高速切削过程绝热剪切局部化断裂预测
2017-1-16 来源:大连理工大学精密和特种加工教育部重点实验 作者:谷丽瑶 王敏杰
摘要:基于高速切削过程绝热剪切饱和极限理论,结合锯齿形切屑绝热剪切带的变形和受力条件,以及材料的动态塑性本构关系,建立以切削速度、切削厚度和刀具前角为预测变量的高速切削过程绝热剪切局部化断裂的预测模型,并以淬硬45 钢和FV520(B)不锈钢为例,预测其发生绝热剪切局部化断裂的临界切削条件。通过高速切削试验和金相试验,讨论了切削条件对绝热剪切局部化断裂过程的影响规律和敏感程度,验证了绝热剪切局部化断裂的预测结果。结果表明:较大切削厚度和较小刀具前角会降低绝热剪切局部化断裂的临界切削速度,建立的绝热剪切局部化断裂预测模型能有效预测切屑发生绝热剪切局部化断裂的临界切削条件。
关键词:高速切削;绝热剪切;锯齿形切屑;断裂;预测
0.前言
切削过程绝热剪切带(ASB)的出现预示着切屑将发生断裂分离。已有试验表明[1-4],随着切削速度的不断提高,带状切屑会向着含有ASB 的锯齿形切屑、到沿ASB 断裂的分离状切屑发展,对应主剪切区的材料会依次经历均匀变形、绝热剪切失稳[5-9]、绝热剪切局部化、绝热剪切局部化断裂(ASLF)。因此,绝热剪切局部化断裂作为高速切削过程绝热剪切演化的结果,难免会造成切削系统的颤振、刀具的磨损和破损,以及切屑形态的改变,研究这种断裂行为有助于深入理解高速切削机理,促进高速切削技术的更好应用。
有学者对锯齿形切屑剪切带的断裂行为作了相关试验和理论研究。KOMANDURI 等[2]通过对镍合金的高速切削试验发现,主剪切区的热集中导致了锯齿形切屑的断裂。GENTE 等[10]通过切屑根部试验观察了钛合金剪切带的形成和裂纹的扩展。BARRY 等[11]对合金钢锯齿形切屑剪切带的断面进行了显微观察,发现高温会引起剪切带的韧性断裂。苏国胜[12]通过高速切削试验认为材料脆性的增强导致了齿形切屑的断裂。王敏杰等[1]通过微观试验观察了高强度钢的绝热剪切演化过程,获得了锯齿形切屑断裂的切削条件。SOWERBY 等[13]提出了利用损伤因子来预测锯齿形切屑形成和裂纹出现。MARUSICH 等[14]采用连续的网格再划分和自适应性网格技术,并结合断裂因子模拟了切削高强度钢时裂纹的出现和扩展。XIE 等[7]指出利用流动局部化参数结合FEM 软件来判断锯齿形切屑的断裂条件。GUO 等[15]利用JC 损伤模型并结合FEM 技术模拟了高强度钢锯齿形切屑的断裂过程。HUA 等[16]通过FEM 仿真技术分析了钛合金锯齿形切屑的断裂过程。在后续研究中,王敏杰等[4,17]通过对淬硬钢的高速切削试验发现,剪切带的形成和断裂具有能量相关性规律,并提出了绝热剪切局部化断裂的饱和极限理论。切削过程绝热剪切变形条件和能量的计算结果表明,对于主剪切区的塑性变形环境,切削速度的提高意味着热集中和能量的提高,其结果必然会导致绝热剪切的发生和锯齿形切屑的形成。之后,当切削速度的提高使剪切带能量超过其所能承受的最大范围时,就会以发生断裂和毁坏的形式释放能量,使相邻锯齿沿剪切带断裂分离。
本文以绝热剪切饱和极限理论为基础,结合绝热剪切变形条件和材料动态塑性本构关系,建立高速正交切削过程绝热剪切局部化断裂临界切削条件的预测模型,以淬硬45 钢和FV520(B)不锈钢为例,进行绝热剪切局部化断裂临界切削条件的预测。通过高速车削试验和金相试验,将预测结果与试验结果进行比对,分析切削速度、切削厚度和刀具前角及材料特性对绝热剪切局部化断裂的影响规律和敏感程度,进一步验证绝热剪切行为的能量相关性规律及预测方法的正确性。
1.高速切削过程绝热剪切局部化断裂预测模型
(1) 绝热剪切局部化断裂力学判据。根据绝热剪切饱和极限理论[4,17],高速切削过程中主剪切区材料在受热软化及刀具扰动的作用下会引发热塑性波的传播,建立Lagrange 坐标系如图1 所示,热塑性区材料在正交切削条件下满足的连续介质控制方程为
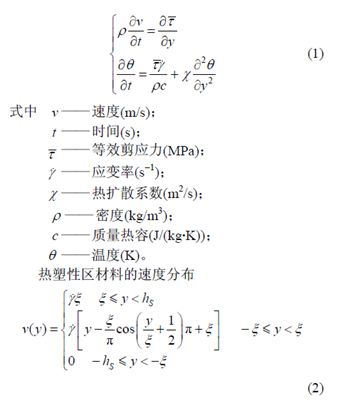
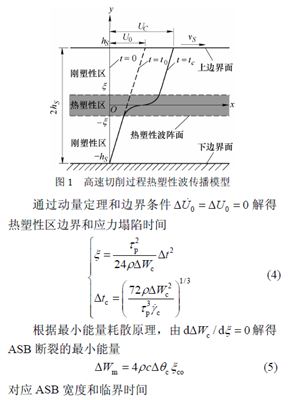
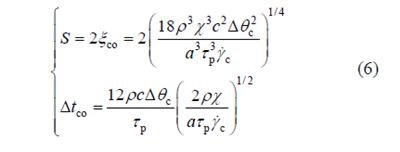
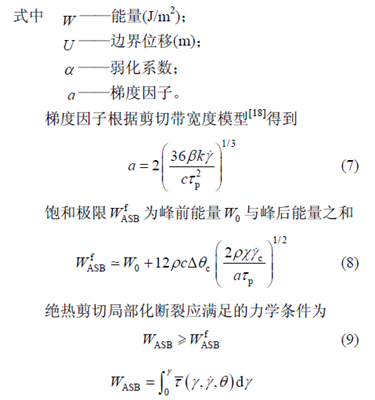
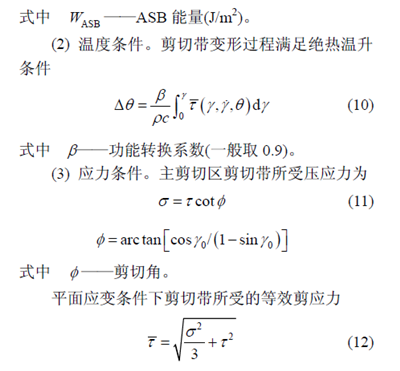
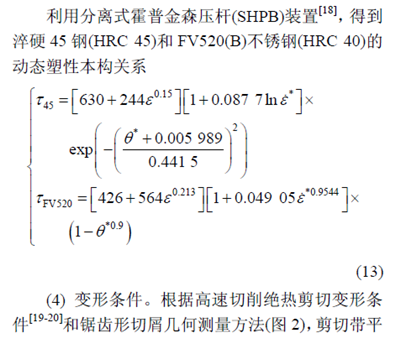
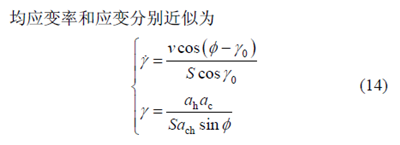
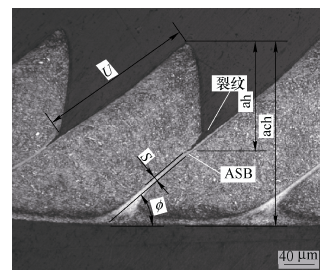
图2 锯齿形切屑几何形态测量
3.高速切削过程绝热剪切局部化断裂预测过程
根据式(1)~(14)构成的绝热剪切局部化断裂预测模型,剪切带的剪应变主要由刀具前角和切削厚度决定,剪应变率主要由切削速度决定。剪切带的压应力、剪应力、温度和能量取决于切削速度、刀具前角和切削厚度。不同切削条件下剪切带能量的理论结果与试验结果如图3 所示,图3 中随切削速度和进给量的增大,剪切带能量的聚集程度也逐渐升高,并最终达到饱和极限。因此,通过输入材料热物理参数、动态塑性结构参数,结合剪切带能量计算模型,就能够得出达到饱和极限时的临界切削条件。
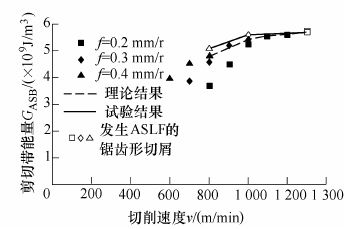
图3 淬硬45 钢不同切削条件下剪切带的能量
根据上述基本思想,计算出淬硬45 钢和FV520(B)不锈钢绝热剪切局部化断裂的临界切削条件计算结果分别如图4 所示。图4 中曲面为绝热剪切局部化断裂的临界切削条件,曲面上侧和下侧分别代表切屑发生和未发生绝热剪切局部化断裂的速度区域,结果表明两种材料绝热剪切局部化断裂的临界切削速度随刀具前角的减小、切削厚度的增大而减小。
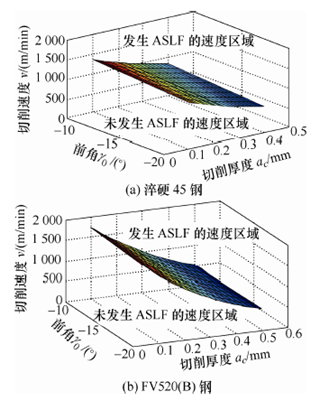
图4 绝热剪切局部化断裂预测结果
4.高速切削试验验证与讨论
4.1 试验条件和过程
为了满足高速正交切削条件的试验要求,采用OKUMA MULTUS-BW400 车铣复合加工中心进行干式车削试验,试验系统如图5 所示。采用的切削参数为切削速度:0~1 400 m/min,切削厚度:0.2~0.5 mm,背吃刀量:2 mm. 淬硬45 钢选用PCBN刀片,Fv520(B)不锈钢选用硬质合金刀片,刀具几何为前角:–10°、–20°,后角:6°. 将试验得到的切屑试样垂直镶嵌在牙托粉中,然后通过研磨、抛光和腐蚀, 制成金相显微观察试样, 利用LELCSAMEF4A 金相显微镜进行观察。
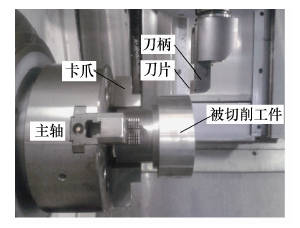
图5 高速正交车削试验系统
4.2 试验结果与讨论
4.2.1 切削条件对切屑形态的影响
图6 为淬硬45 钢切屑形态随切削条件的变化情况。图6a、6b 中,在切削厚度0.2 mm、刀具前角–10°的条件下,切削速度从1 200 m/min 增大到1300 m/min 时,带有裂纹的转变带锯齿形切屑沿剪切带完全断裂;图6c、6d 中,在刀具前角–10°和切削速度800 m/min 的条件下,切削厚度为0.2 mm 增大到0.4 mm 时,锯齿之间的连接程度逐渐减弱,直到完全断裂;图6e、6f 中,在切削速度1200m/min、切削厚度0.2 mm 条件下,刀具前角从-10°减小到–20°时,锯齿化程度迅速增大,最后裂纹扩展到了切屑底部。图7 为FV520(B)不锈钢切屑形态随切削条件的变化情况,基本与淬硬45 钢相似。
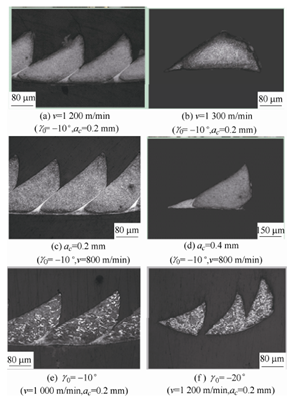
图6 淬硬45 钢切屑形态
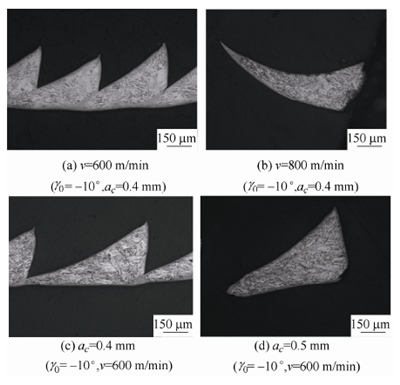
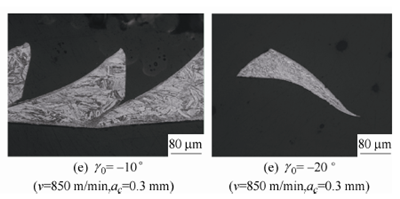
图7 FV520(B)不锈钢切屑形态
试验结果表明,切削速度越高、切削厚度越大、刀具前角越小,切屑越容易发生绝热剪切局部化断裂。切削速度的提高会使剪切带应变率增大,剪切带变形时间缩短,带内热量得不到有效散失,致使带内能量的聚集程度逐渐加剧而发生绝热剪切局部化断裂。进给量的增大会使剪切带内的应变得到提高,同时一定程度上也会增大主剪切区的压应力,使剪切带在较低的切削速度下达到饱和极限。刀具前角的减小会提高剪切带应变、压应力、等效剪应力、峰值应力,从而提高剪切带的能量聚集程度。我们通过观察淬硬45 钢的切屑根部照片[17]发现,绝热剪切局部化断裂虽然短暂,但也经历了绝热剪切的演化过程,随着刀具的切削移动,主剪切区材料不断聚集能量,使局部化变形区发生相变而与周围基体组织的界限趋于明显,裂纹沿转变带扩展,随着锯齿被刀具挤压推出,剪切带内能量达到了饱和极限,锯齿沿剪切带完全断裂分离。因此,切削速度是能量聚集和导致绝热剪切局部化断裂发生的必要加载条件。
4.2.2 绝热剪切局部化断裂敏感性分析
淬硬45 钢和FV520(B)不锈钢发生绝热剪切局部化断裂试验结果基本与预测结果一致,如图8、9所示,其中,虚线代表绝热剪切临界速度曲线,实线代表绝热剪切局部化断裂临界速度曲线,实线右侧为绝热剪切局部化断裂的锯齿形切屑。结果表明:在切削厚度小于0.3 mm 和刀具前角大于.10°的条件下,淬硬45 钢绝热剪切局部化断裂的临界切削速度要低于FV520(B)不锈钢,在进给量大于0.4 mm和刀具前角小于–20°的条件下,则相反。
从绝热剪切饱和极限理论可知,材料的导热性越差,其在高速切削条件下,短时间内就会聚集大量的热,使材料塑性增强而发生绝热剪切。形成的剪切带受高温热软化效应的影响若不容易聚集较高的能量,而不容易发生绝热剪切局部化断裂。由此推断,FV520(B)不锈钢含有的奥氏体虽然具有较差的导热性,但其含有的大量马氏体加工硬化效应较高,形成剪切带之后会保持较好的应力状态,则容
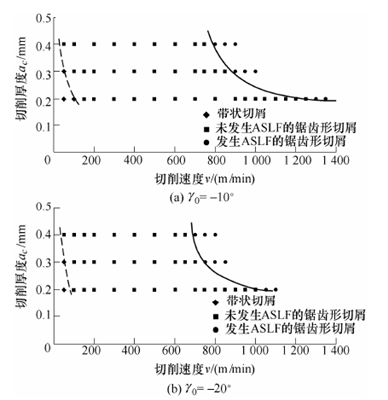
图8 切削条件对淬硬45 钢绝热剪切局部化断裂的影响
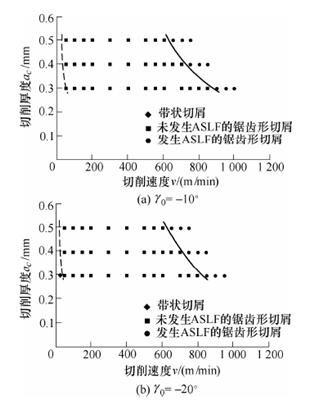
图9 切削条件对FV520(B)钢绝热剪切局部化断裂的影响
易聚集能量而发生绝热剪切局部化断裂。淬硬45钢虽然不容易发生绝热剪切,但其回火索氏体同样具有较好加工硬化程度,在形成剪切带之后的也会保持较好的应力状态,也比较容易发生绝热剪切局部化断裂。另外,较小切削厚度容易使FV520(B)不锈钢受热软化效应的影响,而淬硬45 钢的较好导热性使其受温度的影响相对较小,因此导致不同切削厚度条件下发生绝热剪切局部化断裂时临界切削速度的不同。在较小刀具前角条件下,剪切带剪应变和应变率虽然得到了提高,但会显著提高主剪切区的压应力,而FV520(B)不锈钢在试验中展现出相对较强的压应力敏感特性,因此,其发生绝热剪切局部化断裂的切削速度在较小刀具前角的条件下较淬硬45 钢要低一些。因此,在高速切削条件下具有导热性好、加工硬化程度高、对压应力敏感的材料绝热剪切局部化断裂的敏感程度越高。
4.2.3 预测结果与试验结果比对
通过高速车削试验将淬硬45 钢和FV520(B)不锈钢不同刀具前角和切削厚度条件下的试验结果与预测结果进行比较,结果如图10、11 所示,图中显示了完全断裂分离和未完全断裂分离的锯齿形切削速度区域,两条曲线基本趋势相同,预测结果与试验结果基本一致,当高于临界切削速度条件进行车削时,就会产生完全断裂的锯齿。为了分析绝热剪切局部化断裂临界切削条件预测结果的准确性,采用相对误差计算公式切削速度的预测值Vp 与试验值Vm 的相对误差

通过计算,淬硬45 钢的相对误差基本控制在±12%的范围内,其中最大误差为11.8%;FV520(B)不锈钢绝热剪切局部化断裂预测结果的相对误差基本控制在±15%的范围内,其中最大误差为–14.2%;以上绝热剪切局部化断裂的预报结果,在材料常用的高速切削工艺参数范围内,基本满足实际应用的要求。
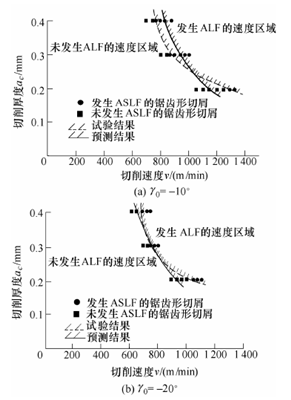
图10 淬硬45 钢绝热剪切局部化断裂预测结果与试验结果
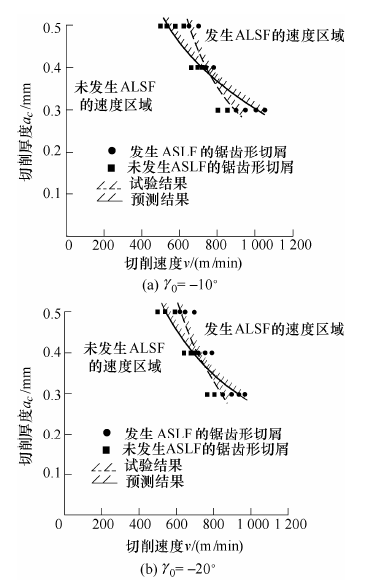
图11 FV520(B)钢绝热剪切局部化断裂的预测结果与试验
经过分析,造成预测结果与试验结果的偏差主要来源于:在理论方面,由于绝热剪切控制方程、材料动态塑性本构关系、锯齿形切屑的受力和变形,以及在求解过程中应用的理想假设条件和估计方法等等进行的简化,会使预测模型与实际情况存在一定的偏差;在试验方面,试验材料在制备过程中存在的缺陷和均匀程度分布较难控制,热处理过程中由于温度不均衡会出现材料性能的不均匀性等,难免会对试验数据造成一定的影响。由此可见,高速切削过程绝热剪切局部化断裂行为具有一定的复杂性,其发生过程难免会受到诸多可知和未知因素的影响。然而,随着高速切削技术的发展和材料特性研究工作的不断深入,应用此绝热剪切局部化断裂预测模型可在少做、甚至不做试验的情况下得到绝热剪切局部化断裂发生的临界切削条件,为今后进一步理解锯齿形切屑的绝热剪切局部化断裂行为对切削实际的作用提供充分的理论和试验依据。
5.结论
(1) 在饱和极限理论的基础上,建立了高速切削过程绝热剪切局部化断裂的预测模型,预测了淬硬45 钢和FV520(B)不锈钢绝热剪切局部化断裂的临界切削条件。结果表明:绝热剪切局部化断裂的临界切削速度随刀具前角的减小、随切削厚度的增大而减小。
(2) 切削速度是绝热剪切局部化断裂发生的必要加载条件,切削速度的提高会使剪切带能量聚集程度增大,使锯齿形切屑发生绝热剪切局部化断裂。
(3) 具有导热性好、加工硬化程度高、对压应力敏感的材料,在高速切削条件下的绝热剪切局部化断裂敏感程度越高。
(4) 高速切削过程绝热剪切局部化断裂的预测结果与试验结果基本吻合,验证了绝热剪切饱和极限理论及预测模型的正确性。
投稿箱:
如果您有机床行业、企业相关新闻稿件发表,或进行资讯合作,欢迎联系本网编辑部, 邮箱:skjcsc@vip.sina.com
如果您有机床行业、企业相关新闻稿件发表,或进行资讯合作,欢迎联系本网编辑部, 邮箱:skjcsc@vip.sina.com