高速切削GCrl5切削力的仿真与实验研究
2017-1-12 来源:郑州科技学院机械工程学院 作者:邱慧,班新星,纪莲清,王明义
摘要:应用Deform.3D软件建立刀具一工件三维有限元模型,研究了PCBN刀具高速切削GCrl5淬硬钢的切削机理,得出不同切削参数下切削力的变化规律,通过对模拟结果进行分析获得了最优切削参数。在最优切削参数下进行切削实验,结果发现:在切削深度和进给量不变的情况下,不同切削速度下的切削力模拟值与实验值变化趋势是一致的,并且其误差不超过10%,这表明利用Deform-3D有限元软件建立三维切削模型可以有效模拟PCBN刀具高速切削GCrl5轴承钢的切削过程。
关键词:有限元模拟;高速切削;超硬刀具;切削力
0.引言
聚晶立方氮化硼(Polycrystalline Cubic Boron Nitride,简称PCBN)作为超硬刀具材料,具有良好的耐磨性和热稳定性?,普遍应用于淬硬钢、冷硬铸铁及其它高硬黑色金属的高速切削加工旧J,并且随着数控机床等自动加工设备的广泛应用,使用PCBN刀具以硬态切削替代磨削工艺已成为加工淬硬轴承钢的新途径。GCrl5是一种最常用的高铬轴承钢,经过淬火加回火后具有较高的硬度,其硬度可达HRC60—62,主要应用于制作各种轴承套圈和滚动体,属于难加工材料行列Ho。近年来,国内外很多学者对PCBN刀具高速切削GCrl5的过程进行了研究分析p剖,主要集中在PCBN刀具的磨损机理、刀具几何参数、GCrl5表面粗糙度、切屑形成机理、残余应力、表面白层等方面,而针对PCBN刀具高速切削GCrl5切削力的研究较少。文中通过使用有限元软件Deform.3D,系统研究了PCBN刀具高速切削GCrl5时削参数对切削力的影响,得到了切削力随切削参数的变化规律,并通过切削实验进行验证。
1.材料与模型
1.1刀具材料
在硬态车削加工中,由于低含量CBN刀具比高含量CBN刀具拥有较高的抗冲击性能和刀具耐用度一],并且具有更好的加工表面质量,通常采用CBN含量较低的PCBN刀具,其机械性能如下:弹性模量587GPa;密度4280kg/m3;泊松比0.15;比热容750J/kg·℃;热传导系数44W/m·oC;热膨胀系数4.7×10“/℃。本实验所用的PCBN刀具几何参数为刃倾角A,为0。,前角7。为0。,后角仅。为6。,刃口钝圆半径。为0.4mm。
1.2工件材料
高铬轴承钢GCrl5具有高淬透性,经热处理后可获得硬度为62HRC,属于典型的难加工材料¨0l,其物理力学性能如下:杨氏模量217GPa;密度7850kg/m3;熔点1487℃;泊松比0.3;热传导系数39W/m·℃;热膨胀系数14.4 X 10~/。C。
1.3材料的本构模型
目前,在应用计算机软件进行模拟时,广泛使用的本构模型是Johnson—Cook模型,它能够很好的描述大部分金属在大变形、高应变率和高温条件下的材料本构行为,其表达式为:
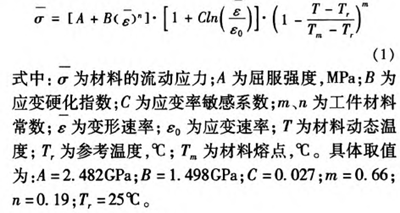
1.4材料的失效模型
Johnson—Cook模型以等效塑性应变作为材料的断裂原则,提出以下材料失效模型:
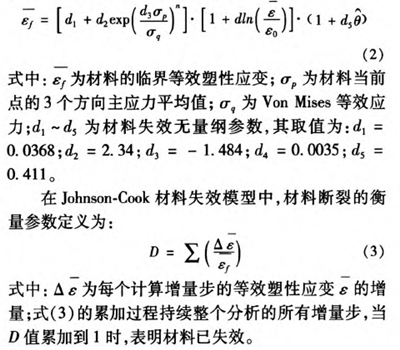
2.切削模拟
2.1切削模拟参数选择
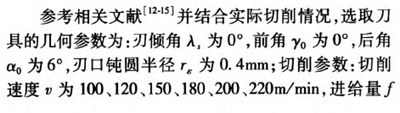
为0.05、0.10、0.15、0.20、0.25mm/r,切削深度口。为0.1、0.15、0.2、0.25、0.3mm。
2.2切削力模拟结果及分析
切削力是切削过程中重要的物理参数之一,它的大小不仅影响加工工艺系统,还影响着工件的加工质量和加工精度¨6|。因此,研究加工过程中切削参数对切削力的影响规律,可以为高速切削加工中切削参数的选择提供科学的理论依据。
在模拟过程中,切削力并非是稳定不变的,而是在某一平衡值附近上下振荡,这与实际切削过程中切削力的变化是一致的。造成这种现象的原因是,在实际切削中,随着刀具刚接触工件,材料会先产生弹性变形,接着工件材料内部的晶格进行滑移并发生塑性变形,此时切削力增大;随着刀具的继续前进,在切削刃附近会出现应力集中,当材料的金属剪应力超过强度极限时,切屑就被剥离,此时切削力会相应随之降低。此过程周而复始,因次切削力曲线为一定范围内的振动波,如图l所示。将切削力以文本格式进行输出,然后求其均值即可得出模拟切削力大小。
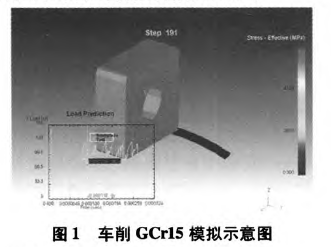
2.2.1切削速度对切削力的影响
进给量.厂和切削深度n。分别为0.05mm/r、0.1rain,切削速度与切削力之间的关系如图2所示。切削速度从100m/min增加到220m/min,进给分力F,和径向抗力F:变化非常小,上下浮动大约在1N左右,而主切削力F。的变化相对较大,最大浮动达到11N。当切削速度从100m/rain增加到180m/min时,进给分力F,和径向抗力t随着切削速度的增加而略有增加,但变化并不是很明显,上下浮动不超过0.1N;主切削力F。随着切削速度的增加而增大,增大幅度达到7.2N,这主要是因为主切削力F,垂直于基面,与切削速度的方向一致。当切削速度从180m/min增加到220m/min,进给分力t和径向抗力t随着切削速度的增加而略有减小,主切削力F,随着切削速度的增加而降低.
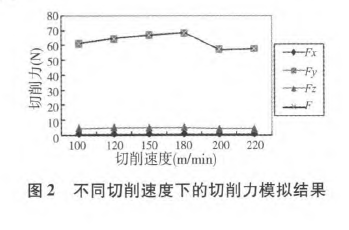
2.2.2进给量对切削力的影响
切削速度秽和切削深度a。分别为150re/rain、0.1mm,进给量与切削力之间的关系如图3所示。进给分力t、径向抗力t和主切削力t都随着进给量的增加而增加,切削合力也随着进给量的增加而增加在刀具切削时,三个切削分力中主切削力F,是最大切削分力,对切削合力起主导作用,进给量厂的改变引起最大变化的切削分力是主切削力,所以进给量,的改变也使得切削合力发生巨大变化。当进给量从0.05mm/r增至0.25mm/r时,切削合力从66.8N增大到191.1N。3
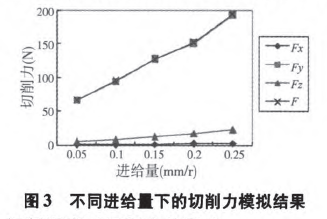
2.2.3切削深度对切削力的影响
切削速度秽和进给量,分别为150m/rain、0.1mm/r,切削深度与切削力之间的关系如图4所示。切削深度%对切削力的影响最大,%每增加一倍,切削力也增大一倍。这是因为切削深度a。增大,切削面积A。成正比增加,弹塑形变形总量及摩擦力增加,而单位切削力不变,因而切削力成正比增加。当切削深度从0.1mm增加到0.3mm时,切削合力从94.7N增加到283.5N,可见,在切削用量中,切削深度对切削力的影响最大。
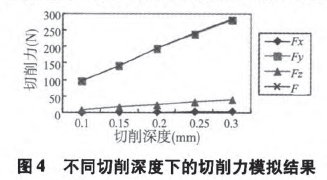
综上所述,从模拟结果中可以看出,切削深度%对切削力的影响最大,进给量厂次之,切削速度移最小。切削力随着切削深度1/,。的成倍增加而成正比增加,这是因为切削深度a。增大,切削面积A。成正比增加,摩擦力及弹塑形变形总量也相继成正比增加;进给量厂对切削力的影响次之,切削面积A。随着进给量,增大也相应增加,但是其变形程度减小,致使单位切削力下降,因而切削力并不随着,成倍增加而增加;切削速度口对切削力的影响最小,并且在速度增加到一定程度时,切削力反而会相应减小,并趋于某一稳定值。为保证刀具的耐用度及切削效率,加工GCrl5的工艺参数应选择较高的切削速度、较小的切削深度和进给量,推荐选取:切削速度为150m/rain,切削深度为0.1mm,进给量为0.1mm/r。
3.切削实验
3.1实验参数及设备
实验刀具:采用郑州博特硬质材料有限公司生产的PCBN刀具,刀杆使用45。偏头外圆车刀刀杆CSSNR2525—150,刃倾角A;为0。,前角^y。为00,后角%为60,刃I=l钝圆半径0为0.4mm。加工工件GCrl5轴承钢。切削参数:切削速度"分别为100、150、200m/rain,进给量厂为0.1 mm/r,切削深度o,为0.1mm。实验设备:车床采用CA6240;测力系统采用瑞士Kisfler9257B三向测力仪。
3.2实验结果及分析
切削过程中使用测力装置获得电信号,经过电荷放大器放大,并对信号进行数据收集,最后通过利用D”o Software软件对信号进行分析处理,从而得出切削力数值显示在计算机上,如图5所示,将切削力数值以文本格式输出,取稳态部分求均值即可得到切削过程中切削力的大小。
图6显示了模拟过程同实验过程中切削力的对比情况,从对比曲线中可以看出,切削力模拟值与实验值的变化趋势是一致的,切削速度从100m/min增加到150m/min,切削力也相应的增加,当切削速度为200m/rain时,切削力有所下降,这符合高速切削的变化规律。比较切削力模拟值和实验值可知,实验值比模拟值要大,不过,模拟值与实验值的误差不超过10%,究其原因是由于刀具磨损增大导致刀具角度改变造成的。在实际切削过程中,由于GCrl5中存在大量的硬质颗粒,刀具磨损较大,使得刀具一切屑接触面积减少,加剧刀具的磨损,使刀具角度在较短切削时间内发生了很大改变,刀具变钝,刀具前角增大,造成切削过程中切削力的增大。
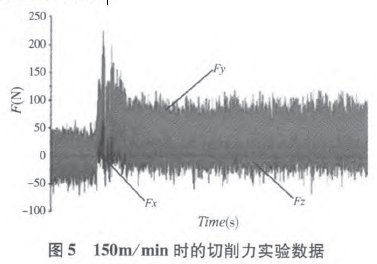
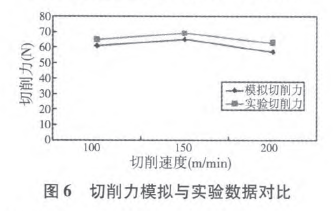
4.结论
通过对PCBN高速车削GCrl5过程进行模拟,得到了切削参数对切削力的影响规律和最佳切削参数,同时在最佳切削参数下进行切削实验,得到以下结论:
(1)应用Deform软件建立三维有限元模型并对切削过程进行仿真,得出切削参数对切削力的影响规律,发现切削力随着切削速度、切削深度和进给量的增加总体上呈上升趋势。
(2)通过对模拟结果分析获得了PCBN刀具高速切削GCrl5最佳切削参数:切削速度为150m/min,切削深度为0.1mln,进给量为0.1mln/r。
(3)切削实验表明,在切削深度和进给量不变的情况下,不同切削速度下的切削力模拟值与实验值变化趋势是一致的,并且其误差不超过10%,进一步验证了使用Deform软件建立有限元模型并对切削过程进行仿真可以准确模拟C,Crl5轴承钢的切削加工过程。
投稿箱:
如果您有机床行业、企业相关新闻稿件发表,或进行资讯合作,欢迎联系本网编辑部, 邮箱:skjcsc@vip.sina.com
如果您有机床行业、企业相关新闻稿件发表,或进行资讯合作,欢迎联系本网编辑部, 邮箱:skjcsc@vip.sina.com
更多相关信息