摘要:绿色工艺(节能、减排、降本、增效、职业健康)是汽车制造企业不懈追求的目标,谁能先掌握绿色工艺核心技术,谁就能屹立于国际竞争的制高点。长安汽车近20年来,在与国际汽车巨头铃木、福特、马自达、PSA合资合作的同时,不断坚持绿色制造工艺设计自主创新,并取得了良好的实际应用效果;尤其在节能、减排方面效果显著。
汽车涂装是消耗能源的重要环节之一。由于汽车涂装过程是一个复杂的过程,需要消耗大量水、电、天然气等能源,其能耗大小对整个企业的能耗及生产成本影响重大。研究先进、实用的涂装节能工艺技术对推进汽车企业节能降耗,建设资源节约型、环境友好型社会具有重要意义。长安汽车在持续追踪国内外先进的涂装节能减排技术的同时,结合到企业自身特点研究应用了一大批先进、实用的节能减排技术,创造了可观的经济效益及社会效益。
关键词:绿色工艺 节能 减排 余热回收 静电喷涂 双摆杆 电动泵
1 概述
汽车行业涂装节能减排研究主要考虑3个重要环节,即工艺方案设计、生产计划管理及工艺设备运行维护管理,其中工艺方案设计环节是节能减排源头。在新工厂涂装车间方案设计时,除满足国家及当地政府节能减排及环保要求的同时,要结合到企业自身特点,统筹考虑涂装工艺原辅料供应商及车身模夹检具供应商资源与成本、车身外覆盖件表面质量、白车身焊接外观质量以及生产线投资许可等来制定工艺技术方案。否则,一味照搬国内外其它先进企业的做法注定是行不通的。长安近20年来,先后与铃木、福特、马自达、PSA等进行了合资合作,在消化吸收它们先进技术的同时,更注重结合自身特点进行二次工艺技术创新,从而走出了一条投资省、产出高、见效快的节能减排之路,并首次在长安某新区建成了具有典型"两型企业"标志的新整车生产基地。
2 涂装节能减排主要技术
汽车整车涂装主要节能减排技术见表1。
表1 涂装主要节能减排技术
序号 | 节能减排技术 |
1 | 烘炉排烟余热回收技术 |
2 | 高效壁挂式机器人静电喷涂技术 |
3 | 打磨、擦净室排风二次回收利用技术 |
4 | 前处理、电泳双摆杆集成输送技术 |
5 | 调输漆电动泵技术 |
6 | 污水处理站中水回用技术 |
7 | RO浓水回用技术 |
8 | 电泳逆向流动技术 |
9 | "加热分离+表面浮油自动收集除去装置"技术 |
10 | 前处理水洗槽免底部循环技术 |
11 | 前处理、电泳RO-DIP输送技术 |
12 | 分车型电泳技术 |
13 | 密封胶湿碰湿工艺 |
14 | 低温低沉渣量磷化工艺技术 |
15 | 3C1B涂装工艺 |
16 | 清洗溶剂回收再利用技术 |
17 | 水性涂料涂装工艺技术 |
18 | 高平整性无铅电泳工艺技术 |
19 | 前处理、电泳逆向补水技术 |
20 | 文氏漆雾处理技术 |
21 | 蓄热式集中排气技术(RTO) |
22 | 集中废气焚烧技术(TAR) |
23 | 颜色分组喷涂技术 |
24 | 底盘密封胶机器人挤涂技术 |
25 | 裙边抗石击机器人喷涂技术 |
26 | PVC机器人喷涂技术 |
27 | 液体表调技术 |
28 | 前处理硅烷工艺技术 |
29 | 免中涂B1:B2涂装工艺 |
30 | 2K清漆涂料涂装工艺 |
31 | 喷漆室排风热能二次利用技术 |
32 | 有机废物处理技术 |
33 | 纳米过滤水净化技术 |
34 | 粉末涂料涂装工艺技术 |
35 | 干式喷漆室技术 |
36 | 组合机器人内口喷涂技术 |
以上共列举了36项涂装节能减排技术,以下主要针对前10项技术进行简要介绍。
3 节能减排涂装工艺技术典型应用简介
3.1 烘炉排烟余热回收技术
简述:如图1、图2,在焚烧炉(电泳、中涂、面涂)排烟管路上设计安装热管气、液余热回收器,将热水管与锅炉连接。通过利用排烟管的热量加热热水锅炉的回水,降低锅炉加热回水所需的能量。
图1 烘炉排烟余热回收流程图
图2 热管气、液余热回收器简图
应用情况:该技术在某涂装线大规模应用,烘炉排烟温度由最高230℃降低至103℃左右。其中,回收热量161万kcal/h。
3.2 高效壁挂式机器人静电喷涂技术
简述:如图3,应用壁挂式静电喷涂机器人,喷漆室宽度较座式机器人减小20%(由6 m减小到4.8 m);相应喷漆室的供排风量以及循环水量减少20%,整个喷漆室的能耗也随之降低20%。
图3 壁挂式机器人喷涂断面图
应用情况:该技术在某涂装线应用实际节约电能185度/h,节约燃气97.8 m3/h,节约制冷量185万kCal/年。
3.3 打磨、擦净室排风二次回收利用技术
简述:将打磨、擦净室的排风二次循环应用到喷涂区、晾干区的供风系统,减少新鲜空气量的用量及能耗。
应用情况:该技术在某涂装线应用实际节约燃气192 m3/h,节约制冷量110万Kcal/h。
3.4 前处理、电泳双摆杆集成输送技术
简述:如图4,结合大型涂装前处理生产线特点,研究选用双摆杆输送系统关键部件,大幅度提升国产化率(达到了95%),并首次在国内大型汽车涂装生产线(55JPH)上集成应用具有国际一流水平的国产双摆杆输送系统。该输送系统特点如下:
1)工件能以45°的倾斜角入槽、出槽,大角度可以排除车壳内的气泡,工件沥水干净,窜液少,避免磷化或电泳缺陷。
2)因轨道和链条在设备两侧,从根本上避免了油污滴落在工件上或槽液内。
3)线路简单,运行平稳,对轨道的磨损小,设备故障率低(≤1%)。
4)空摆杆从前处理和电泳设备下方返回,节省空间和车间面技术。
5)输送柔性程度高,尤其适合多车型、大批量共线生产。
图4 双摆杆输送系统图
应用情况:该套输送设备价格比国外同等水平设备价格低50%左右,直接节约输送设备投资达1600万元;同时由于线体长度缩短21 m,槽体、泵、换热器等设备选型变小,相应节约设备投资105万元;另外,由于节省车间面积1300m2,相应节省土建投资325万元。
3.5 调输漆电动泵技术
简述:在调输漆系统中,油漆循环泵以前通常是气动泵和液压泵。随着电动泵技术的进步,电动泵在维护性、运行成本、对涂料的损害、系统控制等方面比液压泵、气动泵存在明显的优势,已经成为油漆循环泵今后的方展方向。电动泵与液压泵相比,其特点如下:
1)电动泵比液压泵的维护费用节约达80%;
2)电动泵的运行能耗低,每年仅为液压泵的23%;
3)电动泵脉动低,涂料剪切小,对涂料损害小。
应用情况:该技术在某涂装线应用,运行状态良好,液压泵系统单套能耗为2.56度/小时,电动泵系统单套能耗为0.91度/小时,比液压泵低64%左右。
3.6 污水处理站中水回用技术
简述:中水回用处理系统水源为通过废水站处理后的达到国家一级排放标准的水源。将需要排放的废水重新利用,通过提升泵经NaClO、HCl等消毒杀菌、多介质过滤器过滤、活性炭过滤器吸附、自清式过滤器、UF超滤后进入UF水箱,通过供水泵至RO系统处理。中水回用后的水质基本达到国家工业用水的标准。经RO处理后的回用水主要用于纯水站原水箱的补水及涂装车间前处理大流量水洗。某废水站中水回用设计参数如表2。
表2 某废水站中水回用设计参数
项目 | 参数 | 备注 | |
中水回用设备进水量 | 60m3/h | ||
UF系统 | 90% | ||
RO系统 | 75% | ||
设备产水效率 | 67.5% | ||
中水回用设备最终产水量 | 40.5 m3/h | ||
回用水使用点水量 | 纯水站原水补充水用水量 | 60m3/h | 中水回用产水量不够,只能部分补水 |
涂装前处理大流量用水量 | 7.5 m3/h | ||
合计 | 67.5 m3/h | ||
中水回用水利用率 | 100% | 使用点计算 |
工艺流程:
放流槽→提升泵→消毒杀菌→多介质过滤器→活性炭过滤器→自清式过滤器→UF超滤→UF水箱→供水泵→反渗透→回用水箱
应用情况:该技术在某涂装线应用效果良好。
3.7 RO浓水回用技术
简述:汽车涂装车间纯水制备一般采用二级反渗透工艺,该技术会产生约23%左右的RO浓缩水,以一级产水63 m3/h、二级产水28 m3/h的纯水制备系统为例,RO浓缩水高达20 m3/h。这部分水可以通过下表利用起来,如表3所示。
表3 RO浓水回用技术参数
序号 | 回用区域项目 | 用水量 |
1 | 主要车间及办公室冲厕、冲洗马路 | 3m3/h |
2 | 废水处理用的浓废水稀释及设备管路的反冲洗 | 12m3/h |
3 | 涂装喷漆线循环水补水 | 5m3/h |
合计 | 20m3/h |
应用情况:该技术在某涂装线应用效果良好。
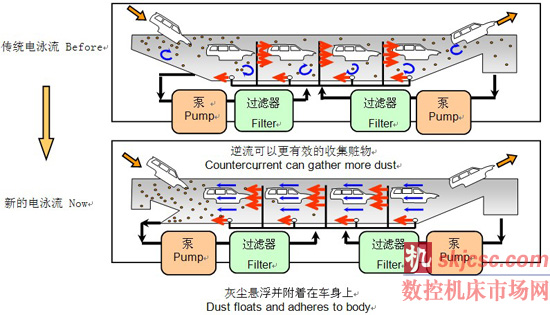
图5 电泳逆向流动与传统电泳流动图
3.8 电泳逆向流动技术
简述:如图5,电泳逆向流技术就是采用电泳涂料与车体逆向流动技术来减少附着在车身上的颗粒、杂质。传统的电泳漆在槽体的流动方式是:槽底电泳漆与车体逆向流动,槽体中部及上部电泳漆与车体同向流动,该方式最大缺点是槽内涂料颗粒、杂质较分散并易附着在车身上,造成车身颗粒多、电泳漆膜打磨量大,浪费人力、物力。新的电泳逆向流技术将槽体内部杂质集中到槽体后段,这不但减少了车体附着颗粒几率,而且便于集中收集处理杂质。
应用情况:该技术在某涂装线应用,减少了电泳漆膜颗粒打磨量约20%。
3.9 "加热分离+表面浮油自动收集除去装置"技术
简述:如图6,采用"加热分离+表面浮油自动收集除去装置"技术;较传统单纯的加热分离除油装置,节省加热槽体积达3 m3,减少装机容量100 KW。按设计产能(55JPH)计算,节约能耗25万元/年。
应用情况:该技术在某涂装线应用节能效果良好。
3.10 前处理水洗槽免底部循环技术
简述:通过合适的槽体设计省去传统的前处理水洗槽底部循环系统,不但可以节约装机容量,还便于集中收集处理槽底部的污泥、杂物,降低倒槽清洗频率,节约运行成本。
应用情况:该技术在某涂装线应用效果良好。
①原水槽②集油口③过滤器④电机
⑤泵体⑥油自动排出装置⑦浮上分离槽
图6 加热分离+表面浮油自动收集除去装置图
结语
上述列举了一些典型的涂装节能工艺设计及应用案例,可供涂装车间的规划建设及节能减排改造提供相应思路。其实,涂装行业中个别企业还有一些更先进的做法,如:一汽大众成都工厂在国内首次采用了免中涂B1:B2涂装工艺、干式喷漆室、组合机器人内口喷涂等先进节能减排技术。但无论如何,企业研究应用节能减排技术一定要与自身情况结合起来,不能照搬照用,否则将会投入大、产出低,达不到相应的节能减排效果。此外,节能减排另外两个重要环节,即生产计划管理及工艺设备运行维护管理也非常重要,良好的运行管理节能减排增效可达20%以上。
网友评论 >>查看更多评论