CK61200车床的关键结构设计及其主轴有限元分析术
2016-10-28 来源:江苏大学机械工程学院 作者:顾寄南,熊伟,陈功,刘家博
摘要:论文先简要介绍自行设计的CK61200系列(32t)重型数控车床的关键结构,包括双刀架及其控制系统和主轴,然后以该车床主轴为重点研究对象,在考虑加工工件自身重力的工况下,基于有限元理论。运用ANSYS Workbench软件对其进行静态、模态分析。在产品设计阶段,分析得出主轴的最大变形和最大应力,以此可以判断刚度是否足够;分析得出其固有频率和振型,以此可以避开共振区域。而上述求得的主轴动静态参数均在合理范围内,验证了主轴设计的合理性,为后续进行机床的整机有限元分析及优化设计奠定基础。
关键词:CK61200车床;关键结构;有限元分析
0.引言
数控机床的高速化和高精密化是其主要发展趋势之一。而主轴系统是数控机床的关键部件,其静态、动态性能的好坏直接影响到机床的最终加工质量和切削效率?。随着机床加工速度和精度的不断提高,对其主轴部件也提出了更高的设计和加工制造要求。因此,国内外众多研究机构和科研院所对主轴部件的动静态特性展开了广泛、深入的研究¨1。
现阶段对机床主轴的结构力学分析研究主要有以下两点不足之处:①将主轴孤立的进行分析,很少考虑在加工过程中,加工工件自身的重力对主轴的影响。这种分析方法只适用于小型机床。但是对于本研究中的重型机床而言,由于加工工件本身的质量很大,对主轴性能的影响也非常大,故工件自身重力不能忽略p J。②多利用经验公式对主轴进行计算,其结果精度难以保证。而有限元法具有很多传统方法无法比拟的优点,如精度高,适应性强以及计算格式规范等,尤其在分析大型复杂零部件时,优势更加明显。利用有限元法可以进行静力学分析和模态分析,如果能够很好的简化处理几何模型,选择合适的单元类型,以及控制好边界条件,那么计算效率及结果精度都会大大地提剐引。
1.机床的关键结构设计
图1为自行设计的CK61200双刀架卧式重型数控车床的结构简图,该车床的总质量约150t,其加工工件的最大质量可达60t,最大加工工件长度为6m,按照系谱的规定,最大长度可增加到8m,10m,14m三种规格。主要用来对不同材料的大直径轴类零件、盘状和圆筒形零件进行高速车外圆、切槽、切断、端面、镗孔等半精加工和精加工,也可用于大型轧辊类零件的高速加工。两个数控刀架分别安装在两个滑板上,纵向(z轴)滑板和横向(x轴)滑板。在伺服电机的驱动下,横向滑板分别由两个滚珠丝杠带动,纵向滑板则由齿轮齿条传动。两个刀架均为四工位自动回转刀架,位于主轴的同一侧,可同时进行2轴或4轴联动加工。
与普通机床相比,双刀架数控机床可多刀同时加工,能极大的提高工作效率,但是,目前双刀架数控机床仍没有得到广泛的应用,其中一个主要的原因是传统的双刀架数控机床大多采用两个独立的控制系统”J,由于两个刀架的数据和加工状态相互独立,不能及时交换,因而两刀不能进行相互协调,零件的加工精度很难得到保证,也容易引起加工故障。本机床采用西门子840D双通道、双方式组控制系统,双刀架系统连接简图如图2所示。该系统配置了一个主轴模块MSD和两个双轴驱动模块FDD。每个刀架分别配置了一个手持单元,两个伺服电机,共用一个OP010、一个PCU20和一个操作面板MCP。PLC为该系统自带的$7-300。通道1(第一方式组)包括:车床主轴SP、左刀架坐标轴Xl和Z1;通道2(第二方式组)包括:车床主轴sP、右刀架坐标轴胞和z2。由于共用一个系统。上述问题得到了很好的解决,两个刀架可以相互协调加工,极大的提高了加工的效率和精确性。另外,由于采用了统一的标准,使得编程和操作更为简洁方便。此外,为了保证该双刀架机床的安全可靠性,还设置了硬限位(数控机床的硬件限位)和软限位(依据机床数据限定)双重安全保护措施旧1。
CK61200机床主轴系统的结构如图3所示。主轴部件可实现分段无级变速,设计的转速范围:500—10000r/min。该机床主轴采用双支撑结构,均采用NSK高精度陶瓷球轴承。主轴前支撑采用双圆柱滚子轴承来承受径向力,可以提高机床主轴径向刚度及主轴的回转精度,同时还采用了背靠背安装的角接触球轴承来承受主轴的轴向力以及降低主轴轴向窜动量,提高轴向刚度;后支撑选用带内锥孔的圆柱滚子轴承来承受主轴径向力。
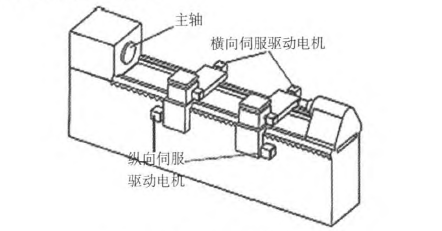
图1 CK61200车床结构简图

图2双刀架系统连接简图
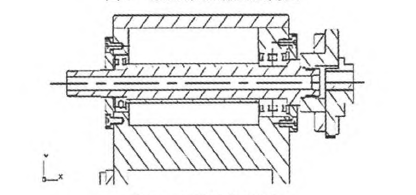
图3主轴结构简图
2.主轴所受载荷分析与计算
在加工过程中,主轴在低速传动全功率的时候力学性能最差,传递全功率的最低转速称为计算转速_7l。为分析主轴的最大变形和应力,现计算在低速重载工况下的受力参数。电动机通过一系列的齿轮传动将动力传到主轴,带动其转动。查阅相关技术资料后可知,CK61200机床计算转速/7,。=150r/min电动机功率P=80KW,工作效率为0.8,由公式:
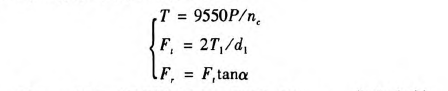
取d=200,得到转矩T=5093.3N·m,求出主轴在齿轮处所受到的圆周力F=15160N,径向力F,=5518N。根据设计要求,强力切削时被切削材料为45钢,车刀进给速度K=240mm/min;背吃刀量%=5mm;进给量.厂=1.6mm/r,在切削加工过程中,车刀所受的切削总力,可以分解为三个互相垂直的分力:进给力t,背向力F,和主切削力t。同时,主轴受到车刀相应的反作用力。根据切削力的指数公式:
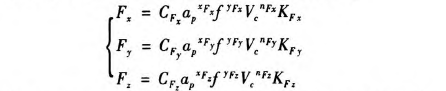
式中:C肌Cn、C凡取决于被加工材料和切削条件的有关系数;戈¨Y¨nt、戈-、YFf、np戈小yf、凡f分别为0P六啡的指数;K,、KF、K,为受切削速度、刀具几何参数、刀具磨损等因素影响的修正系数。以上系数均可通过查表得到,有上述公式可计算到:

3. 主轴有限元模型的建立和边界条件的设定
现以该车床主轴为分析对象,采用三维实体造型软件SolidWorks和有限元分析软件ANSYS Workbench分别完成主轴有限元模型的建立和边界条件的设定。先在SolidWorks中建立主轴的三维实体模型然后导入到ANSYS Workbench中,选用solid45单元类型,自由网格划分完成对主轴三维模型的网格划分,如图4所示。材料选择45钢,其材料属性:弹性模量2.09E+11N/m2,泊松比0.269.密度7.89E+03kg/m3.网格划分结束后,对主轴施加约束以及载荷。
根据工况,在前支撑的节点上施加圆柱面约束限制菇,Y和z方向上的平移,在后支撑上约束Y和z方向上的平移,由此位移约束施加完毕.齿轮和主轴连接传动部分的节点加载E和F,,主轴前端部施加切削力。根据机床设计参数,能加工的工件最大质量为60t,根据此工况,在主轴的右端中心部位加载一个集中力,大小为最大工件重力的一半。这样整个主轴的载荷设置结束。
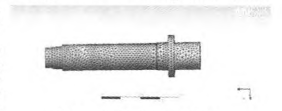
图4主轴有限元模型
4.主轴静力学分析
主轴的静力分析主要包括强度和刚度的计算。对主轴进行静力学分析后,得到了其应力图和变形图。主轴的应力云图如图5所示,它反映了主轴上各个单元的受力情况‘81。从图中可以看出,主轴上的最大应力为9.8x106Pa,小于材料45钢的许用应。力,最大应力出现在主轴与轴肩端面相交的截面上,此处受力最大。主轴的变形图如图6所示,它反映了主轴受力后的变形情况。从图中可以看出,最大变形量为1.247×10~mm,最大变形处位于右端端面处。
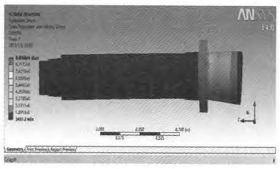
图5主轴等效应力图
根据上述分析得出的结果,主轴上受到的最大应力要小于45钢材料的许用应力;主轴的最大变形量为1.247×10一mm,也小于机床设计手册推荐的值,由此可以判断机床主轴的强度和刚度是满足工作要求的。
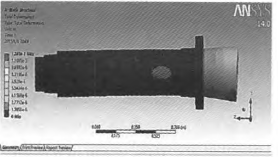
图6主轴总变形图
5.主轴模态分析
根据有限元理论,主轴的动力学方程如下:

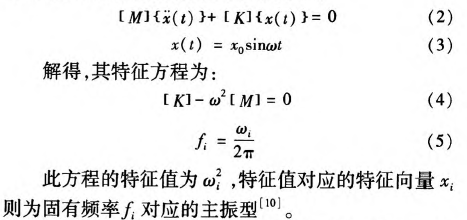
结构的振动可以视为各阶振型的线性叠加,而低阶振型比高阶振型对结构的振动影响大,低阶振型对结构的动态特性起决定作用,结构的振动特性分析通常取前5阶¨1|,对主轴进行模态分析后,得到了其前4阶模态分析结果,见图7~图10和表1。
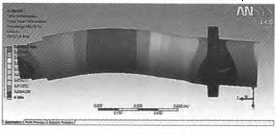
图7一阶振型
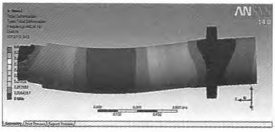
图8二阶振型
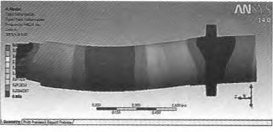
图9三阶振型
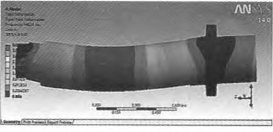
图lO四阶振型
表1主轴模态分析结果

当主轴以临界转速转动时,轴的挠度将达到最大值,到达“I临界”状态,主轴将产生强烈振动,导致轴的寿命下降,甚至破坏轴,根据模态分析得到的固有频率由式(6)可以计算出主轴各阶临界转速,见表2。

式中:n一临界转速(r/min)f--固有频率(Hz)
表2主轴各阶临界转速
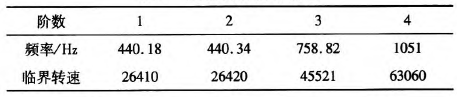
主轴的最高工作转速为10000 r/min,远远小于临界转速。因此该主轴设计合理,能有效地避开共振区域,保证主轴的加工精度。
6. 结论
双刀架数控机床可多刀同时加工,能极大的提高工作效率,本机床采用的西门子840D双通道、双方式组控制系统,由于共用一个系统,很好地解决了两个刀架协调加工地难题,极大的提高了加工的效率和精确性,另外,由于采用了统一的标准,使得编程和操作更为简洁方便。此外,为了保证该双刀架机床工作时的安全可靠性,还设置了硬限位和软限位双重安全保护措施。以车床主轴为重点研究对象,利用ANSYS Work—bench有限元分析软件建立了主轴模型,对其进行了静力分析和模态分析,在考虑工件重力的工况下,得到更精确的分析结果。验证了主轴设计的合理性,在设计阶段就对机床的性能作出预判,缩短产品的研发周期,提高效率,节省成本,增加企业的市场竞争力。同时该机整机有限元分析及优化设计奠定了基础。
投稿箱:
如果您有机床行业、企业相关新闻稿件发表,或进行资讯合作,欢迎联系本网编辑部, 邮箱:skjcsc@vip.sina.com
如果您有机床行业、企业相关新闻稿件发表,或进行资讯合作,欢迎联系本网编辑部, 邮箱:skjcsc@vip.sina.com
更多相关信息