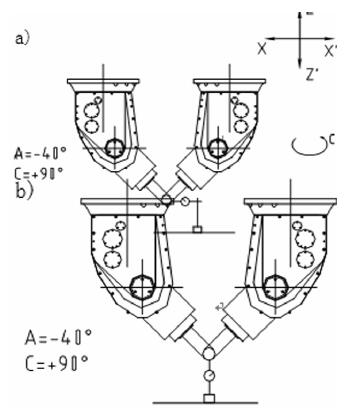
图4 刀具误差测量
5.动刚度优化与抑振技术
衡量机床结构抗振能力的常用主要指标是动刚度。动刚度在数值上等于机床结构产生单位振幅所需的激振力,动刚度越大,则机床结构在一定激振力作用下,产生的振幅越小,其抗振能力越好;反之,抗振能力越差。实际设计中在提高结构的动刚度的同时,还应获得经济合理的结构,通过找出结构刚度过高而造成浪费的部分和刚度不足而限制机床工作能力的部分,使其动刚度得到合理的分配,从而达到抑振的目的。首先,合理设计结构的断面形状和尺寸,主要受扭矩的构件应使截面形状为圆形或接近正方形,在设计横梁、滑枕外壳及滑枕时,采用增加截面轮廓尺寸而不增加壁厚,使之在相同重量下具有较高的刚度和固有频率的方式,结合有限元分析对比多种截面形式,根据分析结论,采用变形量最小,机构形式最优的的截面形式来增加机床定刚度(见图5)。其次,调整振源频率,避免激振力产生的频率与机床系统的固有频率接近而产生共振。通过改变电机的极对数和电源频率来改变电动机的转速,并通过改变机床中主轴的转速等措施,使其避开共振区,此外减小电机转动引起的振动,将机床的电机与驱动部件进行柔性联接,隔离电机本身振动。之后,通过预拉伸的方法消除丝杠间隙,采用双电机消隙的方法,消除齿轮齿条的间隙,来提升系统的刚度和固有频率,防止共振的产生,减小受迫振动。
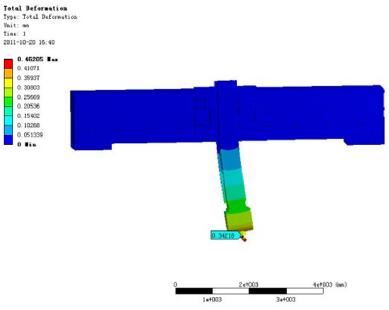
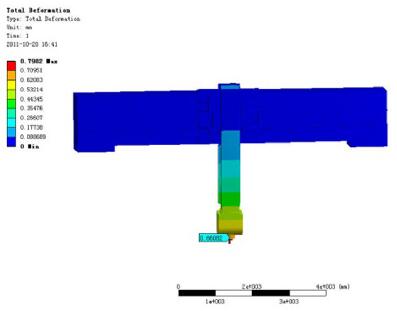
图5
6.碰撞保护的技术
主要采用“负载检测”和“传感器检测”两类技术手段。采用“异常负载检测功能”实现碰撞保护时,不但在编程和操作错误时对机床进行保护,同时对加工过程中因刀具磨损和工件振动产生的异常负载也能起到保护作用,有效地避免了机床加工过程中不可预料错误的发生,降低了机床维修成本,提高了机床精度。异常负载检测防碰撞调试主要针对伺服轴和主轴两部分来进行,伺服系统的高速采样周期对施加到电机上的外力干扰负载扭矩进行实时地观测和计算,机床发生碰撞的时候,电机承受的外力扭矩突然增大,伺服系统将此时电机承受的外力扭矩与在系统内部设置的碰撞发生时机床能够承受的外力扭矩的最大值相比较。如果小于设置的外力扭矩的最大值,系统正常运行。如果大于设置的外力扭矩的最大值,伺服系统产生报警,同时伺服系统向伺服电机发出指令,使伺服电机向相反的方向运动,机械系统与工件碰撞面脱离,从而对机床起到保护作用。另一种方式是采用“传感器信号”采集频率频率、振幅和加速度等,将传感器布置在主轴端及驱动轴硬限位附近,通过传感器生成的模拟量信号分析当前机床的运动状态。从而得出机床是否发生碰撞,通过控制系统及时作出反馈,使伺服轴向相反的方向运动,机械系统与工件碰撞面脱离,从而对机床起到保护作用。
四、成果应用及推广情况
经过多年的经验积累与技术革新,目前我公司GMCu系列桥式五轴产品在我国多个核心领域有成熟应用。在航空领域应用于我国多家飞机制造企业的生产,主要针对飞机框梁类结构件、壁板类结构件等航空铝材料的高精度高效五轴加工;在复材加工领域与我国多家科研院所合作,用于玻璃纤维材料、碳纤维材料的复杂曲面加工;在航天领域应用于高精度火箭储箱加工及结构件加工;在轨道交通领域应用于车辆制造厂,针对于高铁箱体结构件、板梁类零件的加工。
总之,从各方面需求来看,我国都需要更加优秀的国产高档大型五轴数控加工设备来解决国内产能有限以及外国技术封锁难题。我公司愿同机床行业友仁一道,为国家重点领域建设和国防工业提供更有力的技术保障与装备支持,为祖国的工业发展贡献力量。
投稿箱:
如果您有机床行业、企业相关新闻稿件发表,或进行资讯合作,欢迎联系本网编辑部, 邮箱:skjcsc@vip.sina.com
如果您有机床行业、企业相关新闻稿件发表,或进行资讯合作,欢迎联系本网编辑部, 邮箱:skjcsc@vip.sina.com
更多相关信息