车床主轴箱体采用不同定位基准的孔径加工精度的仿真
2016-11-17 来源:辽宁科技大学机械工程与自动化学院 作者:王梓卉敏,梁楠,李润强,柴紫维,徐泽宁
摘要:针对某型车床主轴箱体孔径加工的特点和采用不同的定位基准对孔与孔之间的位置精度的直接影响,选择3 种不同的定位方式来进行对比,即以较大的孔为定位基准、以较小的孔为定位基准和孔之间互为基准进行仿真,选择最佳的定位基准来提高某型主轴箱体主要孔径的加工精度。研究结果表明,采用小孔为定位基准来保证孔与孔之间的位置精度优于较大的孔为定位基准。
关键词:主轴箱体;孔径加工;仿真分析;定位基准;加工精度
车床主轴箱体的平面孔系很多,通常加工的计算量很大,为快速解决平面孔系加工精度问题,查阅了大量的文献资料,未见相关报道。因此,本文提出了关于平面孔系采用不同孔径作为定位基准进行多孔加工对孔间加工精度影响方面的研究。在主轴箱体的平面孔系加工过程前进行数控编程时,系统生成孔的加工位置坐标,可自由变换不同定位基准。在仿真加工中,并不断优化其加工路径,这样不仅可以更好地保证孔间的位置精度,确保设计的程序科学合理,同时节省了大量的人力与财力。为实际的加工生产提供了可靠的依据。本文的主要研究内容是通过UG NX软件进行三维实体建模后,确定加工仿真的方法和路线对某型箱体进行加工仿真,以不同方式进行孔的定位,来对比孔间位置精度的相对误差。
1.箱体的三维建模
以某型主轴箱体为例进行三维建模。建成的三维模型如图1所示。
2.主轴箱体加工仿真过程流程图
实现对数控加工过程的仿真,首先需要在仿真软件中构建机床运动结构,配置相应的数控系统,加载毛坯、工装夹具、刀具、数控程序等加工要素。主轴箱体加工仿真流程图如图2所示。
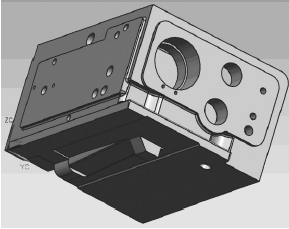
图1 主轴箱体三维模型
3.某型箱体平面孔系位置精度仿真
当进行孔的加工模拟时,因为箱体表面的孔很多,所以会涉及到孔定位问题。因此,选择3 种不同的定位方式,来对孔与孔之间的距离进行比较,选取位置公差最小的方案,这样可以有效地提高主要孔径的位置精度。
第一种:以箱体表面较大的孔1 为定位基准,再加工同一表面其余的孔。第二种:用孔之间互为基准的方式来定位,再加工同一表面其余的孔。第三种:利用箱体较小的孔10 进行定位,再加工同一表面其余的孔。
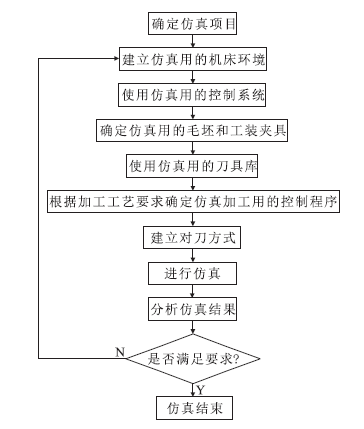
图2 主轴箱体加工流程图
因为此平面需要加工的孔较多,所以对其进行编号。编号如图3所示。
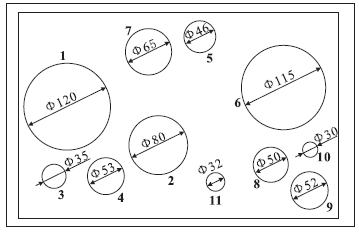
图3 孔径及编号
为了更加直观地观察孔距之间的距离,截取孔1-4,1-6,1-10 之间的孔距。以孔1 为基准得到的结果如图4 所示。图5 为互为基准的定位中孔1-4,1-6,1-10 之间的孔距。图6 为以孔10 为定位基准孔1-4,1-6,1-10之间的轴距测量图。
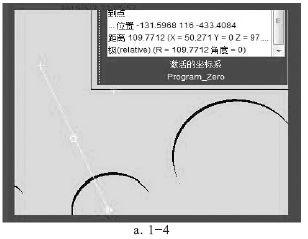
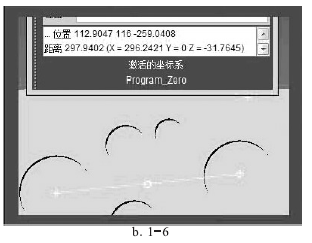
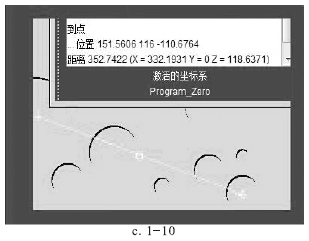
图4 1-4,1-6,1-10 之间的仿真孔距
因篇幅所限,仅截取3 组孔距的对比图,其余数据如表1~表3 所示。由表1~表3 可以计算出,采用孔1 为定位基准得到的位置精度相对误差的平均值为0.254%,使用孔之间互为定位基准其值为0.401%,而以孔10 为基准时,得出的结果是0.169%。根据以上3 个表格,以不同方式进行孔的定位,孔距之间的位置精度相对误差的变化如图7。依据图7 的曲线变化可以得出,以小孔10 作为定位基准得到的孔距位置精度相对误差较小,以大孔1 为定位基准时,其值稍大一些,以孔互相定位的方式,其相对误差最大。这说明,以小孔定位可以更好地保证箱体中孔与孔之间的位置精度。
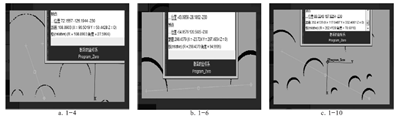
图5 1-4,1-6,1-10 之间的仿真孔距
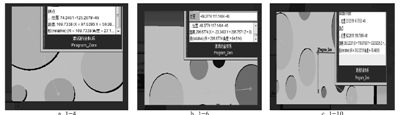
图6 1-4,1-6,1-10 之间的仿真孔距
表1 以孔1 为定位基准的孔距
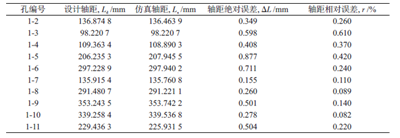
表2 互为定位基准的孔距
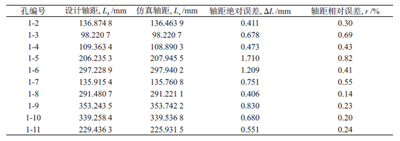
表3 以孔10 为定位基准的孔距
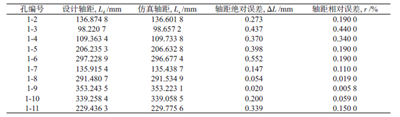
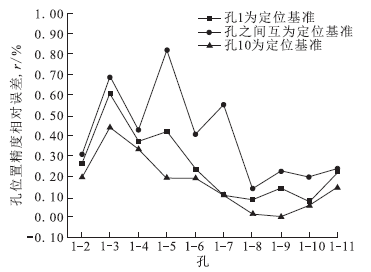
图7 不同定位方式孔位置精度相对误差
4.结论
在某型箱体定位方式的选择上,采用孔1 为定位基准时,位置精度相对误差平均值为0.254%,使用孔之间互相定位时,其值为0.401%,用孔10 为定位基准得到的值为0.169%。通过三者数值的比较可以发现,采用孔10 为定位基准比孔1 为基准,位置精度提高了0.085%,比孔互为基准精度提高了0.232%,所以使用较小孔为定位基准,可以更好地保证孔与孔之间的位置精度。因为采用较大的孔为定位基准,孔本身的尺寸精度就有较大误差,而使用孔互相定位的方法,产生的累积定位误差很大,所以无法确保孔径之间的位置精度。
投稿箱:
如果您有机床行业、企业相关新闻稿件发表,或进行资讯合作,欢迎联系本网编辑部, 邮箱:skjcsc@vip.sina.com
如果您有机床行业、企业相关新闻稿件发表,或进行资讯合作,欢迎联系本网编辑部, 邮箱:skjcsc@vip.sina.com