齿轮及轴承振动信号测试及故障诊断
2020-10-27 来源:同煤集团晋华宫矿机电科 作者:王建都
摘 要: 结合煤矿井下机电设备齿轮和轴承部件具体运行条件与环境,分析井下机电设备齿轮与轴承常见故障及原因,论述齿轮和轴承信号的振动测试过程及振动信号的调理与分析,通过应用齿轮及轴承故障诊断系统能准确发现故障问题,为采取有效处理措施提供可靠的保证。
关键词: 机电设备; 齿轮; 轴承; 故障诊断
0、引 言
煤矿井下机电设备运行效率及稳定性对煤矿开采作业质量有很大的影响。井下机电设备结构逐渐向大型化与复杂化方向发展,尤其在井下恶劣环境中运行时,其齿轮部件及轴承部件故障频发,导致井下采煤作业受到极为不利的影响。所以,以齿轮及轴承部件故障作为研究对象,探讨故障检测诊断的具体方法,为井下机电设备故障诊断提供参考与借鉴。
1、齿轮与轴承故障及成因
1.1、齿轮与轴承常见故障及测试振动信号目的
井下作业中,作业主要对象是岩体以及煤体结构,机电设备运行过程会受到较大的外界载荷作用,极易导致齿轮与轴承部件发生磨损。齿轮与轴承部件设计制造如果不合理,加之部件运行时未很好的维护与保养,均易造成齿轮与轴承部件出现故障。
齿轮与轴承部件故障,主要包含两类:
① 齿轮与轴承部件制造加工或者安装时引发的故障问题,例如齿轮与轴承部件存在的制造误差、轴线不能对中或者出现不平衡等;
② 齿轮与轴承实际运行时出现的故障,因为齿轮使用时会受到一定外力作用,齿轮与轴承运转时,在间接触部位产生较大热量,会引发脉动问题发生,齿轮与轴承连续、长时间工作状况下,极易发生点蚀、磨损和裂纹等现象,甚至还会出现断裂问题。
1.2、 故障测试振动信号目的
(1) 通过对齿轮和轴承部件振动信号的测试,能实时掌握井下极端设备实际运行情况,确保井下机电设备齿轮和轴承部件在运行过程中能一直保持在相应的约束与限值之中,确保能实时了解到井下机电设备具体情况,若机电设备有异常问题,则发出相应警报信号,确保维修人员能够尽早开展维护工作。
(2) 为井下机电设备维护与检修人员提供准确的状态描述,能有效减少设备的拆卸工作量,确保井下机电设备的完整性。
(3) 可在线实时对井下机电设备的维护与检修进行预测,结合监测所获得数据信息,能了解井下机电设备齿轮和轴承变化趋势,确保井下机电设备预测维修工作获得更可靠的数据支持。
2、齿轮和轴承故障信号振动测试系统设计
2.1、 测试系统功能
所设计的齿轮与轴承故障诊断系统是将传感装置设置于齿轮部件或者轴承部件之上,或者设置于与之相连的结构之上,要求能采集齿轮以及轴承运行所产生的各种参数信息,再把所采集的数据信息输送至上位机之中进行信息分析及处理。利用检测项目我们可以对齿轮以及轴承部件运转时所出现的振动信号、温度信号以及转速信号等各种信号加以实时检测然后利用信号调理装置对信号加以调理,为后续的信号分析与诊断工作提供更为可靠的数据信息,再结合检测到的信号信息,对齿轮以及轴承所出现的故障问题进行分析。然后可以将分析结果采用报表方式输出,并且能结合故障诊断所得结果,及时发出设备启动与停运指令,完成设备的启动和停运操作。
此测试系统具有以下功能:
( 1) 运行参数收集功能。所设计的测试系统拥有对齿轮和轴承部件运行过程中相关参数信息实时进行收集的功能。
( 2) 数据分析功能。所设计的测试系统对于所收集的相关参数信息能够实时加以分析,并且得出相应的分析结果。
( 3) 故障诊断的功能。所涉及的测试系统可以结合分析所得结果,利用时域分析方法,对齿轮和轴承的故障问题进行有效与准确的诊断。
( 4) 故障报警功能。所设计的测试系统可结合故障诊断结果实时发出故障警报,若是故障问题较为严重情况下,还可以发出停机指令,确保井下计算设备及时停止运行,确保井下机电设备运行的安全性。
2.2、 振动信号测试流程
对井下机电设备齿轮和轴承部件进行检测,最为重要的是确保应用传感装置,并且确保传感装置必须设置于适宜的位置。传感装置对齿轮和轴承振动所收集的相关信号通常相对弱,因此,必须时信号放大处理后才能够进一步对信号进行分析,因此要用到信号放大器装置。将所收集的齿轮和轴承振动放大处理后的信号输送至信号调理装置中完成滤波以及降噪等处理。经过信号调理装置后所获得信号为模拟信号,对于此类计算机设备无法有效识别,所以,振动信号输入计算机之前,必须经过 A/D 转换卡实现模拟信号和数字信号之间转换,将其转变成数字信号。然后借助计算机,对数字信号进一步开展时域分析,最终完成对齿轮和轴承部件的振动监测与故障诊断。齿轮和轴承部件的振动监测流程如图 1 所示。
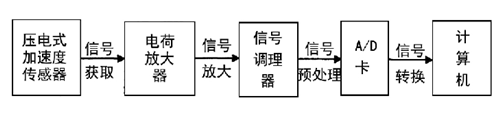
图 1 齿轮和轴承部件的振动监测流程
2.3、 振动信号测试系统硬件构成及功能
( 1) 压电式振动加速度传感装置。此装置结构示意图如图 2 所示,在传感器中质量块和被测量对象会同时进行振动,在质量块震动过程中,其会因为受到震动的作用而进行往复运动,从而会对压电晶体产生一定惯性力,不同振动加速度情况下,所形成惯性力存在差异,由于惯性力不同作用与压电晶体上的载荷不同,所产生的电荷也有所差异,并且两者之间呈线性变化趋势。所以,便可通过检测电荷变化情况得到相应的振动加速度信号。
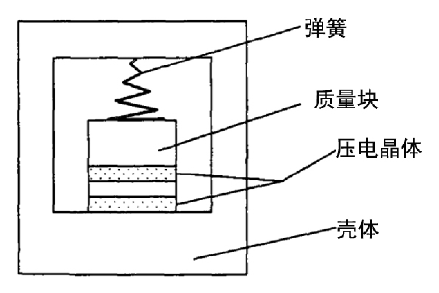
图 2 压电式振动加速度传感装置结构示意图
( 2) 光电式转速测量传感装置。在收集齿轮和轴承振动信号过程中,如果要确保对齿轮和轴承振动信号进行同步、整周期采集,必须对齿轮以及轴承部件所对应的转速值进行准确测试。光电式转速测量传感装置结构示意图如图 3,安装此装置时,首先应当将带有反光纸的转盘结构固定于需要检测的齿轮和轴承上,当其发生转动时,因为反光纸和圆盘结构的表面位置所对应的反射率存在差异,因此,便会出现反光及不反光的交替现象,安装于光电式转速测量传感装置内部的光敏部件便能够检测到相应的信号。
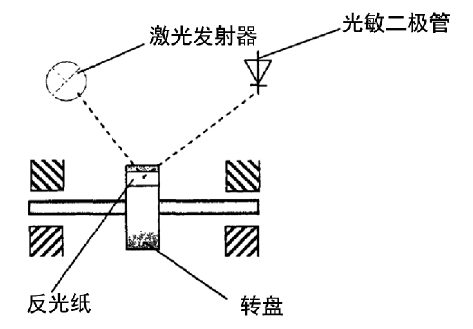
图 3 光电式转速测量传感装置结构示意图
( 3) 信号调理装置。通过利用信号调理装置,能就所采集获得的相关振动信号进一步放大、过滤处理,同时还能起到供电作用,这样便可确保所采集的信号能够更好的与 A/D 相互匹配。此次所设计的齿轮和轴承故障振动系统中应用的信号调理装置为CAMD-6200 型信号调理装置,此种装置能够确保四个不同通道的振动信号可同时输入,能满足系统需求。
3、振动信号调理与故障分析
3.1、 振动信号调理
经过相应传感装置收集的各种数据信息,经由特定的调整后,才能够继续加以处理。信号的调整是将信号进一步过滤及放大处理。过滤处理是把需要的最高频率以上对应的频率信息过滤去除,再进一步对信号加以放大,进行调理后信号再经过 A/D 转换被输送至计算机设备中进行故障的分析诊断。应当注意,信号收集过程中应进行等周期信号收集。所谓等周期信号采集是指所采集信号的对应长度值和转子对应的周期呈倍数关系。比如,轴承在转动一个周期会收集 200 个点数据,而在实际采集过程中收集到了2000 个点的数据信息,这说明在此次信号采集信息的周期为十个旋转周期。信号等周期采集流程示意图如图 4 所示。
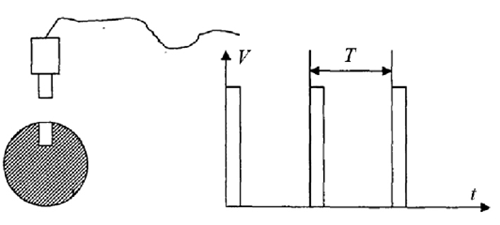
图 4 信号等周期采集流程
3.2、 故障分析
齿轮和轴承故障分析过程是将所采集的振动信息加以梳理与分析,分析采用时域分析法。齿轮和轴承出现各种故障问题所对应的时域信号示意图如图5 所示。
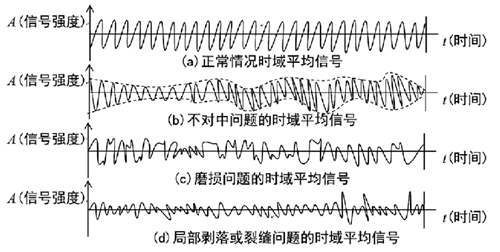
图 5 齿轮和轴承出现各种故障问题时对应域平均信号
图 5 所示是齿轮和轴承处在不同运行状态下,经过时域分析所采集的振动信号进行分析后得出相应的波形图,结合振动波形图特征便能够非常容易的对齿轮和轴承出现的故障加以诊断。图 5( a) 齿轮和轴承运行时未出现故障情况下得到的振动波形图。图5( b) 则是齿轮和轴承出现了一定的不对中故障情况下得到的振动波形图,在这一波形图里所对应的调制频率相对较低。图 5( c) 则是齿轮和轴承出现了一定的磨损情况下得到的振动波形图,这一波形图里所对应的平稳性有所降低,所对应的特征幅值同样出现了一定增大。图 5( d) 是齿轮和轴承出现了一定的剥落或裂缝故障情况下得到的振动波形图,其对应的特征幅值同样出现了一定的增大,并且现场工作人员也能够听到设备运行时产生相应的噪声。图 5( d) 对应的波形证明了齿轮或者轴承出现了较大的故障,要求检修人员必须及时开展检修工作,或对齿轮或者轴承部件加以更换处理。
4、应用效果
此次所设计的系统于 2017 年 6 月在晋华宫矿应用以来,极大的减轻了机电设备维护与检修人员的人工作业强度,使得维护与检修人员在井上便能够针对井下机电设备运行情况实时了解与掌握,确保作业人员能够在更为优良的环境中进行工作。另外,在此系统应用以来,一共准确检测出故障问题 34 次,确保了检修人员及时的发现井下机电设备齿轮与轴承故障问题。从统计数据来看,在未应用此系统之前,齿轮和轴承故障导致井下机电设备停机时间每月高达112 h,应用了此系统之前,齿轮和轴承故障为导致井下机电设备停机时间平均每月为 41 h,从该情况得出,齿轮及轴承振动信号测试及故障诊断能够准确的检测出齿轮和轴承故障问题,具有较强的实际推广应用价值。
投稿箱:
如果您有机床行业、企业相关新闻稿件发表,或进行资讯合作,欢迎联系本网编辑部, 邮箱:skjcsc@vip.sina.com
如果您有机床行业、企业相关新闻稿件发表,或进行资讯合作,欢迎联系本网编辑部, 邮箱:skjcsc@vip.sina.com
更多相关信息