汽车热冲压模具的数字化铸造技术
2019-2-15 来源: 大连理工大学材料学院 作者:李 鑫 姚 山
摘 要:针对汽车热冲压模具这类具有复杂内腔结构的铸件提出一种数字化铸造技术路线。 利用铸造模拟技术进行铸造方案设计;利用 3D 打印技术完成砂型(芯)的制造;将得到的砂型(芯)各部分组合后进行浇注得到模具铸坯;利用三维扫描技术对各个环节的产品进行精度检测。 按照此工艺路线可以对铸造的各个环节进行数字化的控制及调节,从而得到合格的模具铸坯。
关键词:热冲压模具;3D 打印;铸造模拟
高强度钢板代替传统钢板可以减少车身重量,并提高碰撞安全性,实现汽车轻量化。 与传统钢板不同,高强度钢板的成形需要内部带有随形冷却水道的热冲压模具,来保证零件的成形性要求以及良好的力学性能。
随形冷却水道的走向与模具型面的形状基本一致, 且中心距离型面的距离都相同。内部随形冷却水道的成功成形,是热冲压模具制造的重点及难点。 目前热冲压模具制造工艺中,钻孔工艺可以加工方向不变的直水道,但是很难满足随形要求;镶 拼工艺对密封提出很高的要求;铸 造工艺中预埋不锈钢管可以得到随形的冷却水道,但是冷却效果不佳,而 预埋陶瓷芯存在去除工艺繁琐等缺点。3D 打印技术是近几年非常热门的技术,但是受制于打印材料的高成本,此项技术在工业生产上并没有大面积应用。
使用 3D 打印技术打印出普通造型方法难以成形的砂型(芯),对于结构复杂的金属零件, 特别是热冲压模具这种具有复杂内腔结构的金属零件具有重要意义。
1 、技术路线
以某一款轿车热冲压模具为研究载体, 该热冲压模具的设计综合考虑计算机 CAD 参数化建模、热冲压及淬火仿真分析、 水冷模具管道设计及优化等科学问题。图 1 为一个典型车身模具镶块, 该模具具有复杂型面, 由于随形冷却水道要跟型面走向一致且要跟型面距离相等,所以冷却水道的结构也比较复杂。
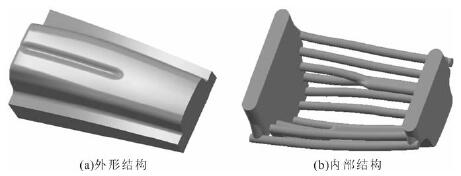
图 1 铸件的外形结构以及内部结构
传统铸造工艺中, 冷却水道部分需要通过下芯的工艺实现,按照设计要求,每一根水道的形状结构不尽相同, 所以每一根水道的成形都需要设计相对应的芯盒来实现,工艺比较繁琐复杂。 由于砂芯比较细,单根砂芯很容易发生偏移而造成最后成形的水道与设计出现偏差。在汽车热冲压模具的数字化铸造工艺路线中,首先对模具镶块进行铸造方案设计, 此部分包括铸件分析、浇冒口设计以及分型设计;将得到分型各部分进行切片处理得到打印数据,将打印数据传输到3D 打印设备中进行加工制作得到相应的砂型(芯);对砂型(芯)进行铸造前处理,将各部分按照分型设计组合后进行浇注试验;其中在各个加工制造过程中,使用三维扫描仪对各部分得到的产品,包括砂型(芯)以及最后得到的铸坯进行扫描,然后进行精度评价。 图 2 为整个工艺流程图。
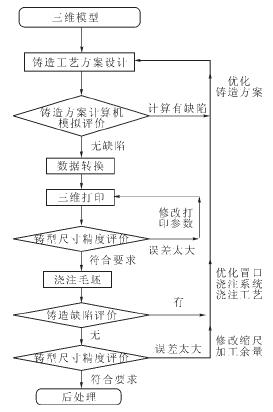
图 2 数字化铸造工艺路线
2 、铸造方案设计优化
2.1 铸件分析
由于后期铸造表面质量并不能达到模具工作要求,模具型面需要后期机加工,而通过 3D 打印的砂型浇注得到的铸坯精度很高, 仅需要一次精加工,加工余量不需要很大,取为 3 mm.
本试验目的是得到一套汽车热冲压模具的数字化铸造工艺路线, 主要为验证基于此路线的模具及其冷却水道的最后成形, 用铸造高温性能与模具钢相似的 35 钢代替验证其成形性 ,铸造缩尺为2.5%。
2.2 浇道与冒口的设计及优化
由于模具的复杂型面一侧为将来冲压的工作面,所以这个工作面需要有比较好的铸造性能,在铸造方案设计时,将这个面置于底侧。 采用底注式浇注方案,浇口设计在铸件的最底端。
由于随形冷却水道的直径大约在 10~12 mm,对应的砂芯直径也很细,钢液浇注时, 需要保证钢液在上升充型的时候要平稳,故采用 开放式浇 注系统,减少钢液对砂芯的冲击。
浇道横截面的面积比取∑F直∶∑F 横∶∑F 内=1∶1.2∶1.5,直浇道为阻流面,根据以下公式计算阻流面面积以及浇注时间:
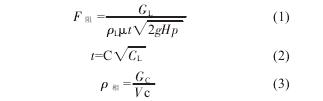
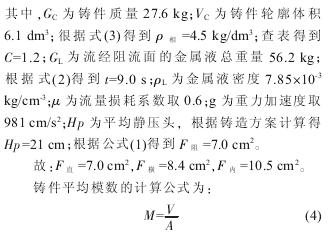
式中 ,V 为铸件体积 3 540.05 cm3,A为传热表面积 1781.22cm2,根据式(4)可得,铸件模数 M=1.98cm。根据铸件模数,通过查,选取冒口为标准圆柱形冒口,其中直径高度均为 120 mm。
依据计算得到的浇注系统以及冒口尺寸,铸造方案设计如图 3。 将设计的铸造方案 CAD 数据转化为有限元网格数据文件后,用 procast 铸造模拟软件对铸造方案进行计算
,对浇注系统以及冒口的设计进行校核。
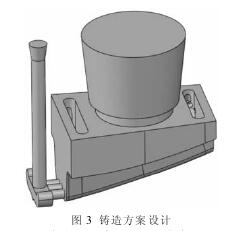
计算结果最后凝固位置位于冒口内,证明了冒口设置的合理性, 但是由于各部分砂型采用 3D 打印的方案制作,所以冒口的设计并不需要完全按照标准形状设计,而可以参照模具的结构进行单独设计。 由于此模具呈长条状,且一侧质量大于另一侧,所以设计冒口形状为腰圆形,且腰圆形两侧圆弧并不相等,圆弧半径较大的一侧对应于模具铸件质量比较大的一侧。
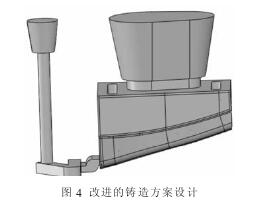
图 4 中所示,改进的铸造方案中冒口为腰圆形冒口。由于随形水道的直径比较小,对应的水道芯的直径也会比较小,为了降低浇注时钢液对砂芯的冲击,所以要考虑降低钢液进入铸型时的速度。 除了采用全开放的浇注系统外,在内浇道与横浇道上做一定的缓流设计,而由于采用 3D 打印制作的工艺,并不会因为浇道设计的复杂而增加制造难度。 图 4所示,改进的铸造方案设计中内浇道与横浇上有缓流设计。
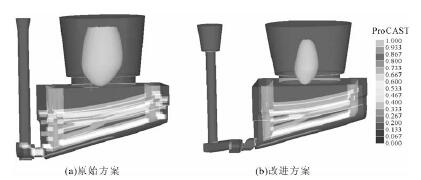
图 5 最后凝固位置
腰圆形冒口形状的设计, 可以起到标准圆形冒口相应的补缩作用, 图 5 所示为两种冒口设计中计算的最后凝固位置, 以看到最后凝固位置都位于冒口中。由于腰圆形冒口与模具形状相对应,可以减少冒口质量从而提高工艺出品率。通过比较计算结果中钢液流经内浇道时的速度, 可以发现在内浇道横浇道上做缓流设计可以减少钢液进入铸件的速度。
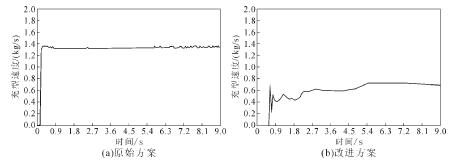
图 6 钢水流经内浇道的速度
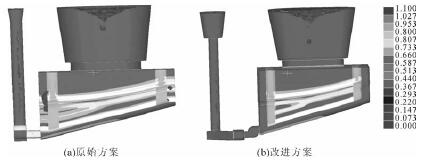
图 7 缩松缩孔示意图
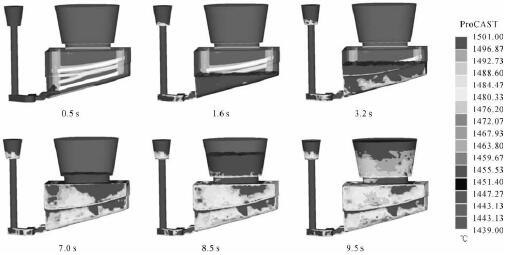
图 8 充型示意图
图 6 所示为不同设计的浇道计算得到的钢液流经内浇道的速度。比较两种设计计算得到缩松缩, 可以发现改进后的方案铸件内部缩孔缩松明显少于初始方案设计。 图 7 所示为缩松缩孔计算结果。选定改进后的铸造方案为实验浇注方案, 图 8所示为不同时间下的充型图, 充型期间比较平稳。3 3D 打印铸型在完成铸造方案的设计以及校核优化后, 需要对铸件的阴模进行分型设计。由于各个部分采用 3D打印工艺进行制作, 所以分型时并不需要像传统砂型铸造分型需要考虑的拔模问题。 考虑到最后各个砂型的组合以及 3D 打印设备制作效率, 将铸件阴模分成四个部分:下型部分,砂芯部分,冒口部分,浇注系统部分。 图 9 为铸件阴模的分型设计。
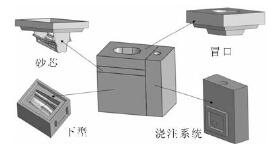
图 9 铸件阴模的分型设计
采用 SLS 法(选择性激光烧结法)加工打印各个部分。 由于砂芯部分中随形冷却水道芯比较细,打印砂芯不能使用一般的覆膜砂,因此采用强度指标比较高的宝珠砂,可以保证打印成功率以及打印得到砂芯强度。 其他部分采用一般砂型所需要的普通覆膜砂。 打印过程中,调整打印设备中激光的扫描功率,以及打印设备腔体内环境温度,特别对于砂芯部分,由于结构比较复杂,在加工时需要对打印参数精确控制。
各部分的加工参数见表 1。将 3D 打印的预成型产品放入烘箱中烘烤以使其强度满足浇注要求。 为了防止在烘烤时发生变形,将砂型周围埋上细小的玻璃珠。 表 2 为烘烤参数。
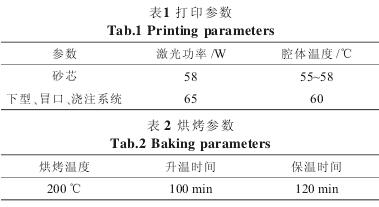
图 10 所示为 3D 打印设备打印制作以及烘烤完成的砂芯以及砂型。打印制作的砂型的尺寸精度直接影响最后得到的铸件尺寸精度。 使用三维扫描仪对打印得到的各部分砂型进行扫描测量, 将测量所得的点云数据与三维 CAD 数据进行精度比对, 确定砂型的制作误差。 图 11 为砂芯的精度比对结果,可以看出砂芯的整体制作误差在 1.5 mm 以内,根据误差分布图以及误差云图显示结果, 随形水道部分对应的砂芯制作误差在0.75 mm 以内 , 且大部分误差在0 . 30 mm 以内。 由于砂芯部分对应铸件的随形水道部分, 而最后随形水道位于铸件内部无法测量其尺寸精度, 所以此时测量的砂芯精度可以为最后铸件内部的随形水道尺寸精度提供参考。
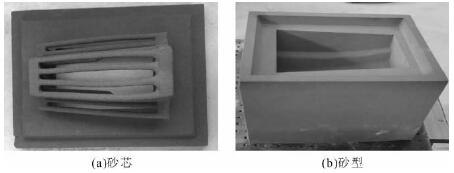
图 10 砂芯与砂型
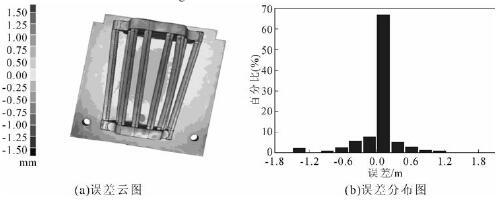
图 11 砂芯精度检测结果
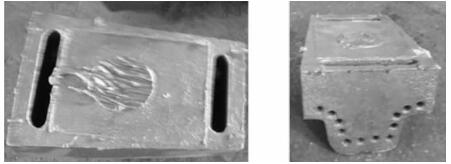
图12 模具铸坯
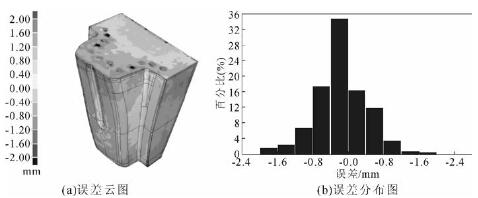
图 13 铸坯精度检测结果
4 、浇注及浇注结果
将各部分砂型按照图 9 的分型设计进行组合,组合完成后进行浇注,按照之前模拟计算得到的 1 560 ℃的浇注温度进行浇注。 图 12 为浇注得到的模具铸坯, 使用三维扫描仪对铸坯进行扫描后再进行精度评价。 图 13 所示为铸坯精度评价,根据结果发现铸坯的整体尺寸误差大部分集中在 2 mm 以内,工作型面的制作误差在 1.2 mm 以内,根据误差分布图分析,大部分误差在 0.8 mm 以内。将模具进行剖分操作, 一方面检验其内部水道的成形情况, 另一方面检测模具内部是否有缩松缩孔等铸造缺陷。
图 14 为铸坯剖分结果,根据剖分结果可以看出,内部冷却水道完全成形,并没有水道堵塞的情况出现, 且模具内部不存在铸造缺陷。
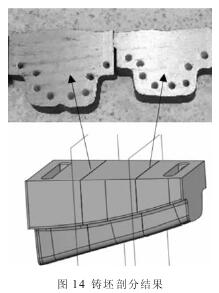
由于得到的铸坯尺寸已经接近所需要的模具尺寸, 所以铸坯进行相关热处理及一次表面精加工即可得到最后的热冲压模具。
5 、结论
汽车热冲压模具由于内部存在随形冷却水道 , 生产制作难度很大 。 本文结合3D打印技术 、传统砂型铸造技术以及铸造模拟技术 、三 维扫描技术 , 提出汽车热冲压模具 的数字化铸造技术 。 利用铸造模拟技术设计优化出最合适的铸造方案 ,通过3D打印技术打印出高精度的砂型 ,将砂型组合后进行浇注得到高精度的铸坯 ,在整个过程中 , 通过三维扫描技术对各个环节的产品进行精度评价 。 整个技术路线中 ,每个环节都可以通过数字化控制与调节以保证热冲压模具的成型质量 。
此种工艺路线对于汽车热冲压模具这类内部复杂结构的铸件成形具有示范意义。
投稿箱:
如果您有机床行业、企业相关新闻稿件发表,或进行资讯合作,欢迎联系本网编辑部, 邮箱:skjcsc@vip.sina.com
如果您有机床行业、企业相关新闻稿件发表,或进行资讯合作,欢迎联系本网编辑部, 邮箱:skjcsc@vip.sina.com
更多相关信息