【数控机床】某数控机床Z轴异响故障诊断及维修
2020-12-22 来源:中国工程物理研究院机械制造工艺研究所 作者:余刚;刘进
摘要:随着数控机床在加工领域得到迅速地普及,随之而来的即使数控机床的故障诊断和维修,数控机床是集成机械、电气、液压以及气动控制等领域一个复杂机电产品,所面临的维修问题更加复杂。本文介绍了某机床Z轴异响故障的故障诊断流程以及维修方法,首先通过“望、闻、问、听”定位故障位置,然后通过分析数控加工程序、电气伺服参数以及机械结构排查确定故障原因,最后确定了维修方案和方法。本文提供的机床故障诊断以及维修方案可为其他故障维修提供参考。
关键词:数控机床;滑动导轨;故障维修
1、概述
随着科技的发展,数控技术得到飞速的发展,数控机床作为其他高精设备的加工母机,在加工制造行业占有重要的地位。在年限使用久的机床,进给轴的异响振动故障现象有发生,已成为一个常见频发故障。某数控龙门加工中心是车间的重要设备,投入使用年限长。机床使用过程中,该加工中心 Z 轴速度不稳定,移动到端部时存在振动、抖动的现象。机床加工过程中工件表面出现明显的刀纹,表面质量不合格,已经严重影响数控设备正常使用。
2、故障定位
2.1 故障现象
该数控机床的加工的产品出现明显的刀纹现象,工件表面粗糙度不合格。通过常规的“望、闻、问、听”的故障诊断手段,发现该机床 Z 轴有明显的异响和振动现象,同时通过控制进给 Z 轴在手动方式下进行移动,移动过程中 Z 轴出现振动异响现象,同时当 Z 轴在端部移动时振动和异响更加明显。
该机床的 Z 轴驱动为交流伺服电机驱动滚珠丝杠进行移动,丝杠轴承的支撑方式为“一端固定,一端支撑”的方式,固定支撑的轴承采用角接触轴承,支撑轴承采用深沟球轴承,Z 轴的支撑方式为滑动导轨。
2.2 故障定位流程
按照维修的思路,提出以下如图 1 所示的故障诊断流程。数控机床进给轴振动、异响的原因有多种情况,依次按照加工程序问题、电气伺服参数、机械结构等流程排出定位机床故障原因。通过该流程的分析流程,可由易到难、由简到繁的顺序排出故障原因。

图 1 故障诊断流程
在程序方面,振动故障常发生于机床加工程序中编写曲线中小线段多,可通过优化修改加工程序,改善进给轴振动情况。
伺服参数方面,进给轴振动的原因有 :速度环参数不匹配引起振动 ;位置环参数不匹配引起振动 ;检测元件故障,编码器和光栅尺故障。通过优化设置相关参数可以盖上情况。
机械结构方面 :导轨副运动阻力大,润滑不良 ;丝杠预紧力不足、弯曲 ;丝杠轴向有窜动间隙 ;丝杠轴承磨损 ;压板与导轨不平行 ;电机与传动轴间连接松动 ;电机本身机械方面故障,轴承磨损等众多原因将导致机床进给轴振动故障。
3、故障分析及处理
3.1 故障分析过程
机床进给轴产生振动、异响有很多种可能,依据维修经验以及故障排查流程,定位故障的根源。通过对操作者的询问和现场观察实验,机床 Z 轴振动明显。通过检查加工程序、加工工件材料、加工进给量等方面,排查了加工程序没有问题。接着排查电气控制伺服参数匹配,光栅尺检测元件的末端是否损坏,最后从机械方面排查镶条和导轨侧面接触面是否符合要求,压板和导轨正面接触是否符合要求。
3.2 伺服参数排查
伺服参数优化方面,按照自动优化过程进行优化:JOG、MENU、调试、优化测试、自动优化、所选轴、优化、确认、启动测量、循环启动、高频、低频、DNS。
优化完成后,在手动和自动状态下分别进行 Z 轴移动,在不同的速度下进行移动,振动、异响未消除。于是参数进行手动修改。每修改一个或者多个参数,在手动和自动状态下分别进行 Z 轴移动,在不同的速度下进行移动,振动、异响未消除。
通过自动和手动伺服参数匹配优化和修改,该故障现象未发生改善,排除电气参数不匹配的原因。另一方面,将全闭环改为半闭环进行电气参数的排除,进入调整页面,屏蔽 Z 轴。进行机床运行,发现机床振动和异响存在,同时排除了电气故障。
3.3 机械方面排查
通过电气控制参数的优化以及排查,故障定位导向于 Z 轴的机械结构,通过观察和触碰 Z 轴滚珠丝杠驱动和滑动导轨支撑,判断为 Z 轴滑动导轨振动明显,确定为振动源。
滑动导轨镶条排查,将镶条松开,在手动和自动状态下分别进行 Z 轴移动,在不同的速度下进行移动,振动、异响依旧存在。
如图 2 所示,滑动导轨压板检查,将压板的螺钉松开,移动 Z 轴,异响和振动现象明显改善。将压板锁紧,异响故障进行了重现,于是判断故障的原因在压板与导轨之间产生,判断为滑动导轨之间间隙过小导致压板与导轨之间摩擦导致异响和振动。初步判断为 Z 轴导轨压板长期使用过程导轨表面出现磨损,中间隙过小。
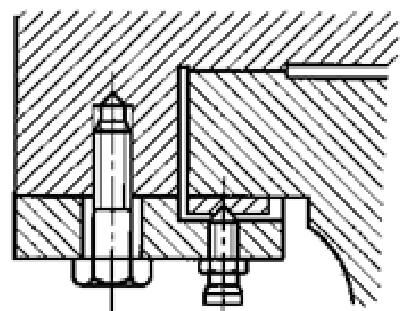
图 2 滑动导轨
4、故障维修
通过对导轨和压板的检查,压板本身的平面度大于 0.02 mm,不能满足使用要求。通过修复压板的平面度,注意压板的高低点的分布、压板刮研量的大小和区域,刮研的方法与检测方法。
4.1 维修过程
4.1.1 确定压板高低点
确定压板的接触面及高低点的分布。将压板接触面打上红丹粉,带上螺钉,轻轻的紧固。机床的 Z 轴沿一个方向运动,观察压板与镶块的接触点。通过镶块的红丹粉的分布确定了压板的高低点位置,做上标记。
4.1.2 确定压板刮研量
将两边压板都装上,在靠近操作者这方的压板下添加铜皮,添加铜皮由 0.01 mm ~ 0.10 mm 进行测试。使用测力扳手将压板每颗螺钉都用 100 Nm(厂家给定值)的力均布锁紧。通过移动 Z 轴看是否有异响。如果有异响就将铜皮进行更换,调整到移动 Z 轴没有异响即可。最后铜皮的厚度,厚度为 0.04 mm,即可确定刮研量为 0.04 mm。
4.2.3 压板刮研步骤
通过确定压板的高低点以及刮研量,将压板进行刮研。如图3,通过检查确定压板的高点和压板的初始尺寸,为刮研后检测进行对比。将压板上涂上红丹粉,将压板在平台上来回运动在将压板反面,进行观察,并将这个时候的初始尺寸记录下来。
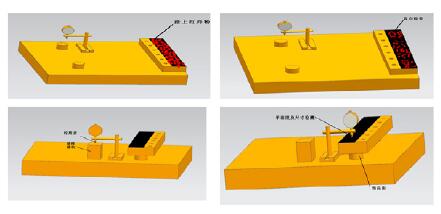
图3 压板高点及初始尺寸
通过对压板的检测后,知道了压板的高点和刮研量。于是对高点进行刮,边刮边检测,最后确定到刮研的量都去掉了并且保证了平面度的要求即可。
4.3 维修结果
将压板装上,使用扭矩扳手将压板紧固螺栓用100 Nm(厂家给定值)的力均布锁紧。
在进行手动、MDI、自动三种方式下分别运行 Z 轴,在每一种方式下使用不同的速度进行移动。Z轴均没有出现振动、异响的现象。Z轴功能运行正常,修复后各个精度检测均达标。达到出厂精度要求,经反复试车跑合,精度保持良好,现机床使用良好。
5、结语
Z轴是整个机床的核心移动部位,通过此次的维修有效的解决了Z轴振动、异响的故障,为以后的维修打下良好的基础。本文介绍了某机床 Z 轴异响故障的故障诊断流程以及维修方法,首先通过常规手段定位故障位置,然后通过分析数控加工程序、电气伺服参数以及机械结构排查确定故障原因,最后确定了维修方案和方法。本文提供的机床故障诊断以及维修方案可为其他故障维修提供参考。
投稿箱:
如果您有机床行业、企业相关新闻稿件发表,或进行资讯合作,欢迎联系本网编辑部, 邮箱:skjcsc@vip.sina.com
如果您有机床行业、企业相关新闻稿件发表,或进行资讯合作,欢迎联系本网编辑部, 邮箱:skjcsc@vip.sina.com