数控龙门高速铸锭复合加工生产线智能控制
2018-3-8 来源: 齐齐哈尔尔二机床(集团)有限责任公司 作者:张会龙
【摘要】: 本文介绍了数控龙门高速铸锭复合加工生产线的智能控制技术,阐述了实现智能控制的方法和途径。
【关键词】: 智能控制; 自动加工;840D
概述
铝锭铣面是铝合金板带材生产工艺流程的一个重要阶段。铝锭在轧制之前,必须将上下两侧表面铣平,以保证最终产品质量,我公司生产的数控龙门高速铸锭复合加工生产线全部实现自动化,用户可对生产工艺参数进行调整,满足不同用户的生产要求,对设备关键点实时进行监测并根据设备运行状态自动提供设备信息、故障自诊断信息、故障处理方法。同时,根据铝加工行业的特点,开发一套生产操作系统,用于完成与MES 和L1 的通讯和数据交换,以及相对应的操作功能和数据处理功能。
1.数控龙门高速铸锭复合加工生产线介绍
如图1 所示,数控龙门高速铸锭复合加工生产线是一条全自动加工单元,采取流水线式布局,由主机和辅机两部分组成。
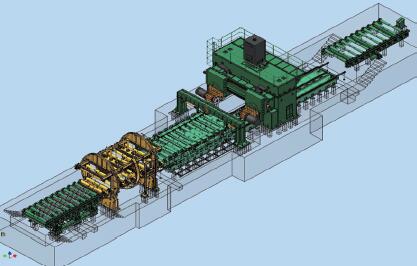
图1 数控龙门高速铸锭复合加工生产线图
主机由上料车、上料辊道装置、翻转装置、龙门、床身、工作台、工件对中机构、卡紧机构、测量装置、主铣头、角度侧铣头、称重、喷码系统、下料辊道、下料车、电气控制系统、液压系统、润滑系统、气动系统等组成。
辅机由吸屑管道、破碎机、吸屑风机、旋风分离器、铝屑收集装置、粉尘吸集装置等组成。
2.控制方式及方法
作为铝锭外表面加工的专用机床,该机床有三个主轴,其中一个方滑枕立式主轴和两个带摆角的卧式主轴,卧式主轴可同时加工铝锭的一个大平面和两个角度小平面,因此主轴角度要求在0-25 度之间可任意调整。机床可以进行全自动循环加工、半自动循环加工、手动铣削、单面铣削,并有单动作、手动调整等功能。
机床的自动化主要体现在以下几个方面: 工件自动上、下料; 工件自动翻转并且自动降速;工件自动夹紧; 工件厚度、宽度自动测量并自动进刀; 数控自动编程及切削参数优化; 自动安全防护回退; 工件自动称重; 铝屑的自动收集等。为提高机床自动化程度及控制系统稳定性的
主要实施以下措施
(1) 控制中心采用840D 数控系统和数字化驱动及1FT6 系列交流伺服电机。系统内部具有对所控制伺服电机的全部保护和控制功能,所有控制的伺服电机运行参数都能在屏幕上显示出来供使用参考。不需外部复杂联线,装配工艺简单,维修方便,工作稳定可靠。可连续不间断工作;
(2) 配置OP015A 型15 英寸彩色显示器具有以太网接口,可以根据用户要求,同上位机连接完成数据交换。设备的所有监示和检测信号都通过PLC 传送给840D 系统,行成中文报警文本,并通过显示器显示,保存成历史记录可供今后查询使用。PLC 所有I/O 接口信号状态都可以在显示器上显示,供操作及维修人员参考;
(3) 所有辊道都采用西门子交流变频器驱动,并且与数控系统之间采用总线方式传送命令,并通过数控编制的程序控制;
(4) 由于设备各控制部件分散较远,故PLC采用西门子S7-300 和ET200 组成,子分站采用PROFIBUS-DP 现场总线方式控制,共采用4个分站,分别是: 滚道及翻转机构分站、龙门工作台分站、主龙门架上分站、主操纵室分站。分站采用全封闭的分线箱结构,安装在被控部件附近,减少了机床控制连线,提高了可靠性,维修更方便;
(5) 毛坯的上料、定位、卡紧、测量、数据传输,各轴的跟踪测量,切削加工均由程序自动完成,主机与辅机之间采用现场总线方式控制,提高了机床的可靠性;
(6) 设备的辅助动作(辊道、液压、气动、润滑等)都由数控系统发出的M 代码经PLC 去控制自动完成;
(7) 辅机驱动的交流电机(破碎机、碎屑风机、铝粉尘收集风机)采用交流软启动和交流变频器驱动,配有完善的监控系统对电机监控(电流、轴承温度、线圈温度监视)通过编制合理的程序,控制变频器完成碎屑风机的节能控制,控制命令来自840D 数控系统。
3.实时采集设备自身运行状态及故障诊断的方法
(1) 研发了一种接触式铸锭测量系统,通过气缸驱动测量板压紧在铸锭被测面上,利用与840D 数控系统相连接的光栅尺和绝对编码器确定铸锭厚度、宽度及斜边的相关参数,并由此确定铣削量和铣削次数。测量精度为±0.2mm,采用全自动控制,确保在最短时间内完成铣面过程;
(2) 主轴箱安装了多点温度传感器和振动传感器,随时监测主轴的温度变化及工作状态;
(3) 破碎、吸屑、除尘电机和轴端安装有温度传感器,实时监控其文段变化及工作状态;
(4) 实时对主轴电机和辅机电机的电流进行监测;
(5) 三个主轴、破碎、吸屑、除尘的传动端安装接近开关,通过高速计数器监测其转速变化;
(6) 对各液压点位和气动点位的压力及流量的监测;
(7) 铝锭定位控制传感器采用反射式光电开关,监控并实时显示铝锭的实时位置;
(8) 三个主轴安装有防撞机构,实时对主轴进行进行监测及保护;
(9) 在840D 系统屏上实时显示铣头的实际位置、侧铣头旋转角度、设备工作中夹紧放松状态、当前正在铝锭加工信息、铣后铝锭信息、自动加工程序进度,以及各部件工作条件、铝锭历史信息等。
当以上监测点出现故障时系统会在界面进行显示并自动进行安全保护,每个故障都具有相应的诊断提示和处理方法; 在主画面和生产监控画面顶端都有报警视图,显示当前报警并可查询报警记录。
4.实现网络通信及数据交换的方法
设备具有生产操作系统,用于完成与MES和L1 的通讯和数据交换,以及相对应的操作功能和数据处理功能。
(1) 实施方案概述
铣面加工生产操作系统通过与数据服务系统进行交互,实现铣面加工生产计划与生产参数等数据的自动获得,并把这些数据通过ODBC 数据接口下达给WinCC fl exible 系统。同时,对于WinCC fl exible 系统产生的生产实绩等数据,铣面加工生产操作系统把数据通过数据服务系统上传给L3。
另外,铣面加工生产操作系统将包含一个独立的数据处理部分,用于把生产过程数据记录转化为iba 的文件格式(*.dat),以实现系统生成数据格式的统一,以方便存储、管理与使用。系统结构图如图2 所示。
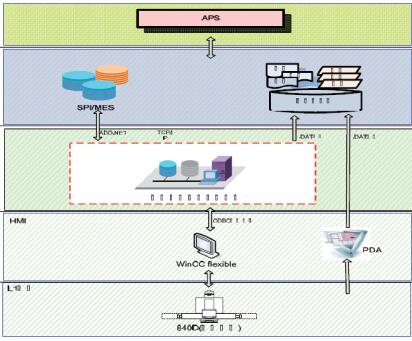
图2 系统结构图
(2) 数据服务系统功能与实现
实现与铣面加工生产操作系统的数据交互,保证L3 数据与WinCC fl exible 系统的自动交互数据服务系统通过TCP/IP 方式与铣面加工生产操作系统进行通讯,并以此下达L3 的生产计划与生产参数数据给WinCC fl exible 系统,最终实现相关数据下达到L1; 同时,数据服务系统通过TCP/IP 方式,从铣面加工生产操作系统获得WinCC fl exible 生产实绩等数据,最终上传给L3 系统。
结论
数控龙门高速铸锭复合加工生产线全部实现自动化,用户可对生产工艺参数进行调整,满足不同用户的生产要求,对设备关键点实时进行监测并根据设备运行状态自动提供设备信息、故障自诊断信息、故障处理方法。同时,根据铝加工行业的特点,开发一套生产操作系统,用于完成与MES 和L1 的通讯和数据交换,以及相对应的操作功能和数据处理功能。最终实现L3 系统中的生产计划和生产参数等数据自动下达到WinCC fl exible 或L1 系统,同时现场生产实绩也能自动上传给L3 系统,使所有的数据交换不再需要手工处理,过程数据和PDA 系统生成的数据以统一的存储方式保存到文件服务器中,以方便用户的管理与使用。用户可对全部过程数据进行分析。通过新建的数据服务系统,在满足数据库管理与数据查询方便的同时,保证数据库的安全。
数控龙门高速铸锭复合加工生产线的成功研制,不仅打破了国外的技术垄断,挡住了进口,为国家节约了大量的外汇,还为有色金属行业的生产提供了技术先进的装备,促进了行业的进步与发展。
投稿箱:
如果您有机床行业、企业相关新闻稿件发表,或进行资讯合作,欢迎联系本网编辑部, 邮箱:skjcsc@vip.sina.com
如果您有机床行业、企业相关新闻稿件发表,或进行资讯合作,欢迎联系本网编辑部, 邮箱:skjcsc@vip.sina.com
更多相关信息