试论如何选择数控铣加工的刀具和切削用量
2020-3-9 来源: 江南工业集团有限公司 作者:彭湘 彭小彦
摘要:中国的机械加工技术呈现出突飞猛进的发展态势,使得机械制造业的经济效益明显提高。数控机床是对机床进行数字化控制,提供运行程序完成各项工作。为了提高数控机床的加工质量和加工效率,就要对刀具以及切削用量合理确定。本文针对如何选择数控铣加工的刀具和切削用量进行研究。
关键词:数控铣加工 刀具 切削用量
计算机技术、网络技术和信息通信技术的快速发展使数控技术不断创新并广泛应用于数控机床。随着人们对产品的加工技术质量要求越来越高,就需要对刀具和切削量正确选择,在确保数控机床安全运行的基础上,加工产品的质量和效率都会有所提高。图1为轴类加工数控铣面钻中心孔机床。
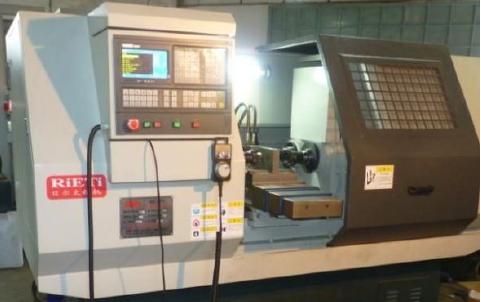
图1 轴类加工数控铣面钻中心孔机床
1、 数控铣加工的刀具选取
应用数字控制技术进行机械加工,可以使得加工的质量和加工的效率明显提高。与传统的机械加工技术相比较,数字化控制技术的加工速度更快,而且可以保证加工部件的质量。在数字化控制技术应用中,要使用计算机对刀具所在位置进行调整,确保数控加工的持续性,由此提升机械加工的速度。目前的数控铣加工中所使用的刀具主要包括两种,即铣削加工中使用的刀具和孔加工中使用的刀具。在对刀具进行选择的时候,要求刀具的刚性要满足机械加工的需求,还要在加工中对参数不断地调整。在铣削加工中通常会采用分层的方法,按照已经设定的程序进行机械加工。
如果铣刀所留出的余量非常大,就需要对更大直径的刀具做好筛选工作。铣刀的耐久性要强,避免损害到防控表层的刀具,还要对刀具的位置进行不断的调整。在选择铣刀的时候,要按照新的数控加工要求进行选择。在加工的过程中,编写程序的工作人员要将最佳型号的刀具确定下来之后,就进入到数控加工环境,对于工件材料的质量、机床所具备的特性、需要遵循的切削加工流程以及切削量达到都要做好综合性判定工作,要求刀具要具有耐久性,操作精度高,而且可以根据加工需要做出调整。具体的刀具选择方式如下。
1.1 数控铣加工中对铣削刀具的选择
当对曲面式的零件进行制作的过程中就要使用铣削刀具。在进行机械加工的过程中,要求刀具的切削要与加工的轮廓相符合,以对工件的轮廓以及刀刃的切割具有很高的精确度。通常而言,可以选择球头刀进行切割,如果采用粗加工的模式,则可以选择双刃式的铣刀进行加工。如果采用精细式的加工模式,则可以选择四刃式的铣刀进行加工。铣刀的表层面积是非常大的,为了使得所加工的工件表面平滑,可以选取盘状镶嵌式的刀具。如果所加工的位置是在键槽处,就可以选择双刃的加工铣刀进行加工。如果铣加工中,对部件的台阶面进行加工处理,或者加工的平面比较小时,就可以考虑选择通用式的铣刀。
1.2 数控铣加工中对孔加工类刀具的选择
数控铣加工中对孔加工类刀具的选择需要遵循一定的规则,即数控加工中对孔的加工都不需要使用钻模。如果切削的环境条件不良,切钻头的刚性不够理想,就需要对钻孔的深度重新设置,要求钻孔的深度与钻头的直径之间的比为5∶1。当进入到钻孔环节之前,要对中心钻的位置明确,划定准确的部位,保证定位的精度。铰孔加工中采用浮动式的刀具,前期要倒角,后期的镗孔要选择镗刀,刀头为对称式的,使得加工中平衡性的振动有所减小。
2、数控铣加工中要设定切削用量
2.1 对切削的深度予以确定
数控铣加工所使用的机床种类不同,选用的加工材料不同,切削的深度也会有所不同,这就需要将匹配工作做好。当明确了切削深度之后,就要基于实际的加工环境条件进行切削。当处于粗加工环节的时候,就可以对切削的深度进一步加深,在刀具的刚度符合规定标准的前提下,要在一次切削的过程中切掉材料。否则,如果刀具的刚度非常低,或者材料比较厚,就会对切削工作造成不良影响,甚至会产生切不断的现象。在进行切削的过程中,刀口要朝向里面,避免刀刃直接接触到机床的金属物而对金属物造成破损。刀具的刚度比较低、材料相对较厚,在强大的冲击荷载下,就要将切削深度减小,使得切削的质量有所改进,这样可以避免刀具在切削的过程中造成损伤。另外,对于切削的深度要合理确定,从加工余量的角度出发来做到余量合理。为了避免加工中造成大量的资源浪费,可以将切削深度减小,以提高切削加工的质量和效率。通常而言,切削的深度介于0.05~1.0mm之间。如果切削深度为半精加工,切削的深度介于1~3mm之间,工作人员进行切削加工的时候,就要在这个范围内灵活调整深度。
2.2 对切削的速度予以确定
进入到铣削加工环节,切削速度决定于刀具的耐用情况。在对切削速度加以确定的过程中,对于各项衡量指标都要明确,包括铣削的总齿数、侧面以及综合性的吃刀量等。如果铣加工的齿数比较多,刀刃负荷就需要相应地增加,还要在切削的过程中增加热能,刀具的磨损度就会增加。要提高刀具切削的速度,就要选择耐用性比较强的刀具,还要对刀具的直径进行延长,使得刀具切削过程中的散热状态得以改善。
2.3 对进给速度予以设定
当数控机床处于运行状态,一项重要的参数就是进给速度。当数控机床加工的过程中,对于进给速度明确之后,就要根据工件的粗糙度和精确度对进给速度进行设定。如果进给速度比较快或者比较慢,都会导致机床运转的过程中受到制约。从工件的边框向拐角处加工的过程中,进给速度需要适当地减慢,以避免边框加工中产生偏差。在进行工件制作的过程中,要保证加工进度快,而且工件的质量合格,就要将进给速度设定好。
2.4 对侧边的吃刀量予以确定
要保证数控机床的加工质量,就要对侧面吃刀量和背侧的吃刀量加以确定。对于工件的侧边加工中,可以将走刀次数适当地减少。根据粗糙程度的不同,可以将数控铣的工序划分为3类,即精铣,侧向吃刀深度为0.5mm;半精铣,侧向吃刀深度为1.3mm;粗铣,侧向吃刀深度为0.3mm,还可以根据具体的数控机床加工情况对侧边的吃刀量做出调整。
3、结语
综上所述,在数控铣加工中要按照编制的程序进行,要保证加工质量,就要保证刀具的良好匹配度,切削用量要适当。从目前的数控铣加工的具体情况来看,依然存在需要进一步完善之处,且还要根据加工需要不断地改进技术,以提高数控加工质量。
投稿箱:
如果您有机床行业、企业相关新闻稿件发表,或进行资讯合作,欢迎联系本网编辑部, 邮箱:skjcsc@vip.sina.com
如果您有机床行业、企业相关新闻稿件发表,或进行资讯合作,欢迎联系本网编辑部, 邮箱:skjcsc@vip.sina.com
更多相关信息