误操作导致自动换刀系统故障典型案例分析
2024-7-22 来源: 中航西安飞机工业集团股份有限公司设备厂 作者:蔚腾,陈国良,卢西宁
摘要:针对数控加工中心由于操作不当引起的自动换刀机构典型故障,分析故障产生的原因和排除方法,提出预防该类型故障的有效措施。
关键词:数控加工中心;自动换刀;刀具管理;刀长
0 引言
作为工业母机,数控机床的应用越来越广泛,实际维修中经常遇到由于操作不当引发的设备故障。特别是对于具备自动换刀功能的机床,由于操作不当造成刀具参数错误引发的设故障,轻则造成工件超差,更有造成设备损坏的巨大风险。
1、换刀子程序重名引起机床换刀动作异常
1.1 故障现象
一台操作系统为 Sinumerik 84OD SL 的加工中心在进行自动刀具交换时动作异常,输入换刀指令 TXX 后,机床 Z 轴未像正常情况抬高至 Z 轴预设的换刀点,而是向工作台方向快速进给,并且主轴开始高速旋转,紧急按下急停按钮终止 Z 轴的继续进给才避免了铣伤工件、损伤主轴的重大设备事故。
1.2 故障分析与排除
维修人员利用发生故障的程序对故障现象进行复原再现。
为了保证设备和人员安全,在输入换刀指令调用换刀子程序进行换刀之前,激活机床的单段进给“Signal Block”模式,并将进给倍率旋至 10%挡位。在进行测试时发现,在进行换刀动作时,Z 轴沿负方向进给并且伴随主轴高速旋转。继续测试发现 Z 轴降低一定高度后不再继续进给,但主轴依然高速旋转,按下“CycleStart”按键继续单歩运行,发现机床 3 个坐标均开始发生位移。
多次按下“Cycle Start”按键继续进行测试观察,发现机床工作台运动轨迹近似于正在加工的工件,经分析判断此时机床在进行自动加工,运行程序为将要加工的下一道工件程序。
询问操作人员机床发生故障之前的操作行为,得知加工的工件为批量产品,工作台面上同时阵列布局 8 个工件,其加工程序相同,只是起到点有差别。通过改变工件原点来进行自动加工,为了便于调用加工子程序,加工时不断更改程序名为 L1、L2 至L6,发生故障时刚好加工至第 5 个工件,在执行换刀指令时发生了上述故障,西门子系统默认换刀子程序名为 L6,机床厂家会编译一个换刀子程序便于使用,该程序通常存储在“Manufacture”文件夹下,标准 L6 子程序一般包含 3 部分,如图 1 所示:
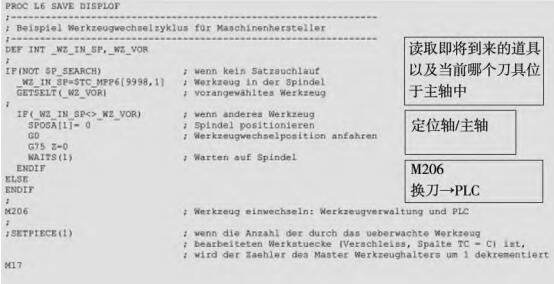
图 1 L6 换刀子程序示例
西门子系统可通过调用 M6 指令、调用 L6 子程序和直接调用目标刀具名 T=“xx”三种方式实现自动刀具交换。在本例中,加工子程序执行到 M6 代码时,激活机床自动换刀功能。故障原因是由于操作人员新命名的 L6 子程序和西门子数控系统的换刀子程序 L6 重名,因此在执行第 5 个子程序 L5 时,当执行换
刀指令时,数控系统直接调用了操作人员新命名的存储于用户加工程序“workpiece”目录下的 L6 加工子程序,导致机床换刀动作异常。重新命名加工子程序后再执行换刀指令,机床顺利完成目标刀具的更换,故障排除。
1.3 故障反思
西门子数控系统 L6 子程序为自动换刀专用名称(西门子系统NC 参数 MD10716 定义,默认值“L6”),通常存储于 Manufacture 循环目录下,在系统执行换刀指令时进行调用。而在这一案例中,操作人员在“工件”目录下建立了一个同名的 L6 加工子程序,导致在进行换刀动作时发生错误调用。针对这一间题,对操作人员进行了培训。同时需要注意的是,西门子系统还有一些用户变量和系统变量都有特殊定义,需要操作人员了解,防止由于重复命名引起设备故障。
2、换刀交换时终止程序致主轴刀具刀长丢失
2.1 故障现象
一台操作系统为 Sinumerik 84OD SL 的加工中心在加工工件时发生故障,主轴刀具撞上加工工件造成刀具断裂、正在加工的产品报废的严重后果。
2.2 故障分析与排除
通过现场模拟对故障现象进行复原再现,发现在加工时刀具路径与发生故障时一致。经询问操作人员,该程序为定型程序确认无误,且在发生报警之前采用该程序进行了一次粗加工,在开始进行精加工运行 2 min 左右就发生了事故。对该设备故障进行分析,发现机床当前主轴刀具刀长(在 Z 轴方向的长度)值为“0”,检查机床设定有效零偏后确认刀长设定值同样为“0”。由于机床主轴刀具有效刀长和实际刀具长度数值相差250.95 mm,因此在加工时 Z 轴向下多进给了 250.95 mm,导致发生设备事故。
经检查确认当前主轴刀具刀号正确无误,但是加工界面下的刀长“0”和刀具管理界面下的该刀具定义的刀长“250.95”不一致。根据操作人员描述,在发生故障前刚进行过一次粗加工,完成后进行了一次刀具测量动作,然后采用同一刀具进行精加工,因此无法确定何时刀具长度丢失。
通过试验,执行换刀命令来更换其他刀具进行测试,刀号和刀长都正确,重新换回发生故障的刀具后刀具刀长变为“250.95”,一切正常。其后继续进行了 4 h 机床空运行对机床换刀动作进行反复测试,模拟可能引起故障的条件,但都未能再现上述故障。
查看机床报警记录,确认机床发生故障前 24 h 内无报警发生,该机床连接有 MES 系统用来监控机床运行状态。打开MES系统运行记录发现机床运行状态基本和操作人员描述一致。在发生报警之前 4 h 机床进行过 2 次短暂的 MDA 运行,其后机床待机 30 min(此时操作人员在进行工件装夹)。采用发生故障时的程序进行了 2 h 左右的加工,再停机 3 min 又有一条只执行了3 s 的程序(程序名:_MA_JOG_STEP1_MPF)调用记录(这与操作人员描述有偏差),引起了维修人员的注意。再结合其后维修测试时的记录,可确认每执行一次刀具交换都会产生一条调用该程序的记录,但是不同的是,其后测试时程序的执行时间在15~45 s 内,这是由于刀具交换时目标刀具在刀库位置不同引起。但是在发生故障前的这一换刀动作纪录仅为3 s,明显存在异常。通过查找资料,在执行换刀指令时,系统会根据程序的执行情况对主轴刀具长度进行实时赋值,主要参数见表 1。
表 1 自动刀具交换时主轴刀长参数
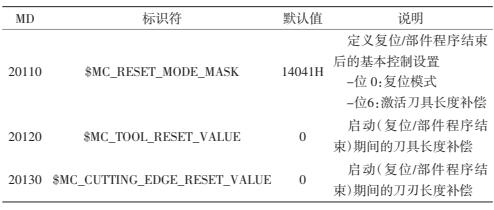
模拟该条记录作如下测试:在执行换刀命令后 3 s 时按下“Reset”按键终止换刀程序,机床未发生任何报警,MES 系统会产生一条该程序时长 3 s 的调用记录。由于程序未执行完毕,系统在程序复位时根据参数 20120 设定的默认值“0”将主轴刀长设置为“0”,而不是正常程序执行完毕后激活刀具长度补偿的“250.95”,这是造成故障发生的原因。
2.3 解决方法
针对这一问题,对操作人员进行了培训,并完善了安全操作规程,以杜绝由于人员误操作导致的事故。
3、忽视刀库异常报警导致刀具错误调用
3.1 故障现象
一台操作系统为 Sinumerik 828D SL 的加工中心在加工时发生故障,主轴刀具刀长异常造成刀具断裂、加工工件报废的严重后果。经过检查发现当前主轴刀具刀号正确,但是实际刀长和刀具管理界面刀具列表的设定值存在偏差,操作人员再次检查确认当前主轴刀具并不是目标刀具。
3.2 故障分析与排除
查看机床报警记录,发现机床在发生故障前有过一次报警记录,提示刀库刀具计数开关信号异常。询问操作人员得知该报警提示发生时为黒色对话框,机床可以正常进给,因此操作人员在进行故障复位后继续进行后续加工。发生故障的原因是操作人员未对机床报警进行正确处理从而引起刀具管理功能数据紊乱。
西门子系统 OPERATOR 人机界面的刀具管理功能对机床刀库和刀具信息进行实时管理,如图 2 所示。
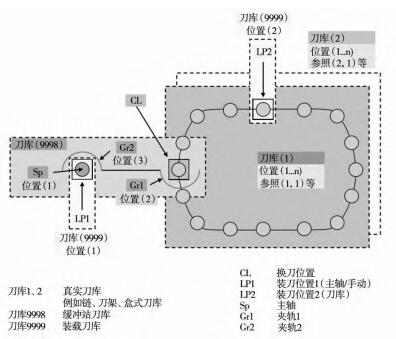
图 2 刀具管理定义的刀库示意图
该机床为 24 把刀的链式刀库,预选刀动作通过异步电机和刀库零位检测开关、刀具计数开关控制。每转过一个刀位,计数开关触发一次并实时更改刀具管理系统的刀具信息参数。当机床提示刀库计数开关信号异常时,系统无法准确计算出实际刀库转过的刀位数,而操作人员未及时停机并告知维修人员检修。在进行下次刀具交换之前机床可以正常运行,当再次执行换刀动作时,由于刀库计数开关信号异常导致机床在刀具寻址时发生偏差,所选择刀具并不是目标刀具,但是数控系统并不能对此错误做出判断,导致机床换刀动作可以正常进行,但是实际刀具是错误的刀具,刀长发生改变引起工件的损伤。
经检查,刀具计数开关存在松动现象,重新紧固该开关并执行机床刀库回零动作,建立正确刀具列表,再次执行换刀动作刀具自动交换动作正常。
3.3 解决方法
该故障的发生是由于操作人员在机床发生报警时忽视机床报警信息而草率进行了复位确认,因此对操作人员进行培训并完善安全操作规程。通过修改 PLC 程序,提高该报警响应级别,在发生该报警时切断机床进给,杜绝由于误操作引发事故。
4、结语
随着数控技术的不断发展,数控系统的开放性越来越高,给机床厂家和操作人员提供了更多的权限和空间,这对机床操作人员技能水平提出了更高的要求。误操作会导致机床报警甚至发生设备损伤事故,因此对于操作人员培训和管理亟待加强,同时需要通过技术手段来规避误操作造成的隐患。
投稿箱:
如果您有机床行业、企业相关新闻稿件发表,或进行资讯合作,欢迎联系本网编辑部, 邮箱:skjcsc@vip.sina.com
如果您有机床行业、企业相关新闻稿件发表,或进行资讯合作,欢迎联系本网编辑部, 邮箱:skjcsc@vip.sina.com
更多相关信息