深孔内腔镀硬铬修复工艺
2020-6-10 来源: 国营芜湖机械厂 作者:马良冬,胡继东,胡水莲
摘要:对某型飞机进气道保护装置作动筒外筒内腔腐蚀镀铬修复进行工艺研究,从腐蚀原因及影响方面论证修复必要性,从零件结构特点,夹具设计,镀铬处理和检验验证等技术难点方面阐述论证。设计一套用于该型号的外筒内腔镀铬修复保护夹具,设定镀铬层厚度参数,磨修参数,热处理方式和检验验证程序等,成功完成对内腔尺寸修复。结果表明:夹具,尺寸,电流和检验等方面设计良好,对同类型产品腐蚀修复具有一定参考意义。
关键词:深孔;内腔;硬铬;修复
引言目前,国内外镀铬修复主要以外圆修复为主,内腔修复案例较少,尤其对于内径尺寸小、孔径深的外筒,镀铬过程中若无法有效保证铬层均匀性与致密性,将为后期补充加工恢复精度增加困难。分析原因,不难发现电镀前内腔表面质量处理不到位、电流密度大小控制不恰当和夹具结构设计不合理等多个因素均会导致内腔镀铬失败。外筒内腔镀铬对铬层质量要求高,一次镀覆合格率约 20%~30%[1],相比其他表面处理方式成功率相对较低,周期较长,无法有效保证生产任务,因此提高外筒内腔镀铬修理质量十分必要。
1、 故障概述
某型飞机进气道保护装置作动筒外筒内腔镀铬属于镀硬铬,经分解检查,发现外筒内腔存在 1处深度约(0.1~0.2)㎜腐蚀坑,清除腐蚀表面油污,涂抹硫酸铜检验。外筒内腔铬层完整的致密性良好,硫酸铜不会与铬层发生化学反应,一旦发生掉块,铬层不致密区域裸露出基体,硫酸铜与基体 Fe发生置换反应生成 Cu 单质,出现铜的红色。化学反应如下:Cr + 3CuSO4= Cr(SO4)3+
3Cu,经检验确认掉铬(见图1)。
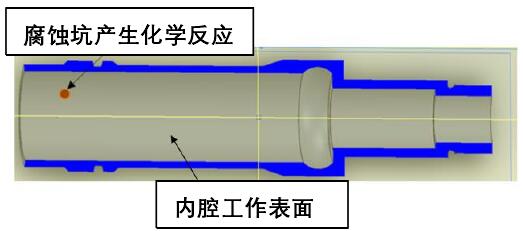
图1 内腔局部腐蚀模拟图
活塞杆活塞头装配的密封圈存在一定凸出量,与外筒内腔属于过盈配合,短期工作过程中内部串油可能性较小,但长期停放以及使用时,串油风险加大,且存在腐蚀若不作处理直接使用,后期腐蚀面积及深度势必会加大。为保证产品性能,对外筒修复恢复其表面质量。
2、 修复方案
镀铬层具有很高的硬度和耐磨性能,维氏硬度一般可达 HV900~HV1200,通过镀铬能够有效提高零件的耐磨性,延长其使用寿命。但是镀铬层也存在其缺陷性即随着铬层厚度的增加,其与与基体结合力随之降低,这意味着脆性增大,零件强度降低[2]。故采用镀铬修复零件表面质量时需要严格控制镀层厚度。
若单独对腐蚀部位进行刷镀,铬层贴合力、强度无法有效保证,产品质量始终处于第一位,对产品采用重新退铬镀铬处理。因外筒内腔重新镀铬合格率低返工率高,在修理过程中充分吸取失败经验,完善修理过程中各步骤相关参数,为同类型产品镀铬修复提供一定借鉴。
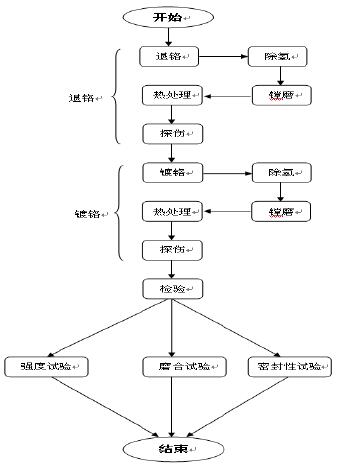
图2 修理流程示意图
2.1 镀前预处理
镀铬质量评价标准中最基本的两项是铬层致密性和均匀性。镀前零件粗糙度值低的产品,镀后表面质量相比粗糙度值高的有明显改善,究其原因,电镀部位粗糙度值低,表面光洁自然较高,铬层沉积过程中与内壁贴合紧密。其他电镀条件相同的条件下,单位表面积铬层沉积致密性能够得到很大提高,自然铬层表面质量以及光洁度能够提高一定等级[3]。故可采用对外筒退铬后进行必要的镗磨处理,提高内腔光洁度,保证铬层具有较强的贴合力。
外筒磨修过程中去除一定尺寸后零件内部产生一定应力,不做处理后期工作过程中容易产生裂纹,一般机加处理后通过低温回火来去除内应力,提高产品质量。
2.2 尺寸控制
图样技术要求铬层厚度为(48~80)μm,图示规定镀后内径为Φ40 mm+0.062 mm(见图3)。经计算,退铬后基体尺寸应控制在如下范围:
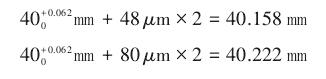
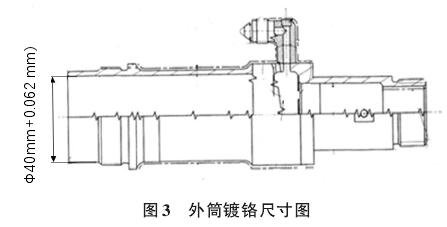
镗磨设备磨修精度为微米级,为减小磨修工作量,需严格控制镀层厚度。根据磨修经验,0.01 mm余量去除需要 1~3 h,余量较大不利于磨修且磨修后表面质量较差。图样要求电镀合格的外筒内径尺寸在 Φ40 mm+0.062 ㎜范围内,去除约 0.01 mm余量,尺寸应控制在 Φ40 mm+0.050范围内,后续采用精磨恢复内径尺寸及表面粗糙度[4-5]。
2.3 夹具设计
液压外筒内孔镀铬质量高低与夹具的结构设计有着直接关系,结构设计合理、恰当,很大程度上可以提高外筒内壁铬层圆度和精度。传统电镀装挂方式适用于内孔深度浅、壁厚和电镀质量要求低的零件,而该外筒内孔小、深、结构发杂且存在无需电镀部位,采用常规的电镀方式无法满足工艺要求。
故需根据外筒结构特性、外形尺寸和工艺镀铬要求重新设计镀铬夹具,选用大小合适的不溶性阳极,且保证阳极与内孔同心,以减小镀层的椭圆度。一方面阳极长短要适当,保证排气畅通,镀液能顺畅流过,另一方面要保证阴阳极之间的绝缘,确保电镀过程中内孔上、中、下部位铬液均匀变化且端口不产生铬瘤、龟裂。针对不需镀铬的部位采用,绝缘保护,防止铬液渗透,而选取的保护材料要能耐酸钾、耐高温,易剥离、易操作[6-7](见图4)
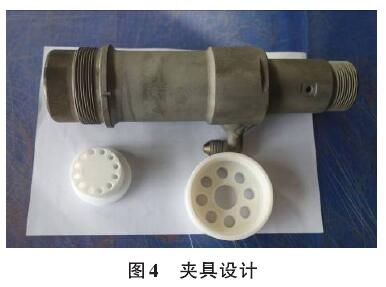
2.4 电流控制
电镀过程中电流过大容易镀层表面大片的起皮并产生镀瘤继而导致修复失败需要二次电镀,严重影响修理周期,同时对于高强度零件,一般镀铬返工次数不宜超过 3 次,否则将影响机体强度,故确定合适的电流参数对修复至关重要[8]。外筒内腔属于异形件,镀层质量要求更高,电镀过程中需要严格把控电镀相关参数(见表 1),吸取电镀过程中失败的经验,最终确定最适宜的电流密度(25~30)A/dm2。最后根据电流密度、温度、镀层厚度和镀层沉积速度等计算出所需电镀时间。
b1
3 、验证方案
外筒镀铬处理结束后,通过强度实验、磨合实验和气密性实验验证产品质量。
3.1 强度实验
重新退铬、镗磨和镀铬等对外筒强度产生一定影响,为检验修复后的外筒质量是否满足要求,采用 1.5 倍工作压力实验外筒强度,要求在高压冷气强度实验台中实验(见图6),具体操作如下:轮流给管嘴 1 和管嘴 2 供 1.5 倍工作压力,并保持 3 min,检查作动筒应无裂纹和永久变形,保压时固定密封处允许出现肉眼看不见但借助滤纸可发现的微滴,活动密封处允许目视可见的积累但不成滴落下(见图5)。
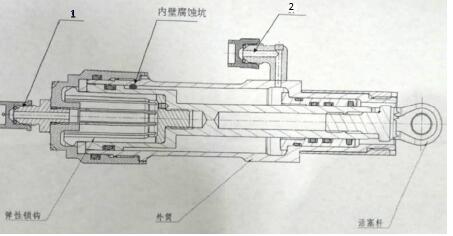
图5产品结构原理图
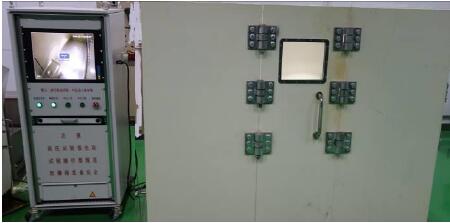
图6强度实验检测
3.2 磨合实验
磨合实验属于模拟机上工作状态,产品在工作压力条件下多次收放,完成磨合后分解检查相关配合零件质量,确认无问题方可装配交付,具体操作如下:对管嘴 1、2 提供工作压力,使活塞杆组件完成100 次双行程,每经 25 次循环,将活塞杆组件旋转90°(见图 7)。磨合后分解作动筒检查其内部密封件、氟塑料挡圈、活塞头部状况。
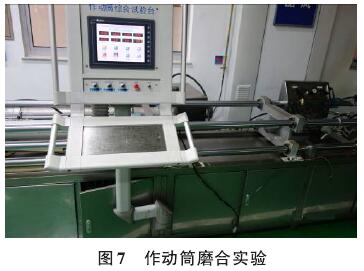
3.3 密封性实验
重新电镀的铬层致密性需要严格把控,产品长期使用过程中铬层疏松会导致渗漏油、串油等风险,故在上述强度实验、磨合实验符合要求后,仍需对产品装配进行密封检测,具体操作如下:向作动筒两管嘴 1、2 同时施加工作压力,保持5 min,作动筒各密封处不允许泄漏(见图8)。
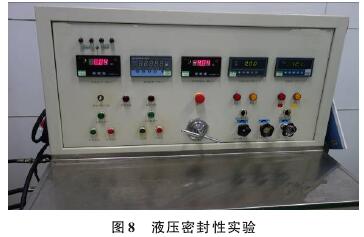
4、 结论与建议
通过参照以往修理经验、摸索该产品结构征,设定合理电镀电流、夹具和机加处理等方式修复产品,并且通过上述 3 项检验要求,确定内腔修复质量满足工艺要求。外筒内腔镀铬修理合格率较低,镀前处理不当、电流密度大小不恰当和夹具设计不合理等多个因素均会导致内腔镀铬失败,返工过程中要能够学会分析研究失败的原因,总结相关参数,摸索出适合该产品的最佳方案,提高产品的修复质量与效率。修复工艺流程、处理方式和相关参数等为同类型产品腐蚀修复具有一定借鉴意义。
投稿箱:
如果您有机床行业、企业相关新闻稿件发表,或进行资讯合作,欢迎联系本网编辑部, 邮箱:skjcsc@vip.sina.com
如果您有机床行业、企业相关新闻稿件发表,或进行资讯合作,欢迎联系本网编辑部, 邮箱:skjcsc@vip.sina.com
更多相关信息