子程序在螺纹铣削中的应用
2018-3-2 来源:总后勤部建筑工程研究所 作者:张力 张少飞
摘要:本文就数控加工中心的螺纹铣削进行了系统地总结。程序简单易懂、套用方便。
1. 单齿和多齿螺纹铣刀加工螺纹
铣削螺纹的刀具叫螺纹铣刀,根据刀具工作部分的形状,它一般分单齿螺纹铣刀和多齿螺纹铣刀。只要直径合适,多齿螺纹铣刀既可以铣削和它螺距相同的内、外螺纹,也可以铣削左、右旋方向不同的螺纹;而单齿螺纹铣刀,则不受螺距和螺纹大小的局限,也就是说理论上它可以铣削比自身直径大的任何内、外和左、右旋向的螺纹。但实际上无论单齿螺纹铣刀还是多齿螺纹铣刀,都尽量要选择比铣削的螺纹孔径大些的,这样的刀具有利于加工时的弧线进刀和退刀,道理和孔的铣削一样。
螺纹铣刀还分为整体合金磨成和装刀片回转式两种,它们各有各的优势和特点。实际使用时,可以根据零件的批量大小、材质、孔的形状大小以及图样中对零件螺纹表面质量的要求进行选择。一般来说多齿的螺丝铣刀效率高,加工的螺纹表面粗糙度稍微好些;而单齿的螺纹铣刀有通用性好、投入成本低等特点。
2. 螺纹铣削的原理
螺纹铣刀铣削螺纹是建立在螺旋式下刀方法基础上的加工方式,设备必须是有三轴联动功能的数控铣床。铣螺纹的原理为螺纹铣刀每绕孔或轴铣一周,刀具在Z轴方向上同时运动一个导程(即一般所说的一个螺距P)。
3. 铣削螺纹前的注意事项
(1)批量大的零件,优先考虑选多齿螺纹铣刀,最好是适合所加工零件材质的、装刀片的多齿螺纹铣刀,这样效率高、互换性好。
(2)铣刀直径最好选比被加工螺纹孔径小5mm以上的,这样加工时,有利于安全进刀和退刀。
(3)尽量提前模拟空试调程序,由于螺纹刀具一般比较昂贵,所以一定要小心。
(4)螺纹铣刀的刀具长度和直径一定要测量准确,记入刀补里。这样一旦螺纹加工一半刀具损坏时,只要重新换成相同规格的刀具,再次测量准确刀具长度和直径,重新记入刀补里,就可以重新从头铣削加工了一半的螺纹,一般不会乱牙。
(5)螺纹铣刀铣出来的螺纹,用螺纹规或者和它相配合的螺塞、螺栓来检验是否合格。螺纹的松紧可以通过调整刀具表里的半径补偿很容易地实现。
(6)为了提高铣削螺纹的效率,多齿螺纹铣刀一般从孔上方Z向快进到孔表面以下2个螺距以上,才开始侧向螺旋进刀,具体要看零件材质和硬度以及刀具的刚性表现。
4. 用固定的子程序样式,通过循环调用加工
利用OKUMA数控系统自己编了一个在该系统加工中心上通用的铣削螺纹的子程序,称其为“螺纹傻瓜程序”,已经使用了好几年,经过实际检验和多次完善,在该系统的数控铣床和加工中心上可以放心使用。子程序格式和内容如下:
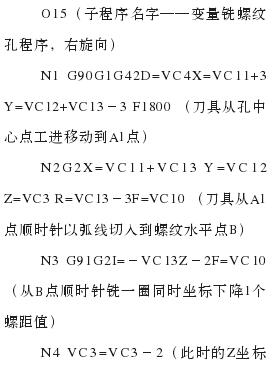
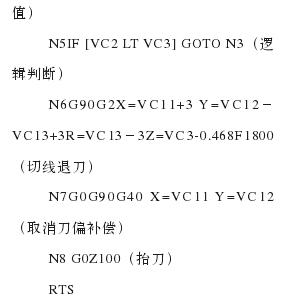
以上为子程序(O15)。现在解释一下程序中出现的几个变量,为便于理解以铣削M65×2、深度11mm的螺纹孔为例,讲解子程序调用。
图 1 所 示 为 M 6 5 × 2 的 螺纹 孔 ,φ 6 5 m m 为 螺 纹 大 径 ,φ 63mm为螺纹底孔,此螺纹孔螺距为P=2mm,零件材质为铝合金。选择回转直径为21mm的10齿刀片式的矩形螺纹铣刀,螺距为2mm,可知刀片可同时参加工作的切削刃长为20mm。图2所示为图1的编程示意图,用这个图来分析子程序的语句。
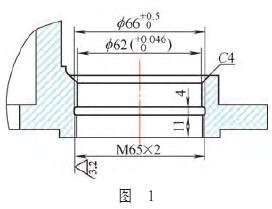
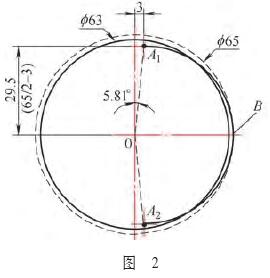
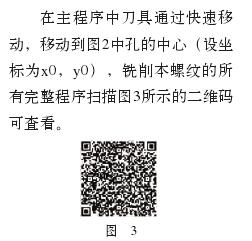
现在就以上程序解释几点:
(1)在OKUMA系统中,变量符号为VC,VC1表示变量1,和FUNAC等数控系统稍微有点不同,但仅仅是表示方法不一样,道理一样。
(2)N600 VC1=-8 表示刀尖不是从外部开始螺旋下刀的,考虑到零件材质为铝合金,刀片有效尺寸为20mm,长切削刃,所以从孔内8m m深开始螺旋下刀,等于螺纹铣刀初次是4个刃开始同时切削工作,如果刀具选择合适,甚至可以考虑下刀再深些,刀具螺旋进给旋转一圈就可以完成螺纹的加工。
( 3 ) N 6 0 0 V C 3 = V C 1 -0.468,表示图2中刀具从A1点弧线切入到水平B点时Z坐标的值。切记,此处一般很容易理解成V C1-0.5,实际上是小于2/4=0.5( 其 中 2 实 际 表 示 螺 距 ) 。 只要 求 出 或 作 图 得 出 O A 1 与 Y 轴夹角,这里夹角是θ =5.81°,0.5×5.81/90=0.468。所以当孔大小不同或者A1点坐标位置不同时,主程序和子程序中表示此值的部分都要重新计算,然后重新输入。
(4)N800 VC4=23,把螺纹铣刀的半径输入到偏置参数H23中,实际使用时自己可以根据情况更改此值,只要和刀补号码一致就可以了。
(5)N900 VC10=240,这个也可以根据螺栓的表面粗糙度和刀具的刚性来适当地增减,当然它和主轴转速也有正比关系。
(6)VC11和VC12分别应该赋予要加工螺纹孔的X、Y坐标值,有正负之分。
(7)N1200 VC13=65/2,这里一定要输入螺纹大径的一半。
(8)子程序中N1段,表示刀具从孔中心点工进移动到A1点,同时带上刀具偏置,此处数值为3,可以通过观察图2理解,它等于螺距加1,当螺距不同时,这个值可不同(这个点设
在螺纹孔内部即可)A1点的X和Y的坐标值就是X=V C11+3、Y=VC12+VC13-3。
(9)子程序中N2段,表示刀具从A1点顺时针以弧线切入到螺纹水平点B。
(10)子程序中N3段,表示刀具从B点顺时针铣一圈同时坐标下降1个螺距值,此处为2,用增量G91编程。
(11)子程序中N4段,表示刀具此时的Z坐标值。
(12)子程序中N5段,表示逻辑判断,当Z坐标值未到最终下刀位置时继续循环加工螺纹,直到刀尖到达的位置不低于主程序设定的VC2=-11.5值。
(13)子程序中N6段,表示刀尖Z坐标达到设定值后刀具以弧线退出螺纹表面,即从B点移动到A2点同时Z坐标再次切入0.468mm。
(14)子程序中N7段,表示去掉刀偏刀具移动到螺纹孔中心。
(15)子程序中N8段,表示刀具快速移出孔,抬到安全位置准备下个孔的加工。
通过以上较为详细的例子,不难理解螺纹铣削的整个过程。那么下面再举个相对比较复杂和实用的加工案例。有了子程序后,编起来就简单多了。零件名称为阀体,零件材质为铸钢,螺纹铣刀为多齿刀片式,螺纹铣刀直径为φ15mm,螺距P=1.5mm。
机床工作台上摆放了6个零件,6个位置是这个零件不同的6 个面。前面钻孔镗孔和倒角的程序省略掉,仅摘出螺纹加工的部分,全盘考虑各方因素,在6个零件的每个位置建立了一个独立的坐标系,如图4中H1 H6所示,图中要铣削螺纹的是M22和M27,螺距均为P=1.5mm。
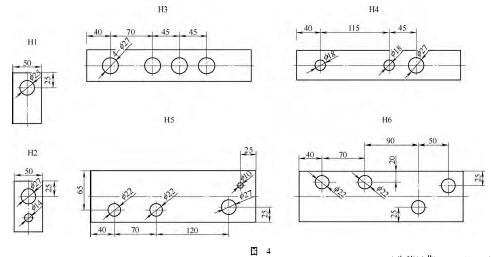
以上钻镗孔程序略,铣螺纹孔程序扫描如图5所示的二维码可查看。
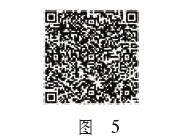
所有子程序和主程序至此结束。可以看出,程序中铣削了M22×1.5和M27×1.5两种不同的螺纹尺寸,它们分布在不同的坐标系中,在零件不同位置上,螺纹深度也不相同,但是有了专门铣削螺纹的两个子程序后,主程序则变得简单明了,极易发现问题和更改参数值,虽然是一把螺纹铣刀通过一个刀具半径补偿来铣削很多螺纹孔,但对个别孔
松、紧的特殊要求也能通过参数“VC13”单独实现。
5. 结语
数控系统众多,但其实都可以参照图2的切削路线,通过不同的系统变量的表达方式和应用计算,可得到需要的铣削螺纹程序。
投稿箱:
如果您有机床行业、企业相关新闻稿件发表,或进行资讯合作,欢迎联系本网编辑部, 邮箱:skjcsc@vip.sina.com
如果您有机床行业、企业相关新闻稿件发表,或进行资讯合作,欢迎联系本网编辑部, 邮箱:skjcsc@vip.sina.com
更多相关信息