金属激光切割机焦点控制系统的设计
2017-5-2 来源:武汉理工大学自动化学院 作者:朱云峰 聂红伟
摘要:焦点控制系统是金属激光切割机至关重要的组成部分,它与激光焦点与工件之间距离的准确性和稳定性直接相关,由此决定了金属工件的切割质量和效率。 为此,采用高性能 DSP、高精度电容传感器等设计金属激光切割机焦点控制系统,对激光焦点与工件之间的距离进行实时精确的控制并配合机床运动控制卡完成整个金属激光切割流程。 首先介绍了金属激光切割机焦点控制系统的结构和工作原理,然后重点介绍了系统硬件设计,同时给出了部分核心软件设计流程。
关键词:金属激光切割机,焦点控制系统,DSP,电容传感器
在金属激光切割过程中,激光焦点与工件距离的恒定极其重要, 采用焦点控制系统对其进行不断的实时校正从而获取最优的切割质量。采用高性能 DSP、高精度电容传感器等设计金属激光切割机焦点控制系统, 利用电容传感器检测技术和模糊 PID 控制算法对激光焦点与工件之间的距离进行实时精确的控制并配合机床运动控制卡协同完成整个金属激光切割流程, 提高切割质量和切割效率。
1.系统结构和工作原理
1.1 系统结构
该系统主要包含两个部分:焦点位置检测模块和焦点位置控制模块。 焦点位置检测模块由电容信号检测电路以及信号传输电路组成。 焦点位置控制模块由电容信号的接收电路、电机控制信号的输出电路、 指令信号的接收电路以及数据存储电路组成,其功能是接收焦点位置检测模块发送的测量电容值,通过控制算法实时输出电机控制信号,调控电机实现减小距离偏差的目的。
系统选用 TMS320F28335 型号的 DSP 作为主控制器,其时钟频率可达到 150MHz,I / O 资源丰富, 支持 SPI 通信、USB通信以及 DA 输出等功能,能实现高效快速运算,从而实现与焦点位置检测模块以及机床运动控制卡的快速数据交换和运算。系统结构图如图 1 所示。
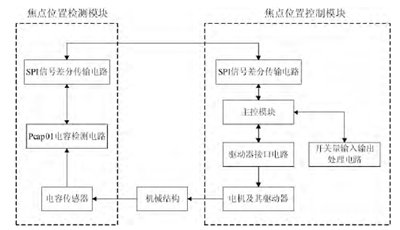
图 1系统结构图
1.2 工作原理
金属激光切割机焦点控制系统的任务是对激光焦点与工件之间的距离进行实时采集以及控制, 使其始终处于最佳切割位置从而提高切割质量, 同时与机床运动控制卡进行数据交换协同完成整个金属切割流程。 通过电容传感器对激光焦点与工件之间距离进行采集, 并通过信号处理电路以数字量形式传给主控制器 TMS320F28335; 主控制器对此距离信号进行数字滤波以及最小二乘法曲线拟合, 从而得到焦点距离与电容值之间的对应关系曲线; 主控制器通过模糊 PID 算法以焦点距离以及焦点距离变化率作为输入, 输出控制电压给驱动器接口电路以驱动伺服电机运动使得激光焦点与工件之间距离始终处于最佳,由此提高切割质量以及效率; 机床运动卡主要实现 XY 平面上的运动轨迹规划, 焦点控制系统则是实现 Z 方向上的切割距离恒定, 二者之间通过 I / O 口进行运动状态的数交换协同完成整个金属切割流程。
2.系统硬件设计
2.1 焦点位置检测模块设计
综合考虑测量范围、 测量精度以及成本等因素, 选用德国ACAM 公司的 Pcap01 专用电容检测集成芯片来设计焦点位置检测模块,实时获取焦点位置。 Pcap01 电容检测芯片内置 DSP信号处理单元,具有高精度、高速度等优良特性,检测频率可高至 500k Hz,电容测量结果具有 24 位精度,且具有超高的温度稳定性和超低温漂。 焦点位置检测模块结构图如图 2 所示。

图 2 焦点位置检测模块结构图
在金属激光切割过程中,Pcap01 电容检测电路将焦点与工件之间的距离值转换为数字量, 并通过 SPI 通信方式将其传给主控制器进行数据处理。 需要注意的是,二者之间的信号线需为双绞屏蔽线且在每组差分信号线之间要添加 1K 的匹配电阻,从而消除差分信号传输线的共模干扰, 在一定程度上加强远距离信号传输的稳定性。
2.2 焦点位置控制模块设计
焦点位置控制模块由主控模块、 驱动器接口电路以及开关量输入输出处理电路三部分组成。 主控模块接收焦点位置检测模块发给的电容信号, 并根据电容值与焦点距离的标定关系得到此时的焦点距离, 并输出通过模糊 PID 控制算法得到的对电机的控制电压信号。 驱动器接口电路对 DSP 输出的焦点位置控制模拟量电压信号与电机驱动器输入范围进行匹配。 开关量输入输出处理电路的功能是接收机床运动控制卡发送的指令信号,并将焦点位置控制模块的状态反馈给机床运动控制卡,从而使焦点位置控制模块处于正确的工作流程。 焦点位置控制模块结构图如图 3 所示。
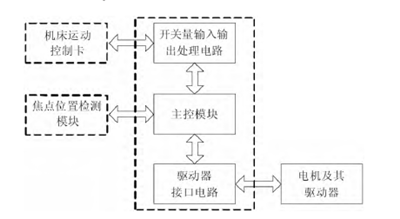
图 3 焦点位置控制模块结构图
主控模块由一个 DSP 最小系统、 外部存储器以及外部 DA共同组成。 其功能为通过接口电路与机床运动控制卡进行 I / O 信号类型的数据交换、 接收焦点位置检测模块反馈的电容测量值、输出对电机驱动器的控制电压。 主控模块硬件框图如图 4 所示。
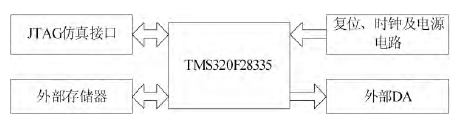
图 4 主控模块硬件框图
本设计选取的 DSP 型号为 TMS320F28335,电压输出范围为 0~3.3V,电机驱动器的控制电压范围为-10V~10V,驱动器接口电路采用运算放大器来实现匹配,其电路图如图 5 所示。
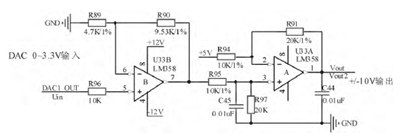
图 5驱动器接口电路
对于金属激光切割机而言, 机床运动控制卡实现的是 XY平面的切割轨迹规划, 焦点控制系统实现的是 Z 方向的激光焦点位置的恒定,焦点控制系统要受机床运动控制卡的控制。 在金属切割过程中,机床运动控制卡会发送随动、穿孔、加工完成等信号给焦点控制系统, 而焦点控制系统也需要将反映当前切割头位置的信号如上升到位信号、 下降到位信号以及切割报警信号等发送给机床运动控卡, 机床运动控制卡接收到这些信号后对其进行分析从而决定可否进行下一步的切割操作。 由于不同机床运动控制卡的开关量输入输出方式可能存在差异, 考虑到机床运动控制卡不同的电平电压, 需要有一个相对适用范围更广的输入输出处理电路。 开关量输入输出处理电路原理图如图 6 所示,与机床运动控制卡通信信号全部进行光耦隔离,并通过指示灯进行示意。
3.系统软件设计
3.1 主程序
主程序主要功能:系统初始化设置、焦点位置与电容值之间的数据标定以及回零操作。各个功能封装成对应子程序,分别为初始化子程序、数据标定子程序和回零子程序,其流程图如图 7 所示。
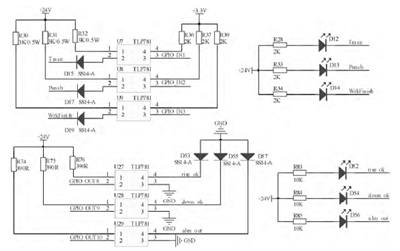
图 6 开关量输入输出处理电路原理图
数据标定子程序流程图如图 8 所示。 在数据标定子程序中,在每个已知距离的测量点处通过 Pcap01 电容检测模块测量电容并进行中值滤波, 将测量范围合理分段后在每一小段上通过最小二乘法进行曲线拟合,实现焦点距离与电容值之间的标定。
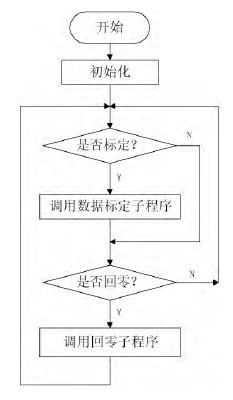
图 7主程序流程图
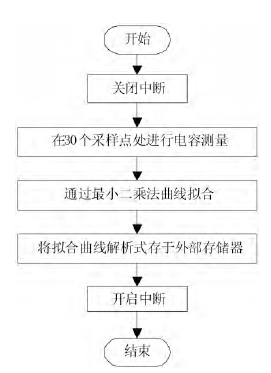
图 8数据标定子程序流程图
需要注意的是,当工件材质或者工作环境改变时,焦点距离-电容值特性曲线也会随之而变化,此时必须重新进行数据标定。
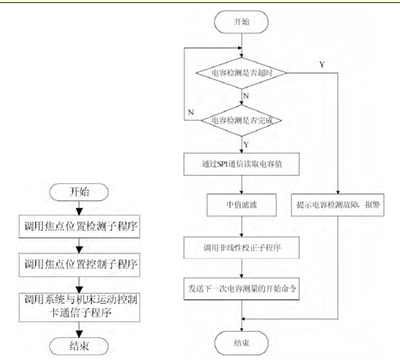
图 92ms 定时中断子程序流程图 图 10 焦点位置检测子程序流程图
主控制器中还有一个 2ms 定时中断,其包含 3 个子程序:焦点位置检测子程序,焦点位置控制子程序和系统与机床运动控制卡通信子程序。 焦点位置检测子程序实现主控 DSP 对电容检测单元的电容值读取; 焦点位置控制子程序实现主控 DSP 对电机的控制电压输出;系统与机床运动控制卡通信子程序接收到的指令信号对应着系统不同的工作状态,其决定着焦点位置检测子程序中程序的走向。 2ms 定时中断子程序流程图如图 9 所示。
3.2 焦点位置检测子程序
焦点位置检测子程序的功能是实现主控制器与电容检测芯片之间的数据通信,获取切割头与工件之间的电容值,并通过由数据标定子程序确定的焦点距离与电容值拟合曲线解析式对应的焦点距离值,供焦点位置控制子程序调用。 焦点位置检测子程序流程图如图 10 所示。
3.3 焦点位置控制子程序
焦点位置控制子程序的功能是读取焦点位置检测子程序接收的焦点距离反馈值, 并将反馈值代入模糊 PID 控制算法中从而获取所需的对电机的控制电压信号, 实现焦点距离的闭环控制。 焦点位置控制子程序流程图如图 11 所示。
4.实验结果
在系统测试平台上, 对系统的具体功能和性能指标进行详的测试。 设置完激光切割参数后 (激光焦点位置参数设置为1mm),系统执行回零操作使切割头位于高处 ,按下数据标定按钮系统进行自动标定;标定完成后,系统接收到机床运动控制卡发送过来的跟随信号后会自动进行焦点位置调节。为了便于系统控制效果的定量分析,通过主控 DSP 输出一路与焦点位置值成正比的模拟电压信号, 并采用运算放大器对信号进行适当放大后再接入示波器进行观测。 在测试过程中,主要是观测在阶跃信号输入下系统响应速度以及跟随稳定性。经过实际切割和示波器波形观测,系统的测量精度要很高,偏差低于 0.05mm,焦点距离控制的精度也达到了 0.1mm,并且在启动 2 个交流伺服电机模拟电磁干扰的情况下系统仍然能够正常稳定工作;焦点控制系统满足设计预期,符合金属激光切割机的切割要求。
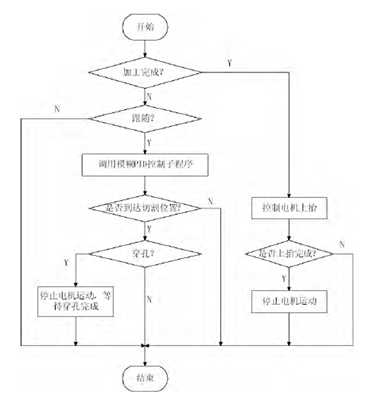
图 11 焦点位置控制子程序流程图
投稿箱:
如果您有机床行业、企业相关新闻稿件发表,或进行资讯合作,欢迎联系本网编辑部, 邮箱:skjcsc@vip.sina.com
如果您有机床行业、企业相关新闻稿件发表,或进行资讯合作,欢迎联系本网编辑部, 邮箱:skjcsc@vip.sina.com
更多相关信息