新型汽车曲轴锻压工艺的优化
2019-1-17 来源: 长春汽车工业高等专科学校 作者:石庆国
摘 要:研究了始锻温度、终锻温度和锻压变形量 3 个工艺参数对 38Mn VAl Mg 新型汽车曲轴弯曲疲劳性能和热疲劳性能的影响。 结果表明:随始锻温度从 1050 ℃增加至 1150 ℃或终锻温度从 750 ℃增加至 950 ℃或锻压变形量从6%增加至 12%,新型汽车曲轴的弯曲疲劳性能和热疲劳性能均先提高后下降 ,中值疲劳强度先增大后减小 ,热疲劳试验后的主裂纹级别、网状裂纹级别和热疲劳裂纹级别均先减小后增大。 始锻温度、终锻温度和锻压变形量分别优选为1100 ℃、850 ℃、10%。
关键词:锻压工艺; 汽车曲轴; 38Mn VAl Mg 钢; 热疲劳性能; 弯曲疲劳性能
曲轴作为重要的汽车零件, 吸引了众多科研工作者和工程技术人员的研究兴趣。 在汽车曲轴的材料选择、热处理工艺和表面强化方面,人们进行了较多的研究,也取得了较多的成果。 但是,关于汽车曲轴锻压工艺的研究还较少。
锻压工艺对汽车曲轴的综合性能有重要影响。 随着汽车曲轴性能要求的提高,现有的 40Cr、38Mn V 等材料往往难以满足市场的需求。 为此,本文对 38Mn VAl Mg 新型汽车曲轴进行不同工艺的锻压试验, 并进行弯曲疲劳试验和热疲劳试验。
通过弯曲疲劳性能和热疲劳性能测试与分析,对新型汽车曲轴的锻压工艺进行了优化。
1 、试验材料及方法
试验材料为 38Mn VAl Mg 钢, 其化学成分如表1 所示。 新型汽车曲轴的锻压工艺如表 2 所示。 锻压变形量的计算公式为:锻压变形量=(锻造前曲轴毛坯 1/2 长度处的横截面积÷锻造后曲轴锻压件 1/2长度处的横截面积)×100%。 新型汽车曲轴为尼桑FD6T 改进后的曲轴 , 主轴颈 71 mm, 连杆径 60mm,中心距为 58 mm。
表 1 38Mn VAl Mg 钢的化学成分(质量分数,%)

表 2新型汽车曲轴的锻压工艺
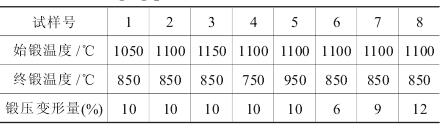
疲劳试样取自主轴颈、连杆和曲柄臂。对不同锻压工艺的新型汽车曲轴试样,采用拉-压加载对称循环疲劳, 在 谐振式曲 轴疲劳试验 机上 , 参照 QC/T637-2000《汽车发动机曲轴弯曲疲劳试验方法 》进行弯曲疲劳性能测试。 试验循环为 1×107次,采用升降法测试,根据公式(1)得出试样的中值疲劳强度,用以表征试样的弯曲疲劳性能。 参照 GB/T15824-2008进行试样热疲劳性能测试, 在 500~25℃冷热循环1000 次后用 PG18 型金相显微镜观察热疲劳裂纹形貌,并依据 GB/T15824-2008 进行裂纹评级,用以表征试样的热疲劳性能。
用升降法测曲拐的疲劳极限M-1,最后确定曲轴的 M-1。

2 、试验结果及讨论
2.1 始锻温度的影响
采用不同的始锻温度、相同的终锻温度(850℃)和锻压变形量(10%)对 38Mn VAl Mg 新型汽车曲轴试样进行锻压试验。 始锻温度对新型汽车曲轴试样的弯曲疲劳性能影响如图 1 所示。
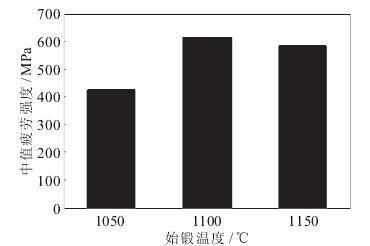
图 1 始锻温度对试样弯曲疲劳性能的影响
从图 1 可看出,随始锻温度从 1050℃增加至 1150℃, 新型汽车曲轴的中值疲劳强度先提高后下降。 当始锻温度为 1100℃时,新型汽车曲轴的中值疲劳强度最高(614 MPa)。
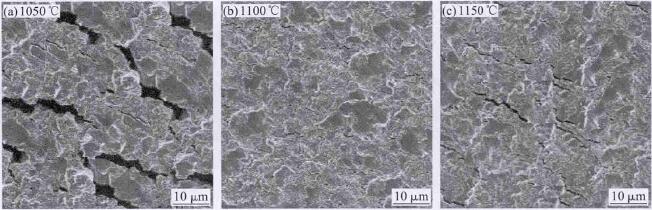
图 2 不同始锻温度试样弯曲疲劳断口 SEM 照片
图 2 是不同始锻温度锻压的 38Mn VAl Mg 新型汽车曲轴试样弯曲疲劳断口 SEM 照片。 从图 2 可看出,采用较低的始锻温度(1050℃)时,新型汽车曲轴弯曲疲劳试验后断口出现较多粗大的裂纹, 试样的弯曲疲劳性能较差; 当始锻温度升高到 1100℃时,新型汽车曲轴弯曲疲劳试验后断口中没有出现明显的粗大裂纹, 仅有极小的裂纹, 试样的弯曲疲劳性能较 1050℃始锻温度试样得到明显改善。
当始锻温度进一步提高到 1150℃时,新型汽车曲轴弯曲疲劳试验后断口中的裂纹明显增大, 试样的弯曲疲劳性能较 1100℃始锻温度试样有所降低。 这与试样的中值疲劳强度测试结果一致。由此可以看出,始锻温度是影响锻压态 38Mn VAl Mg 新型汽车曲轴试样弯曲疲劳性能的重要影响因素。
从改善 38Mn VAl Mg 新型汽车曲轴弯曲疲劳性能出发, 始锻温度不宜过高也不宜过低,优选为 1100℃。
始锻温度对新型汽车曲轴试样的热疲劳性能影响如图 3 所示。 根据国标 GB/T15824-2008,材料的热疲劳裂纹级别等于主裂纹级别与网状裂纹级别之和。热疲劳裂纹级别数值越小,材料的热疲劳性能越好;反之,热疲劳裂纹级别数值越大,材料的热疲劳性能越差。
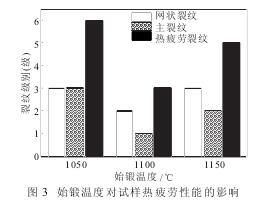
从图 3 可看出,随始锻温度从 1050℃增加至 1150 ℃,新型汽车曲轴的主裂纹级别、网状裂纹级别和热疲劳裂纹级别均表现出先减小后增大的变化趋势。 当始锻温度为 1100℃时,新型汽车曲轴的主裂纹级别、 网状裂纹级别和热疲劳裂纹级别均最小,分别为 1、2、3 级。
图 4 是不同始锻温度锻压的38Mn VAl Mg 新型汽车曲轴试样热疲劳试验后主裂纹形貌。
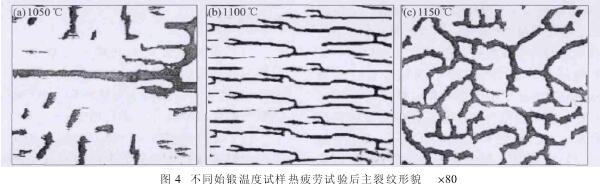
从图 4 可看出,采用较低的始锻温度(1050℃)时,新型汽车曲轴热疲劳试验后主裂纹较粗,与国标 GB/T 15824-2008 规定的 3 级主裂纹相一致;当始锻温度升高到 1100℃时,新型汽车曲轴热疲劳试验后主裂纹细小, 与 GB/T 15824-2008 规定的 1级主裂纹相一致。
当始锻温度进一步提高到 1150℃时,新型汽车曲轴热疲劳试验后主裂纹较粗,与国标GB/T 15824-2008 规定的 2 级主裂纹相一致。 这与试样的热疲劳试验的裂纹级别测试结果一致。 由此可以看出, 始锻温度是影响锻压态 38Mn VAl Mg 新型汽车曲轴试样热疲劳性能的重要影响因素。
从改善38Mn VAl Mg 新型汽车曲轴热疲劳性能出发 , 始锻温度不宜过高也不宜过低,优选为 1100℃。
2.2 终锻温度的影响
采用不同的终锻温度、相同的始锻温度(1100℃)和锻压变形量(10%)对 38VAl Mg 新型汽车曲轴试样进行锻压试验。终锻温度对新型汽车曲轴试样的弯曲疲劳性能影响如图 5 所示。
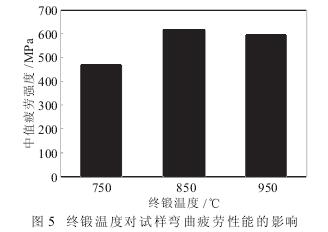
从图可看出,随终锻温度从 750℃增加至 950℃, 新型汽车曲轴的中值疲劳强度也表现出先提高后下降。 当终锻温度为 850℃时, 新型汽车曲轴的中值疲劳强度最大(614 MPa)。 采用不同的终锻温度、相同的始锻温度(1100 ℃)和锻压变形量(10%)对 38Mn VAl Mg 新型汽车曲轴试样进行锻压试验, 终锻温度对新型汽车曲轴试样的热疲劳裂纹级别影响如图 6 所示。
根据GB/T 15824-2008,材料的热疲劳裂纹级别等于主裂纹级别与网状裂纹级别之和。 热疲劳裂纹级别数值越小,材料的热疲劳性能越好;反之,热疲劳裂纹级别数值越大
,材料的热疲劳性能越差。
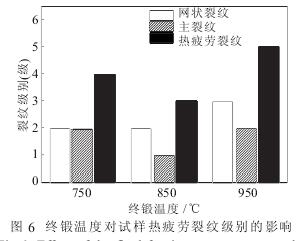
从图 6 可以看出,随终锻温度从 750℃增加至 950℃,新型汽车曲轴的主裂纹级别、 网状裂纹级别和热疲劳裂纹级别均表现出先减小后增大的变化趋势。 当终锻温度为 850℃时,新型汽车曲轴的主裂纹级别、网状裂纹级别和热疲劳裂纹级别均最小,分别为 1、2、3 级。
由此可以看出, 终锻温度是影响锻压态 38Mn VAl Mg新型汽车曲轴试样疲劳性能的重要影响因素。 从改善 38Mn VAl Mg 新型汽车曲轴弯曲疲劳性能和热疲劳性能出发,终锻温度不宜过高也不宜过低,优选为850 ℃。
2.3 锻压变形量的影响
采用不同的锻压变形量、相同的始锻温度(1100℃)和终锻温度(850 ℃)对 38Mn VAl Mg 新型汽车曲轴试样进行锻压试验。 锻压变形量对新型汽车曲轴试样的弯曲疲劳性能影响如图 7 所示。
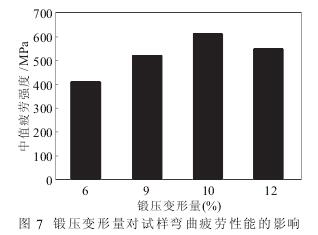
从图可看出,随锻压变形量从 6%增加至 12%,新型汽车曲轴的中值疲劳强度先提高后下降。 当锻压变形量为 10%时,新型汽车曲轴的中值疲劳强度最大(614MPa)。采用不同的锻压变形量、 相同的始锻温度和终锻温度, 对 38Mn VAl Mg 新型汽车曲轴试样进行锻压试验。
锻压变形量对新型汽车曲轴试样的热疲劳性能影响如图 8 所示。
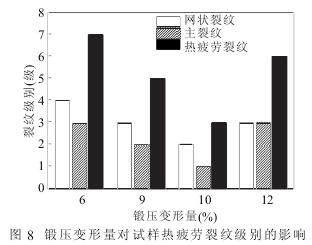
从图 8 可看出, 随锻压变形量从6%增加至 12%,新型汽车曲轴的主裂纹级别 、网状裂纹级别和热疲劳裂纹级别均表现出先减小后增大的变化趋势。
当锻压变形量为 10%时,新型汽车曲轴的主裂纹级别、 网状裂纹级别和热疲劳裂纹级别均最小,分别为 1、2、3 级。 由此可看出,锻压变形量是影响锻态 38Mn VAl Mg
新型汽车曲轴试样弯曲疲劳性能和热疲劳性能的重要影响因素 。
从改善38Mn VAl Mg 新型汽车曲轴弯曲疲劳性能和热疲劳性能出发, 锻压变形量不宜过大也不宜过小, 优选为 10%。
3 、结论
(1) 随始锻温度从 1050 ℃ 增加至 1150 ℃ , 新型汽车曲轴弯曲疲劳试验的中值疲劳强度先提高后下降,热疲劳试验后的主裂纹级别、网状裂纹级别和热疲劳裂纹级别均先减小后增大。
(2) 随终锻温度从 750 ℃增加至 950 ℃, 新型汽车曲轴弯曲疲劳试验的中值疲劳强度先提高后下降,热疲劳试验后的主裂纹级别、网状裂纹级别和热疲劳裂纹级别均先减小后增大。
(3) 随锻压变形量从 6%增加至 12%, 新型汽车曲轴弯曲疲劳试验的中值疲劳强度先提高后下降,热疲劳试验收的主裂纹级别、网状裂纹级别和热疲劳裂纹级别均先减小后增大。
(4) 38Mn VAl Mg 新型汽车曲轴在锻压过程中,始锻温度、终锻温度和锻压变形量均不宜过高也不宜过低,分别优选为 1100℃、850℃、10%。
投稿箱:
如果您有机床行业、企业相关新闻稿件发表,或进行资讯合作,欢迎联系本网编辑部, 邮箱:skjcsc@vip.sina.com
如果您有机床行业、企业相关新闻稿件发表,或进行资讯合作,欢迎联系本网编辑部, 邮箱:skjcsc@vip.sina.com
更多相关信息